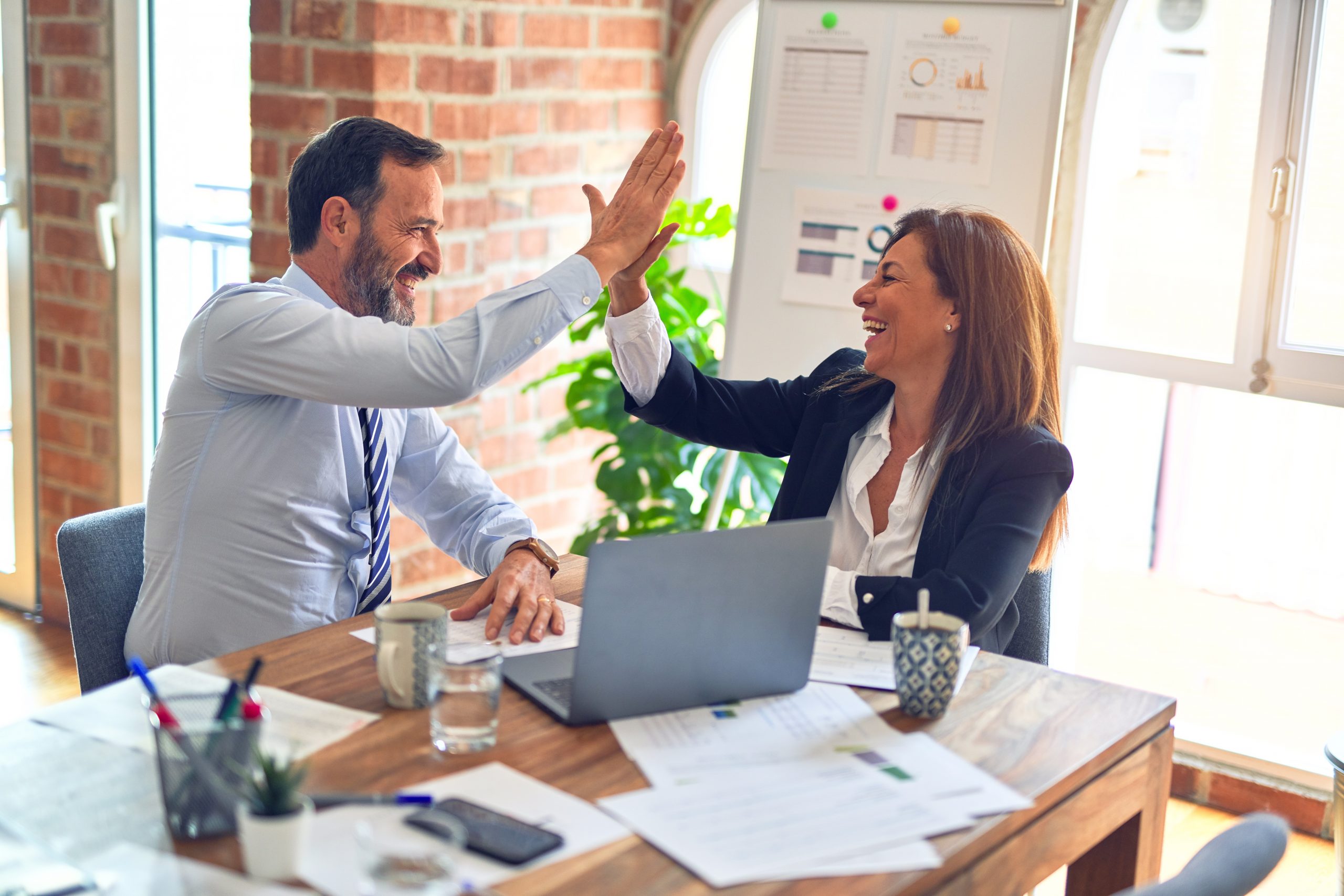
Companies lose an average of 5 percent of revenue annually due to payroll process inefficiencies, errors and fraud. Leaders at Océ Business Services, a provider of outsourced document process management services, estimated that their company had an even greater opportunity because of their outsourcing model – employees based on client premises supporting thousands of individual locations. The company assigned a Six Sigma team to examine the payroll process with the goal of reducing risk, increasing accuracy and improving efficiency.
Defining the Goal
A Master Black Belt and a Green Belt assembled a cross-functional team from the operations, payroll, systems development and human resources departments to work on the project. Their charter: Decrease the risk of payroll fraud and inaccuracies by reducing or eliminating opportunities for payroll errors.
During the Define phase of the project, the team realized that the biggest opportunity for improvement occurred during the time-collection and calculation processes used by managers for the company’s 5,000 hourly employees to determine how many hours employees worked and thus how much they should be paid. While mapping existing processes for submitting hours to payroll, the team found that managers utilized a mixture of approaches for collecting employee time. Managers spent a great deal of time manually calculating hours worked and translating them into the proprietary Océ Business Services I-Times payroll application.
Errors resulting from variations in the payroll process produced an estimated $1 million annually in unwarranted payroll expenses. In other words, the company was spending a significant amount of money paying employees for time when they were not working.
Measuring and Analyzing the Issues
In a survey of 325 managers responsible for submitting time records, the responses indicated that as many as 30 percent of the sites did not have an effective means of tracking and reporting employee time. Less than 30 percent of the managers utilized time clocks at their sites (Figure 1). Results also indicated that 30 percent of the managers surveyed did not keep physical records of time worked by employees. Only 15 percent of sites were utilizing I-Times for payroll entry.
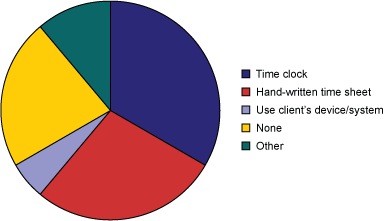
Fifteen percent of the respondents did not deduct time for employees unless they arrived to work more than 15 minutes late. Eight percent did not deduct any pay, even when employees arrived more than 15 minutes late. Corporate policy allowed for a seven-minute grace period. More than 50 percent of the survey respondents used the wrong grace period for lateness (Figure 2).

Finally, the survey responses indicated that only 52 percent of sites required employees to clock out at lunchtime. Many state regulations require that employers maintain accurate records relative to employee lunches and breaks.
The team collected sample data across multiple sites and validated that the following root causes were primarily responsible for defects produced in the information submitted to payroll:
- The existence of multiple processes for collecting time data, including time clocks and handwritten time sheets
- Manual calculation errors for hours worked
To determine the financial cost of the defects produced from the existing processes, the team conducted a pilot test. The pilot enabled the team to make accurate financial projections of the benefits of implementing an improved time and attendance system. The test showed that there was a 0.5 percent error rate in manual data calculations. According to the pilot projection, a reduction in the number of defects produced during the time collection, calculation and reporting processes would result in the reduction of an estimated $1.2 million in annualized payroll expenses.
The project team used this information to make the case for the required improvements to the time and attendance system.
Improving the Payroll Process
The team investigated various technology options for collecting employee hours worked that would address the identified root causes and fit the company’s cost constraints. After an exhaustive search and evaluation against multiple criteria, the team identified an automated time and attendance system (ATAS).
This system addressed all of the root causes for defects, and provided standardization, automated time calculations and structured policy compliance. Additional benefits included quicker payroll processing and better reporting systems.
The ATAS includes browser-based timesheets, browser-based web clocks, biometric readers and phone-based interactive voice response. It ensures that employees work within designated limits, maintains detailed time and labor audit trails, properly credits employees for actual work, and mitigates risks.
Prior to the change in the time-collection processes, the average number of hours paid over a two-week period was just over 80 hours per employee. Once the automated time-collection and calculation system was implemented, the average time worked per employee dropped to 78.6 hours over two weeks. In other words, by removing manual processes and time estimations, the team reduced variation and decreased the average hours paid by 1.5 hours for each payroll cycle (Figure 3).

Solution Roll-out
The ATAS was rolled out in several phases. This allowed the project team and the application provider to identify and correct issues as they were discovered. It also allowed the human resources department to conduct the training needed for all employees and management. By June 2009, all locations used the new system. With little disruption, the project team changed the way the entire company was collecting and reporting employee hours.
The implementation phase of ATAS lasted just under six months. The vendor configured the application to match the rules that Océ Business Services uses to administer pay. In addition, the IT department worked with the ATAS provider to ensure that the application was integrated with Océ Business Services accounting systems.
Controlling the Process
The company’s payroll expenses decreased dramatically as a result of the improvements. As shown in the control chart (Figure 4), the company realized significant benefits as the program was implemented across the organization.

Control data indicated that the team achieved its goals. The improved process and technology reduced errors associated with hours-worked calculations and the opportunity for fraud that could arise from the use of hand-written time sheets, standardized time entry systems, and created a system that enforced company policies automatically. Although the team initially projected a $1 million annual savings, the final results achieved far more than the projection. Based on current trends, the team predicts that the improvements will deliver more than $1.9 million annually to the bottom line.