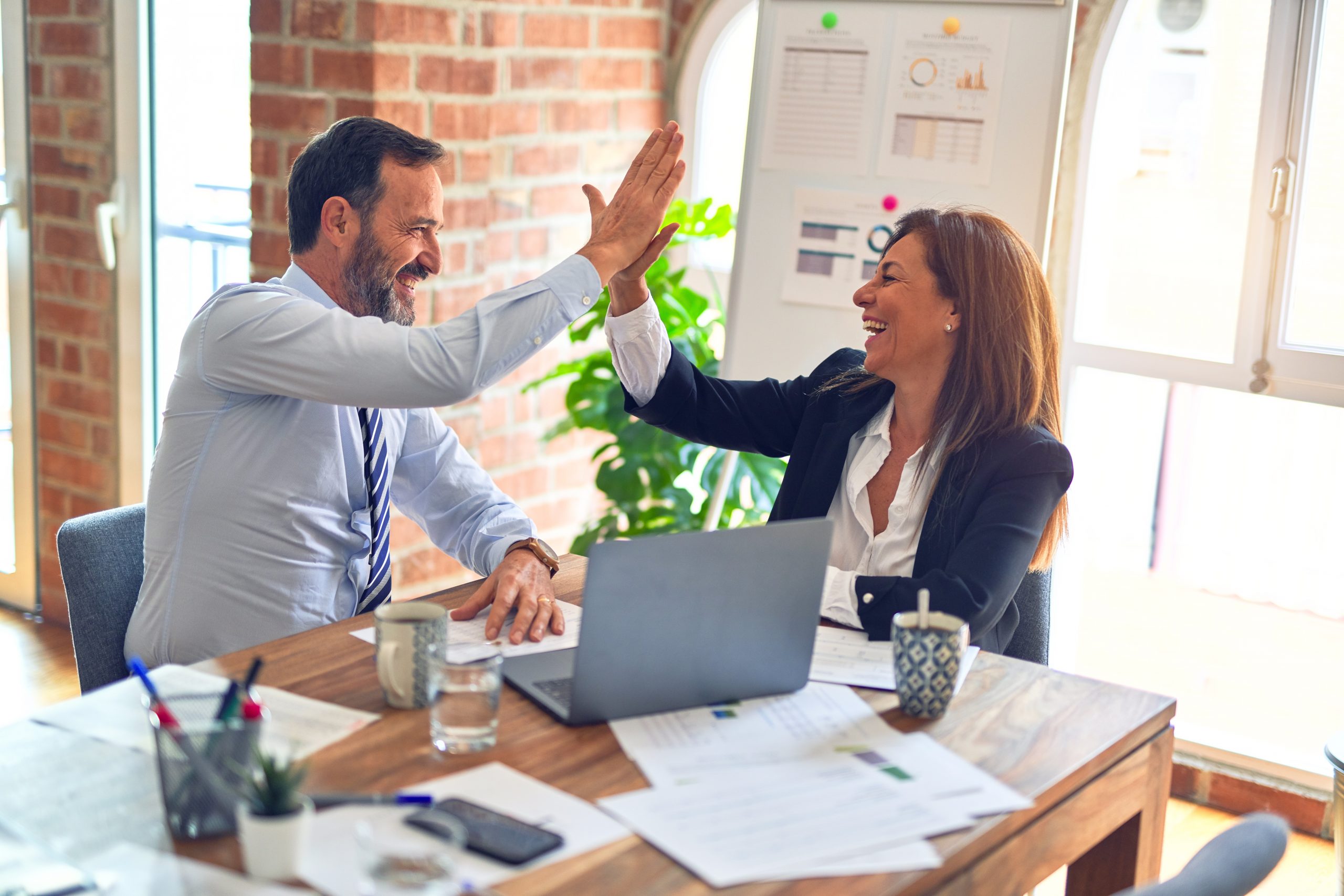
Implementing – Pay for Skills
I recently led an initiative to implement a pay for performance structure within my employer’s Production department. While management unanimously believed the idea was excellent, I was challenged as to whether or not this constituted a Six Sigma project.“I though Six Sigma was about reducing costs. This project looks like it will increase our labor costs so it can’t be related to Six Sigma,” was the response I received from one manager. “But wait- are the costs to cross train a department less than the costs to recruit, hire, and train a new employee to perform a specific task?” asked the Human Resources manager. The challenge had started.
Establishing a cross training or pay for skills program has a lot of soft and hard benefits- improved employee satisfaction, better job coverage, greater employee retention through a more rewarding career with more opportunity for advancement,reduced scrap and reduced down time to name a few. However, there are additional training costs that must be incurred. Do those costs and benefits outweigh new hire costs?How can this be sold as a Six Sigma project? Listed below is my approach thus far:
Define
In the define phase I stated some problems that production had over the prior year due to a lack of employees trained on certain machines and certain products. When unplanned absences or fully absorbed production capacity occurred the plant saw machine downtime, missed orders, and scrap product attributed to operator error. I was able to put a dollar amount to occurrences and make a compelling case that by implementing a pay for skills program these occurrences would decrease in the future and any additional labor costs would be negated by improved quality.
Measure
There was a lot of data involved with this project. I looked at employee attendance records for the prior year, scrap rates, equipment downtimes (and root causes), missed orders and production schedules attributed to capacity causes, and customer returns attributed to human product quality.
Analyze
I used several different tools. When looking at equipment downtimes, I did a Pareto by machine downtime as a % of overall run time and looked for the top machines that were down and then did a root cause Pareto for each machine. I used a regression analysis to determine what impact attendance had on missed production schedules and order shipments, given most employees were trained on very few tasks without backup coverage.
Improve
Based on product and machine usage data, I worked with Human Resources to establish two job classifications in the fabrication department and three classifications in the electronics/assembly departments. The classifications were based on difficulty of machines, complexity of product, administrative responsibilities such as order paperwork, and safety risk. The headcount in each classification was determined by estimated product or machine capacity with a normal distribution graph of capacity used.Formal work instructions were created for each piece of machinery and each mass produced item and training was conducted. Additionally employees were given copies of their new job descriptions and understand their responsibilities in their new cross functional work environments.
Control
Since the pay for skills initiative was only recently implemented I am currently in the control phase. Tune in to a future blog entry to see my progress.