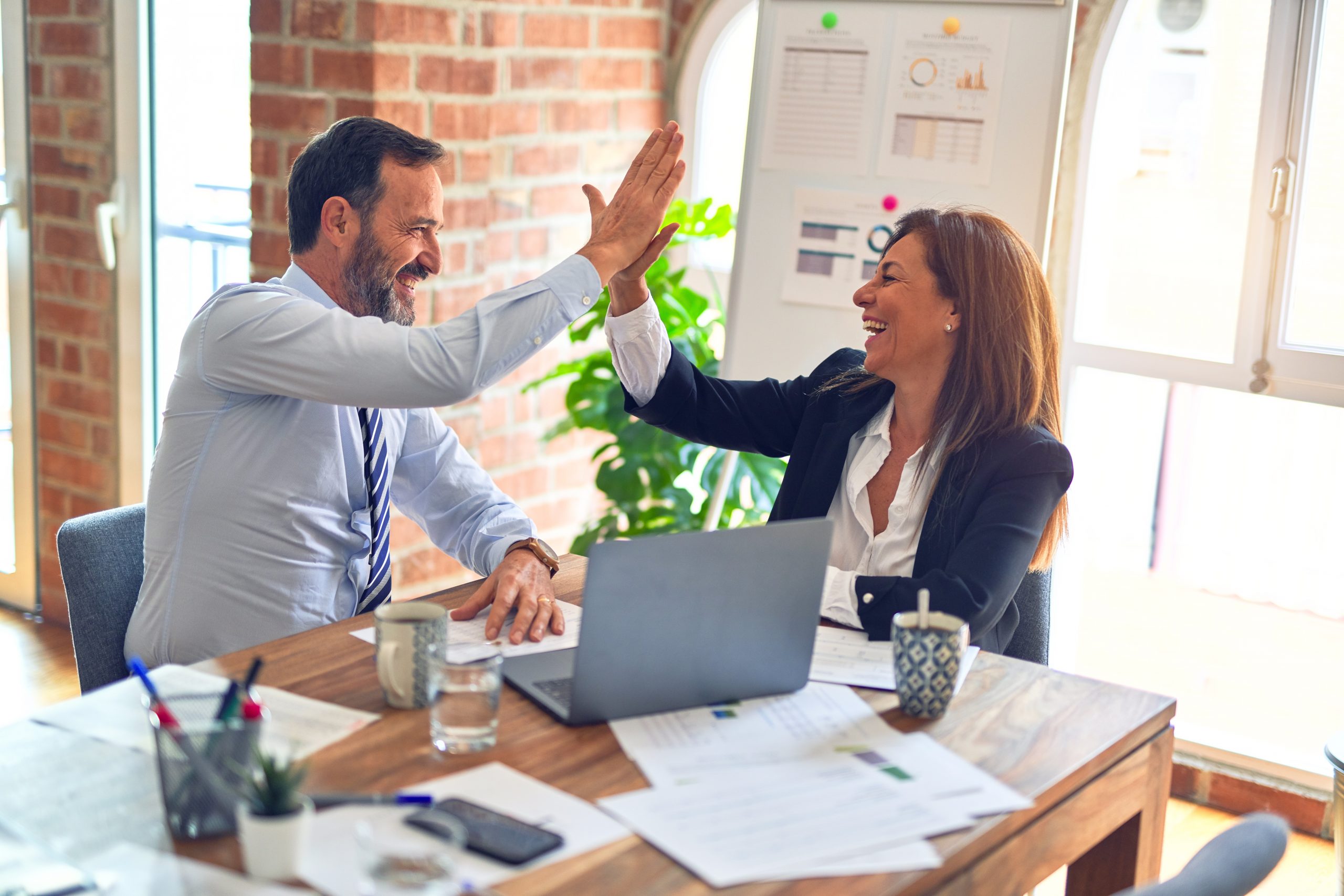
Control charting is a tool used to monitor processes and to assure that they remain in control or stable. Proposed by Walter Shewart in 1924, control charts help distinguish process variation due to assignable causes from those due to unassignable causes.
Table 1: Types of Process Variation Found on a Control Chart | |
Types of Variation | Variation Characteristics |
Assignable cause, also known as special cause |
|
Unassignable cause, also known as common cause or chance cause |
|
Elements of a Control Chart
A control chart consists of:
- AÂ central line,
- An upper control limit,
- AÂ lower control limit, and
- Process values plotted on the chart.
If all process values are plotted within the upper and lower control limits and no particular tendency is noted, the process is referred to as in control. If the process values are plotted outside the control limits or show a particular tendency, however, the process is referred to as out of control (see red-circled data points in Figure 2 below).

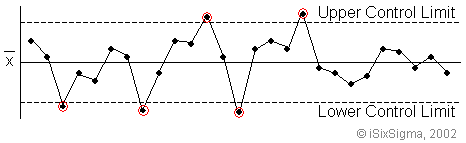
There are many types of control charts. In a future article, we will investigate the different types of control charts by process values and purpose.
In a control chart, control limits are calculated by the following formula:
(average process value) (3 x standard deviation)
where the standard deviation is due to unassigned process variation only.
Constructing a Control Chart
Here is the general process for making or constructing a control chart for your process:
- Select the process you would like to chart
- Determine your process sampling plan
- Collect data from your process
- Calculate the control chart specific statistics
- Calculate your control limits
- Construct your control chart