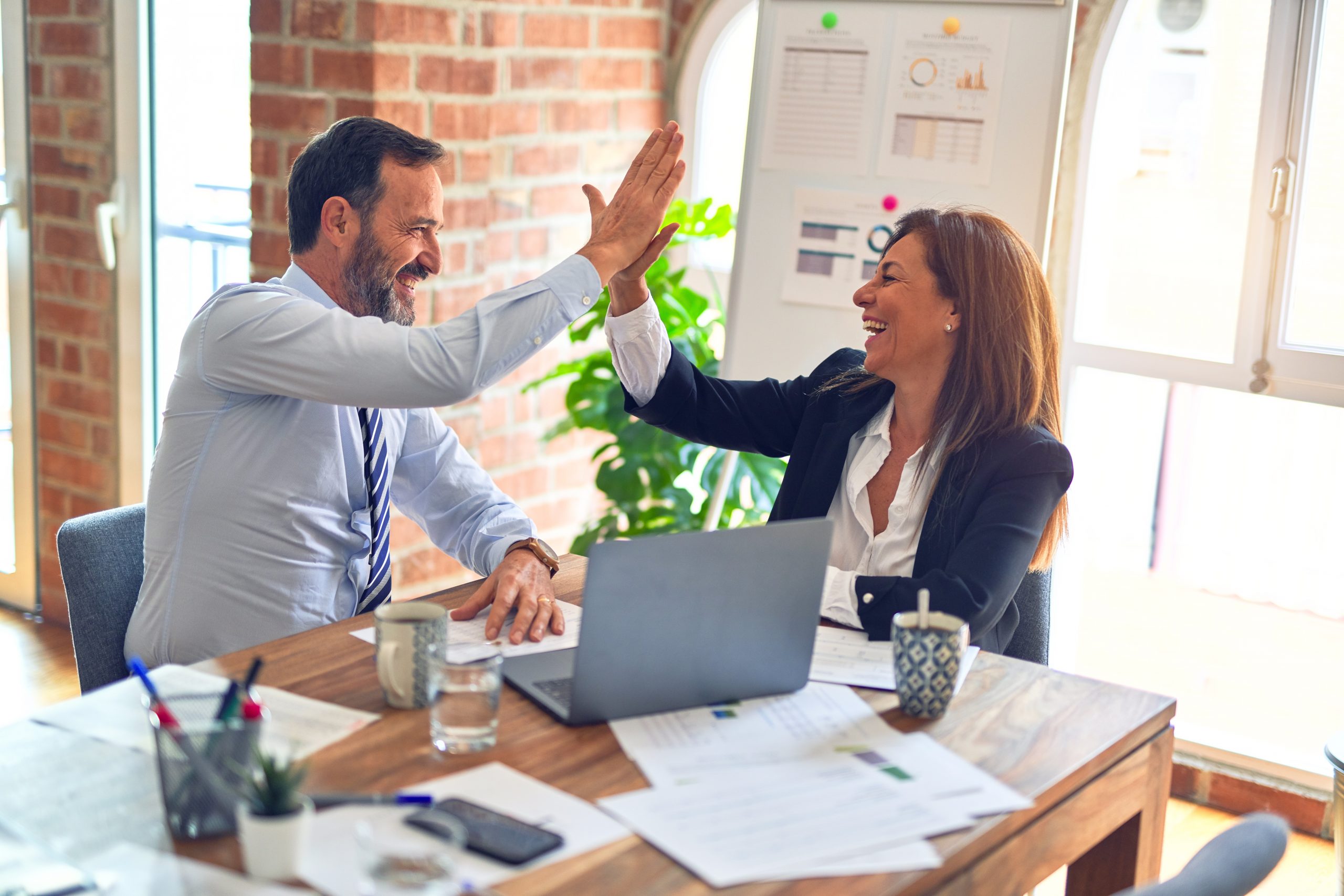
The definition for Six Sigma was clear from the beginning – 3.4 defects per million opportunities (DPMO), allowing for a 1.5-sigma process shift. But the definition for zero defects is not so clear. Perhaps zero defects refers to the domain beyond 3.4 DPMO. Or perhaps it refers to designing defects out of the process or product, so that – theoretically at least – a company can consistently manufacture a defect-free product.
There is value in trying to understand the meaning and purpose of this oft-used term, and whether its use is the best approach in a Six Sigma environment of continuous improvement.
Possible Pitfalls of Pushing Zero Defects
Quality guru W. Edwards Deming believed that slogans and programs such as zero defects are usually counterproductive. D.C. Montgomery, author of the book Introduction to Statistical Quality Control, agrees, commenting that these programs typically do not drive the “use of proper statistical and engineering tools into the right places of the organization,” and they “devote far too little attention to variability reduction.” In other words, the use of slogans such as zero defects to spur quality may lead to a de-emphasis of the tried-and-true tools and culture associated with successful continuous improvement.
But can a mere slogan actually discourage the successful implementation of proven Six Sigma continuous improvement methodologies? This can best be answered by considering the expectations, the conflicts and the different levels of understanding surrounding the term zero defects.
Literally zero defects corresponds to a defect level of infinity sigma, which most practitioners will admit is not possible. And yet an enthusiastically institutionalized zero defects program may unfortunately promote the belief and expectation that true zero can and should be achieved. This is evidenced by several phrases that quality professionals may have heard spoken – or at least heavily implied – by business strategists:
- “All defects are the same, since all defects are bad…”
- “There is no such thing as a benign defect.”
- “If we can get rid of the defects, then we can get rid of the testing.”
These expectations are worth examination.
Statements That Do Not Align with Facts
In fact, all defects are not equal. Defects, depending on their size and type, have different probabilities of impacting the finished product. And these probabilities depend on the technology. In fact, the impact probability of a particular defect may vary within the technology – that is, at the stage or layer in which it occurs. When it comes to the practical definition of a defect, “bad” is a relative term. Many defects are simply neutral. They are never good, but – again, depending on the technology – they may cause no harm either. If all defects are considered bad, then prioritization is difficult.
It is the role of statistically minded scientists and engineers to classify defects and their potential impact, based on data and engineering judgment. This allows them to systematically reduce defect levels in a prioritized fashion, starting with the worst and progressing toward the more benign. Without this kind of problem-solving prioritization, progress may be slow and confused – perhaps even at a standstill. The ability to prioritize is absolutely necessary in the continuous improvement process.
The statement that if fewer defects are produced, then less inspection will be required is incorrect. Actually, the opposite is true. A higher level and sophistication of testing is required to detect a smaller level of defects. The plot in Figure 1, derived from a cumulative binomial distribution (pass/fail inspection) shows how the sample size increases exponentially as the prevalence of a defective unit decreases. The particular curve in Figure 1 corresponds to a probability of detection of 95 percent. In other words, if a defect is present at the indicated level (x-axis), there is a 95 percent probability that at least one failed unit will be detected using the sample size indicated on the y-axis.
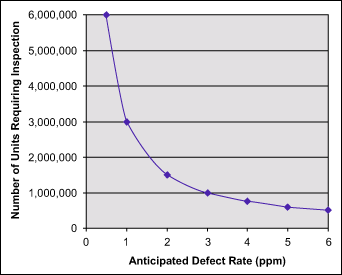
A more intuitive example is: If a shoebox full of needles is mixed into a haystack, only a portion of the haystack will have to be moved before the presence of needles is detected. If there is only one needle in the haystack, every straw may have to be moved before it is found, assuming it is not missed entirely.
This is really the misunderstanding that drives the inappropriate application of a zero defects policy to multiple points along the supply chain (Figure 2). It may be thought that producing zero or near-zero defects at each point will lead to reduced or eliminated inspection/testing prior to shipment to the end-customer. But for zero defects to approach reality, the inspection/testing must remain the same or increase at the final inspection point. If zero is truly the goal, then 100 percent sampling at the “escape” point is required, regardless of defect levels. This implies, then, that any zero defect inspections prior to the escape point may be non-value-added.

Ideally suppliers need to produce the highest quality output possible, in order to maximize yield and minimize costs which ultimately benefits both the supplier and the customer. But a zero defects policy does not provide this motivation to suppliers. When the goal of zero defects is applied to multiple interim points along the supply chain, the undesired effects of increased costs and lower yields are encouraged. The increased costs come from increased tests, inspections and cycle time. The lower yields are likely because of a higher rate of “false fails” (type 1 errors) as the suppliers apply increasingly stringent criteria in an attempt to eliminate potential failures at the customer’s incoming test/inspection. In other words, in an effort to eliminate even the smallest possibility of customer incoming test failures, good product may be scrapped to overly stringent criteria.
Negative Impact on Workforce and Supply Chain
A focus on zero defects may be stifling to a discussion of continuous improvement, and may lead to frustration and non-productivity. To the general workforce, it may be a demoralizing concept. While everyone understands that continuous defect reduction is critical and necessary, most people understand, intuitively at least, that true zero is unachievable. Always striving for an unachievable goal may eventually de-motivate even the most optimistic of employees, particularly if they are frequently told that their defect level is unacceptable – because it is not zero.
For a company’s suppliers, continuing to add tests and inspections in an effort to comply with zero defects (perhaps at their customer’s demand) may eventually drive them out of business. Thus, while continuous improvement is applicable to everyone, zero defects can or should only be applied to the final supplier, rather than at interim points along the supply chain. Attempting to do the latter may eventually put one or more of the suppliers in jeopardy. If a supplier critical to the company were to fail, the company’s supply chain might collapse, which might eventually put the company out of business too
Finally, it should be realized that the inspections and tests themselves (however careful and precise they are) have a finite probability of actually causing a defect. This concept is somewhat akin to the uncertainty principle: “We may significantly modify what we are trying to measure simply by making the measurement.”
Conclusion: Strive to Be Better and Better, Not Perfect
Since the slogan zero defects implies immediate compliance to a defect-free standard, it may not leave time for the continuous improvement process to occur. In fact, it may even slow down the continuous improvement process because of the massive resources that inspected-in quality entails.
Zero defects is a message that can carry with it confusion and misinterpretation, mixed with technical impracticality. It may be appropriate that the idea of zero defects be replaced with a policy of zero escapes, since the latter has limited interpretation. As a company is doing all it can to improve the product and business using continuous improvement techniques, it also needs to consider what it can do to prevent a random, low-level defect from reaching the final customer. In this regard, zero escapes of defects may be a complimentary activity to continuous improvement.
A logical strategy is to employ continuous improvement methodologies everywhere in the business and manufacturing process to improve quality and yield, and reduce cycle time and costs. Then, at the point of shipping the final product to the final customer, employ a zero escapes methodology to help ensure that a randomly defective unit does not reach its final application. The tools and techniques developed and employed at this final gate should be arrived at through a team effort of the various suppliers and interim customers. Expecting individual suppliers in the supply chain to produce zero defects, in an effort to eliminate or minimize the final gate, is likely to be an impractical strategy.
Quality professionals already have specific, descriptive methodologies that are aimed at achieving the same goals as zero defects. Here are but some of the methodologies already in use and being developed to minimize the defects in the end product:
- Design for manufacturability (DFM)
- Design for yield (DFY)
- Design for test (DFT) – “DFM: Worlds Collide, Then Cooperate” by L. Peters in Semiconductor International, June 1, 2005.
- Robust design
It is probably best to not encourage the use of somewhat ambiguous terminology in the place of well-defined and meaningful methodologies such as these.
The concept of continuous improvement is intuitive. It makes sense to always strive for a better process or product, to reduce costs, satisfy customers and gain market share. Absolute perfection can never be achieved, but an organization can move closer and closer with good statistical and engineering practices.