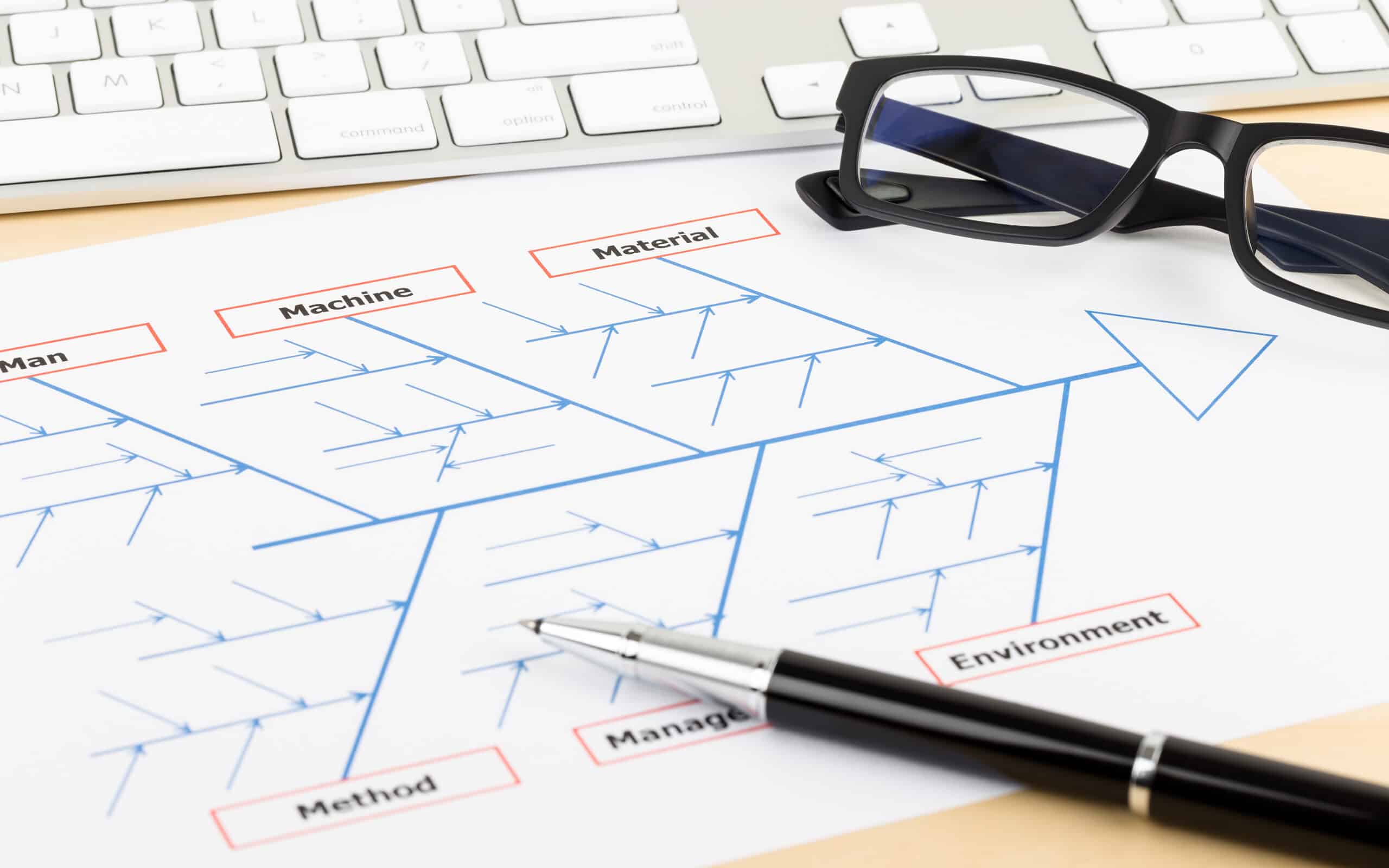
Key Points
- A lack of detail can hinder any Ishikawa diagram.
- Make sure to consult with your team throughout the creation of your Fishbone diagram.
- You should make use of the other QC tools alongside your Ishikawa diagram.
What mistakes are common when using Ishikawa diagrams? As one of the easiest tools to use in the Lean Six Sigma toolbox, there is a very real potential for misusing these diagrams. It isn’t necessarily a lack of knowledge that hinders these tools, but other common pitfalls that make them less effective than is needed.
So, with that in mind, we’re looking at common mistakes and how to rectify them. This is by no means an exhaustive guide. There is no shortage of potential misuse of these diagrams. Instead, it’s the most common mistakes and frequent complaints that center around this common tool.
What Is a Fishbone Diagram?

©Ground Picture/Shutterstock.com
A Fishbone or Ishikawa diagram, is a visualization method that helps to determine the root cause of an issue. Typically, you’ll employ an Ishikawa diagram when an issue has arisen somewhere in your production line. These are effective diagrams because they show the effects and causes of a given problem.
When used in conjunction with other tools and techniques, this is where an Ishikawa diagram truly gets to shine. However, you’ll have to temper your expectations if you think this tool is going to be your only means of recourse for determining the root cause of something.
Developing Effective Ishikawa Diagrams
There is quite a bit of consideration that goes into developing a solid Ishikawa diagram. While these are simple tools at first glance, it pays to know the processes that make up your production line. As with any tool, there is a real potential for misuse simply due to a lack of experience. You don’t enter a job site knowing the most effective way of swinging a hammer after all.
Effective Ishikawa diagrams are a team effort. In an ideal scenario, you are pulling from the wealth of talent of your team to craft a document that helps to hone in on a problem. Additionally, the Ishikawa diagram should be actionable, meaning you have the means to test and prove your hypothesis before setting things in motion.
Biggest Mistakes When Using Ishikawa Diagrams
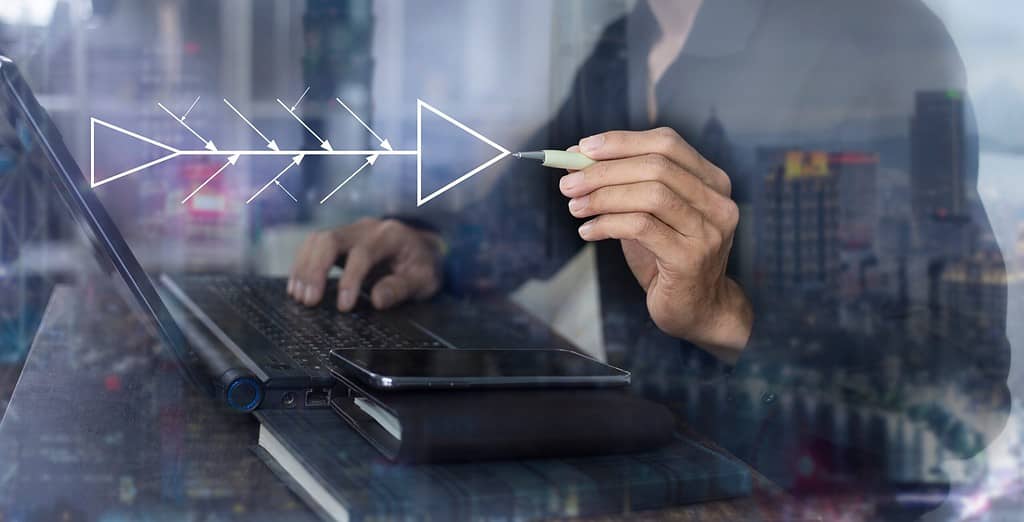
We’ve covered quite a bit when it comes to how to use and employ Ishikawa diagrams to their fullest potential. However, speaking from personal experience, there is plenty that can go wrong with an Ishikawa diagram. Sometimes, this is a matter of inexperience, team members being tasked with creating something they’ve barely done.
More often than not, this is a matter of scope creep. It is one of those dreaded topics that arise time and time again when considering things in the tech industry. But, rather than regale you with tales from the trenches of enterprise technology, let’s dive right in and discuss some major issues you might experience.
Lack of Detail
Imagine for a moment that your team has created a rough draft for an Ishikawa diagram. You walked in with a decent enough problem statement, and the results have finally arrived. However, when looking over the particulars of this Fishbone diagram, you notice things are quite vague. The causes are defined well enough, but the effects lack detail.
If you were to take this information and start testing criteria, you might run into issues. The same goes for a lack of detail in the causes. If a team member is presenting a diagram where the causes are single words that could pertain to anything in the production, that’s a problem.
Shakespeare once quipped, “Brevity is the soul of wit,” but that isn’t remotely applicable to tools utilized in an enterprise environment. You want enough detail to work with, not leave you scratching your head and wondering what to do.
Too Much Detail
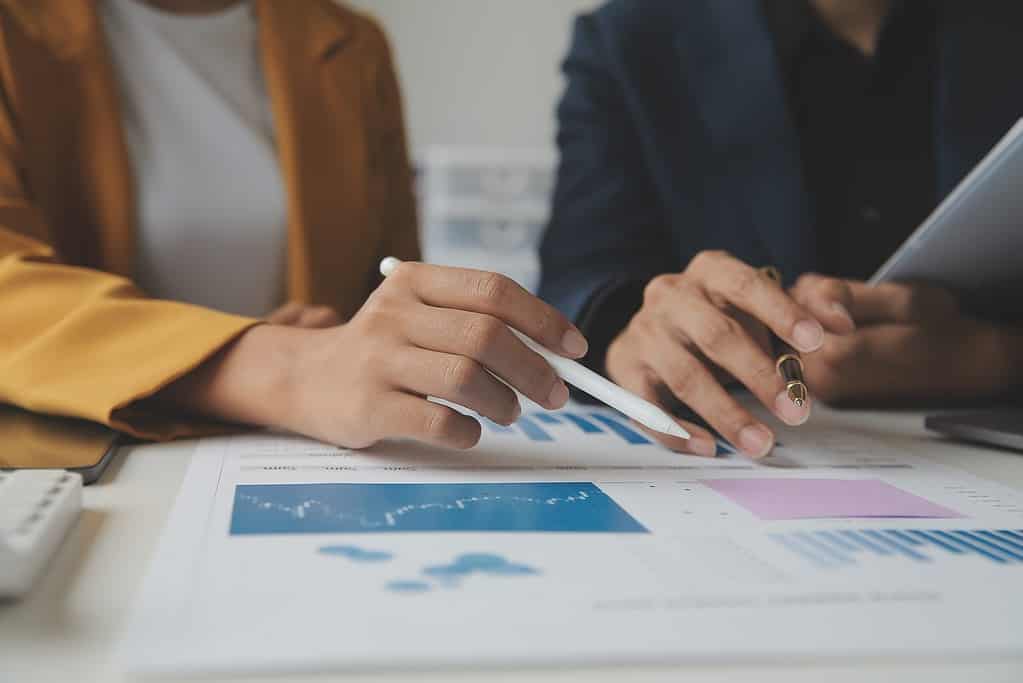
The inverse of a lack of detail is also a major issue when constructing an Ishikawa diagram. If you’ve got a wealth of detail in both causes and effects, that’s a major problem. Think about it, if you’re looking at a graph, diagram, or whatever other visual aid, you don’t want to read an entire essay in the margins.
There should be enough detail to answer a question at first glance, but the minute it starts breaking into multiple sentences, something has gone awry. As such, it helps to pare down details until you’ve got the necessary elements to make your Ishikawa diagram readable and complete.
It takes time to hone this technique, and there’s no shame in admitting you need a bit of help when going about things. Detailed information is great, but don’t lose the forest for the trees.
Unclear Causes and Effects
This ties in somewhat to a lack of detail, but it does have an important consideration to keep in mind. If you’ve got unclear causes and effects prevalent throughout your Ishikawa diagram, it can be difficult to ascertain what you’re working toward. This is one area where honing in on what needs to be addressed with your team is crucial.
However, you’ll want to nip this in the bud quickly, simply due to the potential of going to validate your information and coming up short.
Not Validating Results
Do you build a house with just a hammer and nails? There are a lot of ways that an Ishikawa diagram can fail, but not taking the time to verify your results is going to hinder you. A properly constructed Ishikawa diagram isn’t intended to be a roadmap for what comes next, but rather a piece of information for you to test things.
Taking the time to validate and verify your problem statement is crucial for any root-cause analysis, don’t neglect it.
How to Rectify the Biggest Mistakes When Using Ishikawa Diagrams
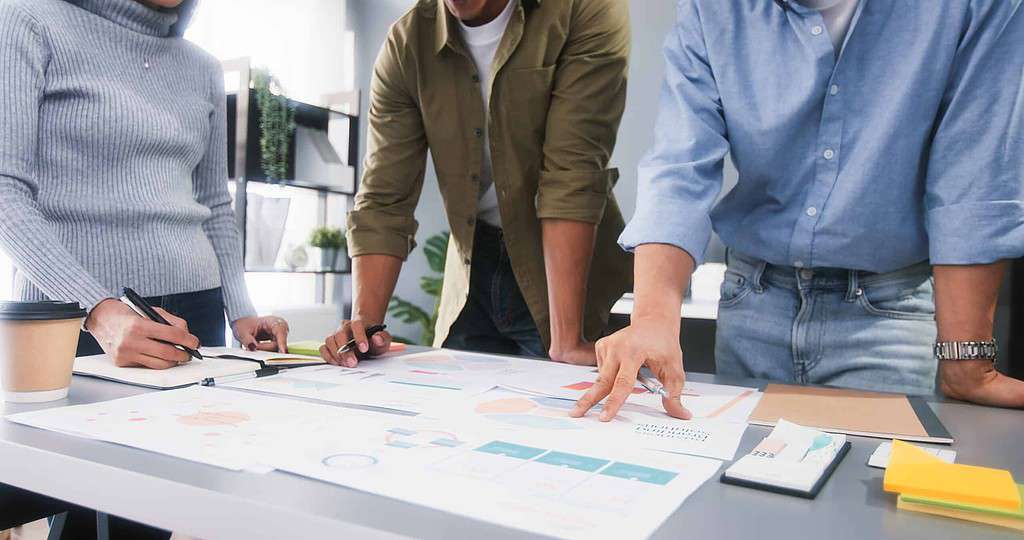
Thankfully, you aren’t adrift at sea without a sail when it comes to fixing these problems. In all honesty, it comes down to focusing your efforts in the right direction to make the biggest impact on your Ishikawa diagrams.
Craft a Problem Statement
This might seem self-explanatory, but it’s something that comes up time and time again. Many would-be diagram creators go out and try to get the Ishikawa diagram created with the information they have on hand. However, that’s putting the cart before the horse.
Before you sit down and fire up your graphic design software of choice to create an Ishikawa diagram, create a problem statement. You don’t have to do this one on your own I encourage you to invite others to assist you in creating your problem statement.
Problem-solving in a Lean Six Sigma framework is rarely a solo endeavor, as team members across all departments have different levels of expertise, strengths, and so forth. Call on that resource, craft a solid problem statement, and you’re well on the way to creating an effective Ishikawa diagram.
Collaborate
We’re back in a team mentality, so call on them to help develop solid categories. Causes can be nebulous at first glance, but if you’re calling on the floor manager of the production line, they know exactly what is going wrong.
This should be your first order of business when it comes time to draft out the particulars of your Ishikawa diagram. You’ve got a solid problem statement, now you need proper causes to determine the effects. This could be time-consuming, but you’re looking to solve a problem, not do the bare minimum to get things back and running.
Taking the time to hammer out the particular effects of those causes is also paramount. You don’t want to grab things in the dark. Actionable information is key to success in any endeavor throughout the Lean Six Sigma methodology. Apply that same need for data to your Ishikawa diagrams and you’re cooking with gas.
Workshop Your Diagram With Team Members
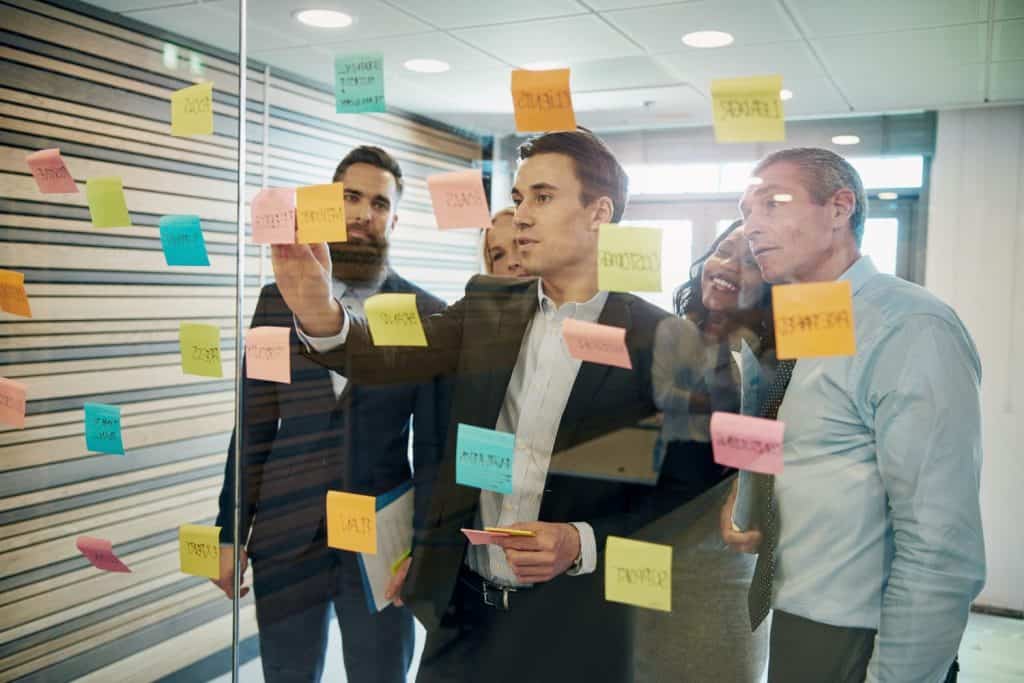
©Ground Picture/Shutterstock.com
Now that you’ve created what you think is an effective Ishikawa diagram, what’s next? Well, you could present it to the higher-ups and go from there. However, you’re doing yourself a disservice if that’s the next course of action.
Take some time and analyze the diagram with your team. Does it address the problem statement you created? If that isn’t the case, you’ll want to go back to the drawing board and tweak things as necessary. From my time in tech, you don’t ship the solution without testing it first.
The same applies to any diagram you’re looking to present. Make sure it’s airtight and there is minimal room for improvement before presenting it to your superiors. Taking the time to hammer it out now is going to save valuable time that would be spent on rework.
Use Additional QC Tools
I think one thing that doesn’t get stated enough is to use the other tools at your disposal. The 7 QC tools aren’t meant to be monolithic. They are complementary for solving problems and assuring quality throughout. You could do well to utilize something like a Pareto chart to help solve issues throughout your production workload.
The information gathered from tabulating your data points for a Pareto chart could directly impact your creation of a suitable Ishikawa diagram. Additionally, learning how to best utilize these tools is going to pay dividends when it comes time to solve problems and determine the root causes of issues.
Someone fixing a car isn’t solely relying on a socket wrench, and the same also applies to your needs. Don’t overly rely on a single tool like the Ishikawa diagram, that’s only part of the equation. Use everything at your disposal and you’ll see the quality match your organization’s intent as far as your customers are concerned.
Other Useful Tools and Concepts
Now that we’ve covered the mistakes to avoid and how to fix them, it’s time to look at some other materials. Since you know what to avoid with making an Ishikawa diagram, why not look at the tools used in businesses around the world to create your own? You don’t have to lean solely on Microsoft Excel to create a visually pleasing diagram.
Additionally, using the Pareto chart is a key part of determining root causes with anything. This powerful and effective tool is simple to use. Don’t take my word for it though, you can learn how to make one on your own and where they’re best utilized in our guide on the subject.
Conclusion
Creating an effective Ishikawa diagram isn’t necessarily rocket science, but it does require the right sort of legwork to be effectively used. With any luck, you’ve come away today with a greater understanding of the mistakes made throughout and how to avoid them. Remember, it’s a team endeavor, you don’t have to fly alone when creating anything.