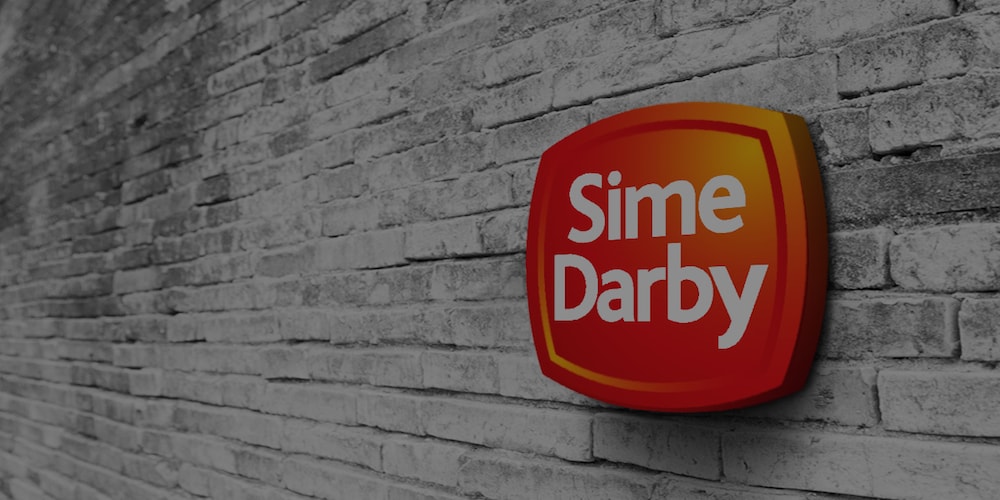
Who Is Sime Darby Plantation?
Sime Darby Plantation is the world’s largest sustainable palm oil producer and has four areas of focus:
- Upstream: 248 estates and 72 mills where fresh fruit is processed into crude palm oil
- Downstream: Production of oils and fats, oleochemicals, biodiesel, other palm oil derivatives and renewables in 16 countries
- Research and development: Developing technologies to improve plantation yields, milling processes and customize downstream products
- Renewables: Investment and development of innovative technologies in the bio-chemicals, nutraceuticals and wellness, and bio-energy spaces
Organizations cannot afford to focus only on the tactical side of Lean Six Sigma (LSS) deployments (i.e., developing learning modules and training for practitioners). Realizing the full potential of a deployment also requires a focus on strategic and cultural approaches to unite all employees. As a team, the organization will benefit and move toward improving revenue generation, implementing cost savings and cost avoidance practices while also embracing effective capital management discipline.
Before the launch of its LSS business management strategy in 2013, the Sime Darby Group recorded savings from its LSS program of less than $4 million (all dollars listed are U.S.) annually, largely derived from the Plantation division’s efforts. As a result, the value of LSS to Sime Darby was questioned by senior management.
Cost Savings, Cost Avoidance and Revenue Driver
In answering that challenge, the team led by Mr. Azman Shah Mohamed Noor, Master Black Belt, vice president and head, Operational Excellence of Sime Darby Plantation carried out an intense benchmark study on the value and returns of deploying LSS. One of the study’s references, a quote from an article in iSixSigma Magazine, stated that “Six Sigma deployments contribute an average 2 percent of total revenue per year for about 53 percent of Fortune 500 companies.”
In 2012, the revenue generated by Sime Darby was approximately $10 billion. Two percent of the total revenue translated to a potential $200 million LSS contribution in benefits (cost savings, cost avoidance and improved revenue generation) in just one year. Striving to be within the ranks of Fortune 500, the team proposed its first LSS target for Sime Darby: to contribute 1 percent of total revenue ($100 million) in its fifth year of deployment, which translates to $200 million in cumulative benefits over the course of the five-year implementation. Out of the cumulative benefits of $200 million, $62 million was to be delivered by Sime Darby Plantation, the Group’s biggest arm. The target represented the measurement of the LSS paradigm shift in Sime Darby, transforming from a statistical improvement tool into an effective business management strategy.
With more than 120,000 employees and world-class involvement in five different industries – plantation, industrial equipment, motors, property and logistics – spanning 26 countries and 4 territories, Sime Darby was a diversified multinational conglomerate. Would this improve or diminish Sime Darby’s chances to achieve the target?
The deployment of Sime Darby’s LSS business management strategy centered around a holistic approach that focused on strategic stewardship, tactical development and cultural transformation to deliver sustainable value to all stakeholders. Holistically, Sime Darby’s LSS strategy was employed to achieve operational excellence benefits in terms of cost savings, cost avoidance and revenue generation.
Strategic Stewardship (Vision and Commitment)
The strategic approach of the deployment involves the development of a strategy blueprint as well as divisional roadmaps. The blueprint encapsulates the various stages involved and key success factors of the deployment in achieving specified target.
Due to the unique nature of each division, the LSS deployment within the Sime Darby Group was customized in accordance with each division’s roadmap to support the larger blueprint. “Operational excellence through LSS is a key enabler in delivering Sime Darby’s sustainability purpose of contributing to a better society (people), minimizing environmental harm (planet) and delivering sustainable development (prosperity),” said Dr. Simon Lord, chief sustainability officer, Sime Darby Plantation. The LSS benefits target was also incorporated as one of the critical categories of the Sustainability Leadership Index which was being carried by all divisional managing directors.
Governance structures were also developed to track and show accountability of LSS operationalization. The LSS working committee – LSS Black Belts and representatives from each division – allowed for collaborative cross-divisional platforms to align with shared goals.
Tactical Development (Skills Development)
The tactical approach involves capacity and competency building, and the development of learning modules that cater to different levels of project complexity. Trained practitioners would then leverage these modules to improve their own processes.
Sime Darby established White, Green and Black Belt programs that allow practitioners to be certified. The certification of employees adds value to not only Sime Darby’s business and operations, but also to the employee’s personal career advancement. Sime Darby’s Black Belt program caters to the development of young leaders and internal consultants with modules focusing on advanced statistical tools and leadership skills, change management, effective communications, enterprise-wide strategic deployment, operational excellence and innovation.
In reporting the true value of an LSS project, an LSS Benefits Guideline was developed to guide the teams in translating improvement outcomes to benefits. A finance representative was included to validate the recorded benefits.
Cultural Transformation (Change Within)
The cultural approach was accelerated with Sime Darby’s call to action to embed its six winning mindsets within the organization:
- Deliver results
- Customer first
- Value talent
- Build trust
- Continuous improvement
- Empowered decisions
In 2015, Sime Darby launched an organization-wide “War on Waste” program and formally established its first form of culture change measurement. The War on Waste program targeted participation from a total of 525 operating units within Sime Darby to undertake continuous improvement initiatives using Kaizen.
In order to reach each employee and operating unit, the team moved away from traditional, physical workshops and used tools such as infographics, e-learning modules, organization-wide engagement bulletins trailers, Kaizen workshops and videos of leaders reiterating their commitment to the LSS program to ensure extensive and meaningful communication with all. The measurement for change in continuous improvement culture was represented by the rate of participation by all operating units. The War on Waste program implementation showed an increase in participation from 29 percent in its inception to 49 percent in its second year.
The culture of continuous improvement was also demonstrated by senior management. For example, the president and Group CEO of Sime Darby has actively championed the program and his commitment was cascaded throughout the organization. LSS initiatives and progress are monitored by both internal and external assurance entities, reported at board level and consistently communicated in Sime Darby’s annual report as the company’s number one performance strategy.
Goal Exceeded
Over the course of the five-year period, the Group saw a total of $250 million in cumulative benefits (including revenue) – exceeding its initial target of 1 percent by a full 25 percent!
Efforts at Present
Following the success of the LSS business management strategy by the now de-merged Sime Darby Group, Sime Darby Plantation (separate from Sime Darby Property and Sime Darby Holdings) has ensured continuity of the Group’s success by launching the second phase of the strategy. Operational Excellence & Innovation Business Management Strategy (OEIBMS) 2.0 plans to deliver $140 million in cumulative benefits by 2022, approximately 57 percent more than what the company achieved over the last five-year period as a division within the Sime Darby Group.
In line with Sime Darby Plantation’s vision of becoming the leading integrated global plantation company, the strategy is comprised of four key programs:
- Clone protocol to replicate previous high-impact projects at other sites
- Lean Palm (launched with the second phase) to expand the operational excellence footprint to cover all regions of operations
- Universal learning to enhance accessibility of LSS resources by leveraging technology
- War on Waste to eliminate inefficiencies by promoting cultural transformation with regards to waste elimination
To learn more about Sime Darby Plantation, click here.