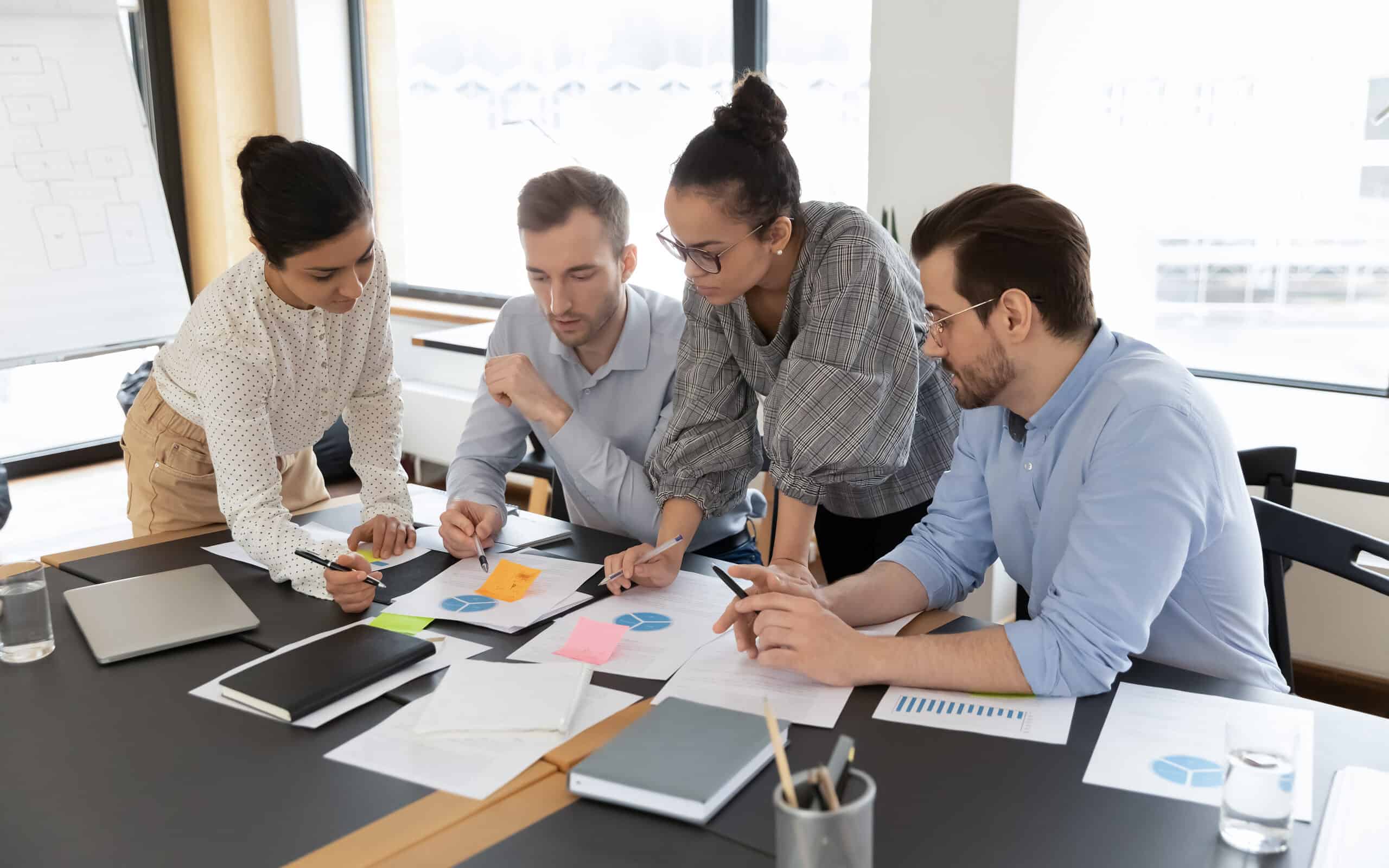
Key Points
- FMEA is a flexible methodology for addressing potential failure points and implementing lasting changes.
- Common mistakes are a normal occurrence in FMEA but are easily addressed.
- Proper implementation of this methodology should see minimal problems, with established documentation being present.
What are the most common mistakes you can make with FMEA? As a framework, FMEA is aimed at creating lasting solutions to potential problems before they even arise. However, that doesn’t mean it’s completely foolproof. As we’ve seen with many of the tools of the trade, there is certainly a right and a wrong way to use it.
So, with this in mind, I’ve taken the liberty of scouring the web for common complaints about FMEA and its implementation. We’ll go over these common mistakes and how to rectify these pitfalls to have lasting changes in your production. More often than not, it’s simply a matter of adjusting your parameters and doing the leg work to ensure you’re making the right choices.
What Is FMEA?

FMEA, or Failure Mode and Effects Analysis, is a comprehensive framework that can be implemented during, before, or after a process’s implementation. It provides the means for users to analyze their process heavily and determine the most glaring pain points. By using FMEA, you’re setting yourself up to have lasting solutions in the long run for your processes and your production line.
When used in conjunction with something like DFSS, you’re setting up the means to have quite a powerful workflow. However, the thing to keep in mind is that you need to do a fair bit of legwork to determine the failure modes present in any process.
How It’s Used
As previously mentioned, FMEA is usable as a few different variants. Design FMEA, for example, considers potential failure modes and implements solutions while designing the process or product. Further, you can see its use in things like root-cause analysis and problem-solving for processes, similar to DMAIC.
Additionally, you can consider other FMEA variants for the likes of services, software development, or operational procedures. It depends on the needs of your organization as opposed to relying on singular means to find failure modes and determine their effects.
Properly developed FMEA protocol will feature extensive documentation, in part to provide some historical data on the steps taken to remediate issues. This documentation also serves to provide a framework for iterative steps in the FMEA process, allowing users to continue its use when other issues might be grinding things to a halt.
Common Pitfalls in FMEA
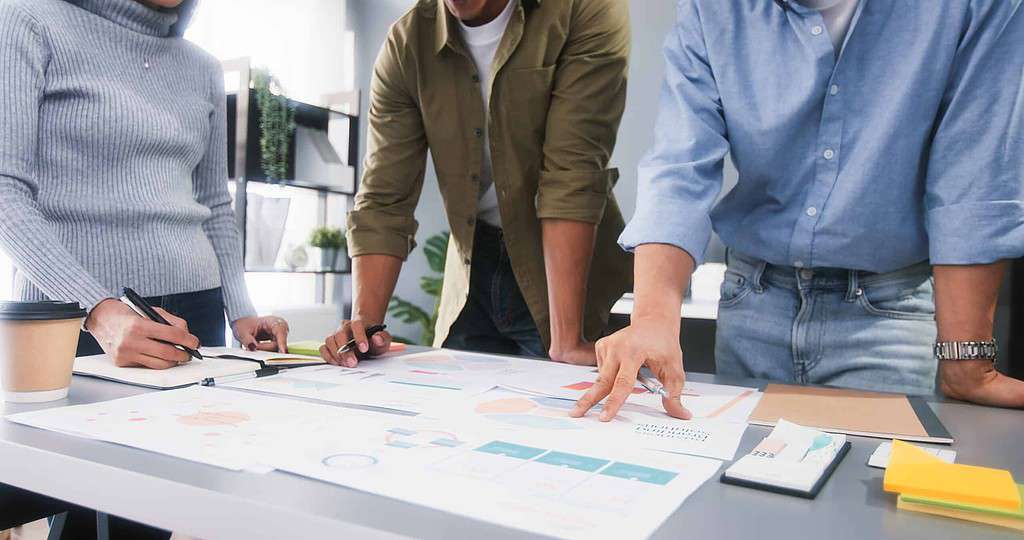
We’ve defined and highlighted some of the uses of FMEA. However, now it’s time to take a closer look at the common pitfalls associated with this methodology. The common mistakes with FMEA are similar in breadth to the issues we see arise in many of the tools and methodologies found in Lean Six Sigma. However, the ways you choose to remediate these issues are going to differ on a case-by-case basis.
Scope Creep
One of the most common pitfalls in FMEA that you’ll find is when things just happen to get a little out of control. Give a team a project, and you’ll likely experience some scope creep in one regard or another. This is completely normal, especially when you think about how complex or involved individual components in a process are.
However, scope creep can lead to the creation of FMEA frameworks that are trying to do too much at the same time. To fall back on an old and tired phrase, don’t lose the forest for the trees. Effectively developed FMEA plans aren’t leaning solely on doing everything at once.
When you’re developing new processes, you aren’t looking to do everything at once. As such, you’ll want to apply a similar approach.
Improper Rankings
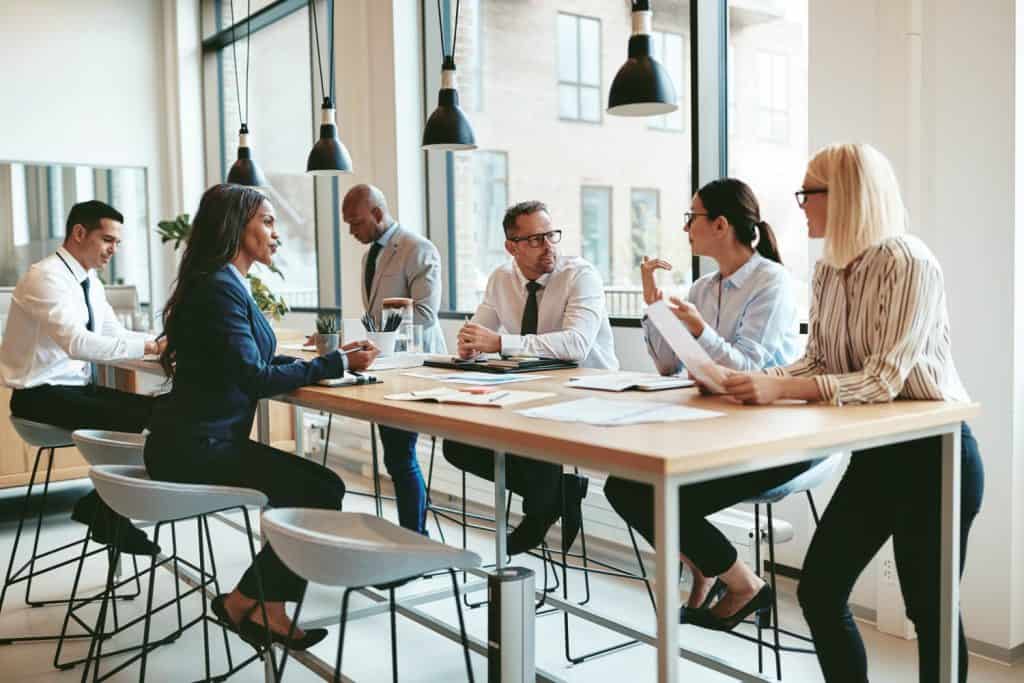
©Ground Picture/Shutterstock.com
One of the key factors in any good FMEA plan is the calculation of RPN. RPN, or risk priority number, is one of the driving factors in deciding where to go next with your evaluation of potential risks. In essence, it determines the severity of each risk, its likelihood of occurring, and how quickly you can detect it.
However, if you aren’t doing your due diligence, you’re setting yourself up for failure. Improper rankings can lead to providing solutions for less pressing failure modes. This leaves you wide open for grinding production to a halt.
As a LSS practitioner, you’re likely used to dealing with the numbers. Leaning on the wrong data can mean the difference between implementing lasting solutions and having to go back to the drawing board. Rework in this instance is going to be a costly endeavor, especially if production has ground to a halt.
Ignoring Procedure
One of the most common pitfalls in FMEA is simply ignoring the groundwork set. When you’re doing any sort of work, procedures are generally developed and put in place to allow for historical proof and to act as a road map of sorts for future action. However, if you simply ignore the pieces put in place and try to go about it alone, you’re going to end up spinning your tires.
Procedures are developed in complex methodologies like this for a good reason. You don’t set out to build a house without a floor plan, so why would you do the same for a vital business process?
Neglecting Your Team and Resources
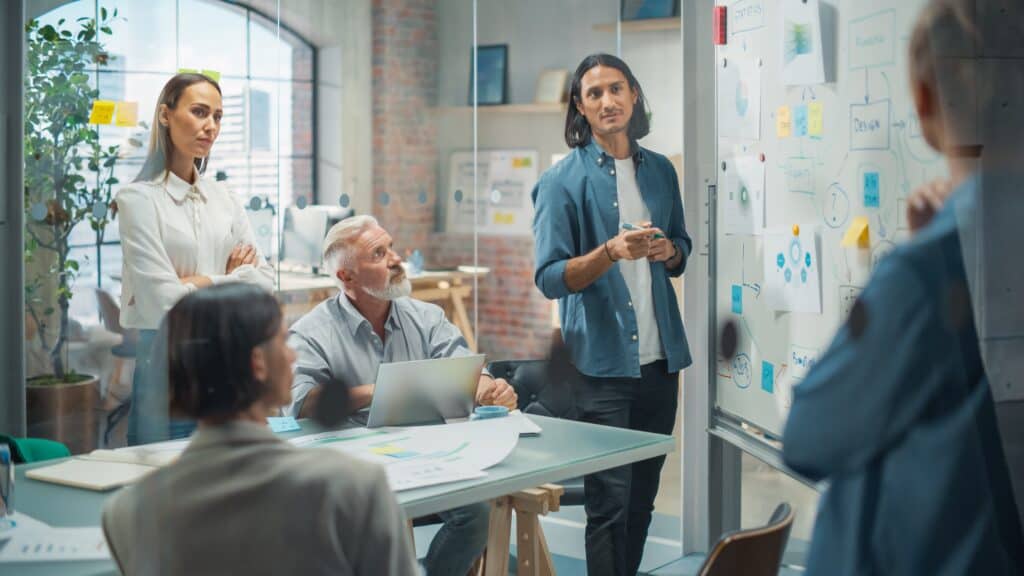
First and foremost, an FMEA plan is a team effort. You’re leaning on the experience and knowledge of your team to help fill in the blind spots where things might go awry. You might be in a solid leadership position and receive top results, but that doesn’t mean much if you aren’t listening to the people monitoring the processes in the first place.
Your team is there for a good reason. If you can’t fall back on their knowledge, then what hope does your process have of seeing continual success?
A Lack of Understanding
One of the most important common pitfalls in FMEA is not understanding the details behind your FMEA plan. At the end of the day, a plan isn’t worth much if you lack insight into what is happening. This is something I’ve harped on about in the past with things like SIPOC and Ishikawa diagrams. If your plan is laden with jargon or nomenclature that you can’t understand, it’s a failed endeavor.
Fixing the Common Pitfalls of FMEA
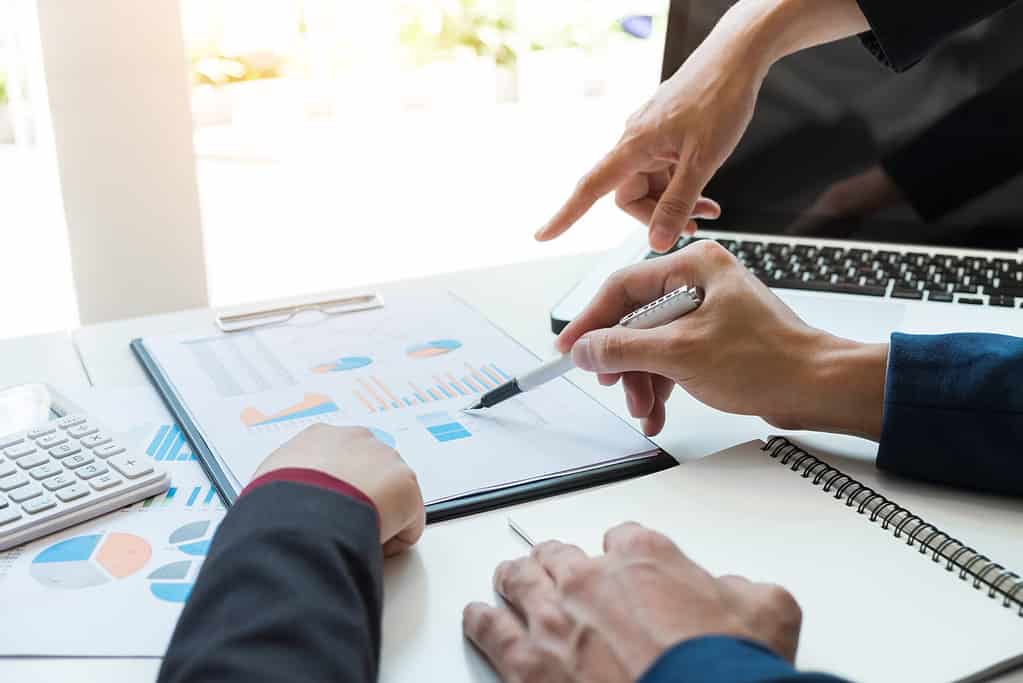
So, we’ve highlighted a few of the more glaring issues, but how do you rectify them? Common pitfalls in FMEA are thankfully relatively easy to remediate. It mostly comes down to common sense as to how you approach them. So, let’s dive into some easy solutions that will see lasting success as you move through developing your plans.
Keep It Focused
When thinking about scope creep, you’ll want to keep it simple. Hone in on just a handful of issues on a single component of your processes if necessary. Limiting the scope of your FMEA plan is a great way to implement lasting solutions that will see continued success as you move forward.
Scope creep is the death knell of many things in businesses, but that is what leadership is for. You want to pull back from those pushing to include a little bit of everything. For example, if you’re looking into quality control missing a vital step in the calibration of a piece of your end product, then why would you start also considering things like the raw materials?
FMEA is flexible in many regards, which is part of what makes it so effective. So hone in on the things that matter in the now, rather than trying to cram everything in the same box.
Run the Numbers
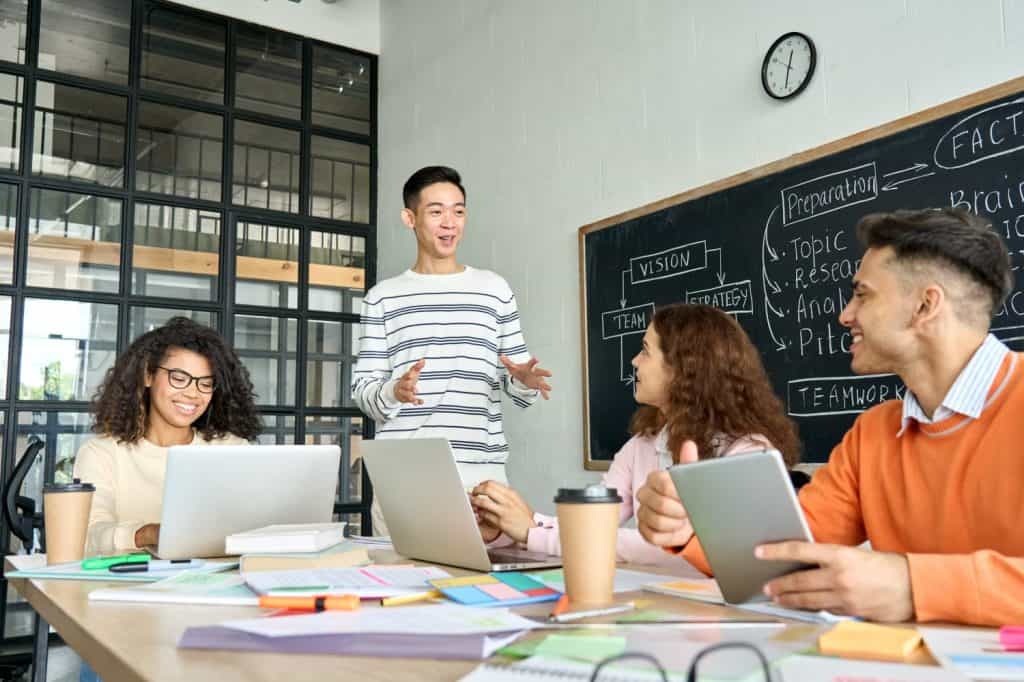
©Ground Picture/Shutterstock.com
How would you treat something that has faulty data? You would go back and try to gather solid empirical evidence, at least I hope you would. If you have the wrong sort of rankings for your RPN per item, then you’ll want to go back and start getting numbers that reflect the reality of the situation.
Sure, this can eat up time and resources, but you’re looking to make a lasting impact. When you’re trying to avoid one of the most common pitfalls in FMEA, it is worth taking that extra bit of time to make sure issues are rectified reliably.
Follow the Plan
If you have proper procedures in place already, why not stick to them? That isn’t to say these plans are immutable, but if you have a group that has already established the working rules for how to implement FMEA in your organization, it’s certainly worth a shot. Established plans have been vetted and have seen continued success in the workplace.
If you’re at an organization that has been using FMEA for years, there is likely a rock-solid framework in place already. As such, don’t try to alter the plan, just stick to what works. These plans likely already have the proper instructions for defining the scope and the best practices needed for getting things rolling.
Collaborate
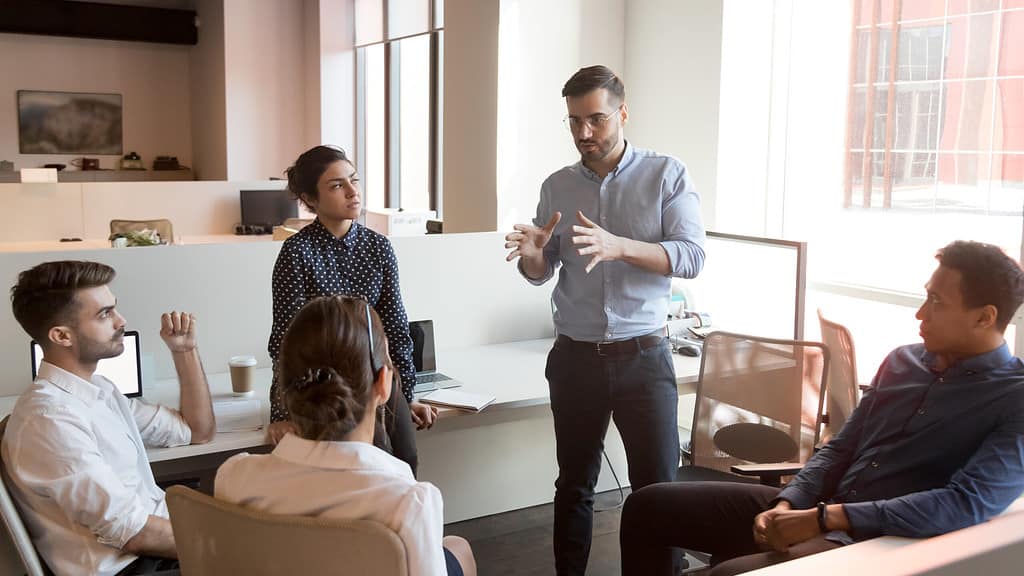
Most things in business are a team effort. Sure, there might be a few star players, given the size of your team, but these people are resources. You can call on their expertise, ask questions, and get into the nitty gritty of how everything works. For example, you might be the production manager of an assembly line, but you won’t know what works without a guiding hand like a foreman.
As such, listen to your team and learn to lean on them when the time calls for it. You’ll see that one of the biggest pitfalls in FMEA falls by the wayside when you start incorporating your team into the fold.
Learn How It Works
If you’re new to FMEA, then this is the best way to gain a further understanding of how this flexible methodology works. Taking the time to learn the best practices from the top minds in the field is only going to benefit your organization. Yes, this isn’t implementing lasting solutions, but it is giving you the means to develop your own.
If you look at an FMEA plan and you feel your eyes spinning, then it might be time to bolster that knowledge base. There is no shame in being a student, as that is the primary means by which we learn to adapt and succeed when presented with the unknown.
Other Useful Tools and Concepts
Hopefully, you’ve still got a thirst for learning, so why not check out some other topics? While we’ve covered FMEA’s common mistakes in-depth, seeing how it works in motion is a vital thing. Thankfully, our article on the subject gives an accurate look at the concept in motion.
Additionally, you might want to take a closer look at the likes of the Ishikawa diagram. This is a simple QC tool, but there are some common mistakes you can make when trying to get things going on your root-cause analysis.
Conclusion
With any luck, you’ve come away from today’s topic with a keener insight into how to avoid the common pitfalls in FMEA. This is a flexible and useful means of implementing lasting changes in your production. Plenty of organizations are using this methodology to deliver quality, learning to avoid these common mistakes could have you right among their ranks.