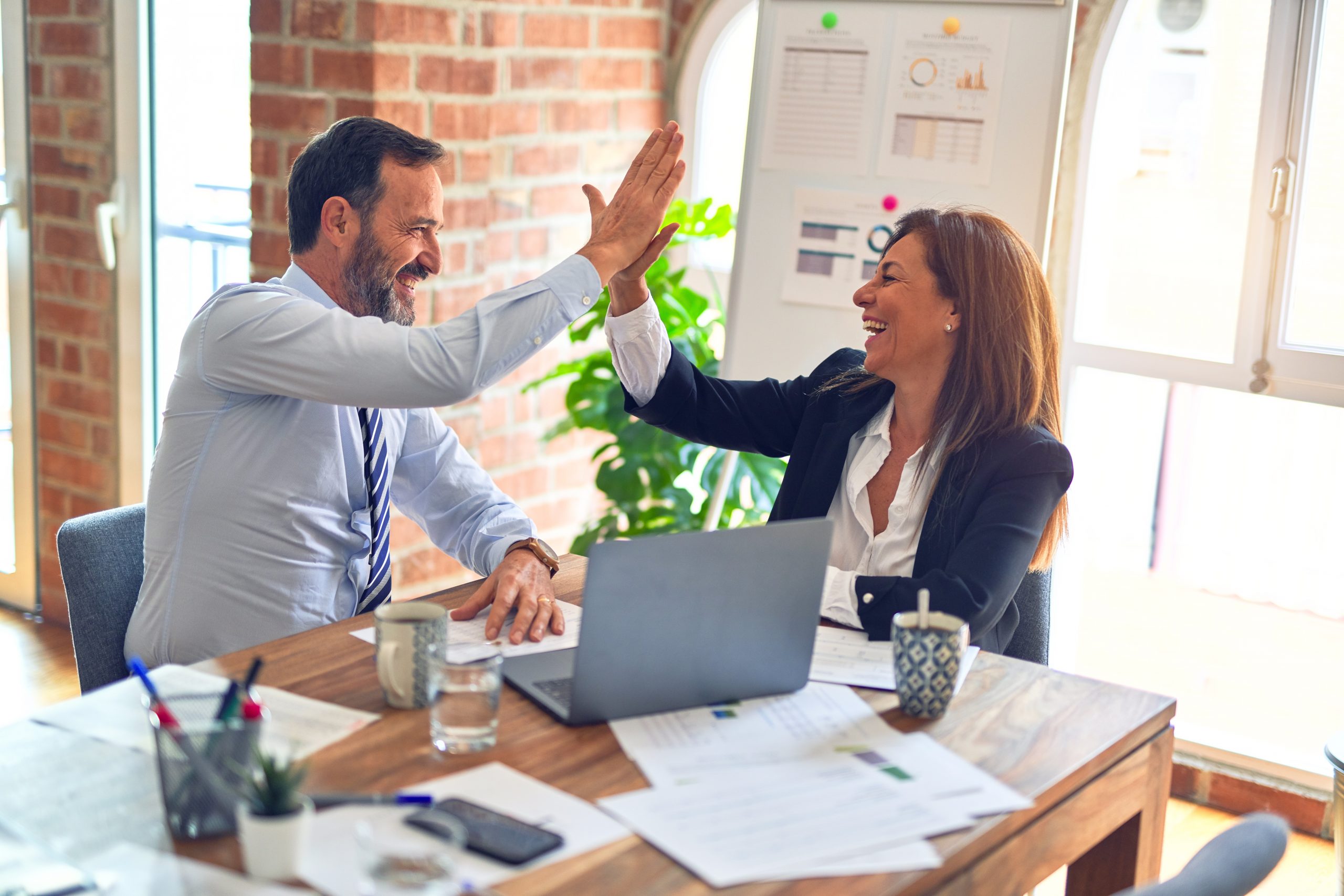
As you likely know, equipment uptime (as well as downtime) is very much akin to product reliability engineering. Many of the same concepts, equations, and methods are commonly shared. Given this, it should be interesting to note that Six Sigma found its genetic roots in the field of reliability engineering. As some of the more advanced practitioners of Six Sigma already know, the idea of “Mean-Time-To-Failure (MTTF)” and that of “Mean-Time-Between-Failure (MTBF)” are both highly interconnected to the fundamentals of Six Sigma.
About 1984, Mr. Bill Smith (founder of Six Sigma at Motorola) had distributed an internal white paper that conceptually interrelated the occurrence of product defects to MTTF and MTBF (as well as other things). On the heels of this paper, and by the introduction of Murry Allen (Motorola GEG), I was connected with Bill so as to investigate and extend this line of research. In essence, Bill’s proposition was quite simple – increase critical product design performance margins from the classic level of 25 percent to an expectedly more difficult level of 50 percent. By doing so, it was believed that a more optimal level of design robustness could be realized. In different words, the increased margin would make a product design relatively impervious to process centering error (on the order of about 1.5s).
By achieving such an increase in design margins, it would be anticipated that the “instantaneous failure rate” of the product would naturally improve, thereby enhancing MTTF and MTBF. From the process engineering point-of-view, the increase in design margins (to 50 percent) necessarily inferred the global need for a 6 sigma level of short-term capability. With such a stupendous level of capability, “in-process testing” could be significantly reduced. In addition, there would be huge benefits associated with the reduction of “burn in” time. Furthermore, the resulting decrease in defects-per-unit (by way of increased design margins) would virtually eliminate the need for in-line test and inspection, thereby reducing production costs, not to mention the implications on reducing warranty costs, work in process and process cycle-time. From all of this, huge economic benefits could be obtained, as well as significant enhancements to customer satisfaction.
For those working in the area of product reliability engineering, the roadmap to quantum change was clear. The idea was to start with a desired MTTF or MTBF and then “reverse engineer” or otherwise “back compute” one’s way to the long-term (longitudinal) capability and short-term (instantaneous) capability, per defect opportunity. A great deal of this approach was developed and pioneered by myself and Dr. Ron Lawson while assigned to the Advanced Quantitative Research Laboratory, Government Electronics Group, Motorola Inc. Some of this work can be referenced as follows:
Harry, M. J. and Lawson, R. (1990) “Six Sigma Producibility Analysis and Process Characterization.” Motorola University Press.
Harry, M. J. Contributing Author. MK 45 Mod 9/10 Military-to-Industrial White Paper. Prepared for Naval Sea Systems Command, Washington D.C. Tactical Electronics Division, Government Electronics Group, Motorola Inc., Scottsdale, Arizona. October 1989.
Harry, M. J. “A Quantitative Model for Assessing Producibility “. Report of the Producibility Measurement Committee, Best Manufacturing Practices, Office of the Assistant Secretary of the Navy, March, 1989.