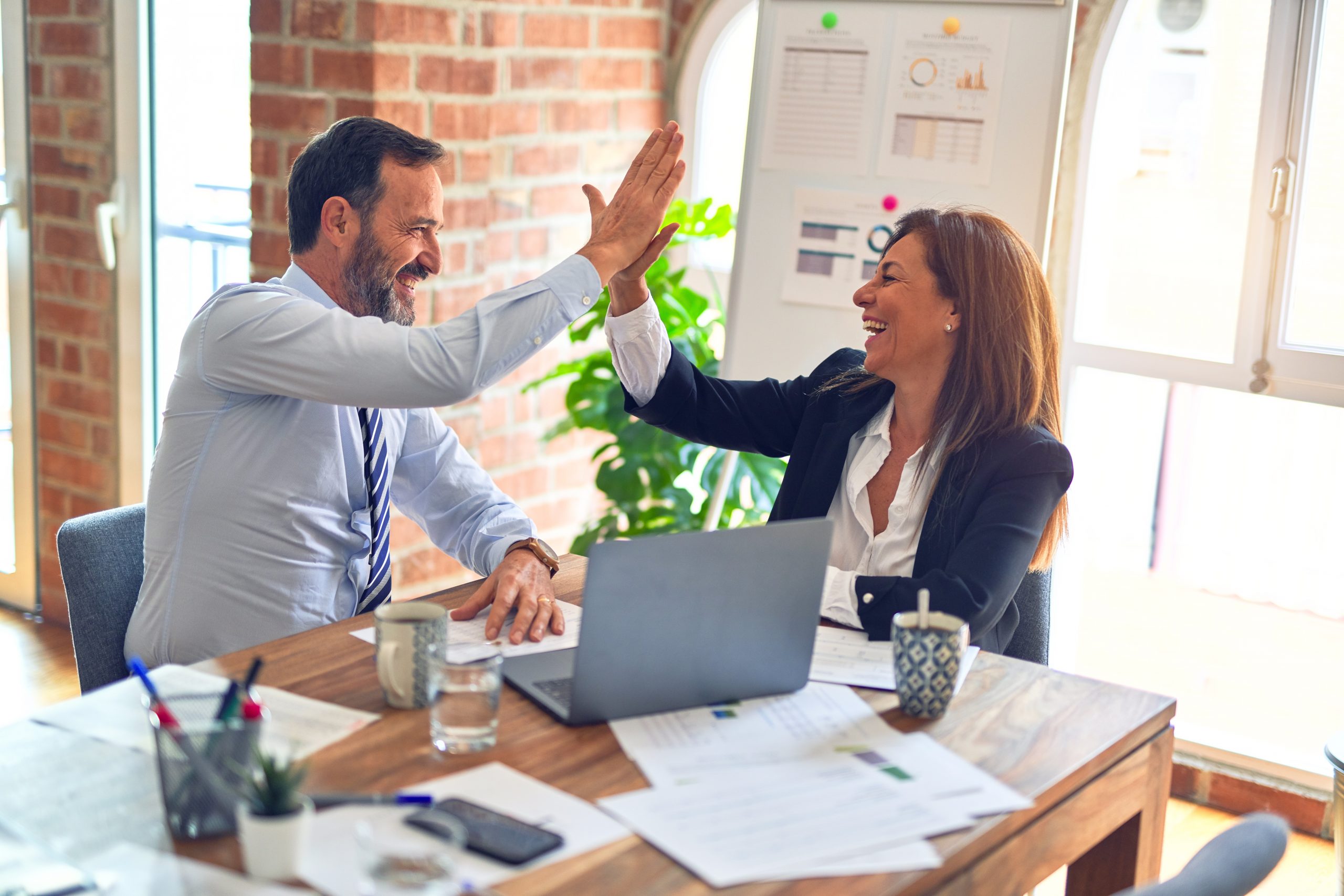
Benchmarking results consistently identify examples of Six Sigma success. Even so, getting “naysayers” on board is a continuous challenge. What do you tell them?
Nayism 23: I can’t put a production worker on a team.I need them out in the field working – not attending a meeting.
Production quotas and productivity are frequently used as an excuse to keep production workers from participating on a Six Sigma team. This excuse may be an indicator of a deeper problem. Additional discussions may help identify the true issue. How should you respond? Here’s what I say . . .
Having production workers participate on teams is necessary to get input and buy-in from the people who are closest to the process. Team participation should only take one to two hours per week. Although it may impact the production of the one person for a short period of time, the overall benefit will be that all production workers may become more productive as a result of the improvement. The one team member will probably have a very small productivity impact relative to the major gains that can be achieved.
If this doesn’t open the door, maybe the real problem is that the supervisor doesn’t believe that improvement is needed or does not want input from his or her production workers. In either case, it’s still not a good situation. The best thing to do is to keep talking to the supervisor and bring examples of how production workers may have contributed to a team in another department or an example of this from another company. Ask for a trial period for participation or ask for an ad hoc team member in lieu of a full time team member. Any small win is a step in the right direction.
In the meantime, strengthen local communications through newsletters, bulletin boards, website and posters – anything that lets you communicate directly with the production workers. Getting them to want to participate or even ask to participate may help your situation.
In all respects, stay focused on your mission and wait for an opportunity to present itself that will crack the door open wide enough to start things in motion. But beware. If the production workers have not been able to participate in improvement efforts for several years, you may find yourself swamped with great ideas!