Category: Concepts
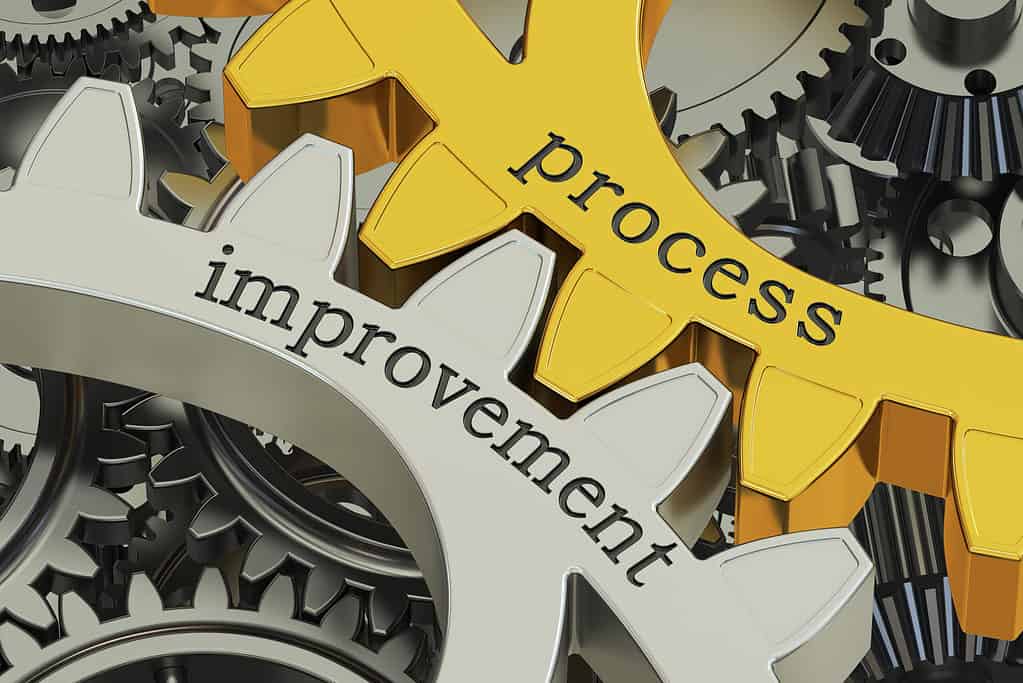
Discover the Power of DMEDI in Process Improvement
Updated:DMEDI stands for: Define, Measure, Explore, Develop, and Implement. This differs from the basic Six Sigma methodology of DMAIC which stands for: Define, Measure, Analyze, Improve, and Control. Both methodologies are designed to improve your processes and products. Whereas, DMAIC is designed for incremental improvements of existing processes, DMEDI focuses on more robust improvements for […]
Read more ยป
How Engineer Change Orders Can Improve Your Business Processes
Updated:When there is a need for changes that will improve end products or components, it is necessary to have proper documentation so that there is a paper trail and to ensure the correct modifications occur. An engineer change order is an important part of making sure that necessary changes to products are handled in a […]
Read more ยป
The Importance of Understanding and Implementing Directives
Updated:Directives are an important tool for organizations that seek to align employees with their goals, increase efficiency, and promote a culture of continuous improvement. Understanding Directives: Benefits, Best Practices, and Common Questions Directives are a critical tool for organizations seeking to improve their performance and achieve their goals. By providing clear guidance and expectations, directives […]
Read more ยป
Driving Process Excellence: Harnessing the Power of DMAIC for Effective Improvement
Updated:In today’s fast-paced and competitive business landscape, organizations strive to enhance their operations, deliver superior quality, and meet customer expectations. To achieve these objectives, many organizations turn to DMAIC (Define, Measure, Analyze, Improve, Control), a structured problem-solving methodology widely employed in Six Sigma. DMAIC provides organizations with a systematic approach to identifying process inefficiencies, reducing […]
Read more ยป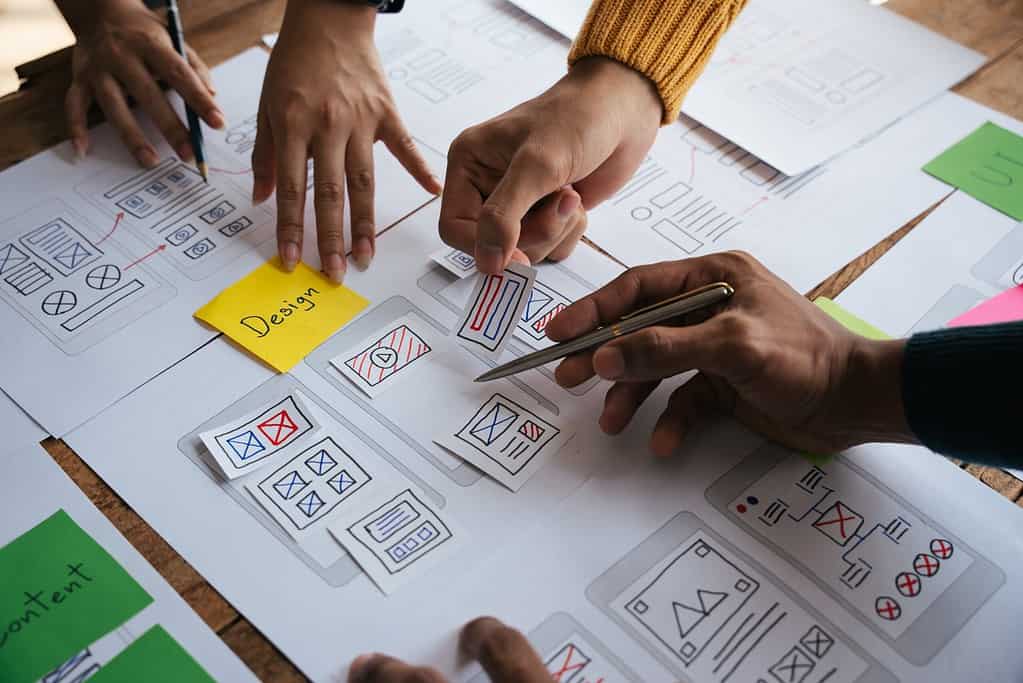
Maximizing Efficiency and Accuracy with Design of Experiments
Updated:A design of experiments (DOE) is a set of powerful designed experimentation statistical tools for understanding the impact that varying your process inputs will have on the outputs of your process.ย
Read more ยป
Ensuring Product Reliability with Design Verification, Production and Process Validation
Updated:During the design or prototype stage of product development, there is a system of checks in place that can help make sure the product is successful in moving into the next stages. The products that are released into the mass market have gone through many stages of development so that they can be trusted by […]
Read more ยป
The Role of DOE in Quality Control
Updated:DOE (Design of Experiments) can be defined as a set of statistical tools that deal with the planning, executing, analyzing, and interpretation of controlled tests to determine if there is a casual relationship between your process factors or variables and your process output. Overview: What is DOE? Two common approaches to DOE are a full […]
Read more ยป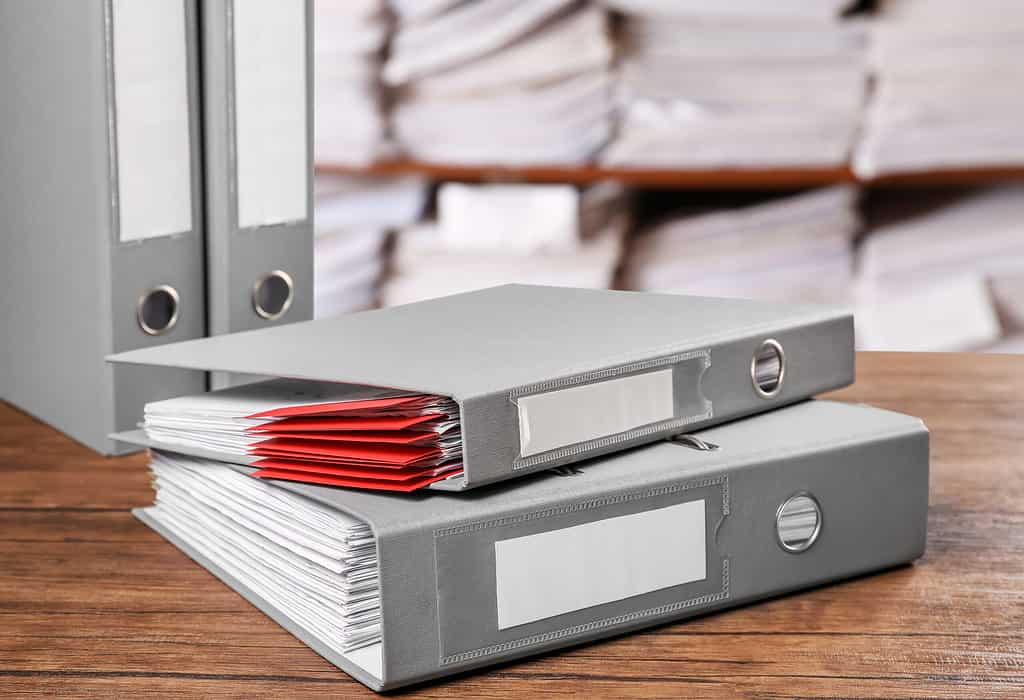
Documentation Matters: The Foundation of Effective Processes
Updated:Documentation can feel like a drag, but it is an important part of making sure your organization is successful. Without proper documentation, there is no record of how to reliably implement processes, and a complete lack of consistency could occur. Documentation is also necessary for important guidelines and policies to be referenced once they are […]
Read more ยป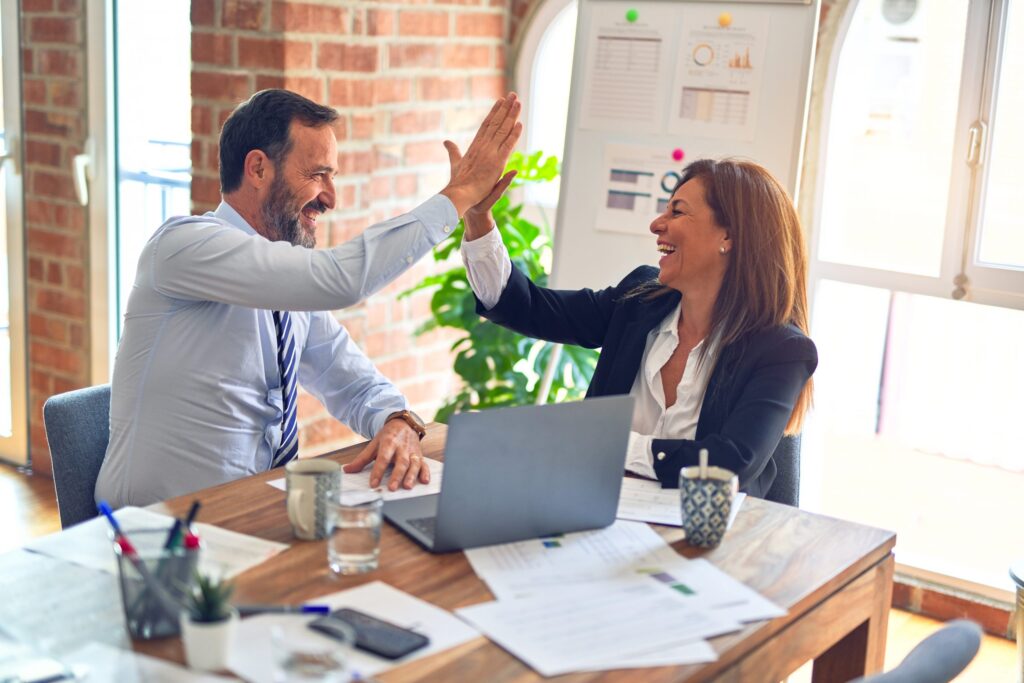
Heijunka
Published:Wouldnโt it be great if your production process ran smoother? Maybe Heijunka is the solution. Letโs find out more about it.
Read more ยป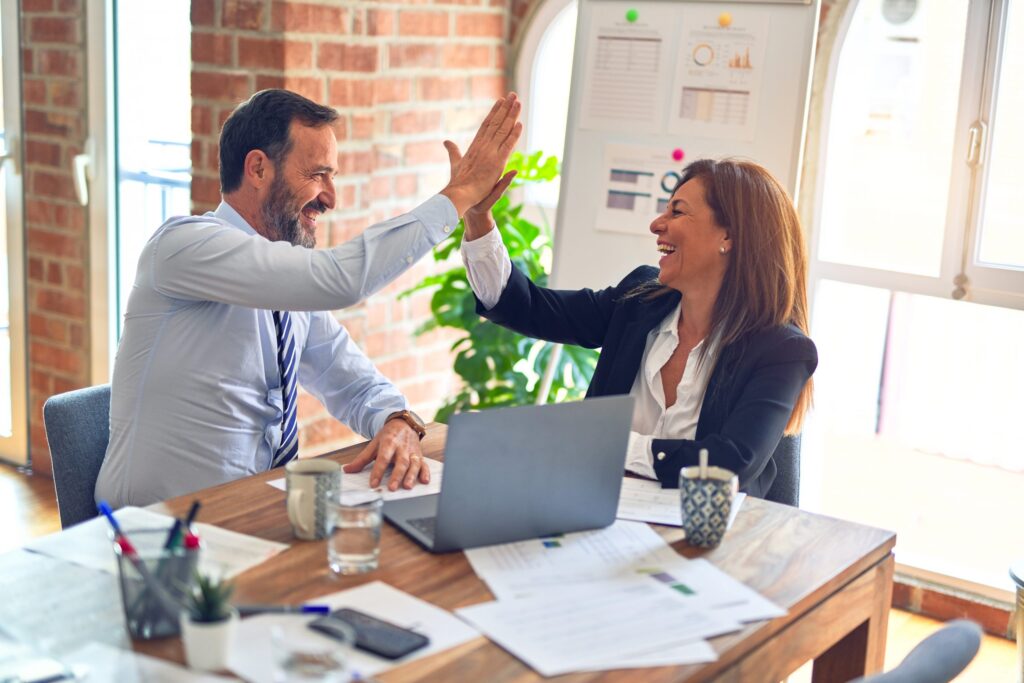
Genchi Gembutsu
Published:How much can you learn about your process sitting in your office? According to Genchi Gembutsu, you canโt learn much. In Japanese, genchi means โactual place,โ and gembutsu means โactual thing.โ In the Toyota Production System (TPS), this concept is interpreted as โto go and see.โ Letโs explore this a little further.ย
Read more ยป
How Customer Focus Can Increase Your Sales
Updated:It is more important than ever for businesses to look at the needs and desires of their customers as indicators for how to operate. Since a business does not exist without customers, having an understanding of what they are looking for in the companies they support is imperative for success. More and more companies are […]
Read more ยป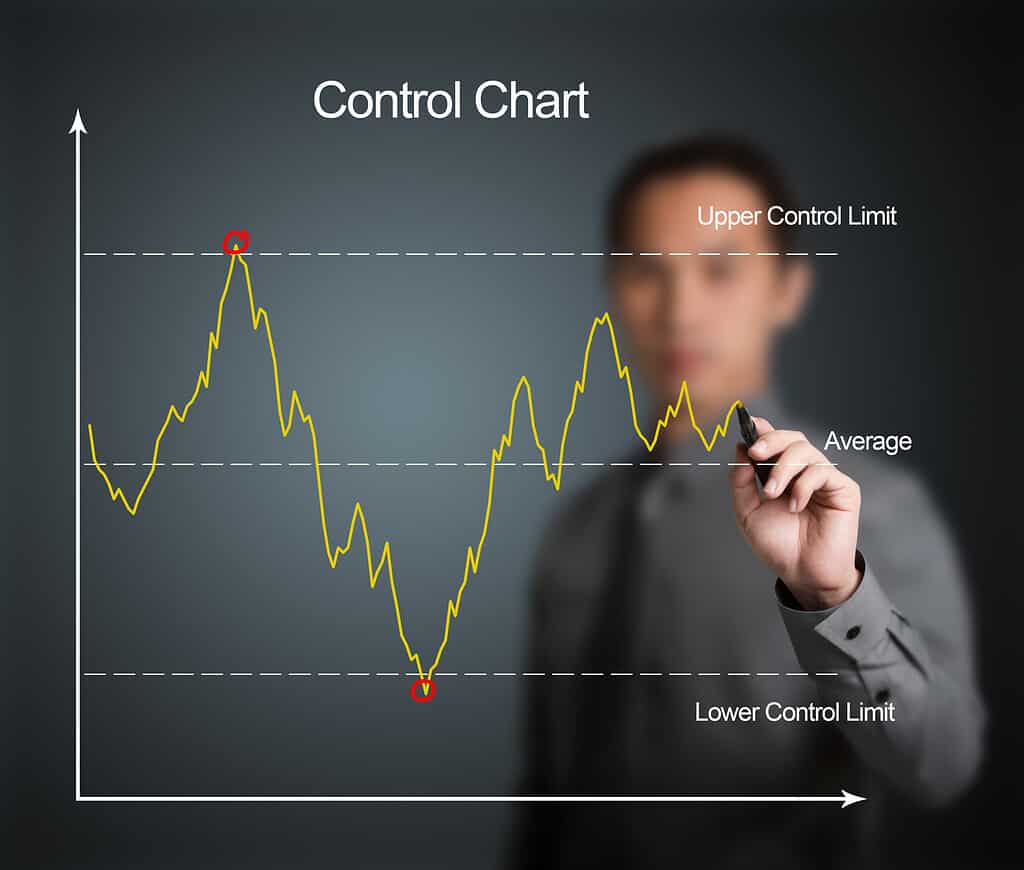
Monitoring Process Stability with Control Charts
Updated:Since there is variation in all processes, how can you tell whether the variation is due to random expected variation, or something unexpected? The control chart is a tool for making that distinction. Letโs learn how that is done.ย
Read more ยป
The Douglass Index: A Powerful Tool for Managing Repeatability and Reproducibility Rates
Updated:Having repeatability and reproducibility rates that are 10% or lower is ideal for applying gauges in capability data retrieval. If your R & R rates are above this level, there is a powerful tool for managing these prohibitively large rates. Working with the Douglass Index allows auditors to crunch data that may fall outside the […]
Read more ยป
Understanding Statistical Distributions: A Comprehensive Guide
Updated:If you plot your data on a histogram, the resulting graphic will illustrate how your data is distributed. This distribution can provide a lot of information about your data and the process from which it came from. Letโs learn some more about distributions. Once you have collected your desired data, you can display the data […]
Read more ยป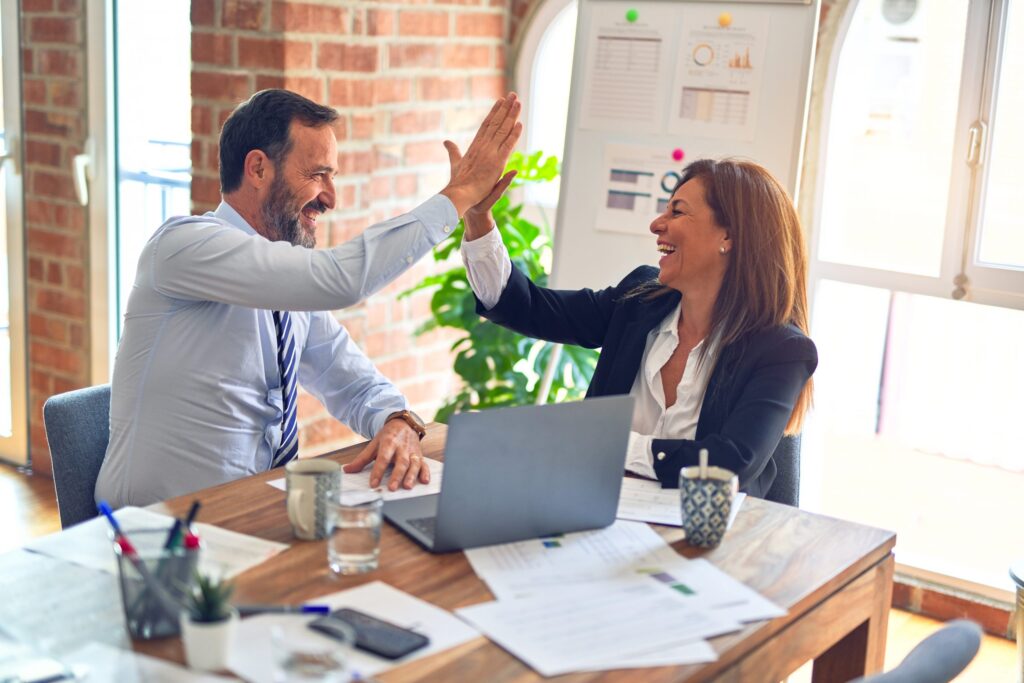
DOTWIMP
Published:You walk by waste in your organization every day. The acronym DOTWIMP can help you identify and analyze your seven most common sources of waste.ย
Read more ยป
Degrees of Freedom and Sample Size: How to Determine the Right Amount of Data for Your Analysis
Updated:Degrees of Freedom (DF) can be thought of as the amount of information you have to compute certain statistics. The more you want to compute, the more data and information you need. Letโs learn more about how to compute and use DF. You can think of DF as statistical money that you can spend to […]
Read more ยป
GLM Essentials: Key Concepts and Applications for Data Analysis
Updated:If you understand multiple linear regression, you already know a lot about the General Linear Model (GLM). Letโs learn some more about how and when to use the GLM.ย
Read more ยป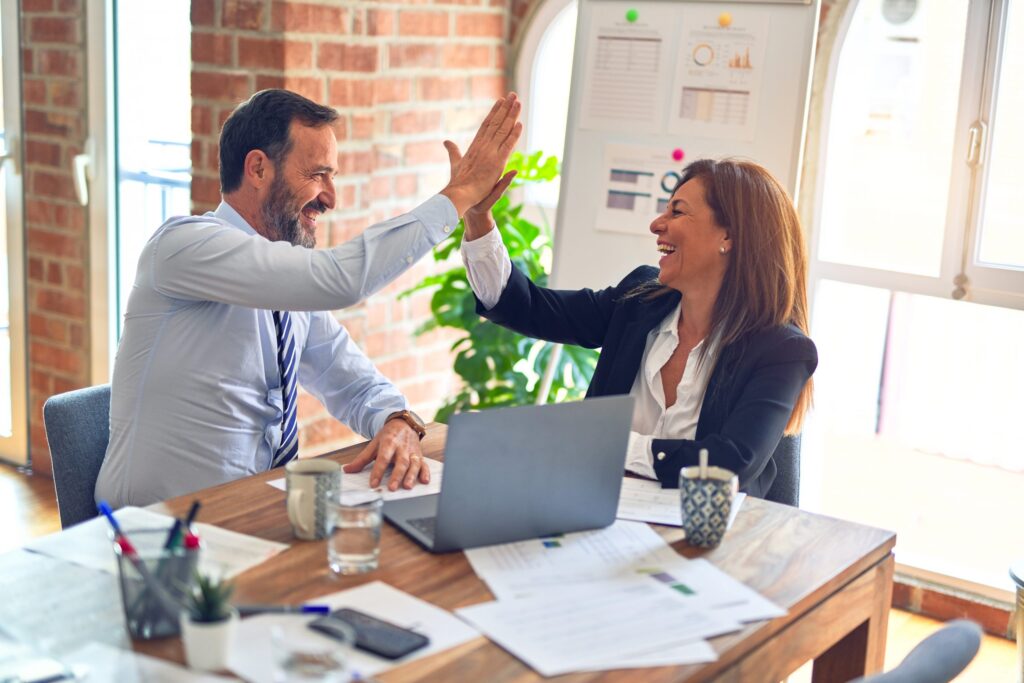
Design Failure Mode and Effect Analysis (DFMEA)
Updated:As complexity increases, so does the probability of error. Rework, defects, retesting, and recalls are all very expensive. With design failure mode and effects analysis, weโll show you the true value of adopting and inetgrating this approach.
Read more ยป
The Benefits of Using Detectable Effect Size in Six Sigma Projects
Updated:Making changes to your organization is foolish without having the proper data to tell you the impact that the changes may have. A tool called a “detectable effect size” can help in making that determination. It is nice to believe that certain changes that are proposed will have an impact on our business, but with […]
Read more ยป
The Role of Efficacy in Minimizing Waste and Defects
Updated:Efficiency and effectiveness are vital elements of any successful organization, but in the realm of Lean Six Sigma, there is another crucial concept that holds the key to achieving optimal results: efficacy. Efficacy goes beyond simply measuring efficiency or effectiveness; it encompasses the ability of a process or methodology to consistently deliver the desired outcomes […]
Read more ยป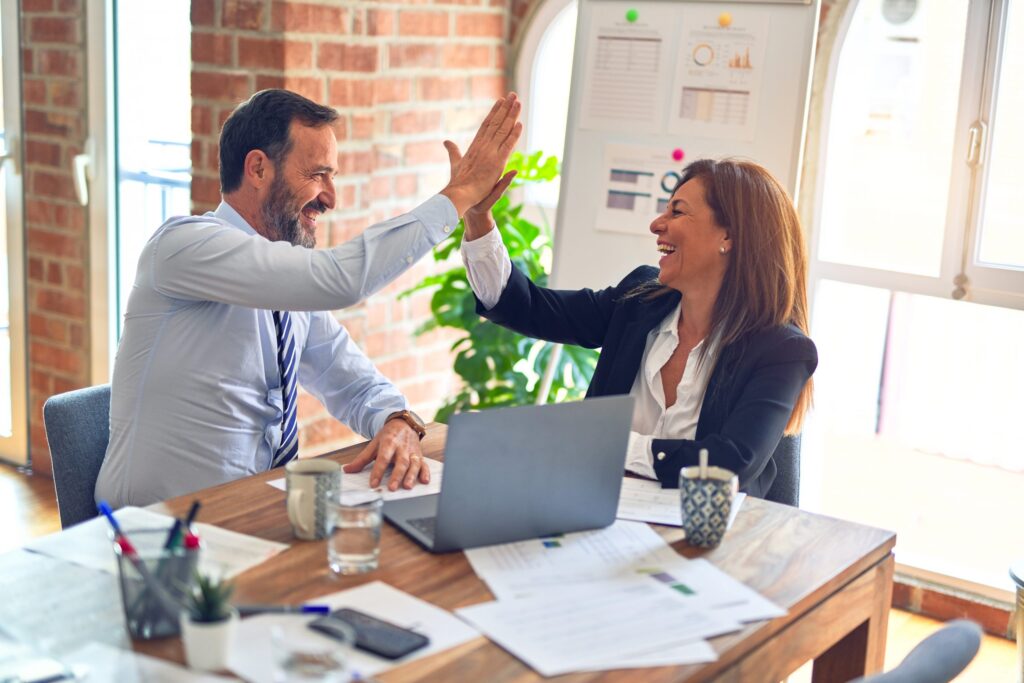
Drift
Published:You finally found the perfect spot to anchor your boat and catch all the best fish. But, the tide is strong and your boat starts to drift away from where you need it to be. The same can happen to your process.ย
Read more ยป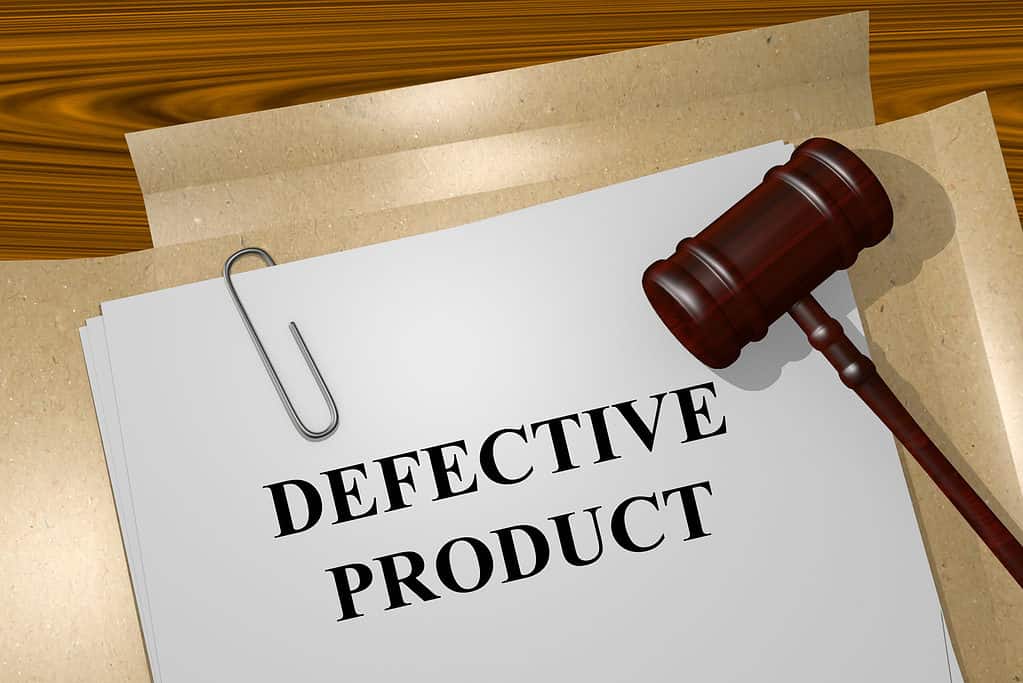
What is a Defective? A Complete Guide
Updated:Unfortunately, sometimes your process produces unacceptable output. These are usually referred to as defects or defectives. Letโs examine what a defective item is and contrast it with a defect. The Merriam-Webster dictionary defines a defective as: having a defect or flaw or imperfect in form, structure, or function. Simply put, a defect is a flaw […]
Read more ยป
Achieving Quality Through Continuous Improvement
Updated:Competition for products and services is cutthroat, and survival should not be taken for granted. Implementing continuous improvement into your organisation and embedding it into your business culture keeps you one step ahead of the pack, locking in both customer and employee loyalty.
Read more ยป
The Power of Data: Understanding What It is and Why It Matters
Updated:The famed statistician, Dr. W. Edwards Deming, frequently talked about data and said, โWithout data, youโre just another person with an opinion.โ Letโs learn some more about data. Data refers to any information, facts, or statistics that can be collected, stored, and analyzed. It can be in the form of numbers, text, images, audio, or […]
Read more ยป