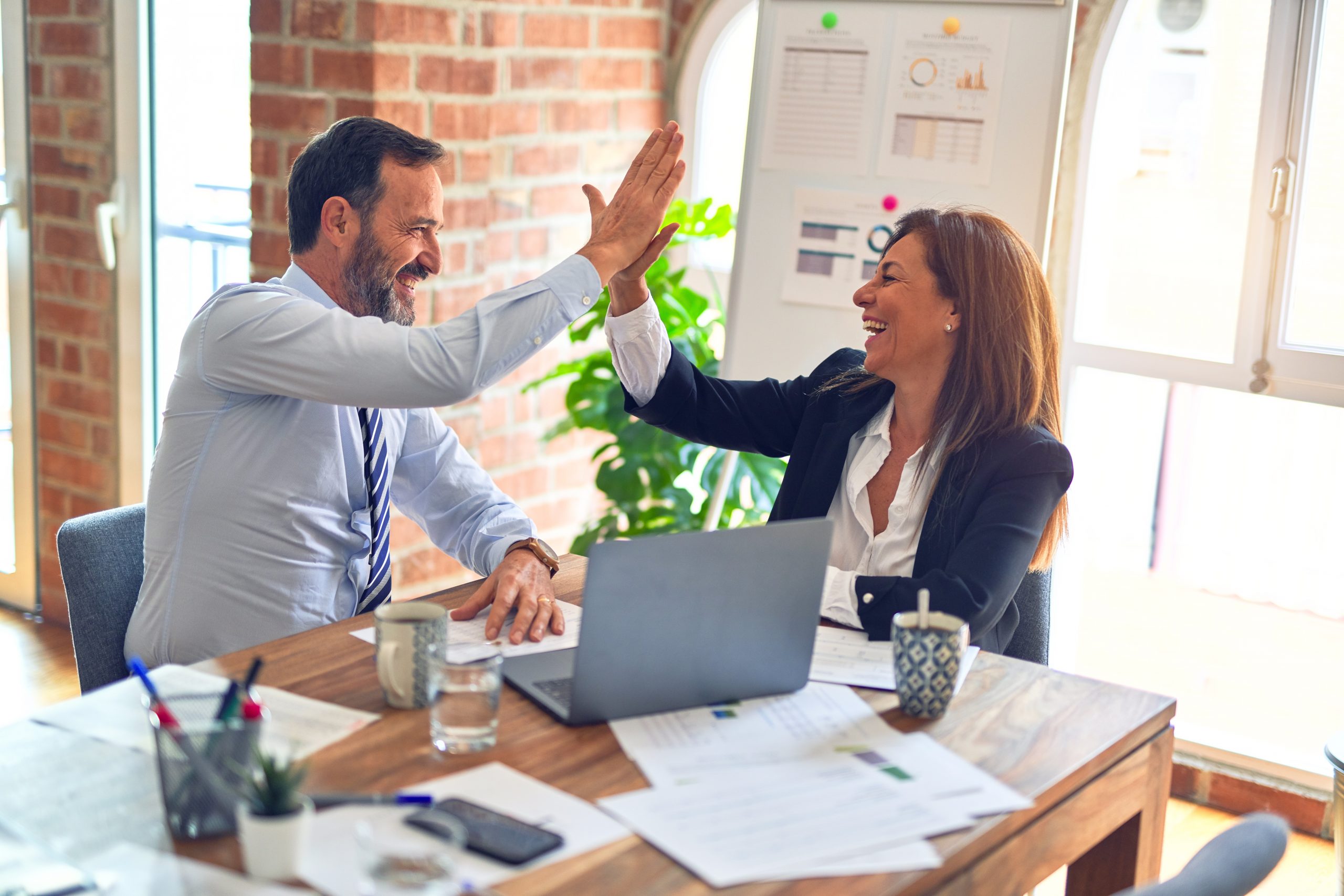
Recent Survey Shows Need for an Expanded Toolkit
It may be the most widely acclaimed performance improvement system across the business world, yet Six Sigma is not immune to a paradox common to most large-scale change efforts:
You can’t expect to sustain top executive support without producing consistent bottom-line results… yet consistent results aren’t likely without sustained top executive support.
This conundrum is a key finding from a recent survey of more than 240 Six Sigma practitioners across industries and around the globe. Sponsored by Leap Technologies, the survey was conducted anonymously over the web through iSixSigma.com, the leading Six Sigma information portal.
The survey used a combination of multiple choice and open-ended questions to gauge perceptions of Six Sigma practitioners on two primary issues:
- What causes Six Sigma projects to fail to produce desired results?
- What would most help to improve Six Sigma project results?
We know these are issues keeping practitioners up at night because these same people are under increasingly heavy pressure to produce and sustain bottom-line results from their projects.

The “CATCH 22” For Six Sigma Practitioners
Not surprisingly, the most often cited reason for Six Sigma project failure was “lack of sustained executive sponsorship and commitment.” It is clearly evident that there is no substitute for top leadership support to achieve sustained Six Sigma success. In close second ranking was “lack of buy-in, cooperation and ownership by frontline managers and employees for implementing and sustaining results on Six Sigma project solutions.” These top two barriers to success create a classic “Catch 22” for Six Sigma practitioners. On the one hand, executive commitment is critical to the funding and mandate Six Sigma practitioners need to challenge the status quo.

On the other hand, sustaining executive support is nearly impossible without consistent delivery of results. Yet this payoff can’t be sustained without active support by those most impacted by Six Sigma solutions…frontline managers and employees!
Six Sigma is, with its dedicated Belt infrastructure and standardized DMAIC methodology, a more sophisticated and effective approach than past quality improvement methods. But, if there is a chink to be found in Six Sigma’s armor, it is the issue of non-Belt participation and ownership. This problem, however, rarely surfaces in the first 12 to 18 months of a Six Sigma deployment. In fact, we’ve observed that, initially, many Six Sigma Deployment Leaders experience a false sense of security about results. Why? Because most of the projects taken on by newly trained Black and Green Belts rarely require high levels of frontline support and, for the most part, don’t challenge top management’s ingrained cultural biases.
At the same time, it’s also not uncommon for organizations adopting Six Sigma to “hit the wall” once “low touch” projects are completed. Top management’s appetite for results has been whetted, but the foundational support in terms of skills, experience and commitment may not be there to tackle the projects that present bigger change management challenges.
More Tools Are Needed
The “Help Needed Wish List” of Six Sigma practitioners generated from our survey supports our hypothesis about Six Sigma initiatives hitting the wall. Survey respondents were asked to rate a list of tactics and tools that they perceived would most help them improve Six Sigma project results. Topping the list were:
- A structured toolset for engaging frontline employees and managers in Six Sigma projects, particularly those with significant behavior change requirements
- More tactics and techniques for reducing Six Sigma project cycle times without undermining effectiveness of solutions
- A simple model for integrating Lean, Innovation and Change Management tools with the core DMAIC framework
According to the Six Sigma practitioners completing the survey, the path to better Six Sigma project results requires equipping practitioners with an expanded set of tools to both tackle more complex projects and improve Belt productivity by getting more non-Belt involvement. This finding is not likely to be a revelation to many of the early pioneers who paved the way to the popularity of Six Sigma. Companies like Motorola, Allied Signal (now merged with Honeywell) and GE, along with other big players, such as DuPont, and 3M (among others), have already taken steps to strengthen their Six Sigma Deployments by enhancing the skills of Belts and expanding the tool kit.

At the same time, the survey results indicate there is more work to do in advancing Six Sigma into a robust and sustainable method for transformational change. The top priority appears to be the expansion of the Six Sigma practitioner’s tool kit to break free of the “Catch 22” syndrome. In fact, the integration of Lean principles by numerous Six Sigma users is a big step in the right direction. However, in addition to Lean tools there also appears to be a growing recognition that more tools are needed to deal with the change management aspects of Six Sigma. Ninety percent of the survey respondents rated the need for a structured tool set for engaging “non-Belts” in projects, particularly those with significant behavior change requirements.
The preceding finding is linked to the second most important reason practitioners stated as the cause for Six Sigma projects falling short (i.e., lack of buy-in, cooperation or ownership by frontline employees and managers). The relationship between these two findings correlates with the anecdotal evidence from more experienced Six Sigma organizations about the keys to accelerating results and reducing project cycle times. As they move down the experience curve and tackle larger and more complex change projects, the most successful Six Sigma organizations have expanded their tool sets and integrated other improvement disciplines such as Lean and Workout seamlessly into deployments.
The Keys to a Better Night’s Sleep
Six Sigma practitioners can break free of the “Catch 22” syndrome by designing their deployments to both deliver consistent results and sustain consistent executive support. The keys to managing this seeming paradox are:
- Expand the tool set early in deployment with methods to get more non-Belt participation and faster results. The key to avoiding confusion or overload is to integrate Lean, Innovation, Workout and other improvement methods into the DMAIC framework versus side-by-side competition.
- Engage senior leaders to go beyond the rubber-stamping of project selections to actually designing the project plan with the Belts. The benefits are a more realistic appraisal of project requirements and deeper understanding of where and how to apply other tool sets to drive bigger and faster results.
- Engage non-Belt managers and employees early on projects where there is existing motivation for change. More specifically, front-load projects that are likely to improve the work environment and improve morale along with the more traditional “low-touch” defect reduction projects.
Taking actions such as these will provide a steadier stream of results, sustained executive support and, just as importantly, ensure a better night’s sleep for Six Sigma practitioners!