Category: Concepts
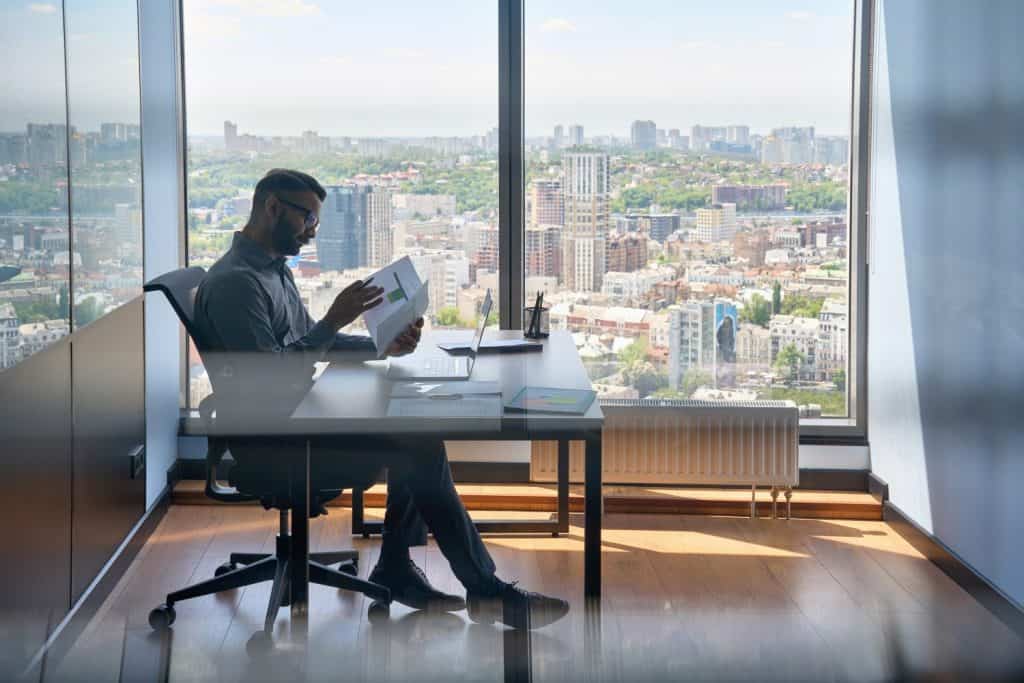
Productivity Target: Reaching Your Goals
Published:A productivity target is an established, quantifiable result from a given process. It represents the minimum acceptable value yield from a given quantity of time and resources invested into it.
Read more »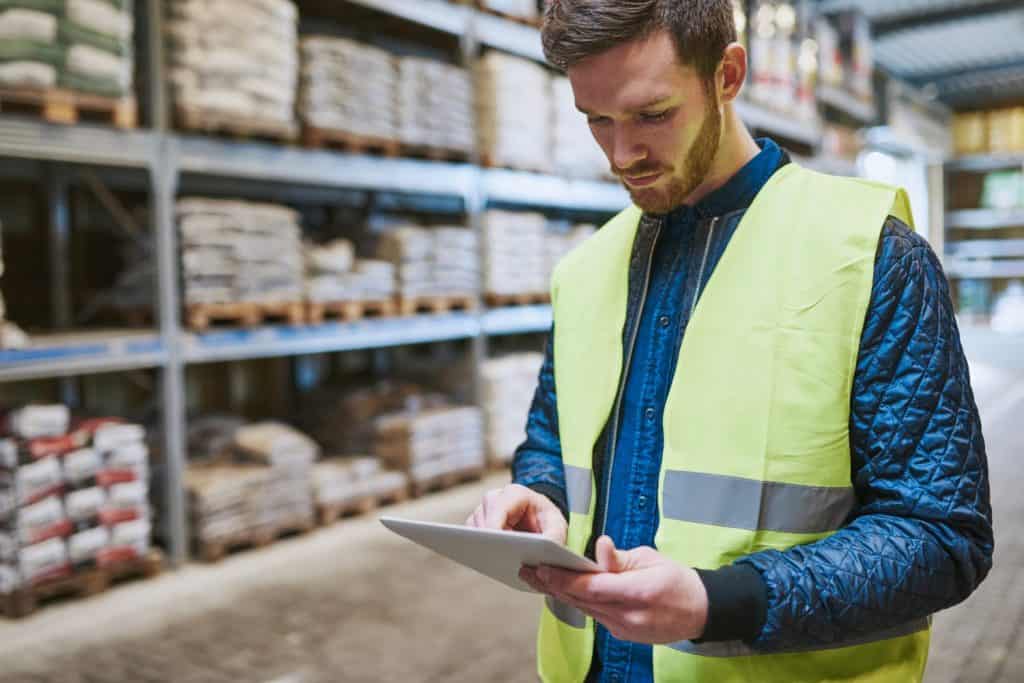
Quality Program Report (QPR): Guaranteeing You Hit the Mark
Published:It is important to regularly check if your processes are operating as optimally as they could be. If not, actions should be taken for improvement. For this to be appropriately determined, you can create a QPR.
Read more »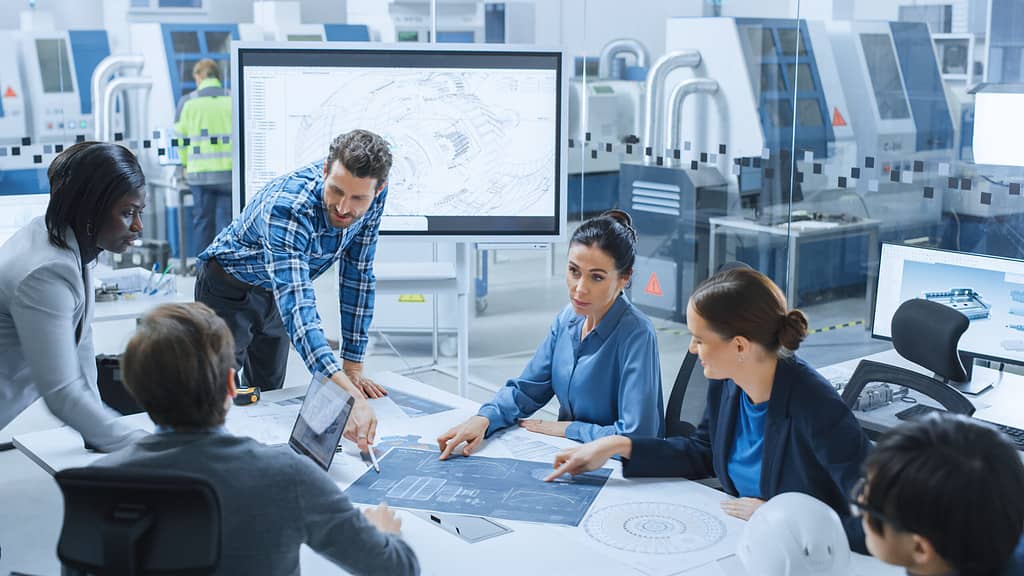
The Hidden Factory: Understanding the Unseen
Published:You claim your process yield is 98%. Are you sure? Have you considered your hidden factory? Let’s find out why you should.
Read more »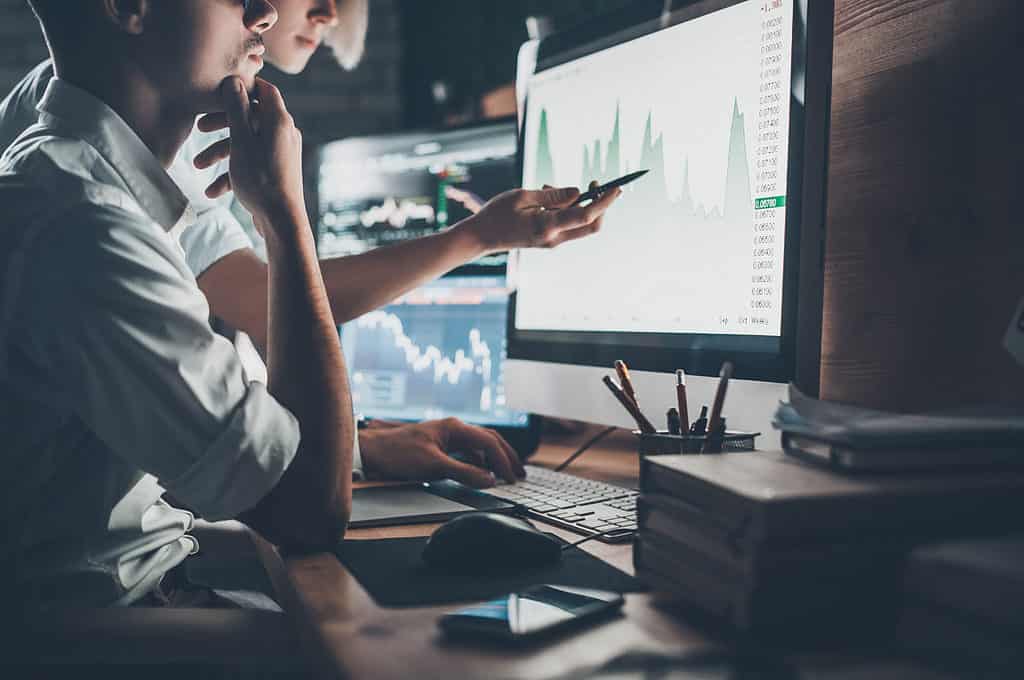
Random Sampling: Key to Reducing Bias and Increasing Accuracy
Published:Random sampling is a statistical method of selecting a sample of data from a larger set in such a way that each data point has an equal chance of being selected so that the sample represents the population from which it was drawn. What Is Random Sampling? Random sampling is a method of […]
Read more »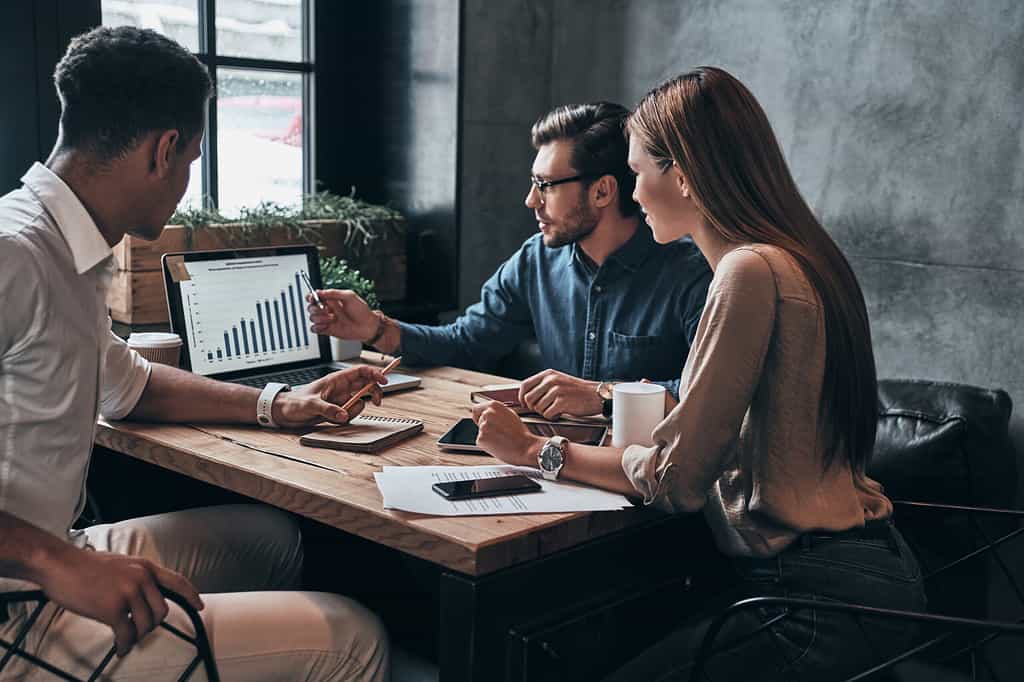
Span: Catching Variation in Your Data
Published:Span is a descriptor of the spread or variation of your data. It is a simple calculation that eliminates the impact of any outliers or unusually high or low values in your data set.
Read more »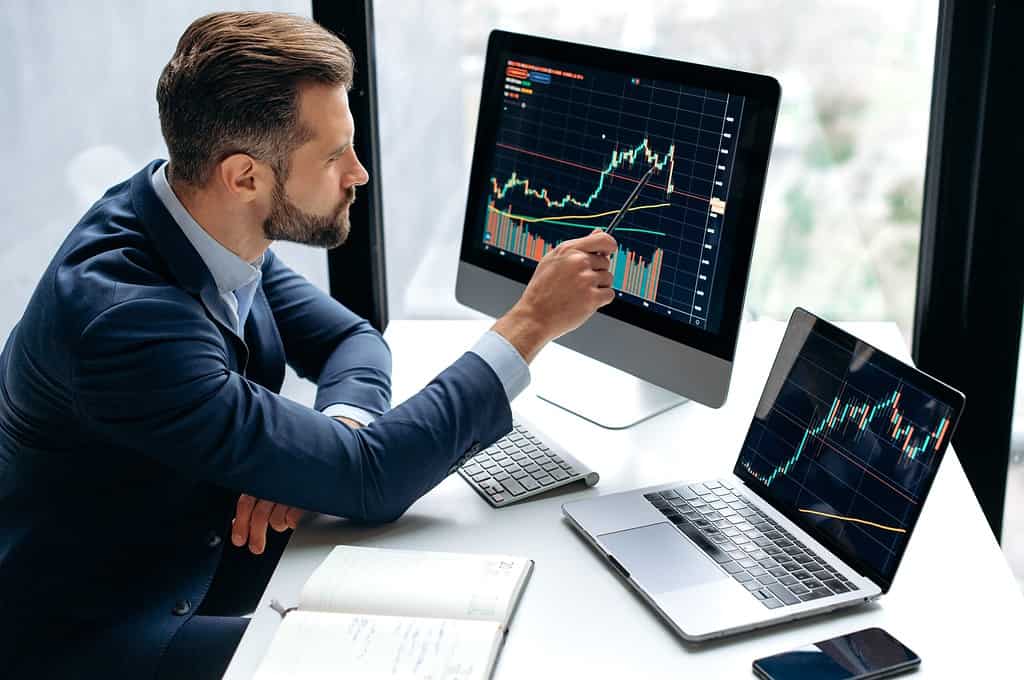
Trend Charts in Quality Management: Enhancing Process Monitoring
Published:You can learn a lot about your process by monitoring its change over time. There are different trend charts which will allow you to do that. Let’s look at a few.
Read more »
The Psychology Behind the Likert Scale
Published:What if you were asked to rate this article on a scale of 1 to 5, with 1 being you didn’t like it and 5 being you loved it. That’s an example of a Likert Scale.
Read more »
Variable Data: Seeing the Change in Your Data
Published:Data is just data, right? Hardly! We hear about discrete data, attribute data, continuous data, and variable data. Let’s unravel some of the confusion.
Read more »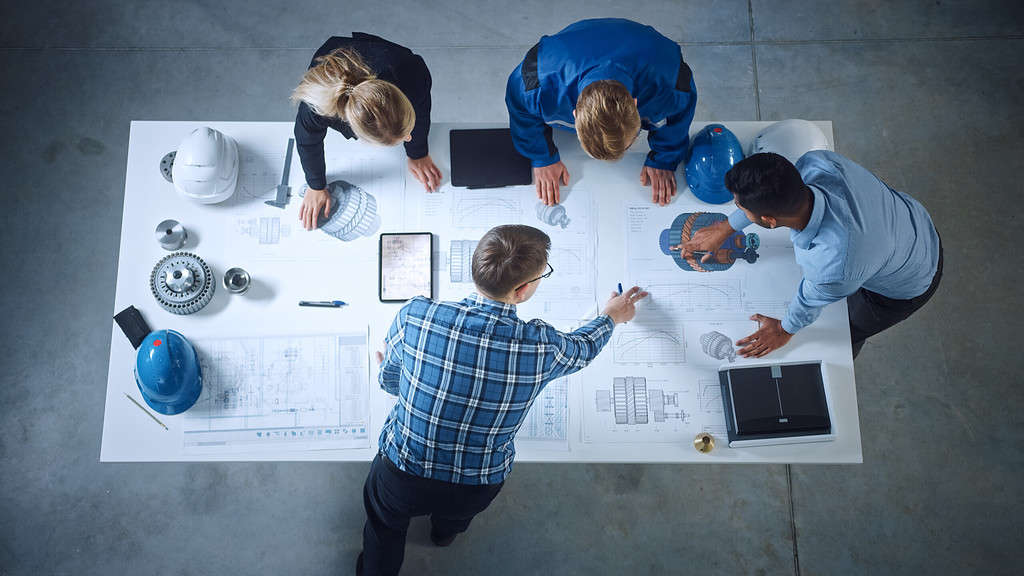
Identify, Design, Optimize, Validate: A Proven Approach to Designing High-Quality Products
Published:Incremental and continuous improvements are great. When appropriate, breakthrough improvement is even better. IDOV (identify, design, optimize, validate) is one tool for accomplishing this. Let’s see how.
Read more »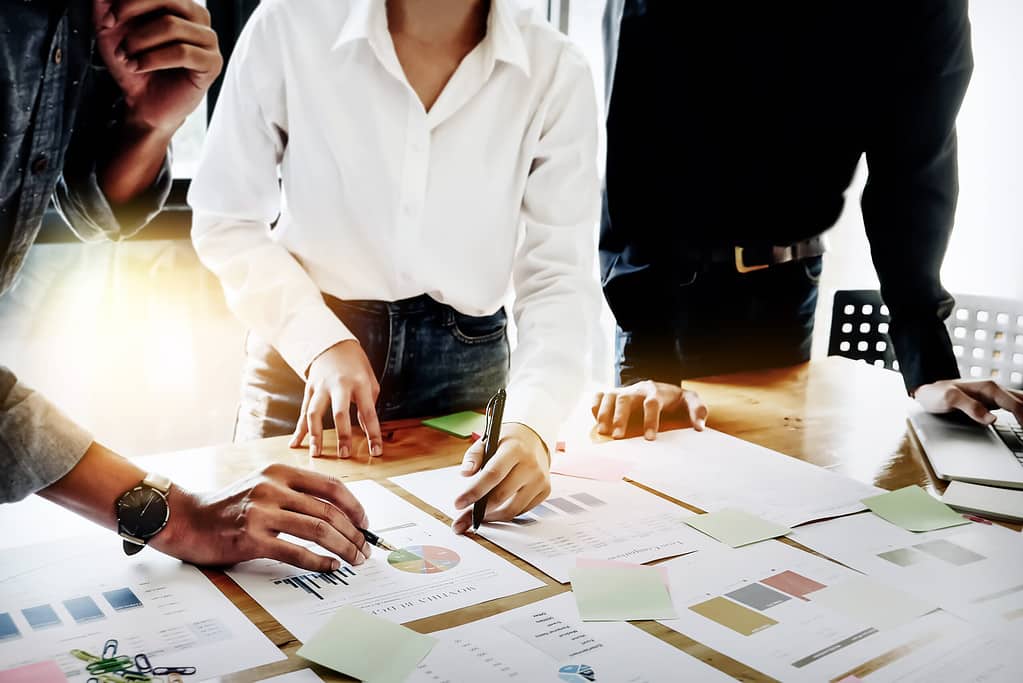
The Role of Process Owners: Driving Efficiency and Quality in Organizations
Published:The role of a process owner in Lean Six Sigma goes beyond being a mere title or designation. By assigning dedicated process owners, organizations can unlock the true potential of their processes, driving efficiency, quality, and customer satisfaction In today’s dynamic business landscape, organizations constantly strive for efficiency, quality, and continuous improvement, all […]
Read more »
Interaction: See the Effects on Your DOE
Published:The phrase “it depends” sums up the concept of interaction in the context of Design of Experiments. Interaction is when the effect of one factor on a response variable depends on the level or setting of another factor.
Read more »
How to Identify and Manage Stakeholders in Your Six Sigma Projects
Published:Your Six Sigma project will usually focus on a process with customers who directly receive the output of your process. But there are also others who will be impacted and have a stake in the outcome of your project. They are called stakeholders, and you need to understand them.
Read more »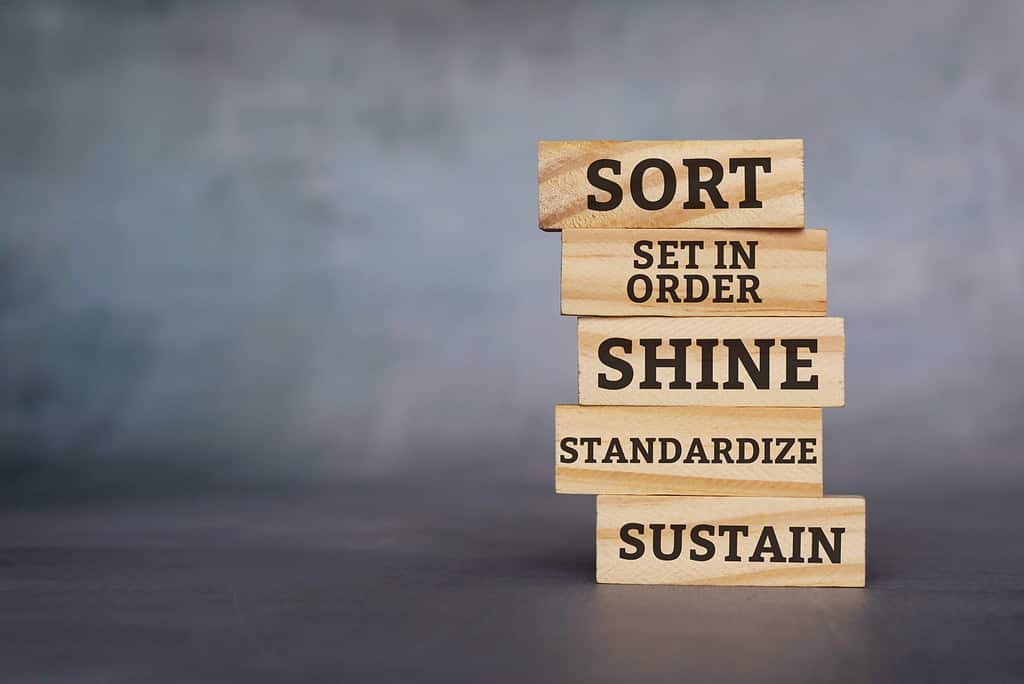
Sorting, Configuring, and Cleaning: The Three Core Principles of 5C
Published:5C is the formal activity of organizing the workplace, and it serves as the foundation of any continuous improvement effort. Explore the 5C framework, and learn how to implement it in your organization.
Read more »
Z-Score: A Handy Tool for Detecting Outliers in Data
Published:Some say that Z is the sign of Zorro (Spanish for fox), the fictional sword-wielding masked vigilante who defended and helped the poor. In statistics, it is something different. In statistics, z usually refers to the standardized score or z-score of a data point in a normal distribution. The z-score measures the number […]
Read more »
Analytical Modeling: Turning Complex Data into Simple Solutions
Published:Complex math is often the best way to make sense of a confusing maze of quantifiable variables and conditional relationships.
Read more »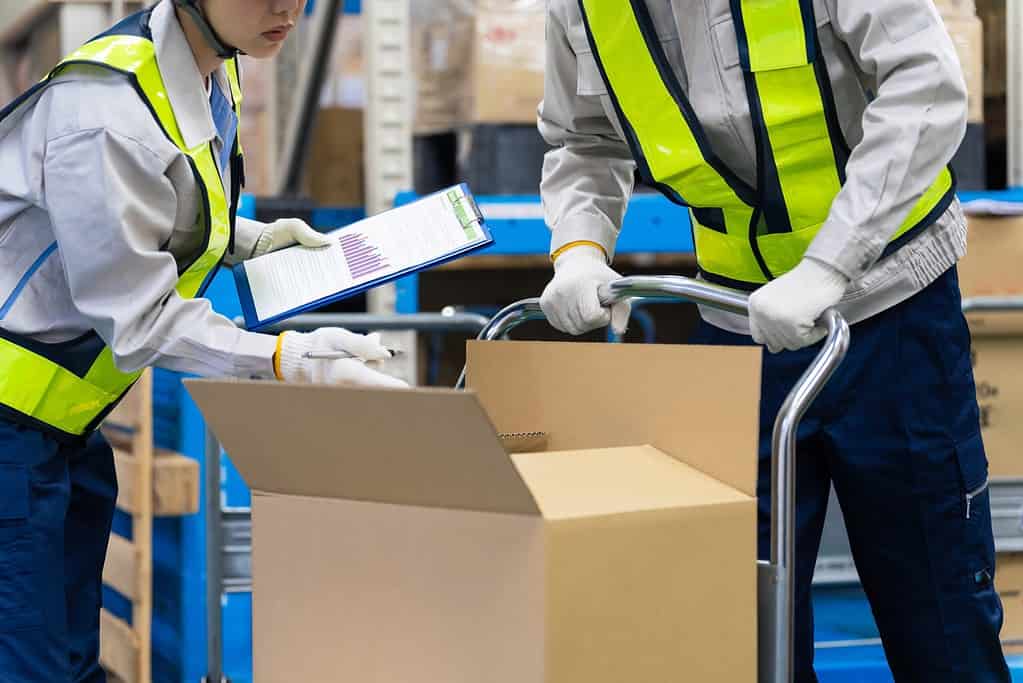
Ensuring Excellence from the Start: The Role of Incoming Goods Inspection
Published:An in-depth look at how IGI can help businesses become more efficient, profitable, and less wasteful by helping managers keep track of incoming good compliance issues while ensuring incoming goods meet quality standards set by the company.
Read more »
Exploring the Benefits of Autocorrelation in Time Series Analysis
Published:To optimize the benefit of your forecasting, you would like your time series values to be independent. Unfortunately, sometimes your values are correlated. This autocorrelation will have an impact on your ability to interpret what the data is telling you. Autocorrelation refers to the correlation between a time series variable and its lagged […]
Read more »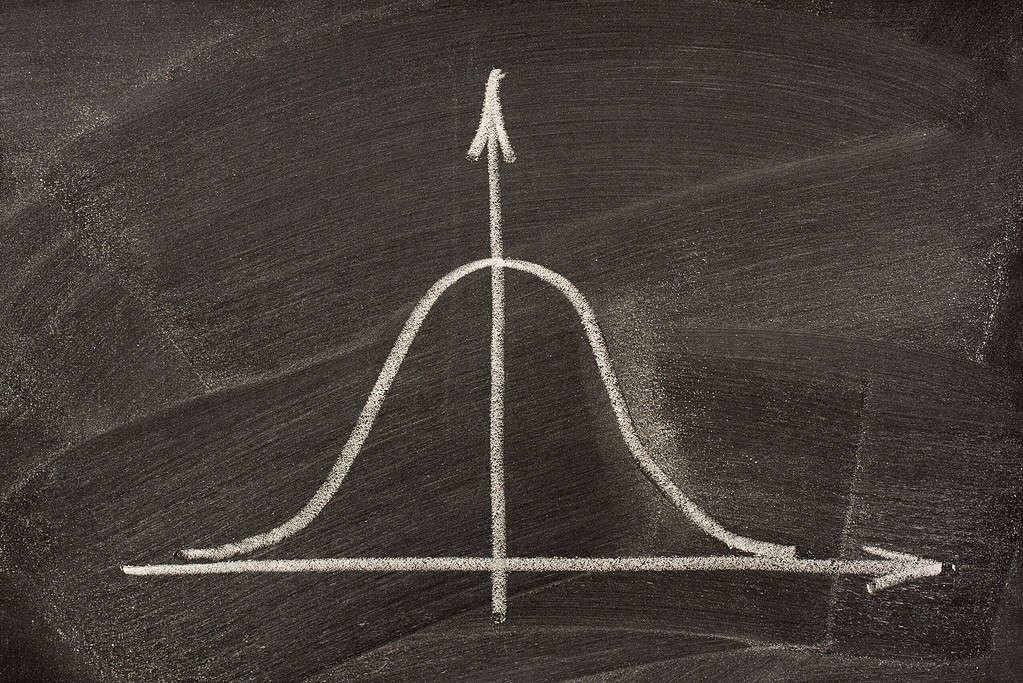
Skewness in Data: What It Is and How to Interpret It
Published:When someone says your data is skewed, do you get upset? Skewness can be a natural state of your data. Let’s find out more about skewness and what it means.
Read more »
Achieving Process Stability with Common Cause Variation: Strategies for Success
Published:This article will introduce you to common cause variation, one of the foundational concepts in quality improvement. We’ll explore guidance for the successful use of common cause variation in process improvement.
Read more »
How to Use Entitlement to Drive Process Improvement
Published:Entitlement is defined as the best performance you can reasonably achieve with the existing process.
Read more »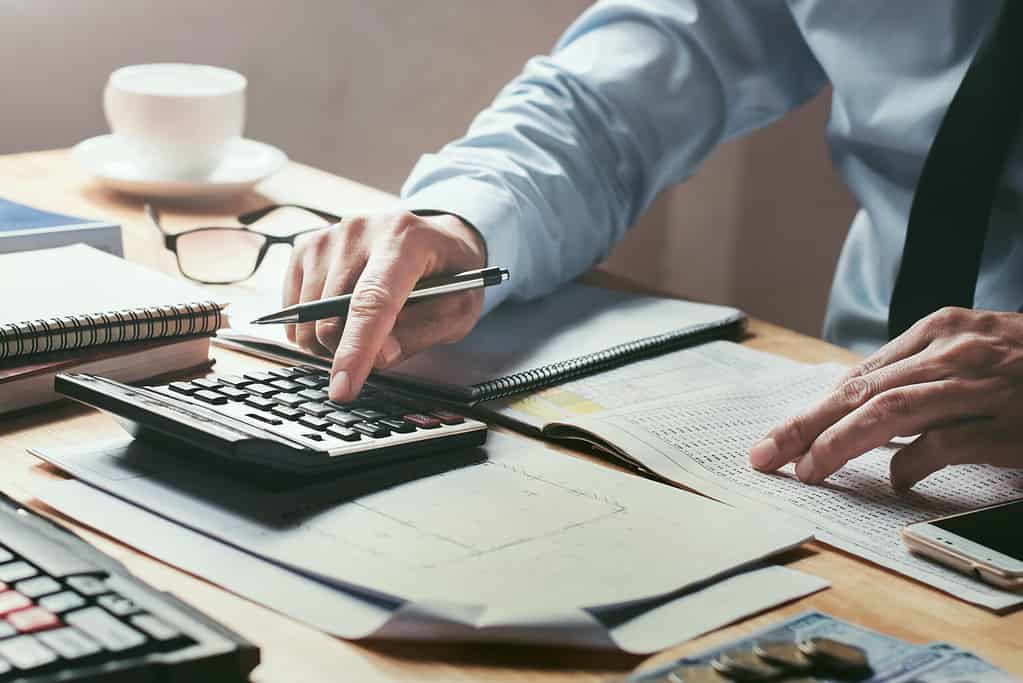
Mean in Lean Six Sigma: How to Interpret Your Data
Published:Central tendency and mean are two of the more significant statistics that are used in Lean Six Sigma. These two concepts have a large place in the developed world of LSS and are important when it comes to implementing new technologies or measuring processes for improvement.
Read more »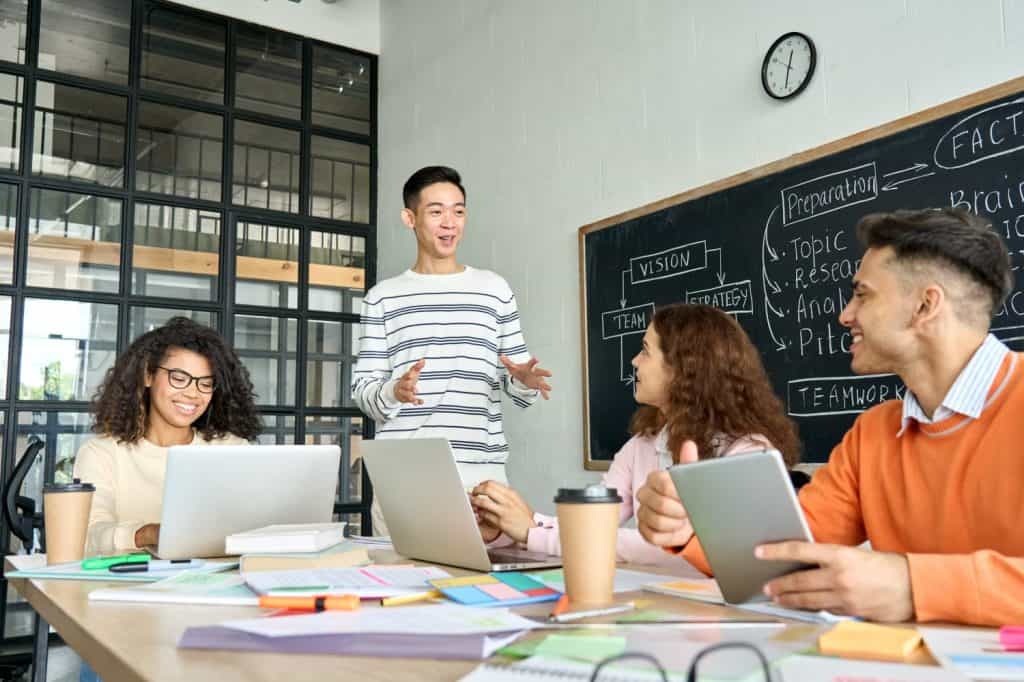
Low-Hanging Fruit: Easily Transform Your Organization
Published:A competitive and successful business needs to critically evaluate all the opportunities for improvement and deploy valuable resources strategically. By identifying low-hanging fruit, high-impact, low-effort activities can be addressed creating a solid foundation for continuous improvement.
Read more »
Insights from COPIS for Improved Efficiency
Published:What does your process look like from 30,000 feet? Your extended process view can be described using COPIS, or customer, output, process, input, and supplier. Let’s get in our balloon and go up.
Read more »
Subjective Rating vs. Ranking: Which Is the Better Data Collection Method?
Published:Subjective ratings and rankings can be used in a variety of applications, such as assessing job performance, gauging customer satisfaction, and monitoring the morale of your workforce. Find out more about this Six Sigma term.
Read more »