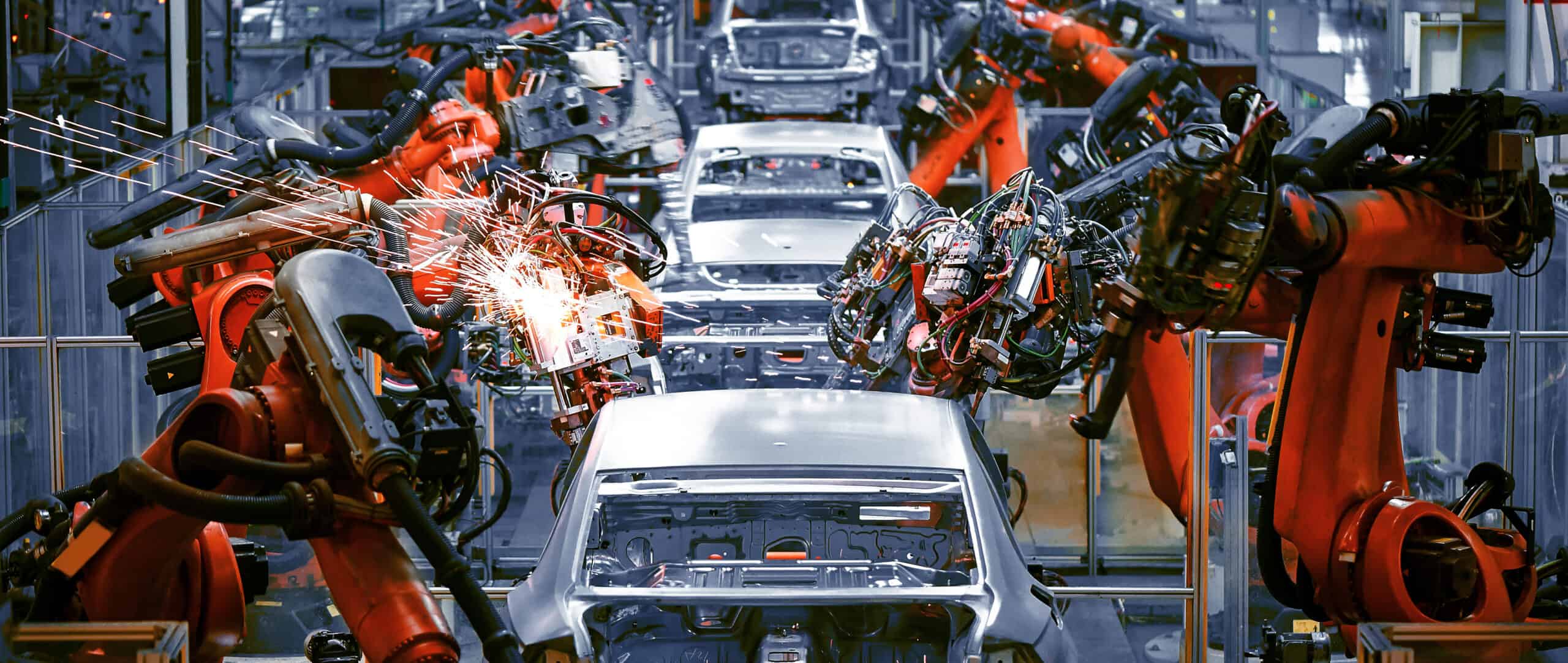
Congratulations! You followed the DMAIC process to successfully improve your operations. The goal was to reduce the amount of time it took to produce a certain product, so you hired a lot more people to get the job done faster. Now your primary metric, time, is looking great!
Problem solved, right? Wait a minute, now labor costs are through the roof! How did we let this happen? What could we have done differently? We could have used some secondary metrics.
Overview: What are secondary metrics?
While the primary metric is the direct measurable output of the process that produces a product or service, a secondary metric provides additional information that may help in your goal but are not directly tied to the result.
3 benefits of secondary metrics
It’s important to make sure that what you do to improve the primary metric doesn’t have unintended consequences on other measures. This is where secondary metrics come in.
1. They provide a holistic picture
Secondary metrics help provide a wider view of the state of operations and help make sure other things are not broken for the sake of improving the primary metric. If the goal is to produce a maximum number of parts per hour, measuring defects as a secondary metric helps make sure that quality is still being met.
2. They avoid problem-shifting
Sometimes, in the name of improvement, workers may shift problems to another department in order to optimize their own work area. By monitoring additional metrics, we help make sure that improving one process doesn’t create new problems elsewhere.
3. They provide protection
When working to improve a process, secondary metrics make sure we are not sacrificing something else about the process to achieve our goal. They protect our overall operations and keep the project team honest as to how they go about improvement activities.
An industry example of secondary metrics
Say you’re an automobile manufacturer, and your primary metric is the number of cars produced. You want to produce as many cars as you can, and there are a lot of ways you can accomplish this. You could hire more people, or tell each person already employed that they must produce a certain amount of cars per hour. This will give you the results you’re looking for, but at what cost?
Hiring additional employees costs money, so labor costs might be something else you want to monitor to make sure they don’t go up too much in pursuit of maximizing the number of cars you produce.
In working to increase the amount of cars produced, employees may start to rush in order to meet the primary metric. This could lead to mistakes in the cars produced, compromising quality and safety. Defects may be another area you want to monitor to ensure that quality is not being sacrificed for the sake of making more cars.
In this example, labor costs and defects are secondary metrics you can monitor to make sure that your overall business is still running well as you try to improve the primary metric (number of cars produced).
3 best practices when thinking about secondary metrics
Since secondary metrics help protect the overall business when making improvements, there are a few things you want to keep in mind.
1. Understand the larger picture
After the primary metric has been identified, think about what needs to stay the same (what cannot be sacrificed) to meet that goal. Costs, customers, performance … these are all areas to consider monitoring to make sure changing one thing does not negatively impact another.
2. Brainstorm with the team
Good improvement projects have diverse teams made up of individuals with different experiences, from different departments, etc. This diversity helps you view the problem from multiple angles, so other team members are a great resource for understanding what else to pay attention to as far as metrics go.
3. Consider what can go wrong
When looking at the process being improved as well as the overall cadence of the improvement project, think about what could go wrong. Anything that risks negating the positive effects of a project is something worth paying attention to and thus a good candidate for a secondary metric.
Frequently Asked Questions (FAQ) about secondary metrics
Do I really need secondary metrics?
Yes, you do. Processes are not one-dimensional, and there are many different inputs. Changing one can impact the others, and you need secondary metrics to gauge this impact and make sure it’s not compromising other areas.
How do you identify secondary metrics?
Consider what areas are critical to quality. Since they are critical, their values need to be controlled. In order to control them, they need to be known and monitored. These are great candidates for secondary metrics.
What if my secondary metrics aren’t where I want them to be?
If your secondary metrics aren’t at the target level, you need to assess whether that is as a result of your improvement efforts towards the primary metric. If the improvements you made are negatively impacting your secondary metrics, you need to go back and find a more viable solution.
Check yourself before you wreck yourself
Where the primary metric measures success, secondary metrics make sure that success does not come at the expense of something else. When looking to improve one area, it is important to make sure you don’t unintentionally derail progress in another area for the sake of reaching your primary objective. When it comes to metrics, remember to check yourself before you wreck yourself.