Category: Concepts
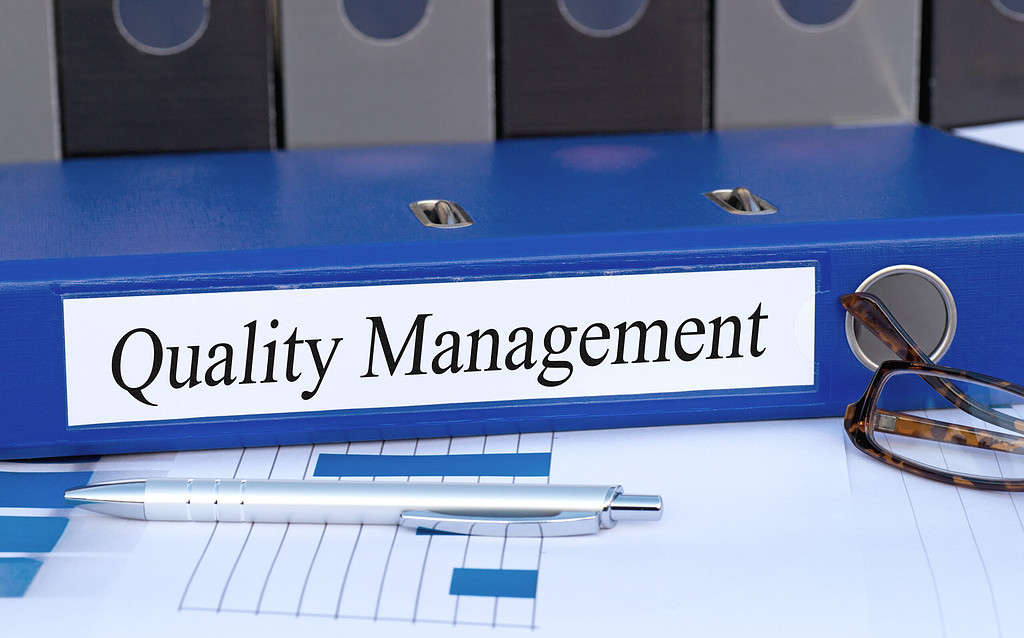
Quality Control vs. Quality Assurance: What’s the Difference?
Updated:What is Quality Control (QC)? Quality control (QC) is a product-oriented approach to quality to ensure that products or services meet specified quality requirements and standards. Quality control focuses on inspection and testing to verify that a product is safe and effective after production. It is often viewed as a process of detection versus prevention. […]
Read more »
Six Sigma vs. Lean: What’s the Difference?
Updated:What is Six Sigma? Six Sigma is a quality control methodology that is utilized to improve processes through the elimination of defects. In practice, the methodology incorporates project management, analysis, and statistics to improve the functionality of a business by addressing defects in a process. The cornerstone of the Six Sigma method is the DMAIC […]
Read more »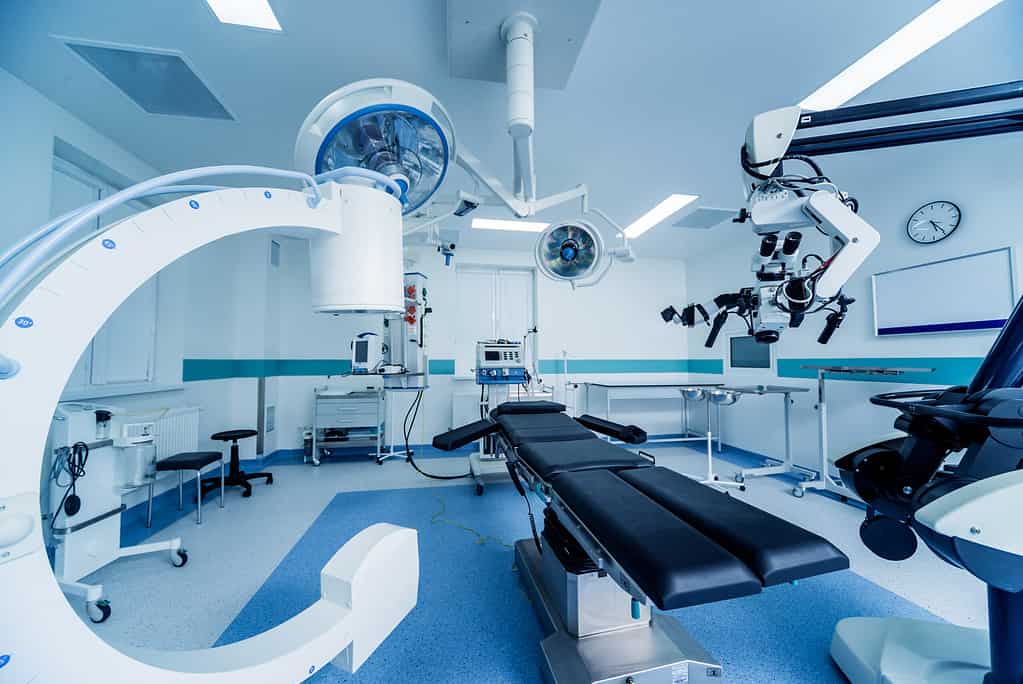
How Abbott Utilizes Six Sigma Methodology to Enhance Business Processes
Updated:Abbott, a global healthcare company, has successfully employed the Six Sigma methodology to improve various aspects of its business operations. By leveraging this data-driven approach, Abbott has achieved significant advancements in efficiency, quality, and customer satisfaction. Abbott’s Journey to Transform Business Processes: Tackling a Critical Challenge Abbott, a leading healthcare company, has built its reputation […]
Read more »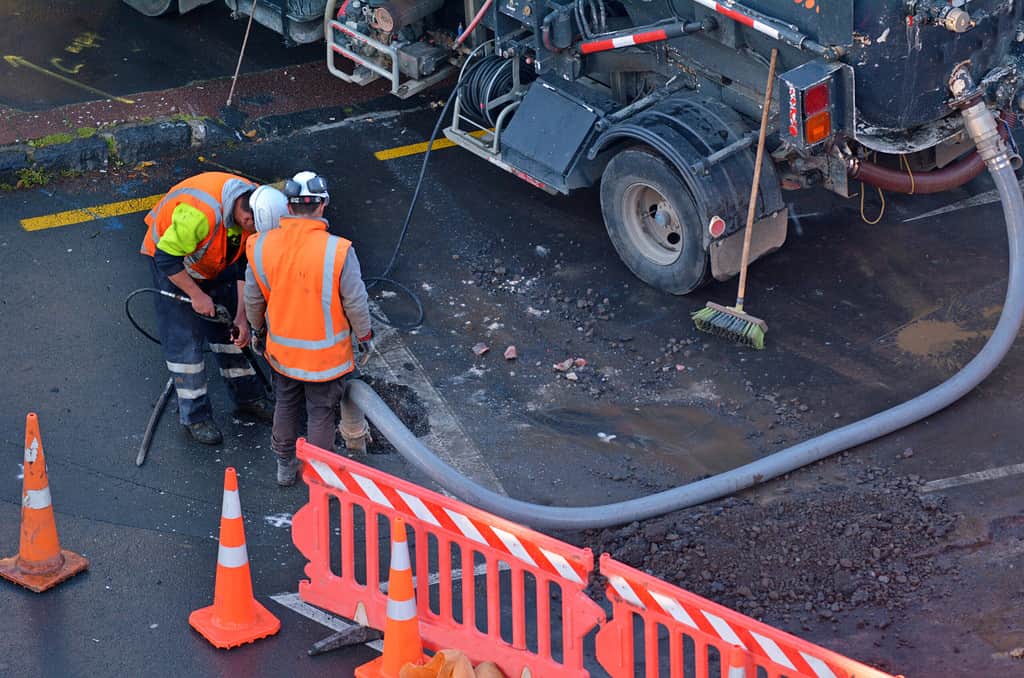
How DMAIC Helped San Antonio Increase the On-Time Payment of Street Maintenance Contractors by Nearly 20%
Published:We all need payment for the work that we do. It is really that simple. If contracted out to do a job by somebody, you need to be able to count on compensation for the work done on that job within a reasonable amount of time. Contractors that worked on street maintenance projects for the […]
Read more »
How DMAIC Led to a Nearly $950,000 Impact on RFR’s Bottom Line
Updated:Utilizing Six Sigma tools like DMAIC saved RFR $928,000 in retained sales as well as $10,000 in cost savings and $9,000 in workplace training. RFR Metal Fabrication Was Having Growing Pains RFR Metal Fabrication began as Advanced Fabrication Technology in 1987, switching names to RFR in 1999. Throughout its history, the organization has focused on […]
Read more »
How Starting With a Six Sigma Scorecard Led to Significant Increases in On-Time Deliveries, Efficiency, and Profit Within a Year
Updated:When many think of Six Sigma, they first think of massive corporations utilizing the methodology for quality and process improvement. They do not generally associate it with the mom-and-pop shop down the street. The truth is that plenty of smaller companies use the Six Sigma method to optimize their businesses. The only reason that most […]
Read more »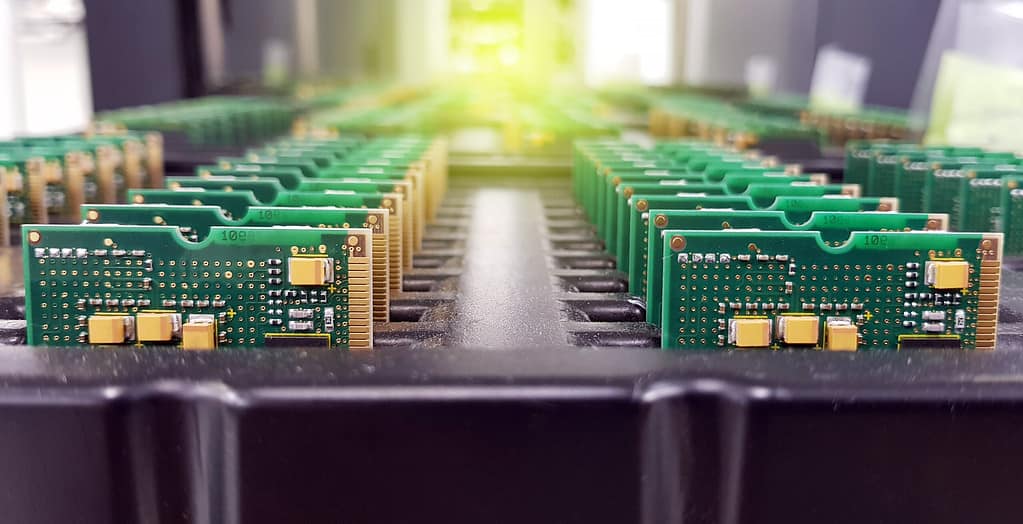
Motorola Uses Data-Driven Six Sigma Methodology to Improve Production Process
Updated:In the early 2000s, Motorola struggled with product defects and a decline in customer satisfaction. To improve its business processes and regain its competitive edge, Motorola turned to Six Sigma. This data-driven methodology for process improvement turned their fortunes around. The Impact of Six Sigma on Motorola’s Semiconductor Production Process Motorola is a multinational telecommunications […]
Read more »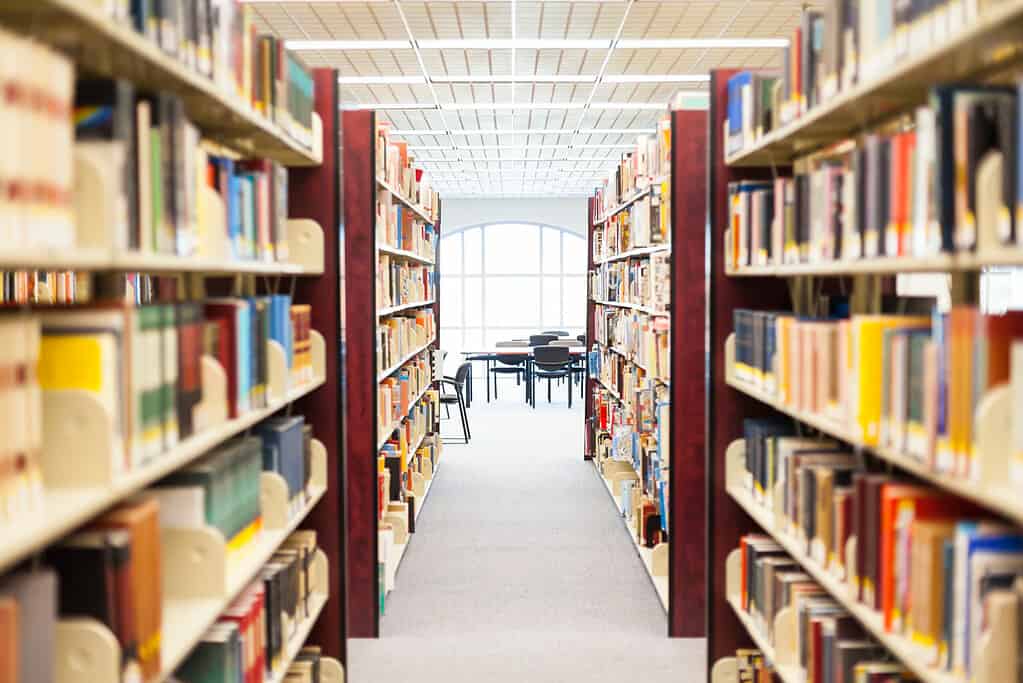
DMAIC Helps Miami-Dade Public Library Improve Services and Save Money
Updated:In 2018, the Miami-Dade Public Library System utilized Six Sigma methodology to improve upon the time needed for the transporting of library materials. The utilization of Six Sigma to meet the needs of this type of organization is an exciting example of just how versatile these tools can be. When we go to the library, […]
Read more »
How Canon Business Process Services Uses Six Sigma to Optimize Business Processes
Updated:Everyone knows Canon as a massive corporation that manufactures cameras, printers, scanners, and a variety of other quality goods. Less known by the consumer market is the role Canon plays in helping other companies improve processes using the Six Sigma methodology. This happens through a Canon subsidiary that operates under the name Canon Business Process […]
Read more »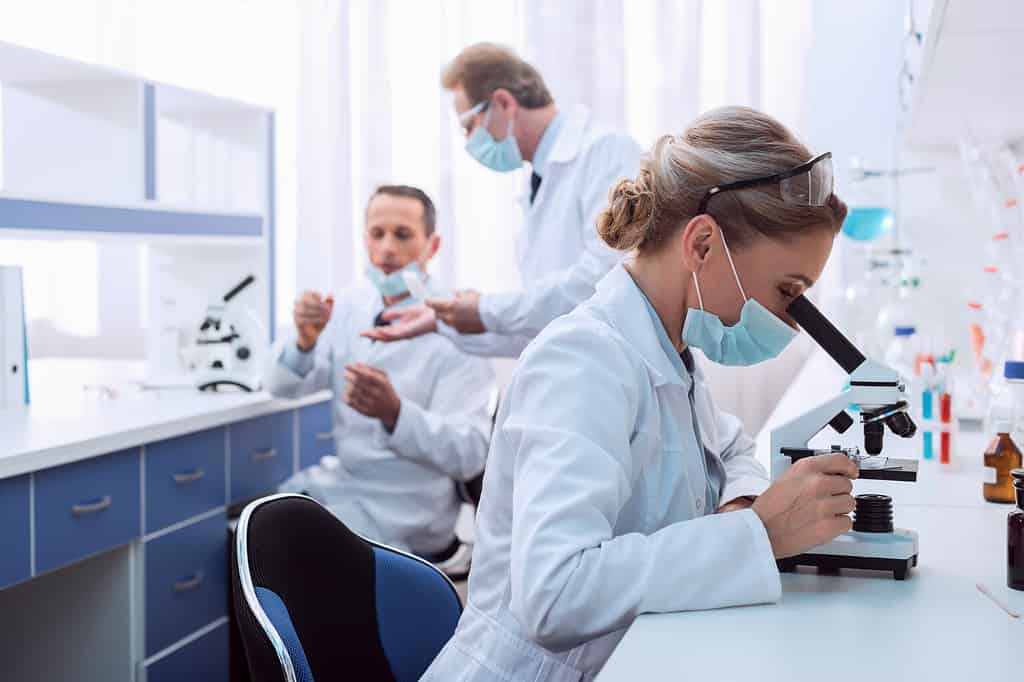
How the Six Sigma Voice of the Customer and DMAIC Tools Brought the Two Sides of SQL Together
Published:With the formation of a joint venture between the original healthcare organization laboratory, Sonora Lab, and the larger Quest Diagnostics, a partnership existed in name only. Both labs went about operating in separate locations while continuing with their individual instrumentation and systems. Over time, this led to issues across both teams, and it became clear […]
Read more »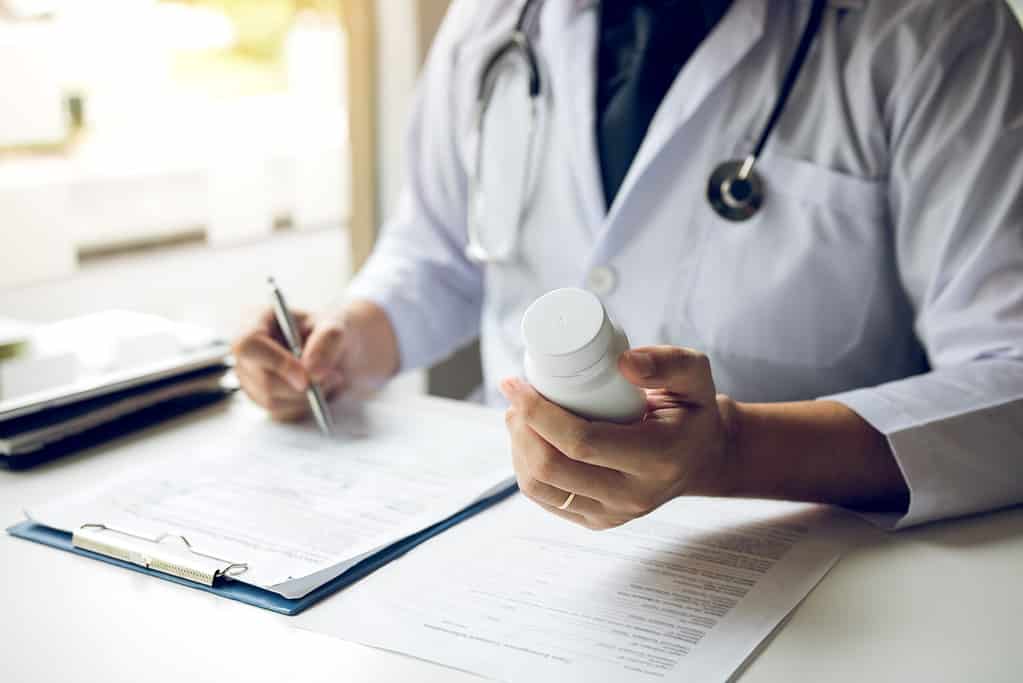
How Six Sigma and Lean Tools Helped Recover Nearly 4 Million Dollars in Annual Revenue
Updated:When faced with the news that drug manufacturers of cancer medication were responsible for causing a massive amount of financial waste, the oncology department at UCSD utilized Six Sigma and Lean tools like a cause-and-effect diagram, a Kaizen Event, the 5 Whys, and others in order to improve scanning processes that could help in recovering […]
Read more »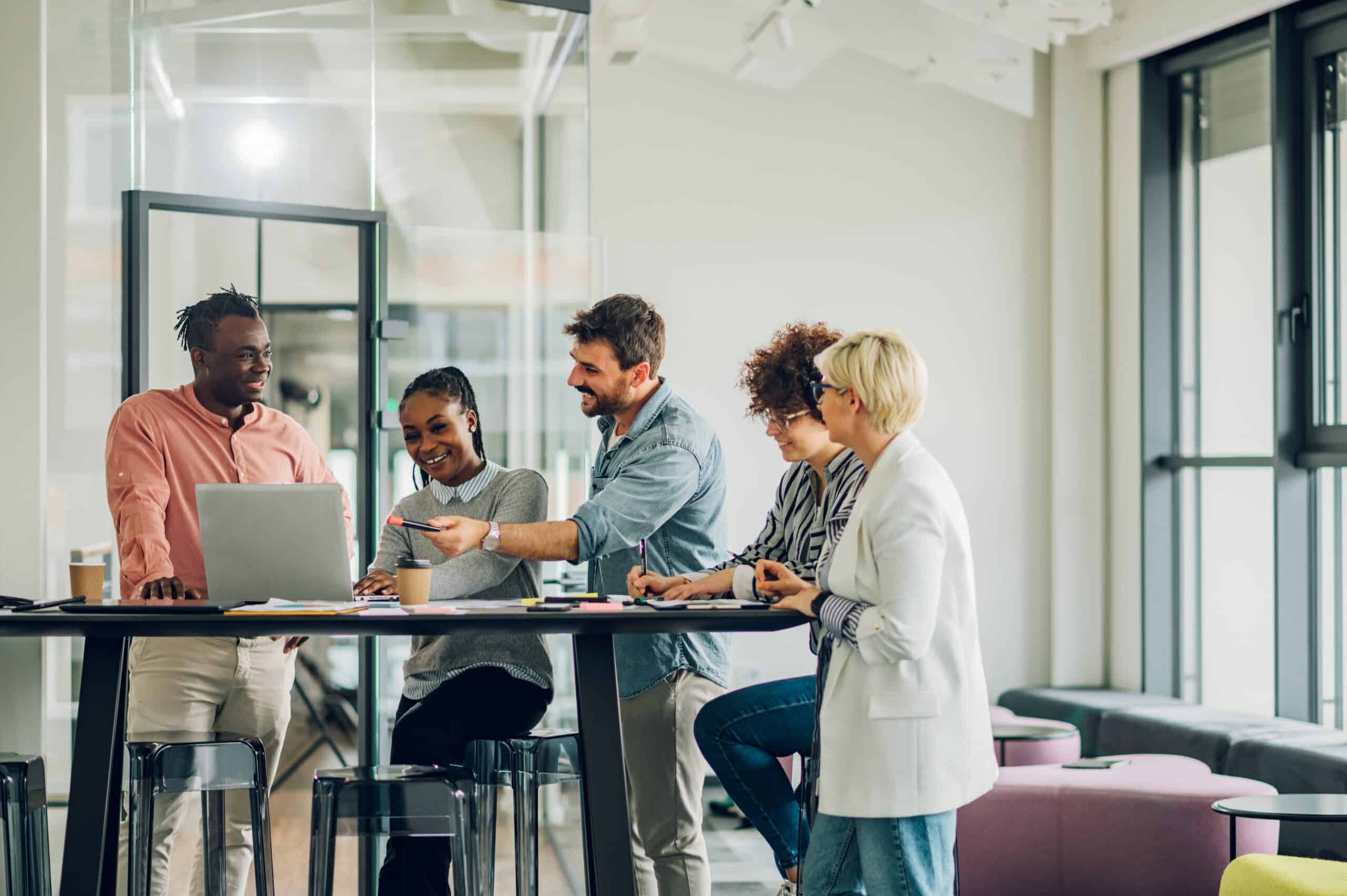
How Six Sigma Tools Sharply Decreased Downtime At The Nature Conservancy’s Headquarters
Updated:The web development team at The Nature Conservancy in Arlington, VA, was able to utilize Lean and Six Sigma tools to close the gap in downtime due to a coding freeze every 45 days. The Nature Conservancy used such Six Sigma tools as process maps, The 5 Whys, and cause-and-effect diagrams to dramatically bring the […]
Read more »
Lean Six Sigma Saves U.S. Army Test Center Millions
Updated:By employing Six Sigma and Lean Six Sigma methodologies, the U.S. Army’s Aberdeen Test Center was able to improve the cost-effectiveness and efficiency of its vehicle maintenance operations. Six Sigma’s DMAIC method gave the Aberdeen Test Center the necessary tool for improving its cycle time, significantly decreasing the wait for its clients between when a […]
Read more »
Maximizing Results with Orthogonal Regression
Updated:Have you ever wondered whether the outgoing inspection values from your vendor are equivalent to the values of your incoming inspection? Maybe it’s time to use orthogonal regression to see if one of you can stop inspecting. If your vendor is doing final outgoing inspection, do you need to also do incoming inspection on the […]
Read more »
How Utilizing the Full Six Sigma Process Helped Turn Wipro Into a Global IT Leader
Updated:In the 1980s, Wipro made the leap from being primarily known as a vegetable oil company in India into the world of IT. In order to be a competitor in this industry on a global scale, Wipro would need to continually improve its performance as well as work smarter towards meeting the needs of its […]
Read more »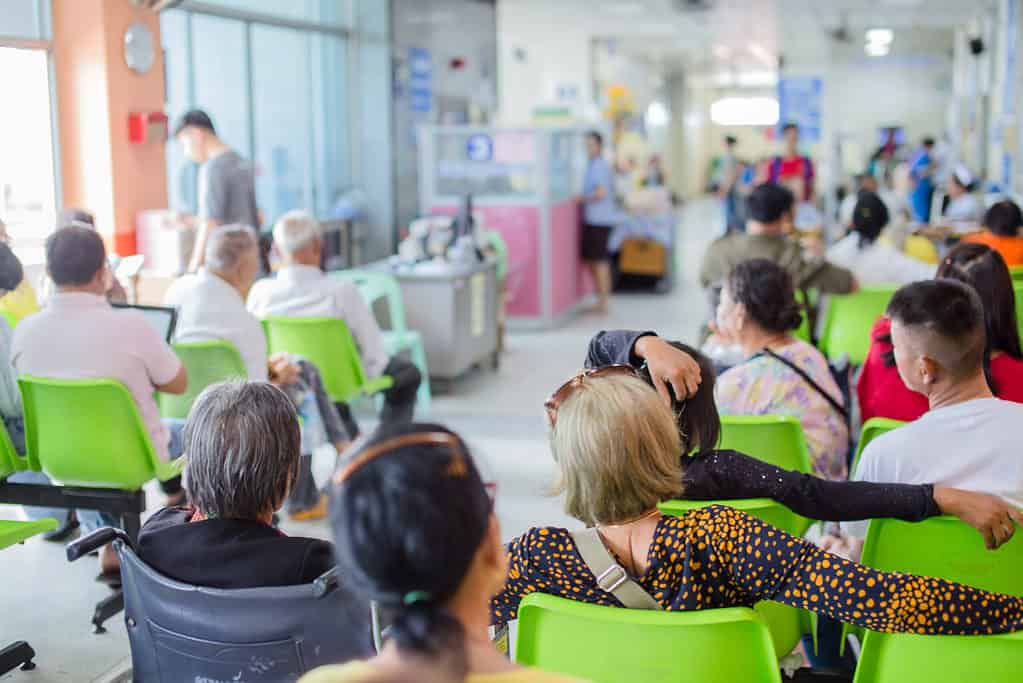
Using Queuing Theory to Improve Patient Experience and Reduce ER Wait Times
Updated:Have you or a family member ever had to visit a hospital Emergency Room? What was your experience? How was your wait time? Let’s see how one hospital handled long wait times and extensive patient dissatisfaction using queuing theory. The Emergency Room of a public hospital was experiencing long wait times to treat patients. Wait […]
Read more »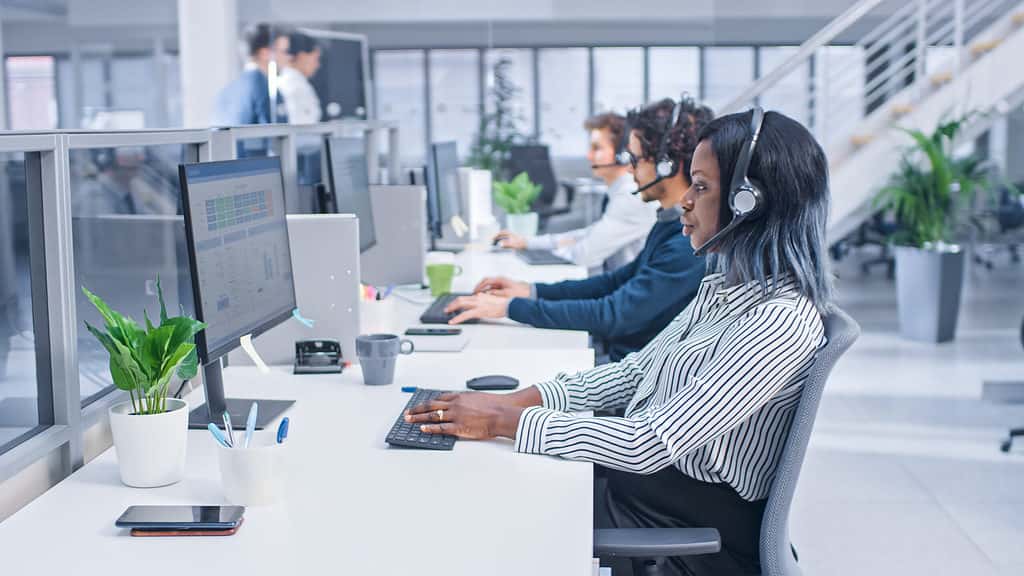
How Green Belt Certification and DMAIC Improved Help Desk Resolution Time By 64%
Updated:Lean and Six Sigma practices are ultimately about helping businesses use efficiency to provide the ultimate customer experience. But what about state and county government entities? Can the same practices apply, and do they even have “customers”? The residents in the counties these government offices serve would likely say “yes”. Kern County spans the southern […]
Read more »
Continuous Improvement and the 3p Approach Helped Deschutes Become An Industry Leader
Published:You may have taken notice of Deschutes lately. In the last few years, it has become much more commonplace to find the brewery’s products on draft at your local pub or at your nearest retailer. Such a marketplace presence did not happen overnight, and the brewery credits the lessons learned from Six Sigma as having […]
Read more »
Randomization: Key to Reducing Bias and Increasing Accuracy
Updated:Not all experiments are created equal. Learn how randomization can improve the validity of any business’ experiments aligned with Six Sigma principles. Randomization in Six Sigma Business owners and managers want to know what works and what doesn’t when it comes to existing processes and methods of operation. Running experiments and assigning inputs and outputs […]
Read more »
How to Track and Improve Customer Expectations Using Result Measurables
Updated:Measurables indicate how a process is performing or how customer expectations are being met. These indicators are quantifiable, expressed numerically, and can have units of measurement. There are two kinds of these indicators. They are process measurables and result measurables. It is important in any business to know if you are meeting the expectations of […]
Read more »
Y
Updated:In discussions about the Six Sigma methodology, you will often find the equation Y=F(x). It is an important formula in working with the methodology and can serve as a very helpful tool in project management. When working with the Y=f(x) formula, X stands for the various inputs utilized to generate an outcome, while f represents […]
Read more »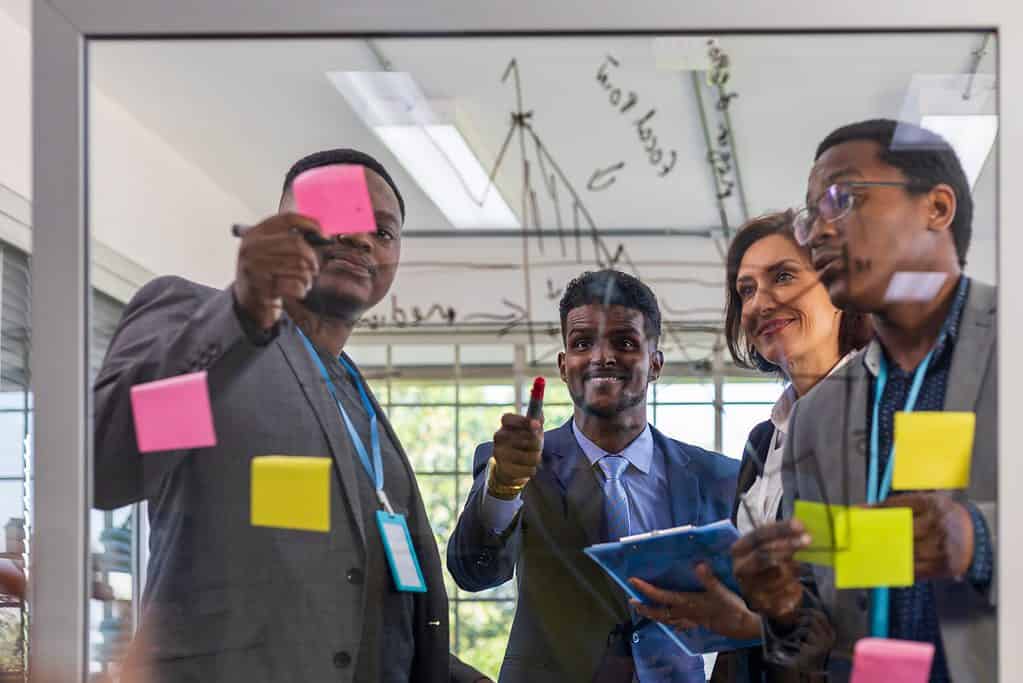
How Simple Linear Regression Helps Make Sense of Data
Updated:What is the point of having a bunch of raw data if you don’t have the tools to analyze it? Regression models provide you with the ability to see if there is a relationship between two types of variables, helping make some sense of data that has been collected by fitting it to a line. […]
Read more »
Determining Total Cost of Quality Can Improve Your Business Processes
Updated:You are probably familiar with the notion that there are costs of poor quality, often shown as COPQ. These represent both internal and external failures to maintain good quality. There are also costs associated with maintaining good quality sometimes represented as COGQ. These costs represent appraisal and prevention costs. Total Cost of Quality (TCOQ) is […]
Read more »
What are Transformations? A Complete Guide
Updated:Many statistical tools assume normality. Is there an option if my data is not normal? Transforming your data might help. Some statistical methods, such as hypothesis testing, have an underlying assumption of the normality of your data before they can be used. Although control charts are generally robust to normality issues, sometimes the data is […]
Read more »