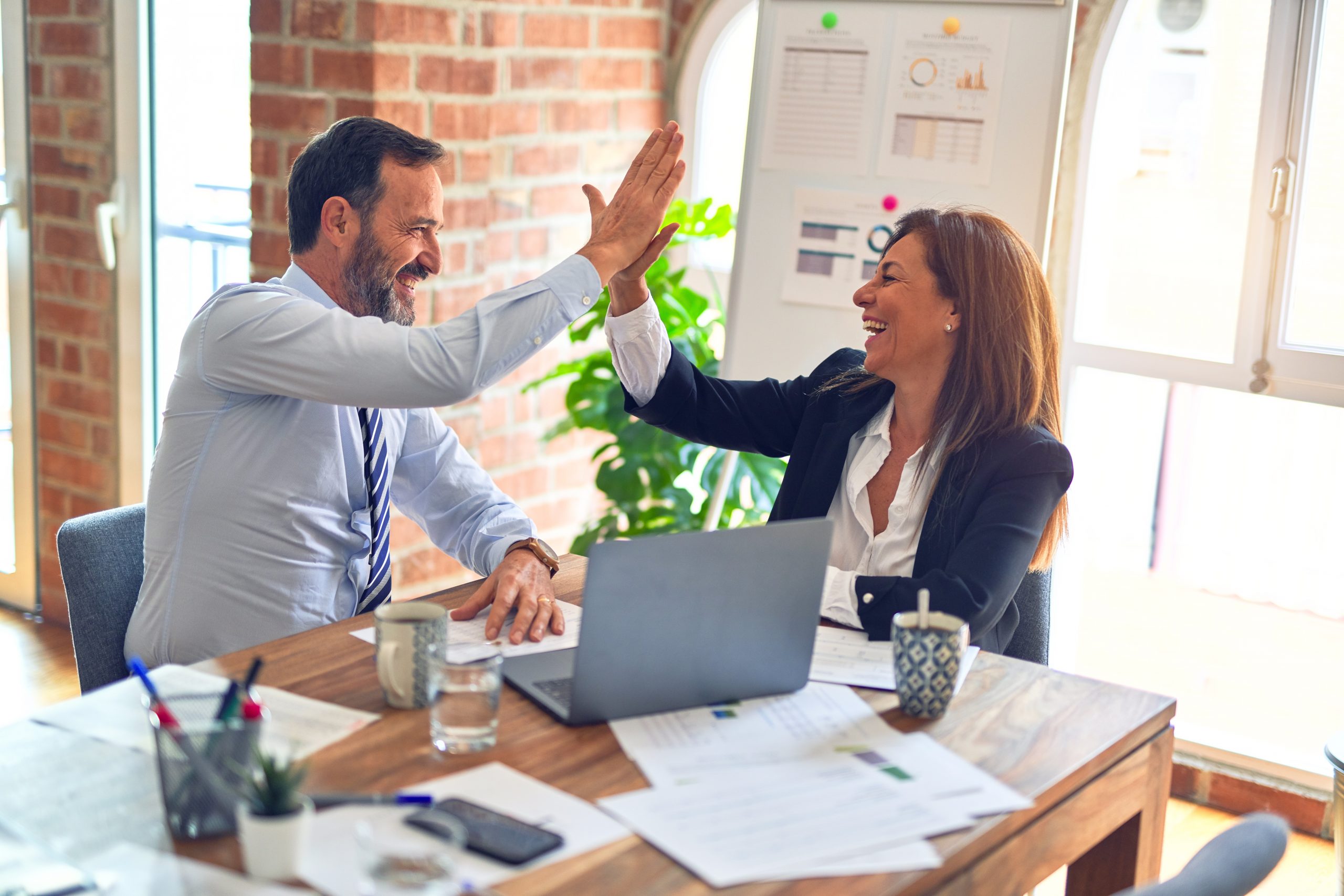
To open our discussion, we acknowledge that not all product (or service) opportunities should be Six Sigma. In the total scheme of things, some are not destined to be critical – to anything. For example, in a garden supply store we can find many different types of tools. More specifically, let us consider an ordinary hand shovel. With this in mind, think about the “clear coat” that is applied to the metal spade.
Without saying, the clear coating has purpose; otherwise it would not be applied. In this context, we recognize its role to keep a customer’s hands clean when the shovel is being handled in the store. Also to be expected, the coating should stop rust (prior to the point of sale). Finally, the coating provides a nice glossy look, thereby making the product more attractive (at the point of sale).
But is the thickness of the coating really a big deal? Is thickness critical to quality? Must the nominal thickness be precisely controlled during production? In this context, does control translate to added value? Although somewhat rhetoric, these questions should serve as a wake-up call to designers. Too often, such questions are not asked – designers simply default some of the key performance specifications (i.e., assign the specifications based on what was done before). Such thoughtless action can often lead to output that is highly sensitive to input variation (i.e., anti-robustness)
Returning to our example, we will say the clear coat is applied in a standard production spray booth. Most likely, this type of process would be far more capable than the application would call for. Perhaps the specification would read something like; “Apply a uniform clear coat to such an extent that the spade is uniformly covered without areas of sparse application, excessive build-up, sagging or runs.”
When such a capable process has been mated to a loose specification, it easy to see why the product quality would be fairly robust (i.e., resilient) to process variations. Ultimately, this is to say that a given state of customer satisfaction would remain fairly stable in spite of moderate product inconsistencies and anomalies. In other words, the product specification is broad enough to tolerate process errors without the burden of quality consequences. From a different perspective, it can be said that the process is free to wiggle around without adversely impacting the outcome.
We now ask: “How can robustness be achieved?” Well, one way is to increase the grade of inputs. For example, a higher-grade paper is generally robust (i.e., impervious) to eraser burns. Another way to achieve this aim is to experimentally discover the optimal settings among the process variables. Doing so might reveal that certain settings can disarm the harmful influence attributable to one or more of the vital few variables. Yet another way would be to simply widen the product specifications of those performance requirements not considered to be critical to quality.
By design and cleaver execution, it is possible to create Six Sigma output with less that Six Sigma input. Frequently, we are able to achieve this aim by: 1) widening tolerances that are not critical, 2) desensitizing process variables, 3) exploiting nonlinearities and 4) taking advantage of variable interactions. For more on this topic, see the many existing sources of information on robust design.