Category: SIPOC/COPIS
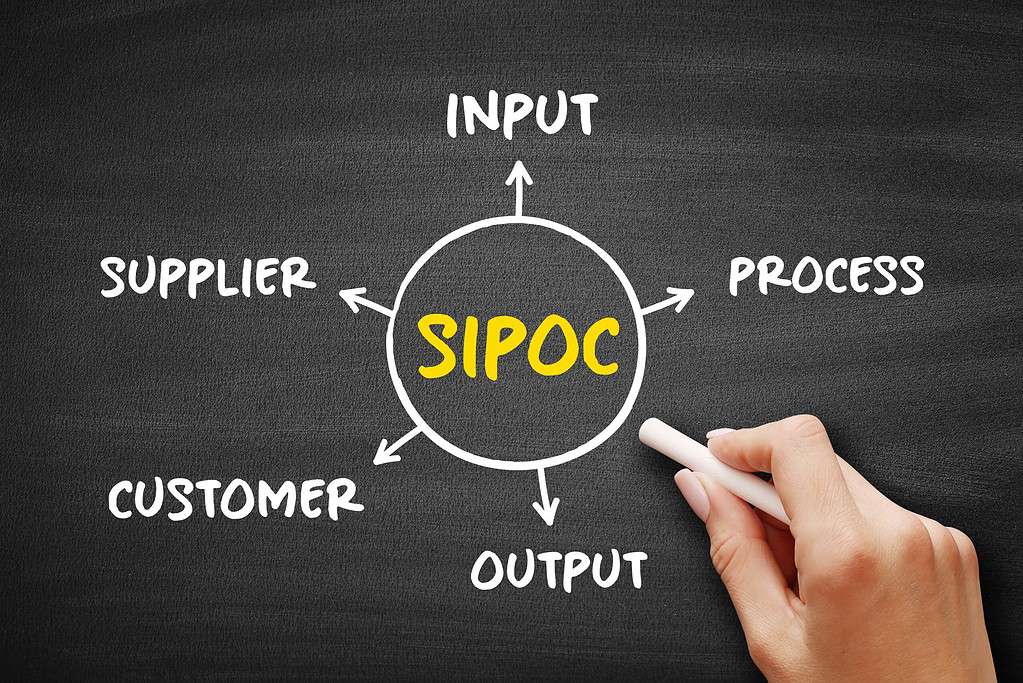
Get Your Team Up to Speed with the SIPOC Diagram
Published:There are a few different ways you can improve a process in your business. Before you get to work with implementing these changes, it does help to visualize the entire thing. A SIPOC diagram is a highly useful tool for mapping out the steps of a process. Processes and projects are complex, but a SIPOC […]
Read more ยป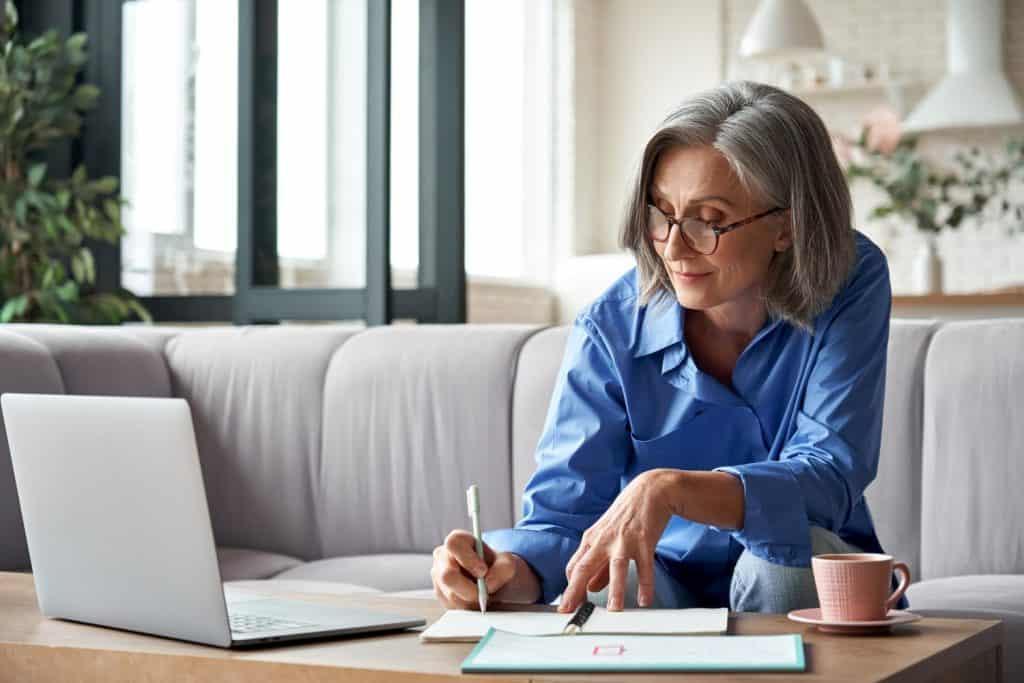
Driving Lean Six Sigma in Hybrid Workplaces: Overcoming Communication Barriers
Published:The workplace landscape has undergone a dramatic transformation with the widespread adoption of hybrid work models. This shift, accelerated by the global pandemic, combines remote and in-office work, offering employees flexibility and autonomy while enabling organizations to reduce operational costs. However, this model also presents unique challenges, particularly in communication, collaboration, and process […]
Read more ยป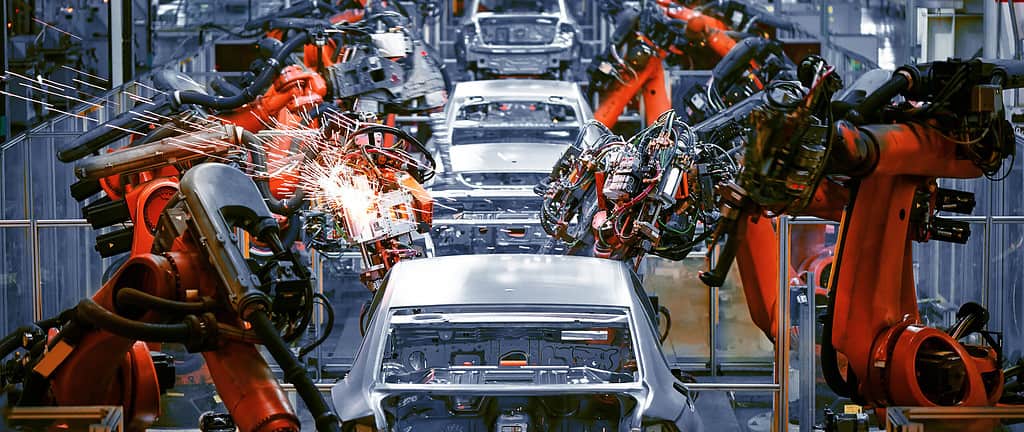
Real-Life SIPOC Examples in Manufacturing
Published:What are some real-life SIPOC applications in the field of manufacturing? While Lean Six Sigma tools and methodologies can be applied to any industry, they truly excel when pointed toward something like manufacturing. When you get right down to it, manufacturing is one of the most complex undertakings a business can undergo. What […]
Read more ยป
Is SIPOC Still Relevant? 9 Alternatives
Published:Is SIPOC still worth using? Lean and Six Sigma have many tools for improving or designing new processes. You’ll see SIPOC diagrams often touted, but there are other tools where you might find they are better suited for your needs. Today, we’re looking at a few alternatives that might just fit the bill […]
Read more ยป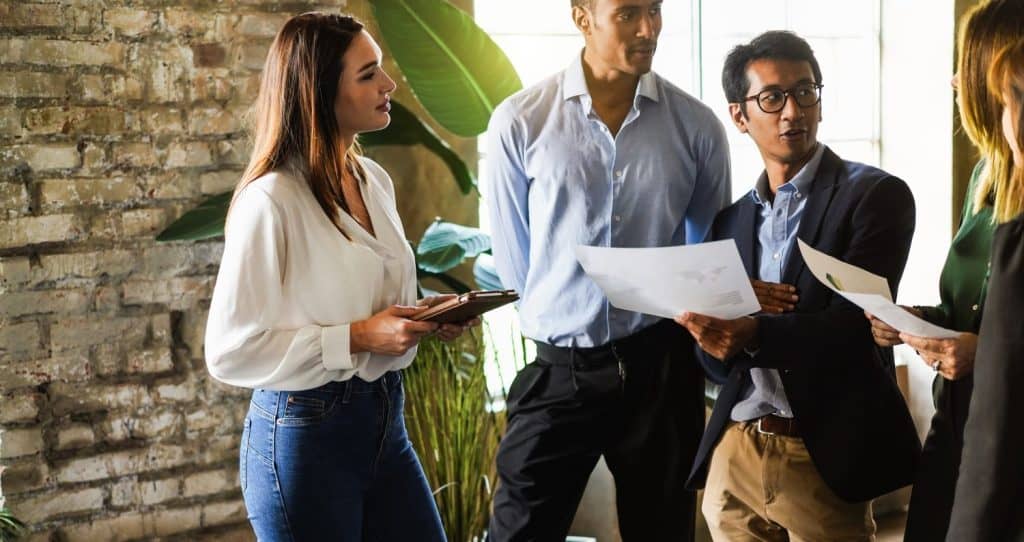
How to Create a SIPOC Diagram: Step-by-Step Guide
Updated:How do you create a SIPOC diagram? Now, I imagine this is a moot point for many LSS practitioners with any degree of experience. However, this might seem somewhat daunting at first glance for newcomers to the methodology. As such, it certainly helps to take a step back and learn some of the […]
Read more ยป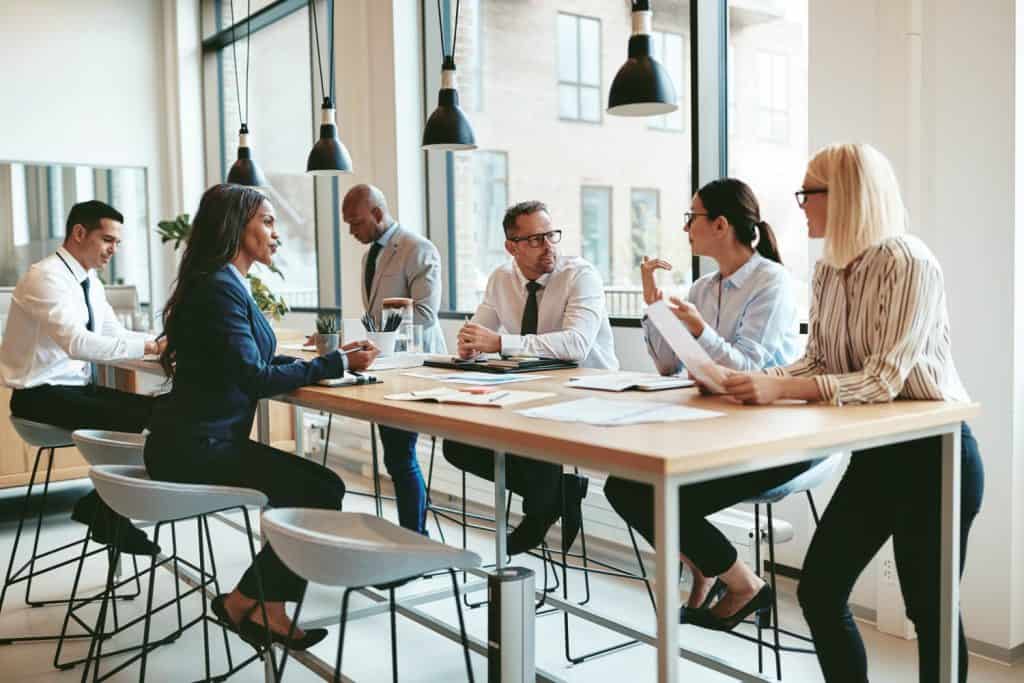
Why SIPOC Diagrams Are Crucial for Lean Six Sigma Projects
Updated:Why should you start a SIPOC diagram at the start of your Lean Six Sigma Projects? Many facets go into planning and executing a project. The last few years have seen the rise of software-centric methodologies like Agile and DevOps, which have become prominent outside of the tech industry. However, SIPOC diagrams remain […]
Read more ยป
Insights from COPIS for Improved Efficiency
Published:What does your process look like from 30,000 feet? Your extended process view can be described using COPIS, or customer, output, process, input, and supplier. Letโs get in our balloon and go up.ย
Read more ยป
Revolutionizing Organizational Change with the CAP Approach
Updated:Do you feel that implementing change in your organization is going too slowly? So did Jack Welch of GE, which is why GE developed the Change Acceleration Process (CAP). Letโs explore how the concepts of CAP might help your organization.
Read more ยป
Common Mistakes When Using SIPOC
Updated:What are the most common mistakes when using SIPOC? The SIPOC Diagram is one of the most useful tools in your arsenal when it comes to process analysis. It readily allows you and your team to grasp the various elements of a process before diving fully into detail on how everything fits together. […]
Read more ยป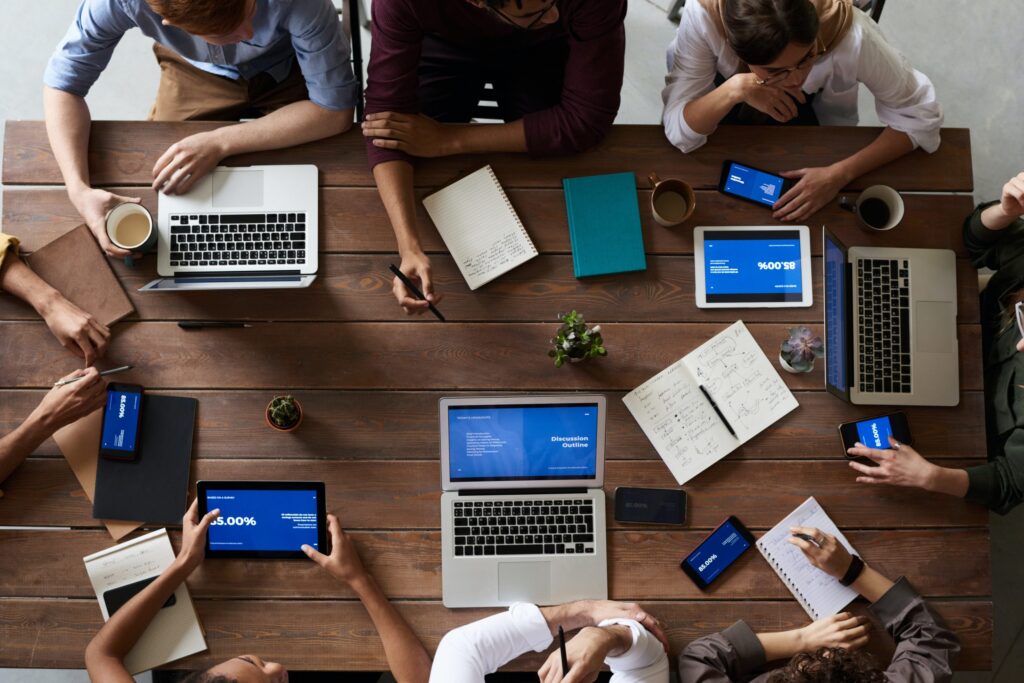
Following the Road to Improvement
Published:As a recently promoted Vice President, Chuck needed to quickly understand what all his people were doing. Chuck, a longtime employee of a major utility company, had been recently promoted to Vice President to take over the leadership of a wide range of different functions than what he had been managing. As a result of […]
Read more ยป
The Cost of Customer Misalignment (& How to Fix It)
Published:This consumer products company has a large portfolio of products. Working with key customers, the company develops and promotes brand marketing programs to help the customer improve their sales which increases the companyโs revenue as well. The CEO of the company realized the percentage of successful promotions was less than he expected. At the same […]
Read more ยป
Tips for Efficient Process Mapping
Updated:A process map is a hierarchical method for displaying processes that illustrates how a product or transaction is processed. It is a visual representation of the workflow either within a process — or an image of the whole operation. Process mapping comprises a stream of activities that transforms a well-defined input or set of inputs into a pre-defined set of outputs.
Read more ยป
Maximizing Value-Added Work: Driving Efficiency and Productivity
Updated:Being busy and working hard donโt necessarily mean what you are doing will have value to your customer. Letโs see why not.
Read more ยป
How to Measure Efficiency and Increase Productivity
Updated:When you hear the word efficient, you probably think of the words waste, productivity, inputs, and outputs. An efficient process will allow you to provide your customers more and better products for less effort.ย
Read more ยป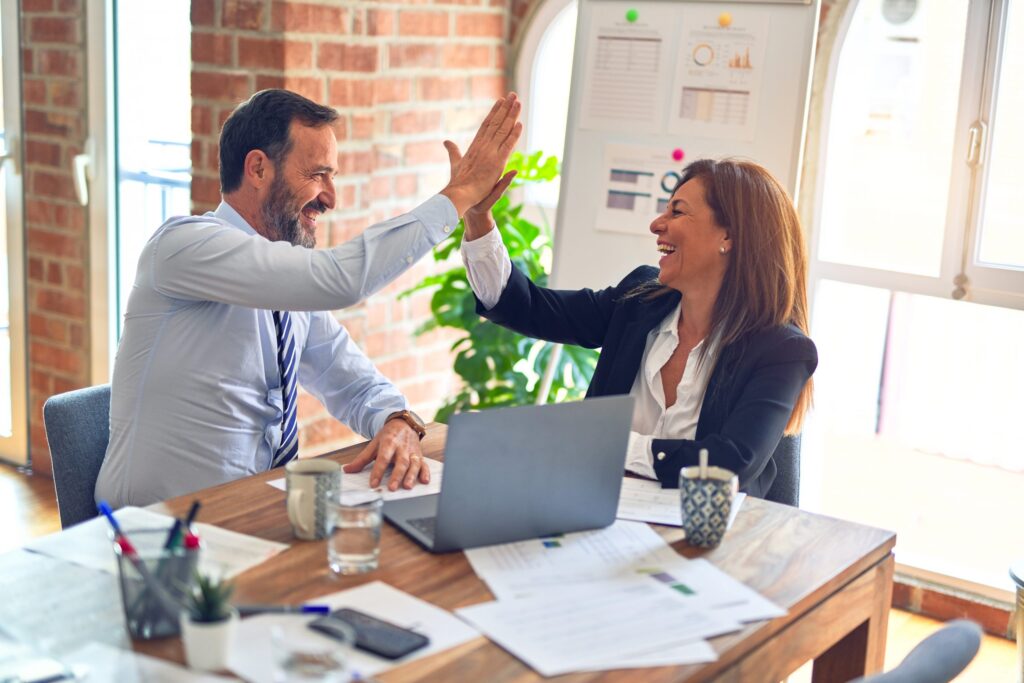
SIPOC: Beyond Process Mapping
Published:The Six Sigma tool SIPOC (supplier, input, process, output, customer) is used to map processes at a high level. SIPOC diagrams are typically included as a slide in project presentations โ often as a required element of a presentation template โ accompanied by a perfunctory description. Presenters may not know what do with the SIPOC […]
Read more ยป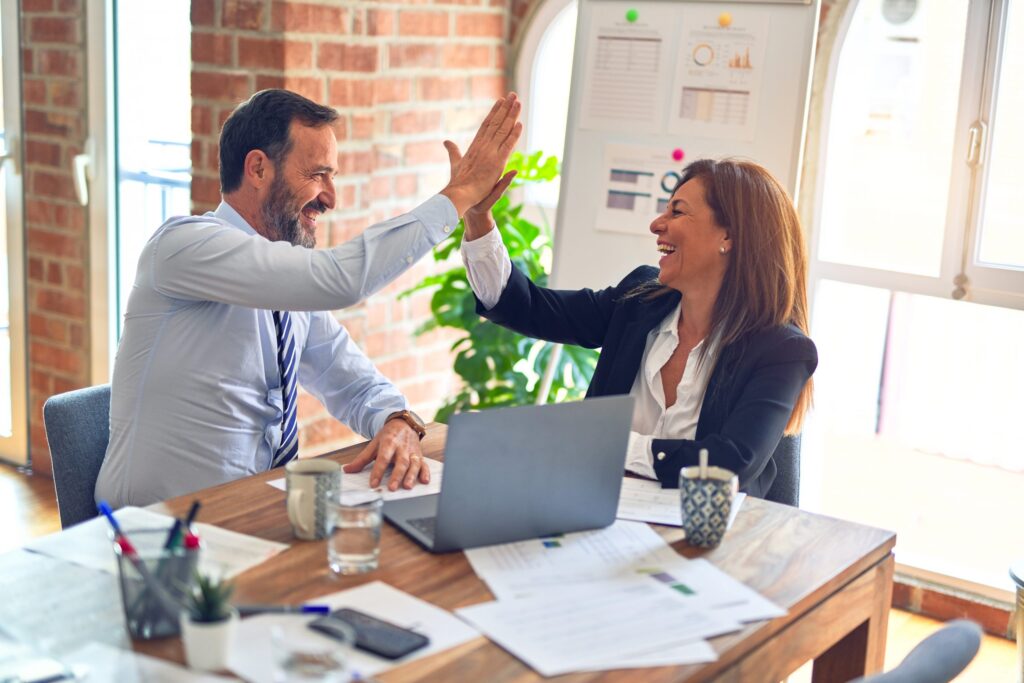
Mastering the Use of SIPOC
Published:One of the most popular search terms on iSixSigma.com is SIPOC (suppliers, inputs, process, output and customers), a process mapping tool. The reverse of SIPOC, COPIS (customer, output, process, input, supplier) is also a frequently searched tool. The best SIPOC/COPIS references on iSixSigma can be found at the following links: Better Involvement/Requirements with LURE and […]
Read more ยป
Better Involvement/Requirements with LURE and COPIS
Published:Implementing technology requires stakeholder involvement and good requirement development. When there is a misalignment in those areas businesses and their customers both suffer. LURE and COPIS can clarify perspectives and help avoid misalignment.
Read more ยป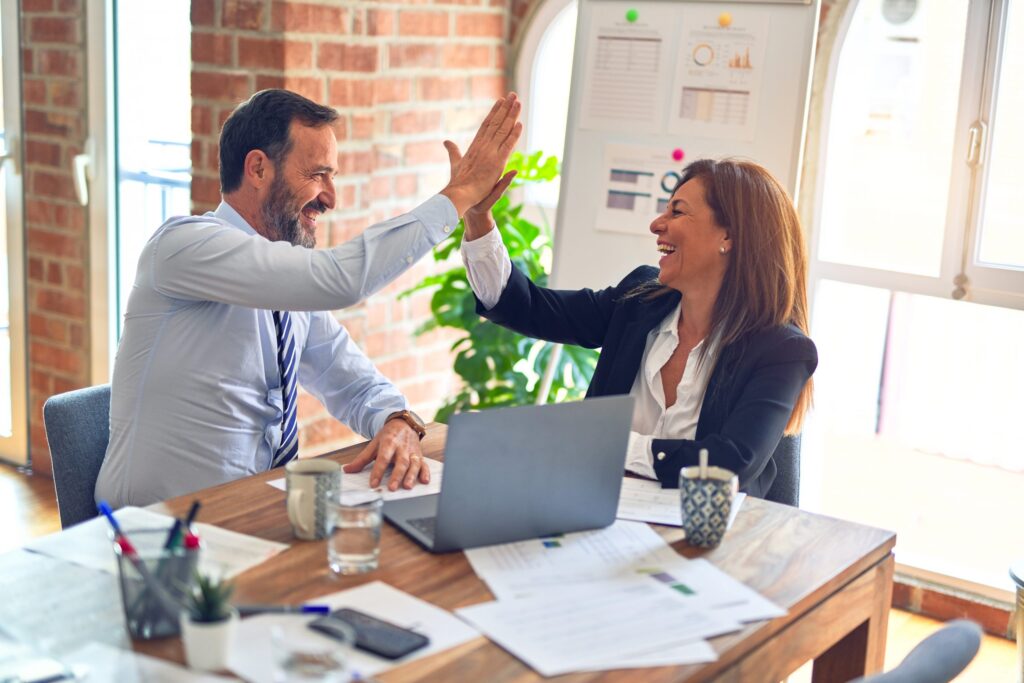
Hocus POCIS: The Magic of the SIPOC Diagram
Published:The SIPOC (suppliers, inputs, process, outputs, customers) process map is one of the most valuable tools in a Six Sigma professionalโs toolbox. It typically can be completed with the project team in less than an hour, and has a strong tie to the project charter. It also makes previously unknown customers suddenly appear out of […]
Read more ยป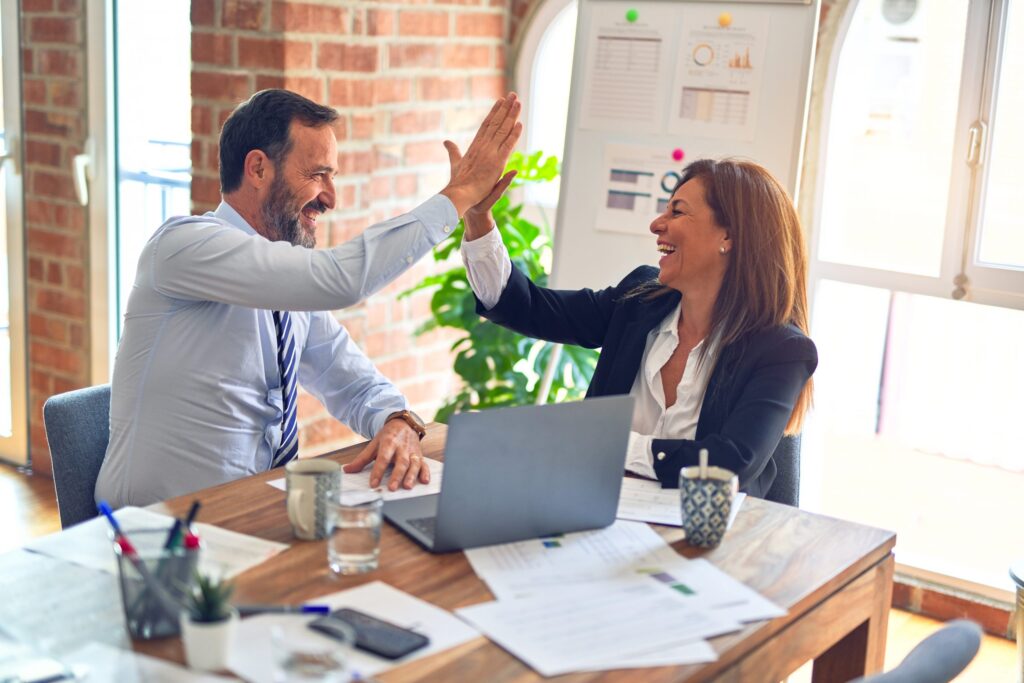
Tools That Complement SIPOC and Help Uncover Details
Published:A SIPOC (suppliers, inputs, process, outputs, customers) diagram is a standard part of most Six Sigma projects for good reason: It helps a team to pose and answer important questions about customers, suppliers, requirements and dependencies. In many cases a SIPOC table and a simple process map can go a long way in discovering the […]
Read more ยป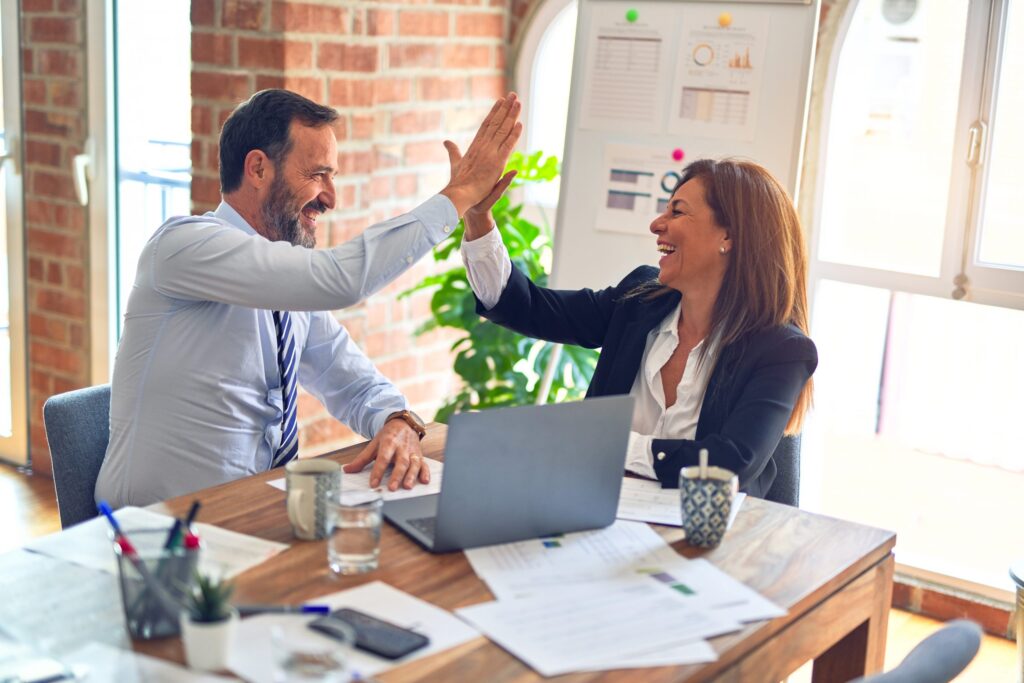
Identifying High-Level Requirements Using SIPOC Diagram
Published:Often times it almost seems as if the people who run a business and the people developing and implementing the information technology (IT) systems for the business do not speak the same language. So it was with a project team that had developed a high-level, future-state process map for a renewal process in the insurance […]
Read more ยป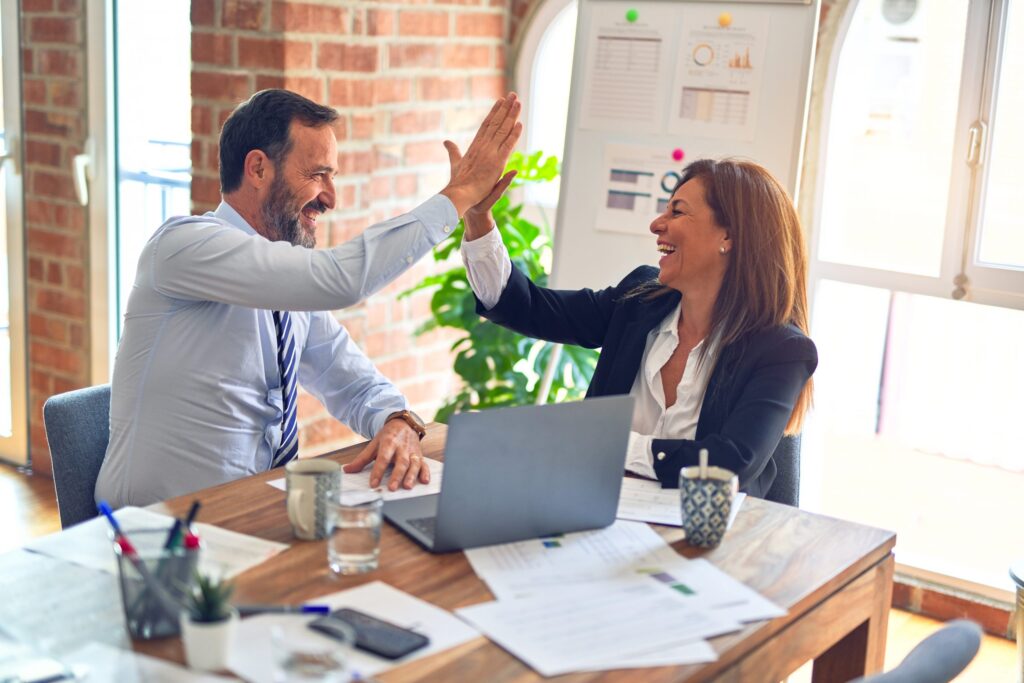
Combining SIPOC with the Cause-and-Effect Diagram
Published:Six Sigma practitioners strive to find the root causes of defects fast and accurately. One of the tools that provides a good initial view of the process Six Sigma is being used to optimize is SIPOC (supplier, input, process, output, customer). This tool is especially helpful when the improvement project is aimed at a process […]
Read more ยป
SIPOC Leads to Process Mapping and Project Selection
Published:Companies new to Six Sigma need an agreed-upon, easily communicated picture of current processes (“as is” state). Building a SIPOC diagram is a good starting point.
Read more ยป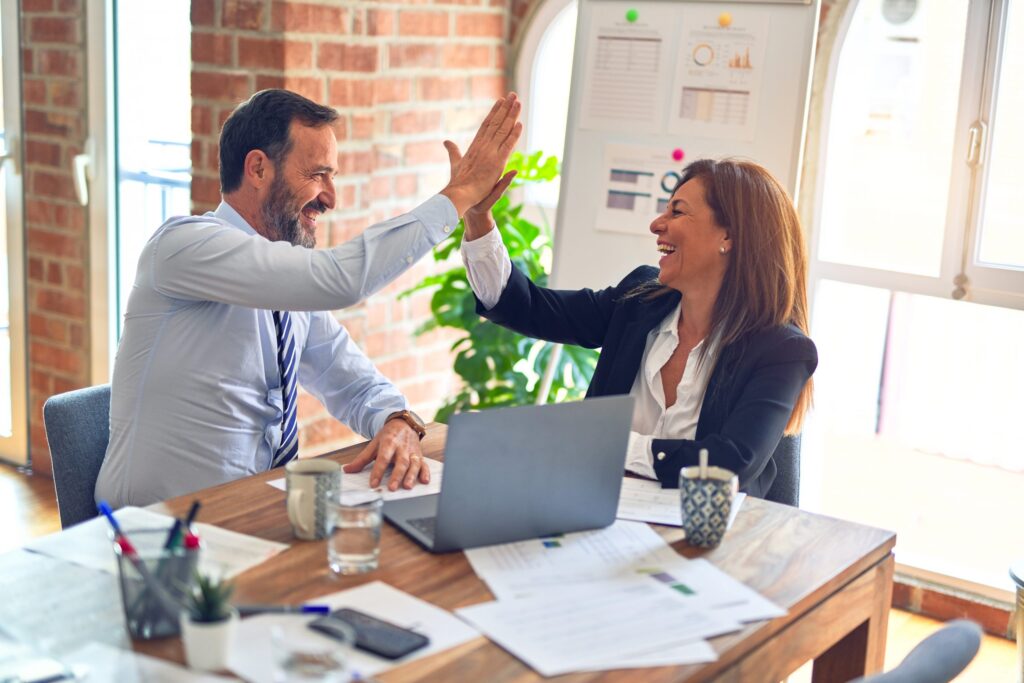
Important to Understand the Process Before Improving It
Published:To create sustained continuous improvements in organizational processes, an organization must first understand its processes. In a services environment, this can be difficult. A service by its very nature requires human interactionย โ people serving people. This means that a single organizational process may be perceived as diversely as the people performing it. And with merger […]
Read more ยป