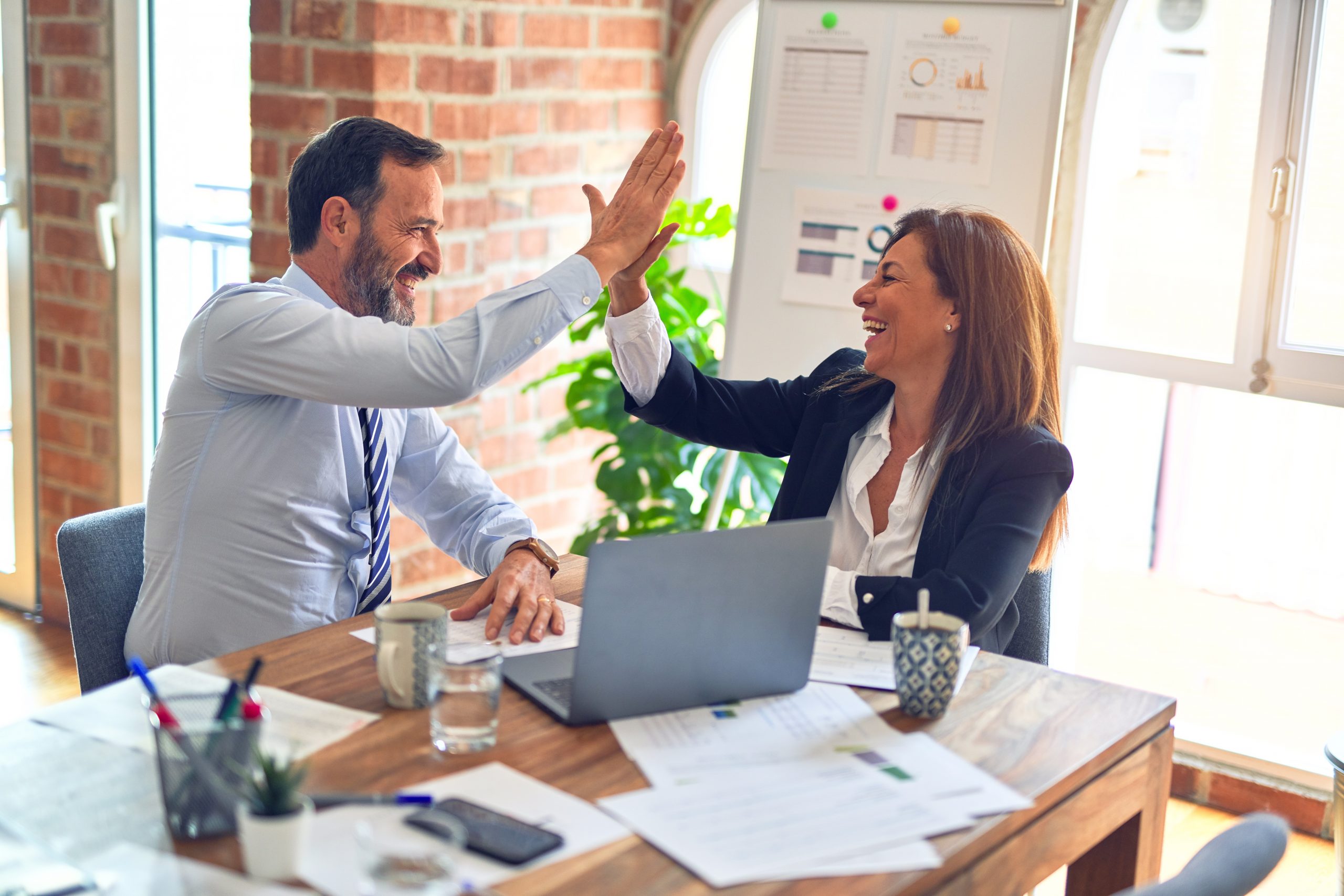
In June, GS1 UK, a supply-chain standards nonprofit, released the results of a six-month study with Cranfield University’s School of Management, of Bedford, England, stating that 80 percent of the product supply chain data captured by the top four grocery retailers in the U.K. were inconsistent with data used by suppliers. Of the 66 “core data attributes” identified in the study, only 14 were matched between supplier and retailer.
Soon after the study was released, U.K.-based LCP Consulting published a white paper that analyzed the GS1 retail data from a Six Sigma perspective. “Understanding the True Costs and Benefits of Data Accuracy,” by Alan Braithwaite of LCP Consulting and Richard Wilding of the Cranfield School, found that the scale of the errors between suppliers and retailers, as well as their frequency, were the main drivers of the true data discrepancy costs, which LCP estimated could run as high as 1.8 percent of annual revenues.
Here are eight key steps that the LCP report outlined to improve data accuracy:
1. Measure actual performance continuously – By using data capture and validation methods, practitioners can find duplicate data, missing fields and other errors more quickly and can provide a better sense of the impact these errors have on the rest of the process.
2. Use dimension-scanning equipment to capture missing data – When dealing with physical products, the use of dimension scanning and weighing systems can track pallet loads, making it easier to perform periodic audits.
3. Monitor and analyze data adjustments – By recording all data adjustments that are made, and by whom, practitioners can get a better sense of the underlying performance of their processes and identify the data areas that are most at risk. The monitoring can be used in stock auditing, pricing, physical measurements and supplier data.
4. Set up a perpetual audit process – This auditing system can be integrated with a perpetual inventory auditing process to validate and manage data, and to provide an idea of the scale of any accuracy issues that arise.
5. Identify value potential and focus on the big opportunities – An integrated framework should be set up to convey the cost impacts of data accuracy problems, which can enable process improvement teams to prioritize actions.
6. Systematically improve processes to manage input – Practitioners should apply data management plans to improve performance, but should also be careful to add processes that have no direct costs to the business or involve only short-term reassignments of resources.
7. Build Six Sigma accuracy into cross-functional KPIs – Publishing key performance indicators (KPIs) is a good way to ensure that quality at an organization is everyone’s responsibility. Reporting accuracy against Six Sigma standards can help raise the profile of the issue and can be used to help celebrate success when improvements are made.
8. Automate data alignment where possible – While countries such as the United States, Australia, Canada, the Netherlands and Germany all use global data synchronization technology to automatically align data between suppliers and retailers, LCP notes that this system is not yet available in the U.K.