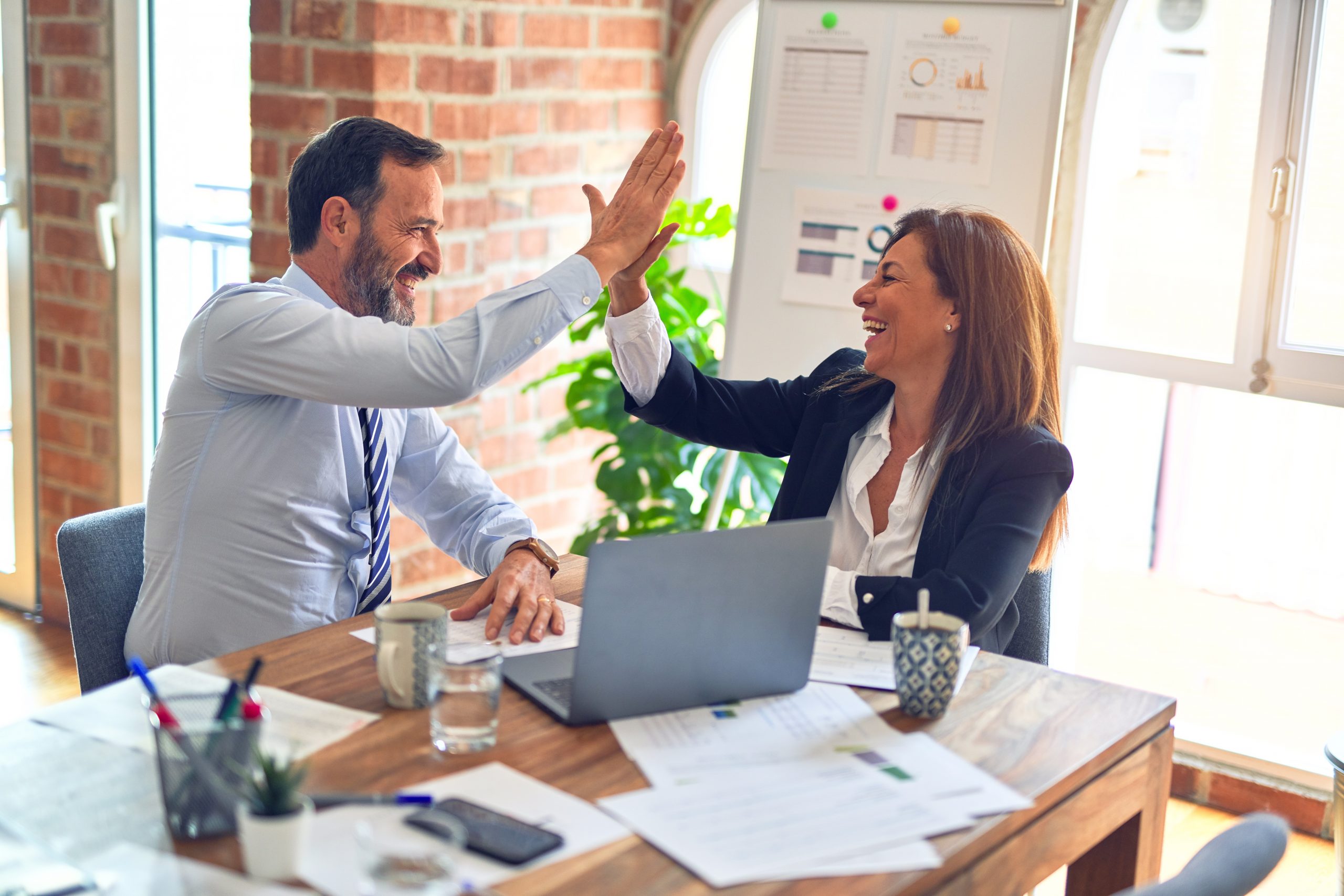
Cummins Inc. began using Six Sigma and Design for Six Sigma (DFSS) in 2000. In April 2004 they completed their 2,000th Six Sigma project and in the same year began working on Six Sigma projects with customers. Cummins is featured in the Corporate Leadership section of the July/August issue of iSixSigma Magazine. In the article, Ernest Lifferth, DFSS Leader for Cummins, details the progress they have made since deploying DFSS and describes the ways Cummins is using DFSS to develop new products and “solve those production problems that just won’t go away”.
Savings and Benefits
“Our successful Six Sigma program will continue to drive cost savings and quality improvements, while serving as a leadership development tool for employees.
“In 2004, we began to do Six Sigma projects with customers to jointly focus on the improvements that mattered to them.”
2004 Annual Report
“In the second half of the year, our businesses were generating a profit largely due to increased sales and ongoing cost-reduction efforts, especially our Six Sigma initiatives.”
“Our ongoing use of Six Sigma, a disciplined approach to drive rapid process improvement, has resulted in approximately $400 million in cost savings since January 2000 when we launched this program. In addition, we have trained 1,300 employees in Six Sigma practices and processes. These initiatives to improve quality, manage spending and relentlessly cut costs will continue even as our markets begin to trend upward after a three-year recession.”
“Our focus in 2001 remained on cost reduction and cash management. The cornerstone of our cost reduction effort is Six Sigma, a quality improvement program that uses statistical tools and a disciplined approach to drive rapid process improvement. Since the program began in 2000, more than 700 Cummins employees trained as “belts” have delivered $100 million of savings with substantial improvements in product and service quality.”
“Reducing the amount we pay for quality issues associated with some of our new products is also a focus, and we have implemented a quality improvement program called Six Sigma. Led by project leaders called Black Belts and Green Belts, Six Sigma uses statistical tools and a disciplined, logical approach to drive rapid process improvement. We now have more than 100 Black Belts and 170 Green Belts working on improvement projects. The completed projects have already resulted in an additional $27 million to the bottom line, exceeding our first-year goal by $2 million.”
Articles and Links
The 14 Million Dollar Woman, Quality Digest, May 2005
Six Sigma with Energy and Enthusiasm at Cummins, Inc., iSixSigma.com, Apr 2005
Top Six Sigma Projects on Display at Cummins Expo, Forbes, March 31, 2005
Quality Time, Minnesota Technology Magazine, Spring 2005
Six Sigma helps marketing improve design, save money, B to B, November 8, 2004
Cummins Case Study, The Times 100, Jan 2003
Case Studies: Cummins Witnesses Savings, Quality Magazine, May 9, 2003