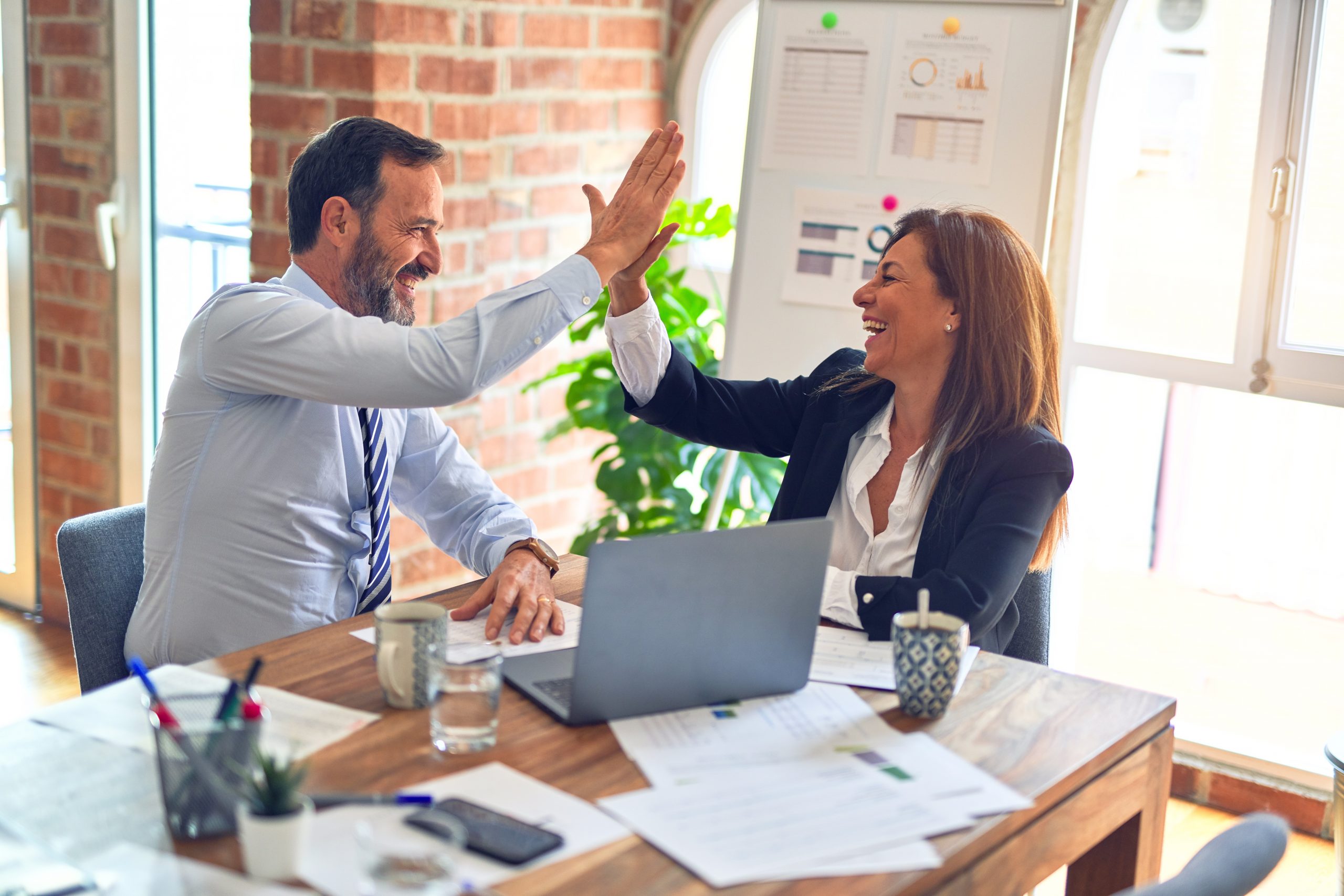
In my blog a few weeks ago I mentioned an article in McKinsey Quarterly about removing barriers to knowledge worker interactions. I pointed out a hidden barrier: lack of concentration or too much work-in-process (WIP), which slows down knowledge worker interactions.
In that article, physical barriers were cited as common, especially in many large global organizations like the one I work at. Technology certainly helps bring people closer, virtually. But physical barriers are not limited to distance. I sometimes have trouble booking a conference room for a project, where people are working at the same location. In many cases, I have to either use teleconference (using Net-meeting, which is not effective for many Lean Six Sigma types of activities), or delay the meeting until a room is available. I am sure many of you have experienced similar situations. We very often just accept this as the way life is too many meetings but not enough rooms.
Strangely enough, while this is happening, many businesses continue to consolidate facilities (to save money), with an unintended consequence of reducing available space for knowledge worker interactions.I don’t know how individual decisions are made, but mistakes in capacity planning often include the failure to take into account the demand variation and cost of either under- or over-capacity.On paper the available space or capacity is often larger than the average demand, and capacity utilization data support it.
If 50% of the rooms are unused 50% of the days, does it mean we have excess capacity? My answer is “it depends.” What I know now is how much and how often demand is less than supply (over-capacity). I have to know 3 additional pieces of information to answer the question.
How much/often demand is more than supply (under-capacity)
Total cost (or cost tolerance) of over-capacity
Total cost (or cost tolerance) of under-capacity
To make an educated decision, I would compare the cost and degree of over-capacity with the cost and degree of under-capacity. The tricky part of this analysis is that the cost is subjective because the calculation is not limited to financial or quantifiable costs. The final decision always has a subjective component. As a LSS professional, I highly value speed and face-to-face interactions with my team in a work room. So the total cost of under-capacity is very high for me. However, attempts to financially quantify the loss of productivity due to lack of effective interactions are futile because the calculation is soft and subjective, which is no comparison to the hard dollar calculation of over-capacity.
In addition, demand is often not known or measurable.It’s easy to know that the rooms are unused 50% of the time because we can log when the room is booked. It’s not easy to know how often additional rooms are needed but not available, because the failure to book a room is rarely recorded.
So naturally there is bias to justify fewer rooms than what is really needed. [Interestingly, the reverse is often true when it comes to inventory, because the cost of under-supply is (or at least is perceived as) significantly higher than that of over-supply. But I will save that topic for another day.]
A lesson here is that the challenges we (as LSS or CI professionals) face are huge. Lean and Six Sigma bring us a lot of concepts and tools, but they are not enough. Daily business decisions involve subjective input and incomplete information. Lean Six Sigma helps us understand the root causes of imperfect decisions, but it doesn’t necessarily provide a practical solution.