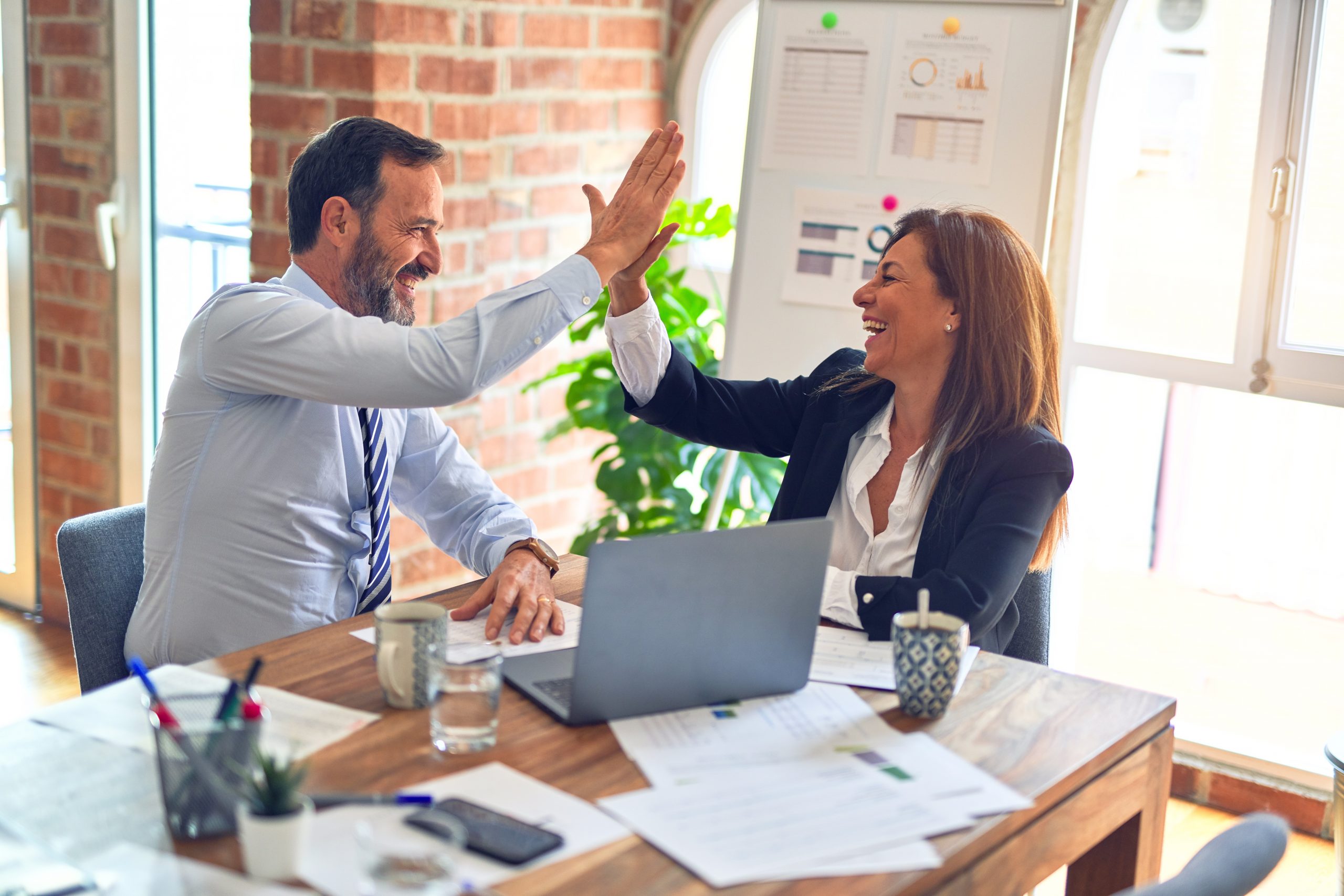
Leslie Behnke, Vice President Six Sigma Business Excellence, is leading the Six Sigma initiative at CIGNA. She joined CIGNA in 2002 from Motorola where she led Six Sigma activities for over a decade. The initiative is called “Six Sigma Business Excellence” and includes the standard DMAIC and DMADV methodologies. CIGNA annual reports do not mention the initiative but the 2004 CIGNA Dental brochure gives us some insight into what they have accomplished.
Savings and Benefits
“Six Sigma emphasizes producing better, faster and lower cost products and services than the competition and stresses breakthrough improvement for enhanced bottom line results. Nearly 100 of our employees have certified Six Sigma belt status, ranging from black belt to yellow belt, with significant training around process improvement. As a result, we’’ve seen:
“Four completed projects in 2003 achieved $3 million in annualized savings versus an original target of $2.4 million. 2004 projects are under way with projected savings of $995 thousand.
“Customer metrics with sustained improvements from baseline metrics in April 2003:
1. DHMO average hold time reduced (from 312 seconds to 281 seconds in May 2004)
2. DHMO average call waiting reduced (from 97 seconds to 63 seconds in May 2004)
3. Pended Claims aging volume reduced (pended volume reduced by 50%)
4. Front-end Claims Processing time reduced (from 13 work days to fewer than 10 work days)”
Leslie recently spoke at the ASQ annual conference in Seattle, Washington, USA:
“This opportunity to present to top quality experts and show how CIGNA implements a Six Sigma approach throughout our company was a tremendous endorsement of our commitment to quality,” Behnke states. “The selection process for this conference was rigorous, so only companies that are truly moving forward with meaningful quality initiatives were chosen to participate. I am honored to represent CIGNA and demonstrate our process for continual quality improvement.
“Behnke’s presentation focuses on how Six Sigma can strengthen health care industry processes, leading to reduced medical costs and improved health outcomes. CIGNA has a company-wide Six Sigma program designed to identify areas for potential improvement. The organization then develops and implements improvements to better and more efficiently serve its customers and members. CIGNA offers its Six Sigma training in conjunction with Smarter Solutions, a recognized leader in quality and quality improvement program development. The program is integrated across all business units and product lines, allowing for a more comprehensive implementation of the company’s Six Sigma methodology.”
CIGNA Newsroom, May 16, 2005
Articles and Links
CIGNA’s Six Sigma Expert Talks Business Improvement, UConn School of Business, October 19, 2004