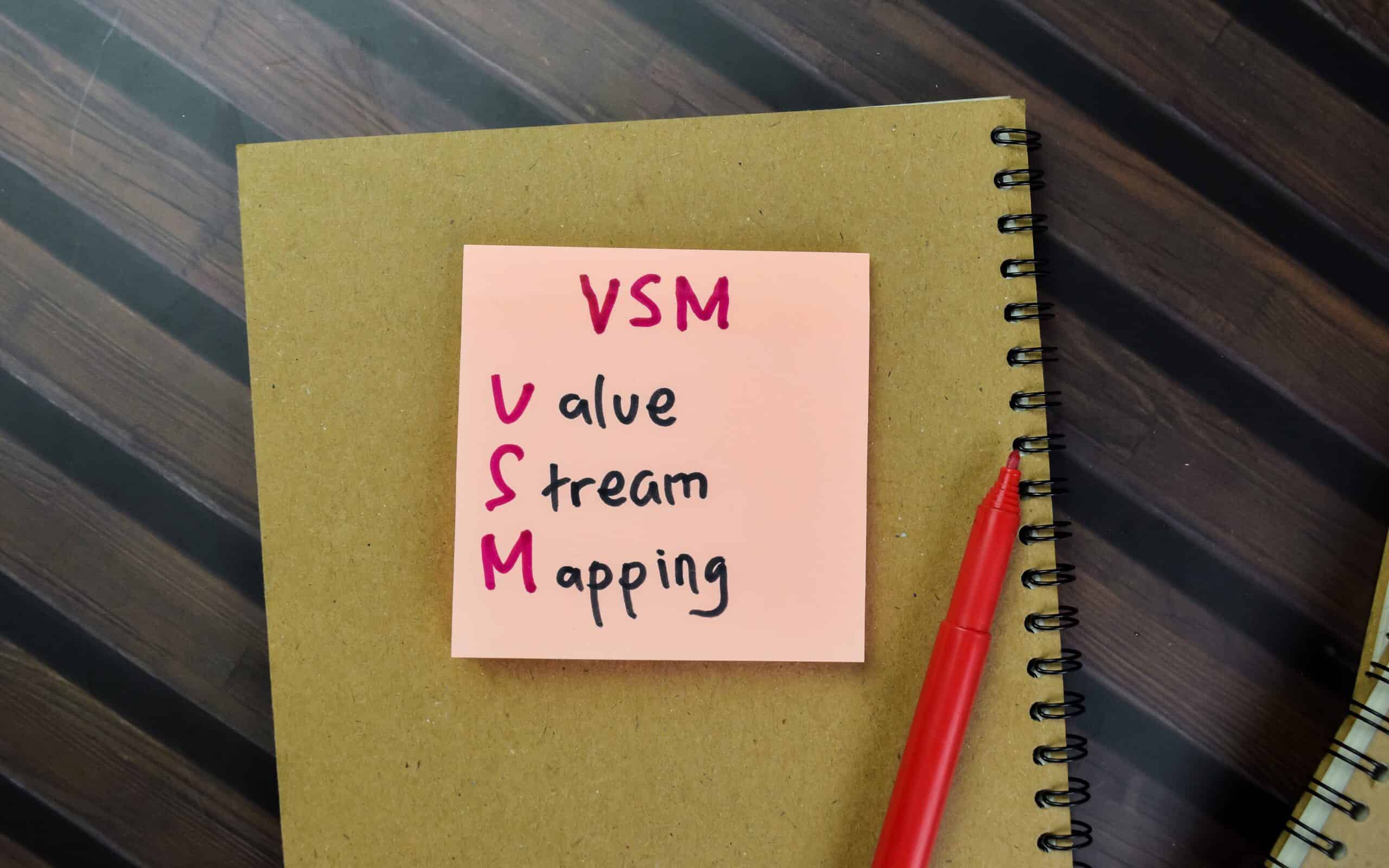
You are a new manager, responsible for making sure the process satisfies your customers time and quality expectations. So, what exactly do we do, here? What is the work, from a high-level perspective, that is done to get the customer what they want? Looking around, the process almost seems impossibly complex to understand. There are so many moving pieces. How does one person get a better understanding of the big picture? One does so by creating a value stream map.
An overview: What is a value stream map?
A value stream map is a high-level visual representation of the processes involved in delivering a product or service, with the purpose of identifying and eliminating the waste within the system.
By themselves, these maps will not be able to identify the root cause of a problem, but they do help identify bottlenecks within the system. Bottlenecks in the system should be examined first, as the throughput can only be improved in the overall system if the improvement is made to the bottleneck.
The map holds many components. The first is a general flow of the product or service, demonstrating the flow from one process to the next. Each process block will contain key metric information for the process. Inventories between each process step are included, as well as their metrics.
The value stream map provides key inputs and outputs of work, materials, and information flows from supporting departments, suppliers, and customers. It helps by creating a better understanding of the customer requirements and demands, as the process both starts and ends with the customer.
Image source: Breezetree.com.
Value stream maps utilize a system of symbols that help communicate the information quickly, designating concepts such as push versus pull systems, inventory supermarkets, physical versus electronic sources of data, FIFO, and more.
RELATED: SPAGHETTI DIAGRAM VS. VALUE STREAM MAPPING
3 benefits of attending to value stream mapping
A value stream map allows you to communicate the high-level view of the current state of a system in an efficient way. It assists by communicating various key pieces of information as well as the bottlenecks to all parties involved.
1. Communicates the overall value stream quickly
A value stream map is an extremely efficient method for communicating the high-key features of a complicated system. It shows not just how the product or service travels along the processes, but it also demonstrates where it sits, unproductive, in the system. The map clearly shows what inputs are used at each process as well as the support department that supplies the information, a great benefit as many organizations do not have a clear understanding of how their support systems tie in to and add value to the system.
2. Identifies key bottlenecks of complicated systems
The value stream map is a key early step in identifying where process improvement efforts should be focused. Once completed, it’s used to identify the greatest delays in time.
The map highlights issues with availability, yields, resource constraints, and other factors that delay the completion of the product or service.
Using this information, the worst offending issues can be identified, providing data verifying the bottleneck of the process. Process improvement efforts need to address the bottleneck in order to expect an overall improvement to the system as a whole.
3. Gets various departments a unified understanding of the system
When working on reaching an improved future state, the unification of many different departments is required. A value stream map is a powerful tool that can help make complicated systems easier for all departments to understand. This understanding can lead to better levels of cooperation between these departments.
3 value stream mapping best practices
1. Hold an event
Because of the intense amount of data needed to create a value stream map, you might want to hold an event to collect key process owners for the creation of the map. Having the team members communicate together during the creation helps minimize the errors, especially regarding how inputs and outputs between departments occur. It also helps get definitions standardized and helps reach buy-in with the results.
2. Physically map it out first
When creating the value stream map, start by mapping it using a large blank wall space and some sticky notes. This allows multiple department representatives to make additions and corrections easily during development. After a solid rough draft has been developed, begin migrating the map into an electronic form so the information can be documented and shared easier between departments — and to help develop the future state plans for the value stream.
3. Focus on the current state
When creating the map, be sure to focus on the current state. You should be confident that the current state has been accurately represented prior to trying to make improvements. Remember that this tool identifies bottlenecks, not root causes, and understand that finding the root cause is paramount to developing the correct solution.
RELATED: VALUE STREAM MAP VS. PROCESS MAP
Frequently Asked Questions (FAQ) about value stream mapping
How much detail needs to be included with each process step?
Each process block shown on the value stream map represents a greater number of smaller steps. The value stream map should not go into granular details regarding a process, like you would when making a process map. The process map should include critical metrics regarding each process block, such as yields, manpower levels, downtime, etc. The value stream map is the high-level tool used to see the bigger picture. It helps identify the bottleneck but does not provide the root cause of the bottleneck. You’ll need other process improvement tools to determine the root cause.
How often do I need to revisit a value stream map for updates?
It’s important to keep an up-to-date value stream map, though it will not require daily corrections. Every time a major process improvement is implemented, the map needs to be corrected to reflect the change. Also, it is advised to update the metrics of the map every month or so. As data and flow changes, the potential of the bottleneck moving to a different part of the process exists, which in turn directs the company towards that area for future process improvement efforts.
We have multiple products at our company, many with different value stream map flows. Where do we start?
This question can have different answers depending on your company’s goals. Start with a product that is predicted to make up a significant amount of the company’s revenue in the short- and long-term future. Beware of performing on a product with poor definition, as it will require a lot of effort to keep the value stream map updated and accurate.
Value stream maps provide a high-level understanding of a business
Value stream maps are a great tool for communicating complex business systems using a simple-to-understand visual method. They are a great tool for identifying bottlenecks, identifying where limited process improvement resources should be allocated. The maps are key in getting departments together to understand the true current state, assisting departments in improving how they interact with each other.