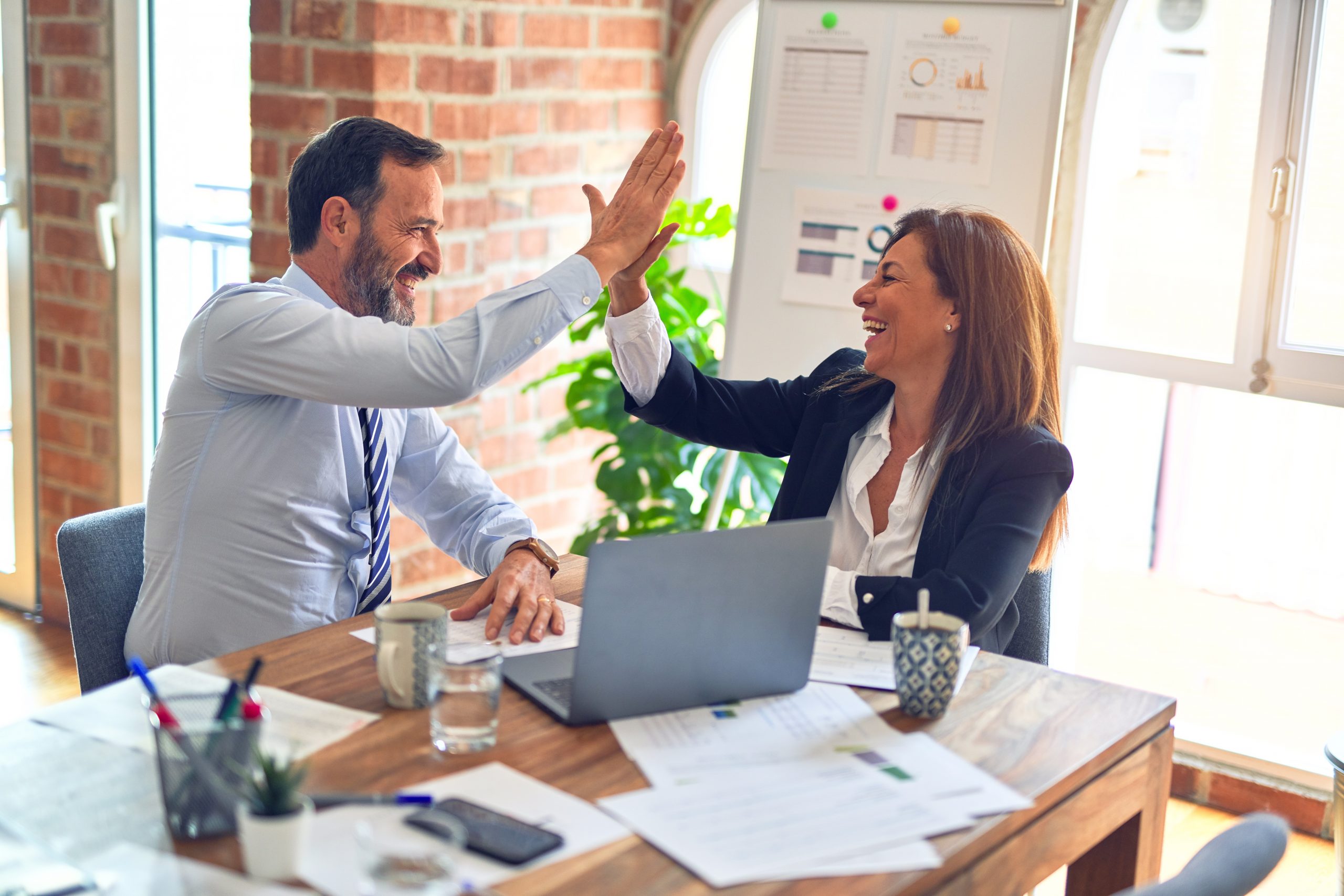
CBS News recently had a report about “How BMW Deals with an Aging Workforce.” To develop solutions to overcome loss of productivity due to the aging workforce, BMW tested one assembly line by staffing it with workers with an average age of 47, the projected age of the entire workforce in 2017. They made 70 small changes to reduce errors and physical strain, at a cost of about $50,000. The results were improved productivity and zero defects.
Sound familiar? It is the philosophy of Lean and Kaizen, engaged management listening to the workforce, small and rapid improvements that lead to visible results. What makes this interesting to me is that they set out to address a known and common root cause of a general problem – lower productivity of older workers. Therefore, the design of experiments and test of solutions were highly focused and efficient. It’s in clear contrast to many Lean or Kaizen efforts where improving productivity has no clear focus but fishing everywhere for waste.
There is another lesson. While we can certainly benefit from their approach and specific solutions, such as special shoes and magnifying glasses, more importantly, management in other organizations needs to have the courage and leadership exhibited by the BMW managers. Instead of focusing on the liabilities associated with older workers, they value their patience, skills and experience as assets, and develop specific solutions to ensure these assets are utilized to the fullest extent. That is the responsibility of the management, and that is the leadership an organization demands.