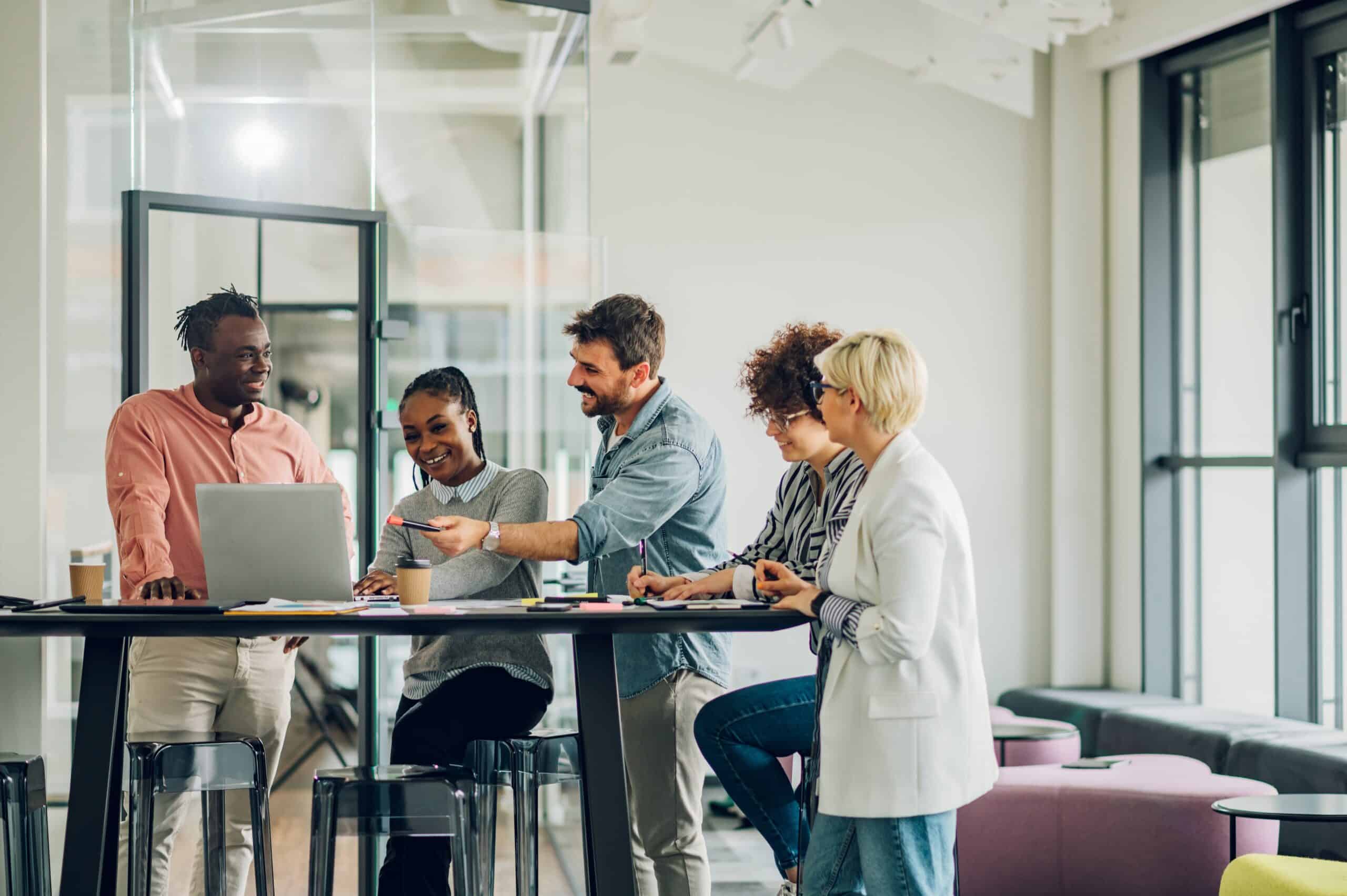
The web development team at The Nature Conservancy in Arlington, VA, was able to utilize Lean and Six Sigma tools to close the gap in downtime due to a coding freeze every 45 days.
The Nature Conservancy used such Six Sigma tools as process maps, The 5 Whys, and cause-and-effect diagrams to dramatically bring the organization’s lost code development time during a release cycle from 168 hours all the way down to 3 hours. That is a 95% improvement! Let’s look into The Nature Conservancy’s history with Six Sigma and how this project was decided upon.
The Nature Conservancy Had a Problem
The Nature Conservancy began in 1951 as a grassroots organization and, over the years, has become one of the largest non-profit environmental organizations in the world. The organization has over a million members, 400 scientists, and a large staff spread out over 79 countries and territories, along with every state in the United States.
The organization’s headquarters is located in Arlington, VA. At the organization’s headquarters, many decisions that affect all of the branches are made. It is also where the non-profit’s primary interactions with the world take place, including maintenance of its public-facing website.
Every month and a half, the web development team would handle a new release of its content management system. These new releases allowed the team to make updates to their website quickly and easily. The only problem was that while the team tested any new code related to the updates, there would be a code freeze for a week, which severely hampered productivity. Finding bugs that had to be eliminated could make the freeze even longer.
They Decided To Use the DMAIC Process and Its Sigma Tools
The senior IT business analyst, Tadeo Reyes, and his manager decided to tackle the problem. Already being a certified Lean Six Sigma Green Belt, it is likely that having an understanding of Six Sigma methodologies led him to use its tools in the improvement strategy.
This would also not be The Nature Conservancy’s first encounter with Six Sigma concepts. In 2006, a paper was published by Foundations for Success that detailed two years of meetings between board members of General Electric and the science staff of The Nature Conservancy’s Eastern New York branch. It is well known that General Electric has long been a champion of the Six Sigma methodology, and the meetings were to see how General Electric’s Six Sigma approach to a quality improvement system compared and contrasted with The Nature Conservancy’s own Conservation Action Planning Program.
While this was not the conservancy’s introduction to Six Sigma and its benefits, finding time to work on any changes was a key concern of the web developers. There was definitely reluctance to make any fundamental changes as the team was already bogged down by the errors that they were having to deal with. There was also pressure coming from the business side to not slow things down any further.
Upon meeting with the web development team, Tadeo worked towards pinpointing the root causes of the problem.
He used DMAIC, a cornerstone in Six Sigma methodology, and incorporated related tools like process maps, cause-and-effect diagrams, and the 5 Whys. Each of these tools is used within a phase of DMAIC. Process maps are tollgate #3 of the Define phase. Cause-and-effect diagrams are primarily worked with during the Analyze phase as are The 5 Whys.
With these tools, Tadeo found many significant errors and merge conflicts on top of the long freeze time. He learned that some environments were simply not being used whatsoever, while others were being used in ways that were unintended. He also found that the development team had no real system in place that allowed for quality assurance of their work. Code branches were also tightly packed and cluttered, and quick changes or fixes were not possible with the branching.
Upon demonstrating the need for improvement to the development team and the higher-ups, Tadeo received the go-ahead to address the problem. He worked along with the head web developer, and they came up with improvements. First up would be cleaning out the quality assurance environment as well as reassigning the development environment so that they could both be used as intended. Another improvement would be to update the branching strategy so that the development code branches could be broken out by feature, allowing for easier examination of code that had been approved. Lastly, a dedicated release branch would be created, allowing for constant development and integration.
The Outcome Was Monumental
By following Six Sigma methodology and making the necessary improvements, the web development team at The Nature Conservatory’s headquarters was able to drop the code freeze time from 168 hours (or an average of 7 days) all the way down to 2-3 hours. Not only that, but lost development time dropped to 1% from 16%. Developers could now test work without putting a stop to development. They could also now make fast fixes without having a negative effect on the testing and development that were in progress.
Together, these improvements cut down on downtime while also allowing developers much more time to focus on new features as well as on quality assurance.
The drive for improvement did not stop with the completion of the project. When working with Six Sigma, continuous improvement is part of the culture. This is seen in Tadeo’s further efforts after the completion of the project to then move on working towards wiping out the freeze time completely.
5 Best Practices When Convincing Higher-Ups To Utilize Six Sigma To Correct A Problem
Tadeo received pushback and skepticism when it came to convincing the development team and higher-ups to make the necessary changes that would improve the code freeze downtime. Ultimately, he received the go-ahead to move ahead and was able to succeed. Here are some best practices for convincing others that making changes is beneficial:
1. Success stories
Sharing success stories like this one can be a factor in getting your company to make the switch towards using Six Sigma in order to improve processes and improve the customer experience. There are plenty of examples available of organizations that have thrived utilizing the Six Sigma methodology, and the more examples that you are able to provide, the greater the likelihood of convincing the decision-makers. Try finding an example that an executive would find relatable, such as an organization of similar size and structure to yours. You can also provide examples of companies that your boss admires.
2. Training
Part of getting everyone onboard in your organization will have to do with providing the proper training. Everyone involved will need to have a total commitment to the method in order for it to have maximum success. This includes the higher-ups.
3. Consequences
While change might be feared, demonstrate the consequences that will result from not making improvements.
4. Continuous improvement
One major factor in being able to convince higher-ups to let you embark on a Six Sigma project is if you have prior experience in Six Sigma projects at the same organization in the past. Being able to demonstrate previous success and how your proposed project will lead to further improvements could carry a lot of weight.
5. Data-driven instead of intuition
A key part of the Six Sigma process is that it is driven by data analytics. Bosses generally trust hard data more than intuition. If you are able to present real company data that shows how Six Sigma can transform current processes for the betterment of the organization, you have a better chance of getting the approval of the higher-ups to proceed.
Six Sigma and The Nature Conservancy
Many mistakenly relegate the rewards that can be reaped from utilizing Six Sigma to large corporate entities. The Nature Conservatory’s success with the methodology is a great example of how the tools can be used in the non-profit sector. Six Sigma is a data-driven system that sets out to eliminate waste in an organization to improve processes and allow you to provide a better customer experience. All organizations have waste, so it stands to reason that all organizations could benefit from Six Sigma.
Many organizations also make the mistake of thinking that if their organization is at a certain level, its processes are what they are, and there is no need to improve. With such a large non-profit as The Nature Conservancy, the higher-ups likely were concerned about tampering with the processes of an organization whose way of doing things had gotten them to that point, whether or not the issues were causing them a significant amount of waste. It is important to remember that no matter how large an entity is, there is always room for improvement. The root causes of the code freeze at The Nature Conservancy were surprising, and some relatively small changes were able to bring it down by 95%. Just imagine what Six Sigma could do for you, whether your organization is small, medium, or large.