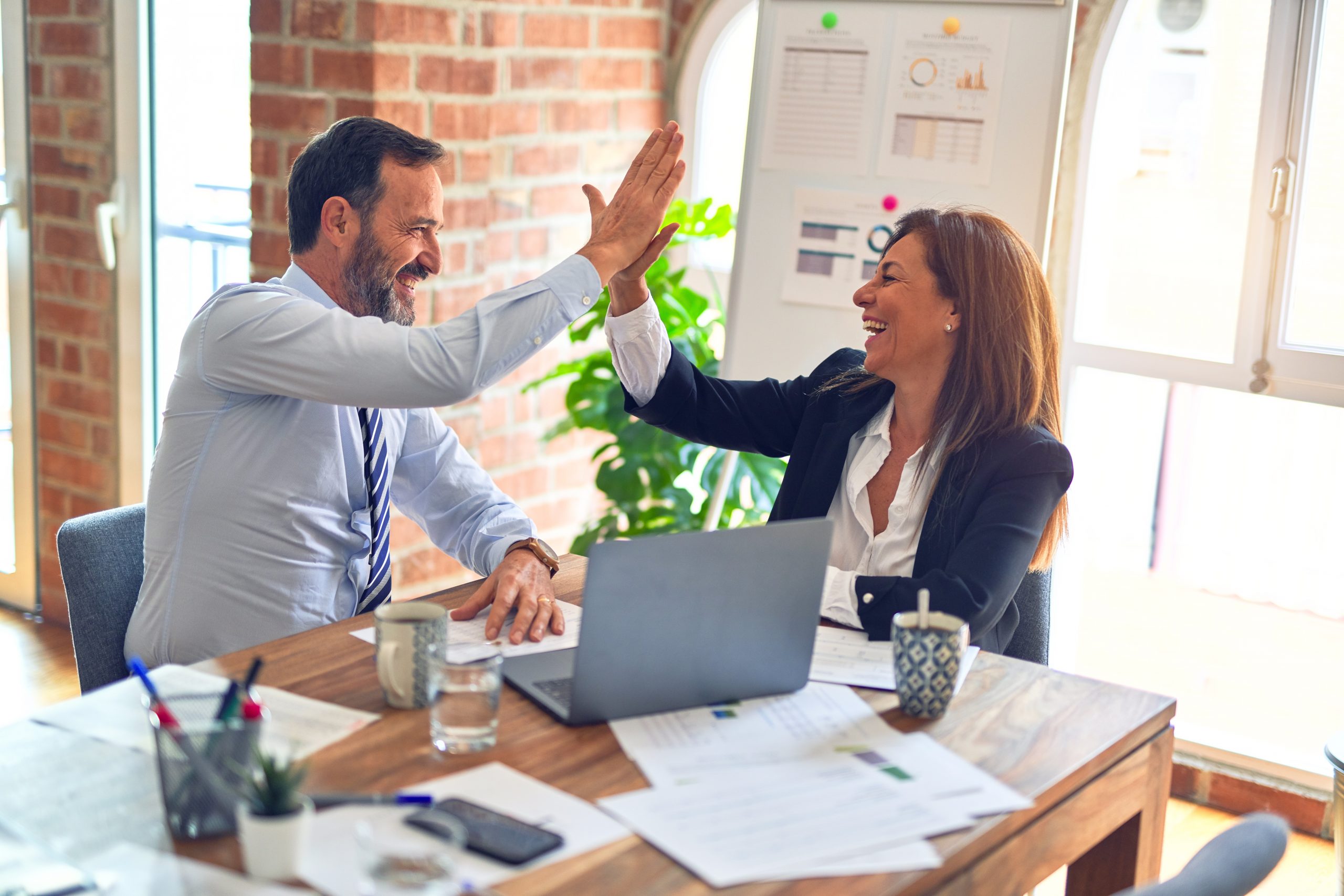
Xerox has a successful history applying Lean Manufacturing techniques in their operations since the early 90s. In 1998 Six Sigma was introduced in various manufacturing and supply chain operations. Although these operations achieved efficiencies, the scope of the deployment was limited. In 2002, Six Sigma and Lean were integrated and driven as a corporate-wide strategy. For a complete history Six Sigma at Xerox, read Xerox Lean Six Sigma.
Forbes.com recently published an interview with Lawrence Zimmerman, CFO of Xerox. When asked how Xerox keeps its prices competitive, Zimmerman responded:
“Xerox has become a Lean Six Sigma company. We’re focused on efficiencies in our operations and in the ways we deliver value for our customers. Lean Six Sigma projects have already contributed hundreds of millions of dollars in cost savings, cost avoidance and revenue to the company. More than 1,500 projects have been completed or are under way with the assistance of more than 600 Xerox Black Belts and Master Black Belts.”
Forbes.com, Aug 12, 2005
Savings and Benefits
“Internally, we’ve generated more than $150 million in economic profit during 2004. These are reductions in our operational costs and driving our revenue.”
Dave Rowlands, VP Quality, Xerox
nextslm.org
“In 2000 the company rededicated itself to quality—long a core value at Xerox—and updated its set of quality principles and resources to be faster and more focused. “New Quality” integrated components of Xerox’s traditional “Leadership Through Quality” strategy and was strengthened with Six Sigma concepts. Building on that experience, in 2002 Xerox began an enterprise-wide effort integrating Six Sigma and Lean Manufacturing tools and processes into a comprehensive strategy called Xerox Lean Six Sigma. It is a disciplined, data-driven method of reducing waste and variation in processes so they consistently deliver products and services at the quality levels, speeds and prices that customers value—and therefore improve Xerox business results. Dedicated Xerox Lean Six Sigma deployment managers and “Black Belt”-led projects now exist in every business throughout the company.”
Xerox Online Fact Book for 2003-2004
“Using Xerox Lean Six Sigma methodology, we analyze in detail all of the document intensive processes our customers use to run their businesses. We identify the exact costs of the way our customers manage printing, copying, faxing and scanning functions. Perhaps even more importantly, we analyze the way real people work with real documents in the real world.”
“Office Document Assessments – a Six Sigma-based consulting tool – evaluate a company’s entire document environment to identify areas where operating costs can be reduced, processes simplified and productivity improved.”
“We will continue to introduce competitive technology, to drive costs down, to streamline our business, and to execute against our business model. To ensure that we are best in class in every aspect of our business, we have introduced Xerox Lean Six Sigma – a powerful set of tools that will drive improved results.”
Customer Case Study: Sun Microsystems
“The call to action from Sun Microsystems was to reduce its overall document management costs in Europe and South Africa where Sun operates 190 sites in 31 countries. Xerox Global Services conducted an audit of Sun’s document devices from printers and copiers to fax machines and scanners. The Xerox Office Document Assessment (SM) tool studied Sun employees’ use of devices, such as the number of pages printed in individual workgroups, why certain groups needed full-color printing more than others and why some employees depended heavily on scanning and faxing. Armed with data and a clear understanding of work practices in Sun’s offices, Xerox applied Lean Six Sigma practices to develop a more efficient document management infrastructure, guaranteeing a 25-percent reduction in Sun’s document costs. Through a multi-million dollar contract, Xerox is now responsible for Sun’s entire fleet of document devices in Europe and South Africa, managing the maintenance and supplies contracts not only for Xerox systems but also for products from other vendors. And, Xerox people serve as the frontline of support when Sun employees need assistance with any document system.”
Articles and Links
Xerox Lean Six Sigma, Xerox Website
Lean Six Sigma Leads Xerox, Xerox Website
Xerox Lean Six Sigma and Quality Go Hand in Hand, Xerox Website
Xerox Global Services Drives Quality with Six Sigma, Chief Learning Officer, July 3, 2003
How Xerox Got Up To Speed, BusinessWeek Online, May 3, 2004
Six Sigma Performs for Xerox, Search Takes a Bath, BtoB, Oct 27, 2004
Author Tells How to Put IT Costs on a Diet With Lean Six Sigma, nextslm.org