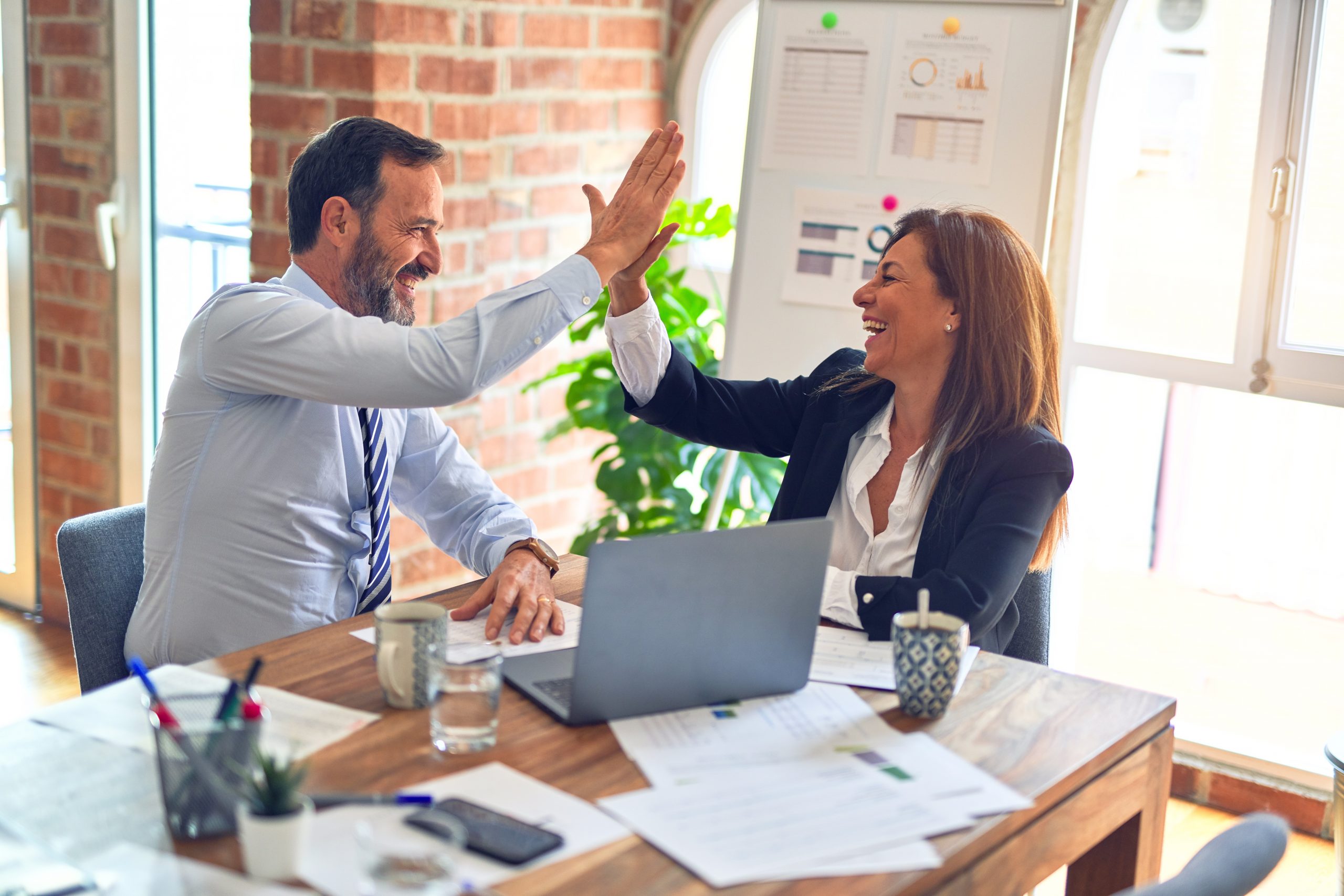
While managing process improvements on a daily basis, it is easy to lose sight of the big picture. Practitioners may view every separate event with a unique perspective using a different dimension and frame of reference than they would use to view other, seemingly unrelated events. When addressing each event, problem and improvement in isolation, there is a possibility that practitioners will just improve things right, rather than improve the right things.
Using systems thinking can give practitioners a powerful perspective, a universal framework, and a set of specific tools to solve complex problems in life and work to get sustainable solutions.
What Is Systems Thinking?
A system is an interdependent group of parts forming a unified pattern. Systems thinking is the ability to see things as a whole (or holistically), including the many different types of relationships between the diverse elements of a complex system.
The traditional process improvement analysis breaks a system down into its parts, tries to explain the behavior of these parts and then attempts to aggregate this understanding into an understanding of the whole. It may not always succeed because when a system is taken apart, the system and its parts lose their essential characteristics.
Consider a car. If a mechanic makes improvements to the steering wheel or radiator, does it guarantee that the car will run faster? The answer is clearly no, because the mechanic has only addressed parts and not the system. The same holds true for most complex systems and organizations.
Systems thinking is a conceptual framework for practitioners to go beyond events, to view patterns of behavior and seek underlying interrelationships, which are responsible for the patterns of behavior and the events. It is based on the principle that the component parts of a system will behave differently when the interrelationships are removed and seen in isolation.
Why Is Systems Thinking Needed?
To better understand the need for systems thinking, it may help to analyze a sample situation. In this example, the employees in the operations department of a manufacturing firm are complaining that they face several issues related to email and the Internet that are time-consuming to resolve because the typical lead time for issue resolution by the information technology (IT) help desk is quite high.
A practitioner’s first thought for improving this situation might be to launch a Six Sigma project to reduce the lead time of resolving IT issues. Systems thinking, however, would suggest understanding where and why the issues arise in the first place and the interrelationships that exist in the system. In the example, the manufacturing firm employees have spent most of their professional lives in factory shop floors, and do not have even the basic computer skills needed to solve minor issues. That lack of skills leads to a higher volume of requests received by the IT help desk. Therefore, it takes longer for the IT technicians to resolve issues. Using systems thinking, the solution for this problem is providing training for employees to improve their basic computer skills.
Simply reducing the response time of the IT help desk may discourage the employees from acquiring those basic computer skills and becoming self-sufficient. That is an example of the destructive effect of improving a process or resolving issues in isolation.
Systems Thinking Tools and Concepts
There are a number of tools and concepts that help practitioners in the systems thinking process:
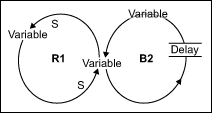
Causal loop diagrams consist of arrows that connect variables, which change over time, in a way that shows how one variable affects another (Figure 1). The direction of the relationship is labeled same (S) or opposite (O) based on the direction of causation. Time delays can occur and are important. Each loop is also given one of two labels:
- Reinforcing (R) – The causal relationships within the loop create exponential growth or collapse.
- Balancing (B) – The causal influences in the loop keep things in equilibrium.
Behavior-over-time graphs are similar to typical line graphs. They have vertical and horizontal axes and a line that shows how a parameter is changing over time. These graphs depict patterns of behavior that practitioners should explore, and also encourage them to think about what time-frame to consider.
Systems archetypes are common patterns of behavior in organizations. As diagnostic tools, they provide insight into the underlying structures from which behavior and events emerge over time. The archetypes can be used in two ways: diagnostically and prospectively.
Archetypes are based on the method of universal behavioral patterns. Each archetype has characteristics that illustrate problems encountered in daily life and a set of strategies to solve them. There are 11 negative (undesired) and positive (desired) archetypes in the systems-thinking approach. The archetypes are mapped out so that practitioners can examine the parts of a system and the relationships among those parts to understand and work through the problem. The archetypes themselves consist of causal loop diagrams.
The 11 common archetypes are:
- Tragedy of the commons
- Limits to success
- Accidental adversaries
- Balancing loop
- Drifting goals
- Escalation
- Fixes that fail
- Growth and underinvestment
- Reinforcing loop
- Shifting the burden
Stocks and flow diagrams contain specific symbols and components that represent the structure of a system (Figure 2). Stock is any entity that accumulates or depletes overtime, such as head count or material inventory; the flow is the rate of change in a stock. Mathematically, a stock is the integral, or accumulation, of the flows over time.
Stock is represented by a rectangle and flows are indicated by valve-like structures. The net revenue in Figure 2 is the difference between revenue and expense.
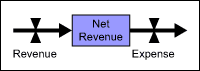
Practitioners may apply systems thinking to help them understand a wide range of corporate, economic, political and ecological systems.
While Six Sigma can be utilized to focus on data (raw facts) and information (interpreted data), systems thinking may enable practitioners to focus on knowledge, which is derived from information by integrating information with existing knowledge, and thus provide a broader degree of understanding.
From a strategic view, systems thinking can help to identify which functions or departments within an organization should be prioritized for launching process improvement projects. From an operational point of view, system-thinking tools can be used in conjunction with Six Sigma or Lean techniques in the various stages of a process improvement project.
Creating a Better Process
Some practitioners tend to go after the low-hanging fruits or quick fixes, which takes their attention away from viewing the state of affairs from the systems perspective. As the worlds of business and technology are growing more complex, it is essential to understand not only the parts of a system, but also to focus on the interrelationships in a system.
By looking at issues through a systems-thinking lens, it is possible to work with a system and not against it – and to deliver sustainable and comprehensive process improvements. Essentially, systems thinking will improve the process of process improvement.