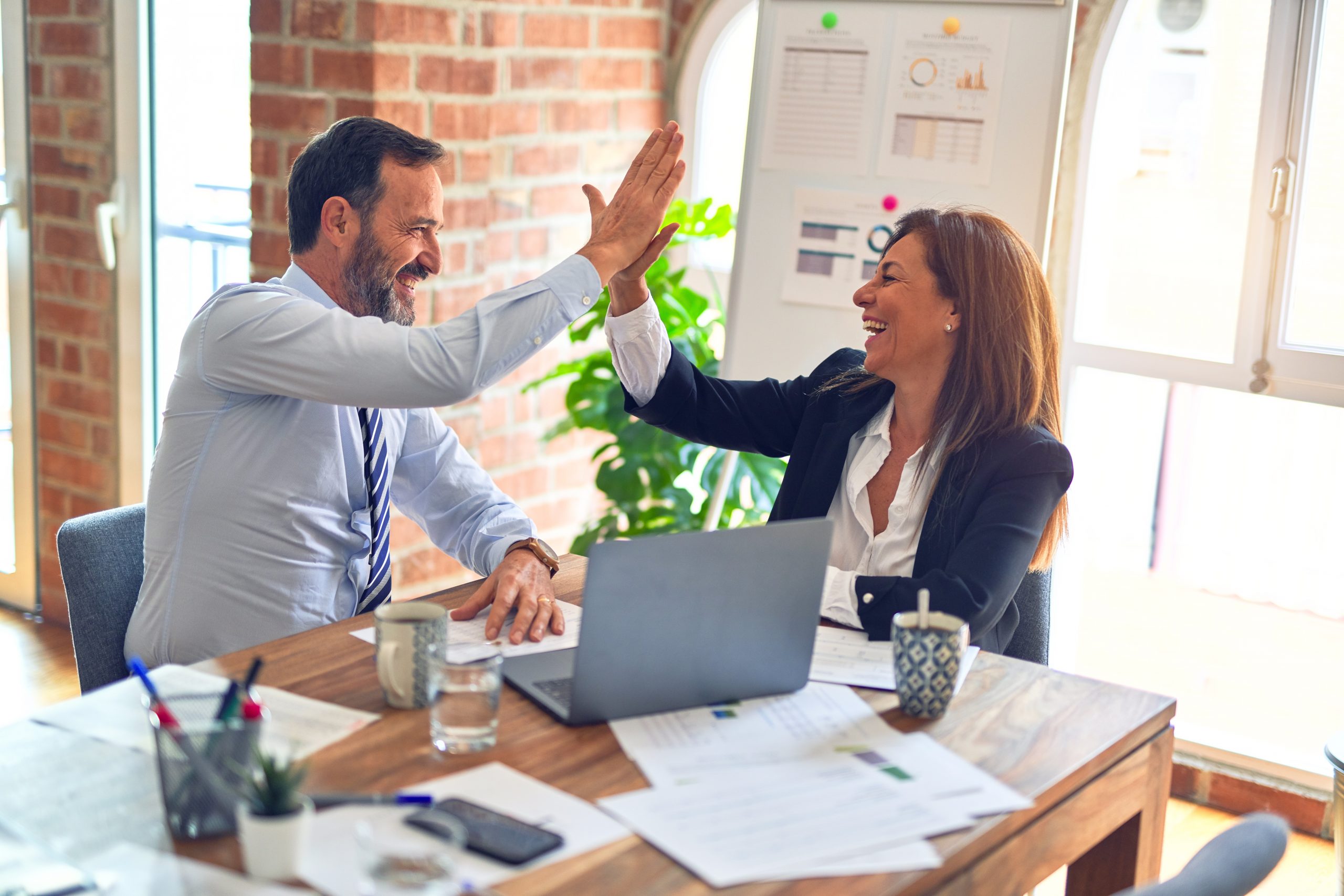
Daniel Burnham brought Six Sigma to Raytheon from AlliedSignal in 1998. Their enterprise-wide deployment has prospered and is known as Raytheon Six Sigma. They follow the unique Raytheon Six Sigma Process, six steps that guide projects to completion: visualize, commit, prioritize, characterize, improve, and achieve. They have also customized the titles they give the Six Sigma workforce: Specialists (Green Belt), Experts (Black Belt), and Master Experts (Master Black Belts).
Raytheon annual reports are loaded with Six Sigma success stories and project results. From 1999-2004 Six Sigma is mentioned 93 times! Today William Swanson continues to drive Raytheon Six Sigma to new levels.
Savings and Benefits
Currently Raytheon Six Sigma infrastructure includes:
- over 1,200 Raytheon Six Sigma Experts
- 46,000 Raytheon Six Sigma Specialists
- 50 Master Experts
- 9,000 senior-to mid-level trained leaders
Results:
- $3.8 billion in financial benefit
- Common language and culture across the business
- Has become the Raytheon way of doing business
Raytheon Six Sigma, Conference Brochure
Process discipline. We believe this helps us become more predictable in everything we do, from program management to software development. Raytheon Six Sigma (R6s), for example, has become part of the DNA structure of our company. With tens of thousands of R6s Specialists, hundreds of Experts, and dozens of Master Experts, R6s is embedded in the company. Over the years, the application of R6s has transitioned from cash management to program performance, engineering and suppliers, and now to growth.
A Raytheon Six Sigma project, the Radar Affordability Project, resulted in a 30 percent reduction in ballistic missile defense system radar unit costs.
2004 Annual Report
Supported by the principles of Raytheon Six Sigma’s and our world-class Integrated Product Development System, our objective is to meet our commitments and help our customers defend against the proliferating missile threat.
2003 Annual Report
We initiated Raytheon Six Sigma four years ago, and today it is firmly established. Raytheon Six Sigma has achieved a cumulative gross benefit of some $1.8 billion in its first four years. So far, 14,000 employees have been trained as Raytheon Six Sigma Specialists and 1,100 as Experts. Raytheon Six Sigma operates on a very simple principle: envision the desired end state, define the current state, then fill the gap. This is how our employees seek to meet our customers’ needs and grow our company.
Drawing on Raytheon Six Sigma and innovative technology, the business achieved a rise in parts availability from 57 percent to 92 percent, a reduction in warranty claims processing from 31 days to eight days, a reduction in average time an aircraft is grounded due to maintenance issues from 14 days to less than 25 hours, and the successful launch of an industry-leading retail parts Web site.
2002 Annual Report
Raytheon Six Sigma is our approach to improving everything we do. It teaches us to address a problem by defining where we are today, using data for an objective assessment, and then defining where we want to be – the desired end state. The challenge is to close the gap using disciplined processes.
In 2001, Raytheon Six Sigma initiatives generated approximately $150 million in operating profit and $300 million in cash flow. We have qualified over 6,000 Raytheon Six Sigma Specialists to date, with thousands of others in development. We now have 865 Experts who have completed training. And in 2001 and early 2002 we identified 28 Master Experts. Their assignment is to work with business leaders in our operations to develop ways to leverage Raytheon Six Sigma to help us achieve operational goals. Raytheon Six Sigma is becoming an integral part of our culture.
Applying Raytheon Six Sigma with a coordinated plan at manufacturing centers in Forest, Miss., Andover, Mass., and El Segundo, Calif., resulted in a 400 percent increase in radar production throughput – and delighted customers.
In 2001, C3I identified and carried out Raytheon Six Sigma improvement initiatives with more than 20 customers. The objective was to help the customer solve problems – and make Raytheon the kind of company with which it is easy to do business.
2001 Annual Report
In the year 2000, Raytheon Six Sigma initiatives generated approximately $100 million in pre-tax profit and $200 million in cash flow – and many satisfied customers and empowered employees.
2000 Annual Report
Raytheon Six Sigma can provide competitive advantage. It can empower the workforce. It will focus on productivity, cash, and technology. It is not a panacea. It is a step in the right direction. And it is a step most companies will have to take sooner or later to remain successful.
1999 Annual Report
Great companies are the most productive in their industries. By improving productivity, they reduce costs, increase their ability to win new business, and grow. Since Raytheon’s employees will drive the company’s growth, they will be given the most powerful tools available to get the job done. One of these tools is Raytheon Six Sigma, launched in January 1999, but already at work in informal ways in 1998.
At Raytheon, Six Sigma is more than a quantitative statistical measure of processes; it embraces every aspect of work, using a disciplined, fact-based approach to problem solving. It is a new way of thinking about work and customer value. It is also a powerful force to create one corporate culture.
The program goals for 1999 are to educate 800 leaders of the company in Raytheon Six Sigma; to complete accelerated training of 75 legacy experts, employees who came to Raytheon with significant Six Sigma experience; to graduate 125 new experts — similar to “Black Belts” in other Six Sigma programs; to end the first year of the program with another 250 experts in the training pipelines; and to graduate 250 specialists — similar to “Green Belts.” The goal is that by the year 2001, Raytheon will have 1,200 trained experts initiating major cost savings processes and 25,000 trained specialists adding value to their work areas. The objective is substantial productivity savings and growth.
1998 Annual Report
Articles and Links
Raytheon Six Sigma, Raytheon website. One of the best descriptions of a corporate Six Sigma initiative. Including What is Raytheon Six Sigma, the Raytheon Six Sigma Process, Success Stories, and Products and Services.
Ready, Aim, Fire, the MANUFACTURER.com, March 31, 2005
Using an Integrated, Continuous Improvement Model to Transform Organizational Culture and Maintain a Focus on the Customer, APQC 2005 Members meeting
Raytheon’s New Challenges, New Solutions, and Documented Results, Defense AR Journal, August to November 2004
Raytheon’s Six Sigma Process and Orgasnizational Innpvation and Deployment (PDF), Defense Technical Information Center NDIA/SEI CMMI Technology Conference, Denver, Colorado, USA, November 16-18, 2004
Raytheon’s Six Sigma Process and Its Application for CMMI (PPT), Defense Technical Information Center, NDIA/SEI CMMI Technology Conference, Denver, Colorado, USA, November 17-20, 2003
Tabtronics In Raytheon Six-Sigma For Suppliers Program, TABTRONICS press release, November 11, 2002
Raytheon Six Sigma Culture on LPD 17 program Force Multiplier for Productivity, National Shipbuilding Research Program