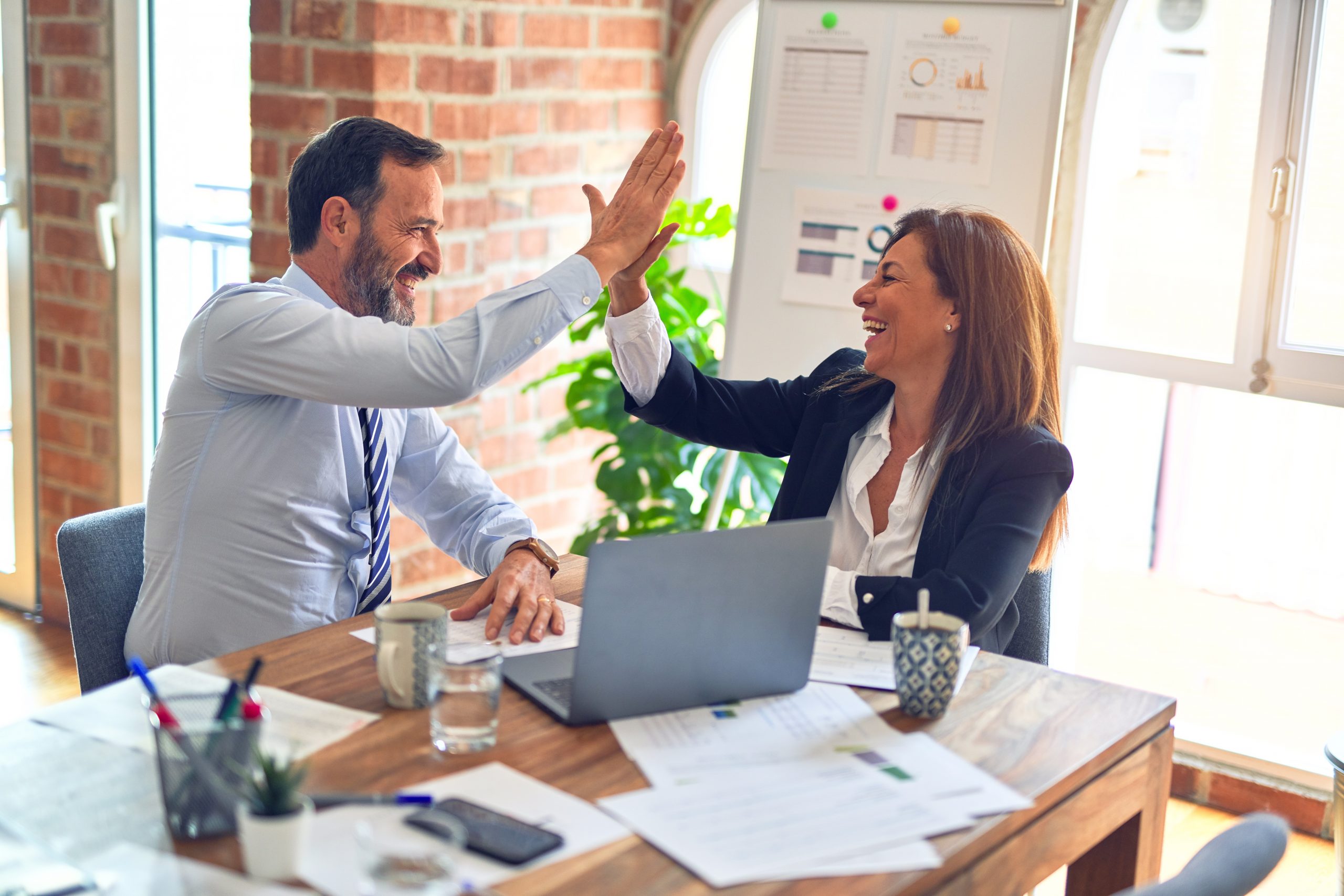
First, let’s define single minute exchange of dies (SMED), also referred to as quick changeover. This method was developed by Shigeo Shingo in Japan, and arose from automotive machine setups and changeovers that were taking up to 24 hours. This was downtime that was robbing production capacity. The SMED methodology focuses on the waste in the setups and reducing those wastes to optimally achieve a setup under 10 minutes (“single minute”).
I have been a part of implementing SMED at several companies as a Lean and Six Sigma consultant. SMED events are a great way to gain quick return on investment (ROI) to fund an implementation, but without the infrastructure for – and sustainment of – Lean and Six Sigma, the SMED efforts will eventually revert back to the old (unimproved) way. In my experience, there is a common misconception related to an effective implementation of the SMED methodology: focusing on an operator’s individual area rather than considering the cell as a whole.
Many of the organizations that I’ve worked with have had a previous SMED effort. As consultants, we are brought in to implement Lean and Six Sigma, which includes reducing setup or changeover time. As part of an SMED event, we have a primer on the first day to cover the purpose of Lean, Six Sigma and SMED in which we also discuss what happened during the SMED event that preceded our arrival. Most of the time, I hear the same thing: In companies that have cells of machines (or machines in a line or a “U” shape that are dependent on the previous machine), the operators tell me that the previous SMED efforts taught them the tools to speed up their machine. This is beneficial to learn. But those operators had not been taught how to speed up their cell as a whole. They had not been taught how to think of their cell as a combined entity.
The previous SMED education was to reduce changeover time of their machine. What is missing? The focus on the constraint in the cell setup. If I reduce the time to setup my machine by 20 minutes (from 40 minutes down to 20 minutes) but another machine that I am dependent on takes 60 minutes to setup, then my net setup time for the whole cell is 60 minutes. In this departmentalized thinking (reducing the setup time of “my” machine), the operators, after finishing their setup, start working on external tasks (tasks that can be done while the machine is running). These tasks are being performed while the cell is not producing.
We teach the operators an alternate understanding of SMED – one in which the focus is on reducing the setup time of the entire cell – not just their machine. They learn to focus on the longest setup in the cell. They determine (before the setup begins) what is the best “choreographed dance” to allow the team to flex (move to another machine) and setup other machines. This allows them to optimize capacity of the cell setup so that they can reduce setup time. This kind of thinking usually reduces setup times by 30 percent to 50 percent without making any other improvements. Once we make improvements to the setup time of each machine, the net setup time of the cell is further reduced.
Do you have a changeover process in your organization that has multiple processes in a line or cell? Have you had an internal effort to reduce setup/changeover time that did not work?