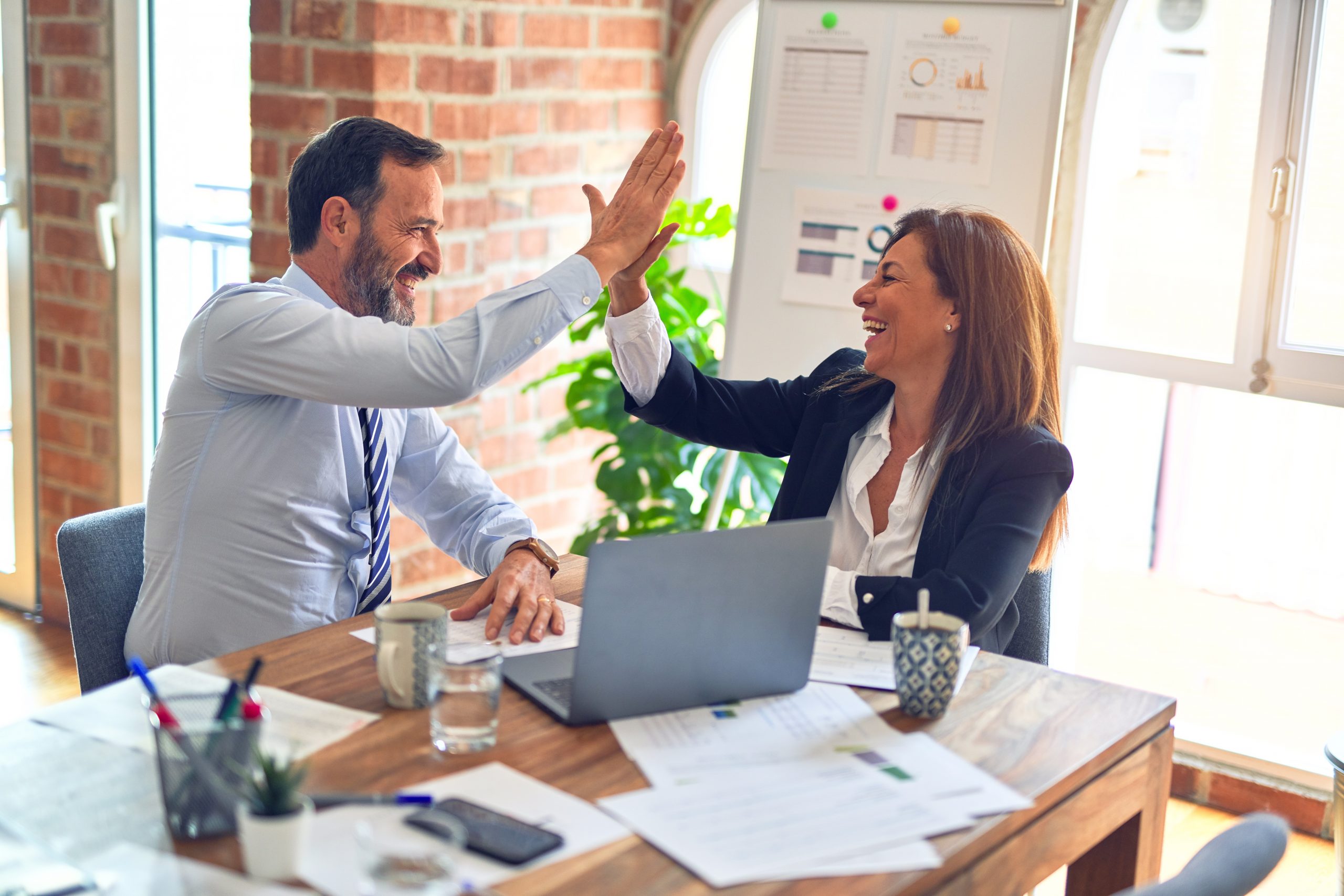
Time flies! My last “week of a Black Belt” blog dates from May 12th already. Anyhow, when things are busy and interesting things happen, there are lots of ideas to blog about, but no time to actually publish them.
Six Sigma’s 20th anniversary will be celebrated soon. Since 1987 and its first success stories, it has not gone by unnoticed. The number of published books, consultant organizations, internet publications, are no longer countable …
However, many people I talk to remain with some burning questions “When is an organization ready to adopt Six Sigma?” In many cases followed by “Or should we do Lean first?” and “What about BPM, are we better of with that?”
I also observe that the companies who adopt it are generally local representations to US based multinationals or their suppliers. Also the infrastructure associated with a full pledged Six Sigma deployment is (rightfully or not?) perceived as too heavy on the small and medium enterprise that account for about 70% to our local economy.
Personally, I think it really doesn’t matter what name an effort goes under. In all methodologies are good tools that can bring a lot of value to any organization, whether it is big or small, in service, transactional or production environments. The best approach for the organization is depending on its level of maturity. Maturity here is not defined in terms of age or magnitude, but in terms of how well the organization knows its customers, their needs and how well the business processes are able to satisfy those.
Consider 2 examples:
1. An organization with low maturity. Typical characteristics of such an organization: strong functional silos, no continuous improvement culture (it works, so why change it?), no clear understanding of customer needs and wants, management cannot sum up core processes when asked …
This organization should start with the basics: get to know its processes, its customers and their needs. To achieve this, it should use VOC tools. It should use SIPOC, process maps or value stream maps to document its processes. Start documenting at a high level, e.g. core process level. Once this is done, it should look for the biggest gaps between the VOC and the process outputs. These should be this organization’s first improvement projects. The organization should be process mapping again to detail the (core) processes that most contribute to the identified gaps. It should use simple and basic quality tools to get to those improvements implemented. Along the way, it will surely find some waste in the processes. Eliminate it! After the improvements are in place and obvious waste is eliminated, the organization should reflect on the learnings and start again. All along the effort document everything. Look for possible (future) process measurements.
Some might call this endeavor business process management, some might call it lean, some may call it Six Sigma. It doesn’t matter! It’s about getting the basics right first and institutionalizing a continuous improvement culture. To get this in place, there is probably no need for advanced training, for Design of Experiment or Design For Six Sigma …
2. Consider the other end of the spectrum: an organization where core processes are defined andhave owners at high management level. Key Performance Indicators (KPIs) to monitor the performance are in place. The customer’s needs and expectations are known and understood.
Probably this organization has not just started a continuous improvement effort; they have started a while ago. However, the basic concepts of the improvement program are the same as in the low maturity organization, but this organization will need more sophisticated tools. This organization also needs to know its customers needs. The needs of customers today may differ of their needs tomorrow. Thus, by default, listening to the customers using VOC tools is a continuous ongoing exercise, for any organization.
Having KPIs measuring process performance, implies that measurement systems are capturing process data continuously. This data is reported hourly, daily, weekly, monthly, quarterly … KPIs are use to manage the daily operational business. This requires quality measurements! The interest is in detecting and understanding variation in the processes and making the correct fact based decisions.
Frequent gage R&R exercises will need to sustain the quality of measurement and consequently the quality of operational management. For improvement purposes, this organization will also need to identify its biggest gaps between its outputs and its customer’s expectations. This will create an improvement initiative engine as there is always room for improvement. As defect levels drop, the room for improvement by structured common sense will decrease as well, creating the need for more sophisticated tools and methodologies. This is the stage where e.g. DOE, DFSS, multiple regression, non-parametric tests and other come in.
So, when are we ready for Six Sigma ?