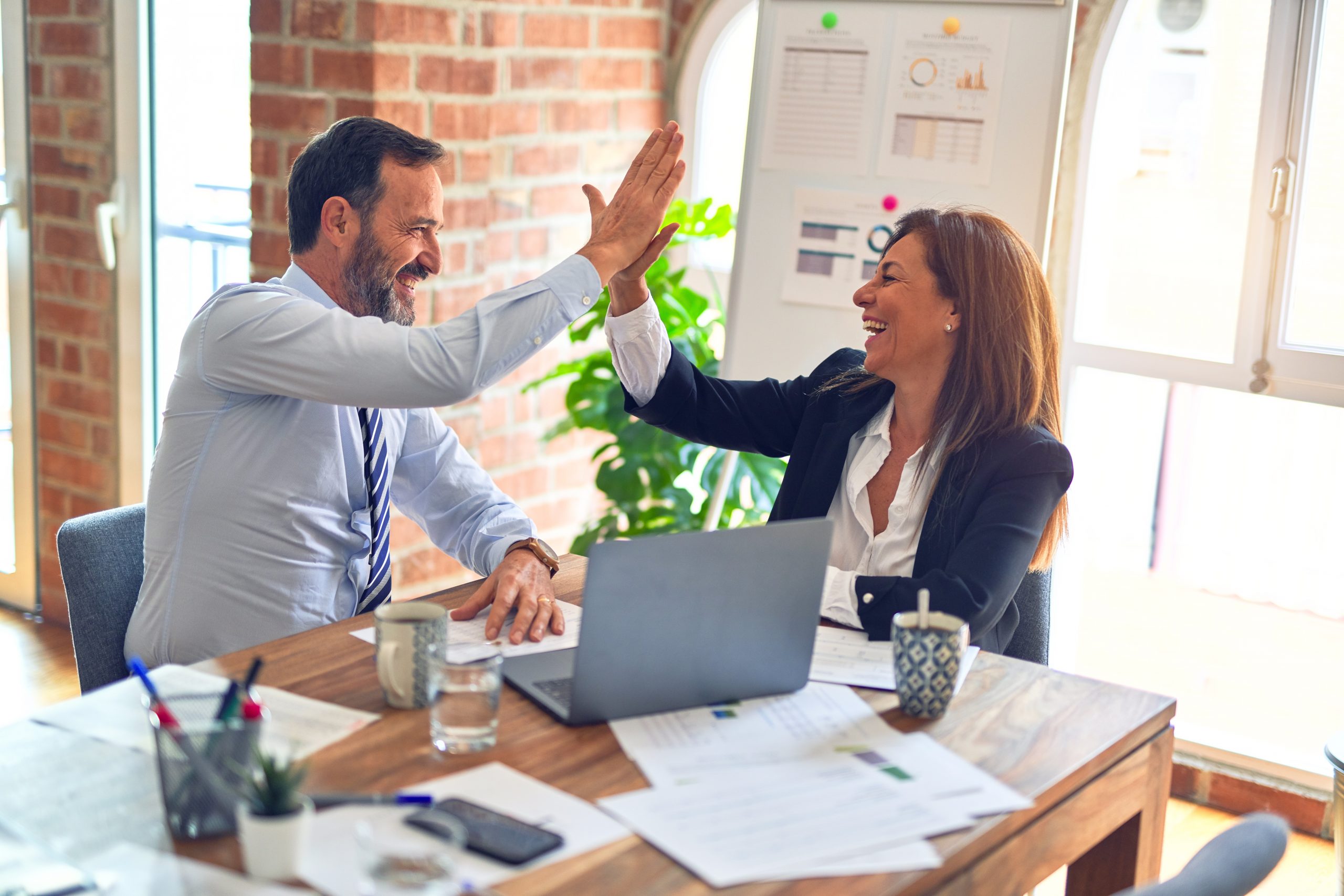
Whirlpool started to investigate Six Sigmashortly after GE and at least a full year ahead of Maytag. Named Operational Excellence, the initiative went corporate-wide in 1997 and involves a blend of methodologies. Just like clothes need a washer and dryer to get clean, Whirlpool has been using Six Sigma and Lean to scrub away inefficiencies. The latest savings reporttotaled $175 million in the first three years. Operational Excellence at Whirlpool does more than just cut costs, it has alsobeen known to shorten cycle-times while increasing quality and productivity. Today, Whirlpool focuses on Customer Centered Operational Excellence (ccOPEX). You can bet Whirlpool’s suppliers know a thing or two about Six Sigma as they have extended training to includethem.
Savings and Benefits
“Since 1997, we have successfully applied Six Sigma and Lean Manufacturing processes across our global operating platform, and certified over 1,500 black belts and master black belts. Consequently, we are generating millions of dollars in annual cost savings.
“Quality and productivity remain vital value creating levers for the company and are a key focus of our global operations. Operational Excellence, our Six Sigma process, and Lean Manufacturing are the tools we use across the enterprise to continually improve productivity and sustain cost savings.”
2004 Annual Report
“Whirlpool’s tradition of driving continual improvements in quality and productivity remains a key focus of our operations and a vital competitive lever. In 2003, productivity improvements by our North American and European operations reached record levels. Operating Excellence, our Six-Sigma process, is the tool we use to improve and sustain these cost savings.”
2003 Annual Report
“To sustain the productivity savings that are being achieved by our operations, we have embedded our Operational Excellence process – based on Six-Sigma and lean manufacturing skills and capabilities – within each of our worldwide manufacturing facilities. Based on these capabilities, our operations turned in a record improvement in total cost productivity in 2002. A parallel process is being instituted across the entire enterprise in an effort to eliminate additional costs and to create as many resources as possible to invest in innovation that builds customer loyalty to our brands.”
2002 Annual Report
“By working from a global platform, our company can drive key operational initiatives for maximum impact. This includes the company’s customized Six Sigma methodology, known as Operational Excellence, which ensures that we consistently improve our quality levels, even as we lower our costs and shorten cycle times.
“By creating breakthrough solutions for our most difficult challenges, Operational Excellence has generated more than $175 million in global manufacturing savings during the last three years.”
1999 Annual Report
“And we continued to benefit from our Operational Excellence program, Whirlpool’s “Six Sigma” methodology for improving quality in processes, while also significantly enhancing productivity, reducing costs and shortening cycle times across the enterprise. Today more than 70 people have been certified as “experts” in Operational Excellence, which uses sophisticated analytical methods to drive fundamental improvements. This program has already produced significant cost and quality results in North America, and during 1998, we began to expand its use at our other regional businesses.”
1998 Annual Report
Articles and Links
IXPERION Conference, Master Black Belt Douglas Rodriguez spoke on the application of Six Sigma to Whirlpool’s hedging process, Apr 2005
IQPC Business Process Excellence & Six Sigma for Retail Conference, JD Rapp, Director Customer Centered Operational Excellence at Whirlpool, will be speaking on improving customer service while Master Black Belt Ben Brotzki will speak about customer loyalty. August 23-24, 2005, Atlanta, Georgia, USA
A Six-point agenda, The Hindu Business Line, March 15, 2004
Whirlpool aims to cut costs 5% annually, Purchasing.com, August 9, 2001