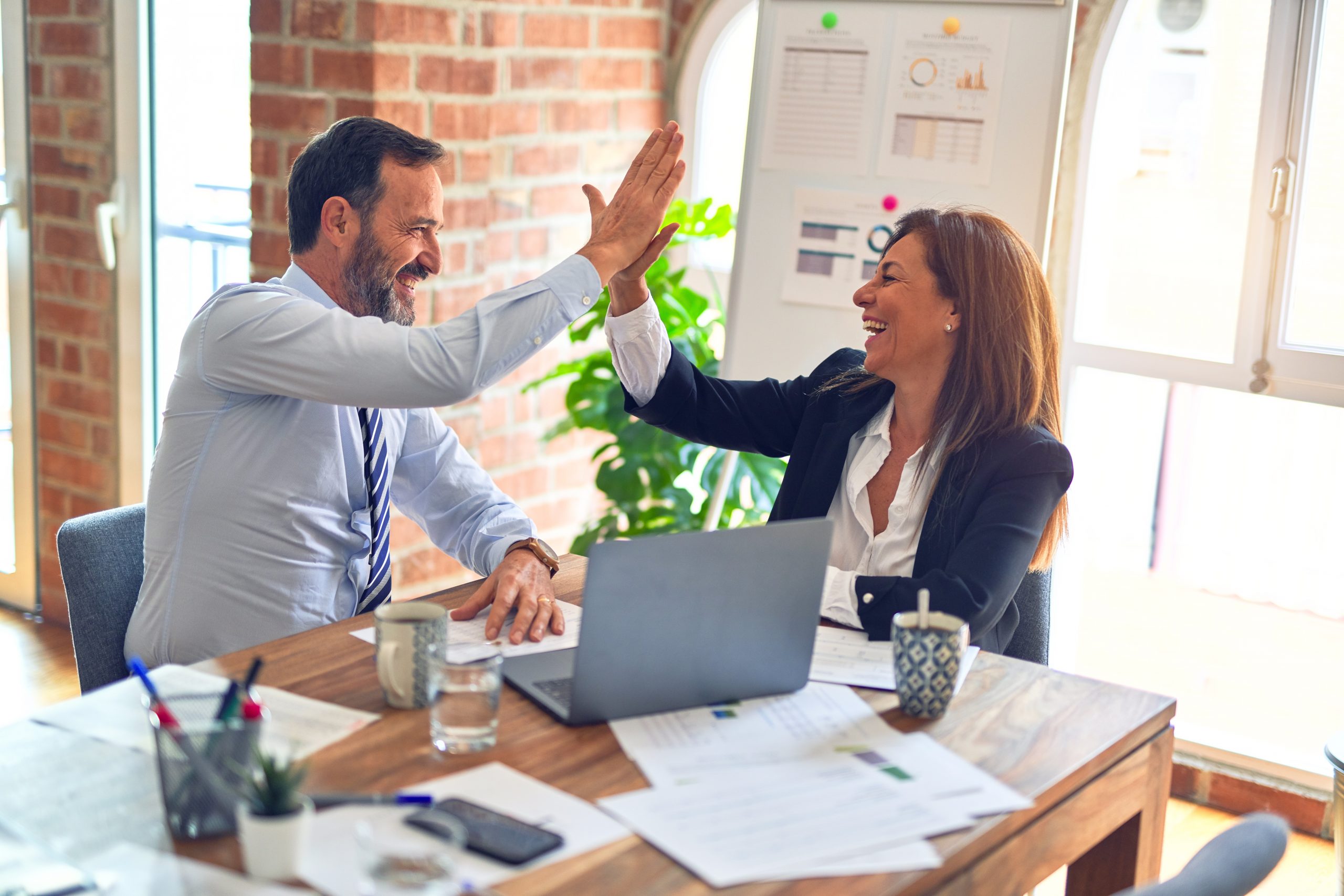
In my process engineering experience I have found a good number of people confused about the important process measure indices of capability and performance. The capability index is useful for measuring:
- Continual improvement using trends over time, or
- For prioritizing the order in which process will be improved, and
- For determining whether or not a process is capable of meeting customer requirements.
- This latter use is the original intent of the capability index and should not be applied to performance index.
Capability for variables data can be described in terms of the distance of the process average from the specification limits in standard deviation units, Zmin = minimum of ZUSL or ZLSL. The Z-index helps to predict the yield if normal data distribution are applied. Capability may also be measured with Cpk index, which accounts for process centering and is defined as the minimum of CPU or CPL. It relates the scaled distance between the process mean and the closest specification limit to half the process spread, that is the six sigma range of a process variation. Both indices relate to each other, Cpk = Zmin /3.
The question is what process variation we mean, and what sigma should be applied to describe a variation. A process may be qualified as a short-term, which is based on measurements collected from one operating run, and a Long-term, when we study data collected over a longer period of time. Accordingly, two kinds of variation have to be distinguished:
- Inherent process variation, that is portion of process variation due to common causes only
- Total process variation, that is the variation due to both common and special causes
As far as namely the common causes of variation should be reduced to improve process, we have to focus on inherent process variation, and to study short-term capability, or simply called capability. The capability actually reflects past-process performance.
The inherent process variation should be estimated from control charts using a simple formula for sigma, s = R / d2, where R is the average of the sample ranges, and d2 is a constant varying by sample size, which values can be found in statistical table (d2 = 2.33 for often used sample size equaled 5). So, we should use not a total, or actual, but estimated sigma s to measure capability index, Cpk.
On the other hand, a long-term capability, based on total process variation, reflects future-process performance or simply called performance, which is quantified by Ppk index. In this case, sigma total should be estimated that include both the within-subgroup variation along with the effects of any shifting between subgroups. In other word, we have to use Sigma s– the average of the sample standard deviation, using all of the individual readings obtained from either a detailed control chart or a process study. To be more exact, to evaluate performance, we should again allow for sample size n used, and take sigma = s / c4, where constant c4 can be found from statistical table (c4 = 0.94 for n=5).
I assume that many quality-responsible people compute the performance measure Ppk while thinking that they measure process capability, Cpk. Moreover, the capability indices sometimes are measured for statistically unstable process that is meaningless. Process data normal distribution (this is the point of a separate discussion) must also be prerequisite to measure of process capability. Even when those conditions are met, it is difficult truly understand a process on the basis of a single index, whichever. The indices Cp and/or Pp should be used in conjunction with Cpk and/or Ppk to account for both spread and centering.
Capability studies can estimate future process performance only when such performance is consistent over time (stable process). A stable process may be predictable. To estimate the process potential, the performance index Ppk should be used along with sigma standard deviation s. It has to be employed only to compare to or with Cp and Cpk, and to measure and prioritize improvement over time. To estimate whether a process is capable to meet customer requirements, we should use Cpk index along with sigma estimated s = R / d2. The performance index is obviously lower than the capability index.
It is also strongly recommended that graphical analyses be used in conjunction with the process measures. Examples of such analyses include control charts, plots of estimated process distributions, and loss function analysis graphs. In addition, particularly for unstable processes, it might be helpful to plot inherent process variation s2 versus total process variation s2 to gain an appreciation for a rough perception of the gap between the process capability and performance, and to track improvement. These types of graphical analyses should be done for better process understanding even if process measures (i.e., Cp, Cpk, Ppk, etc.) are not computed and/or used.