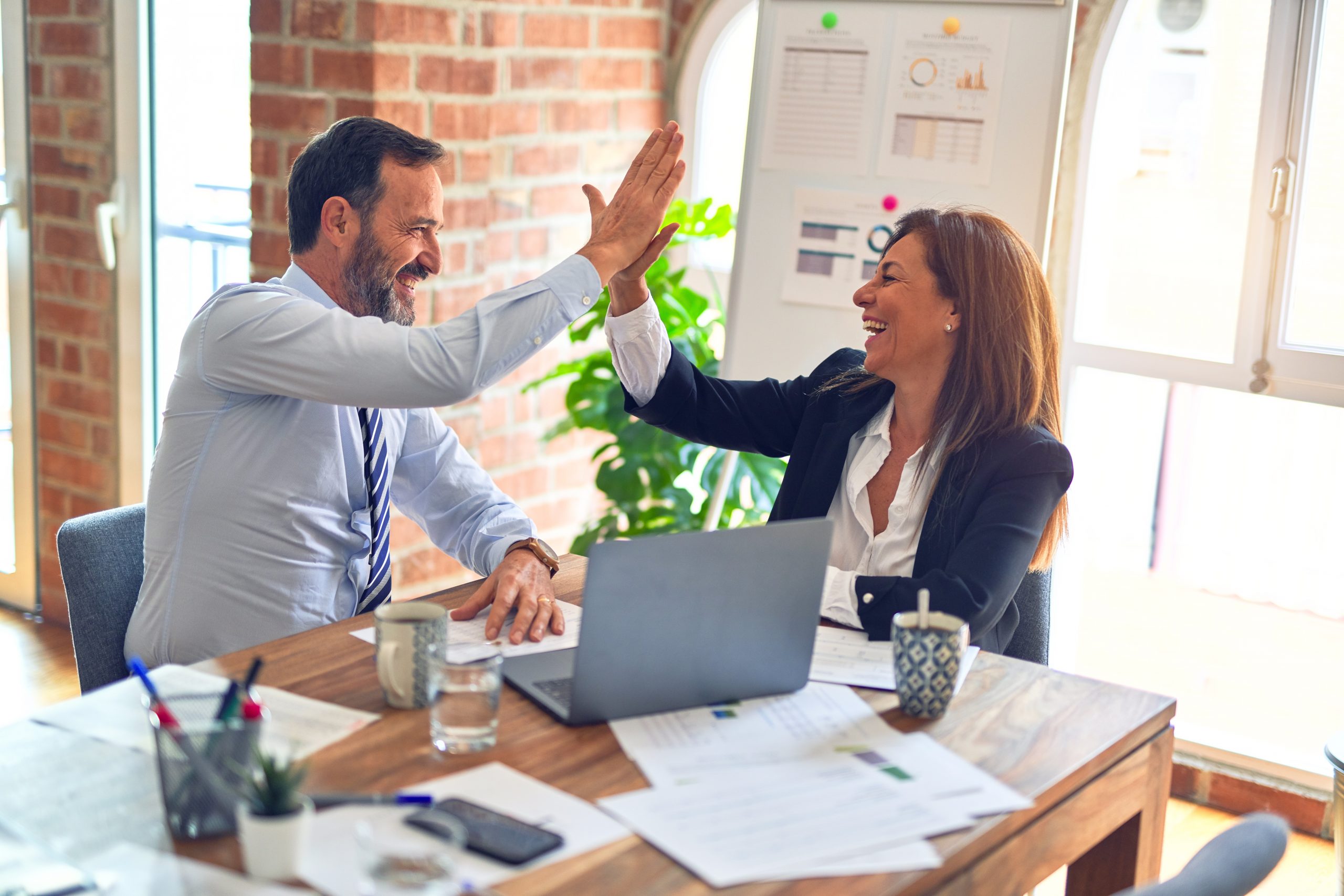
Many times in our industry, organizational leaders spout that they desire and believe in continuous improvement. They use the latest buzzwords and seem very serious when they communicate the new direction that they want to take. I don’t know if CI is truly understood by many organizational leaders due to the fact that most of where the tools and philosophies are implemented are only on the manufacturing floor. Sure, improvements are great when they increase production numbers and reduce or totally eliminate downtime; however, CI requires much more integration than that.
Sometimes, CI is even implemented as an optional program. Leads, supervisors and unit managers can choose to be engaged or not. They can choose to develop the employees or choose to continue the same old grind, only assisting in implementation by not fighting changes when they occur.
It is my belief as a CI engineer that this is where organizational leadership gets it wrong.
When an organizational leader commits to CI, it should not be implemented as an optional program. If it is not highly sought after, it will inevitably be viewed as a “flavor of the month” and it will turn bitter very fast. CI needs to be the corporate identity, philosophy and mind-set.
Ultimately, CI could be compared to a company moral. A moral is defined as a principle or rule of conduct that distinguishes between right and wrong. Most individuals would not break into a store and steal a television regardless of how much they want it or how easy it would be because they understand it is the wrong choice. A company needs to value CI to the same extent. A company needs to refuse to bend on the rules of CI and choose not implement waste, even if it is the easy way out. They should not allow waste to be implemented because they know it is wrong.
In order for CI to be fruitful, all of the organizational leaders must embrace its philosophies and tools, and develop teams according to its ideals. They need to refuse to bend and have that CI moral mind-set.
Everyone in the organization must be trained and measured to Lean/CI, from the shop-floor employee to the president. This is essential. It must permeate into all processes, practices, procedures and policies. This means that engineering, quality, safety, fabrication and logistics departments must all be required to develop ideas to eliminate waste, build culture and improve the value stream. It is only then that culture will truly take root.
However, the organizational leader also must deeply understand CI. The departments listed in the previous paragraph cannot just randomly implement ideas for the sake of measurement. The organizational leader needs to have a big picture and understand what he wants the company to look like in one, three, five and/or 10 years and then communicate that vision to the departments. That way, whatever ideas they develop and implement can all be working to paint that big picture.
CI is vital to organizational survival, but we must implement it the right way or we are not gaining any value with the philosophies and tools. We must build the culture around a program that is NOT optional and one that works toward a grand goal.
Let’s do it!
Please let me know what you think of this blog post (respond below or via email at [email protected]). We in the CI world are one community and can learn from one another’s ideas and opinions. We must work together to ensure the success of each of our companies.