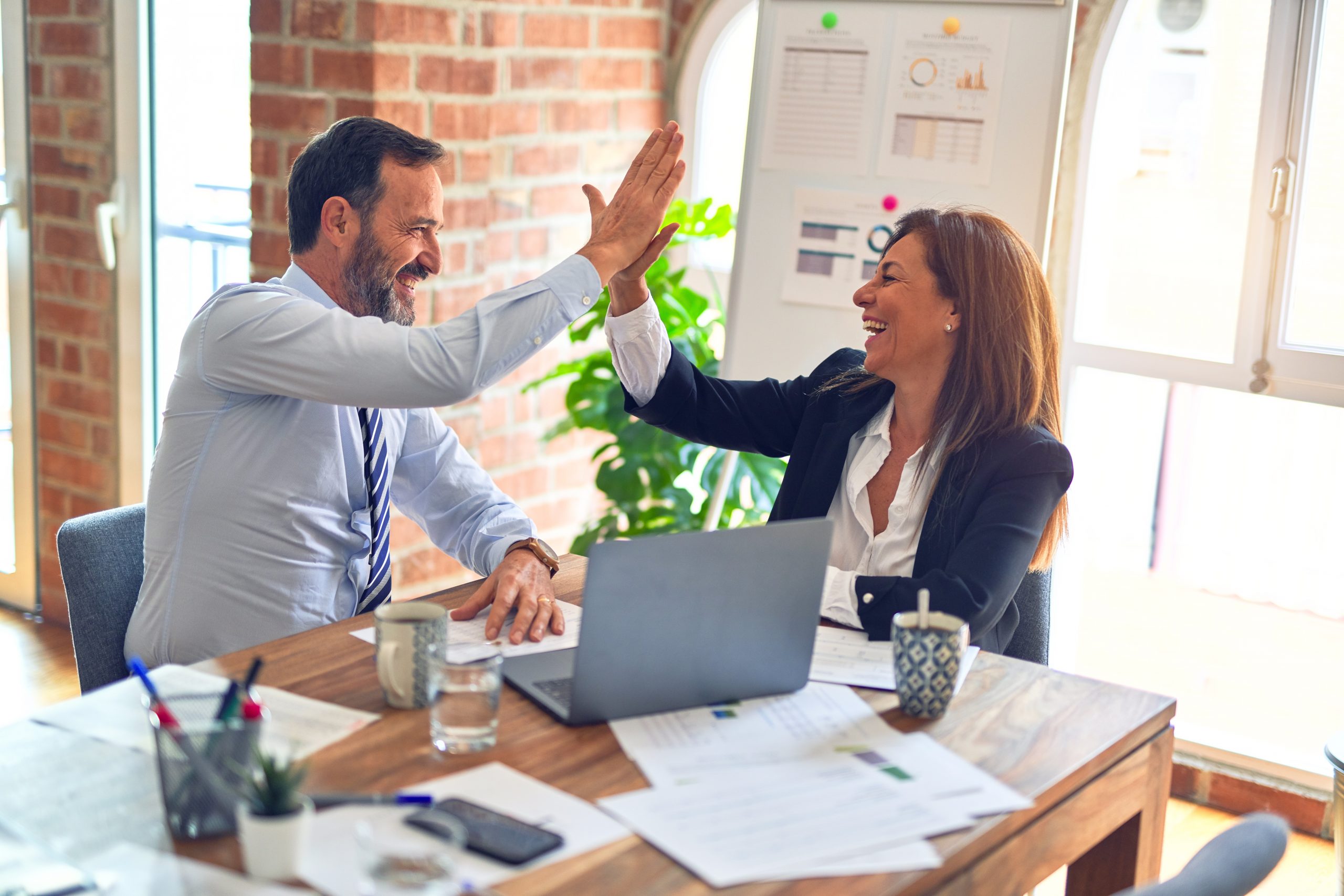
Applying Lean Six Sigma (LSS) to the architecture/engineering/construction (AEC) industry can create unique challenges. LSS is not heavily used in the service industry and almost never used in AEC businesses. When LSS is presented to an AEC firm one of the first comments from the company’s team members is, “If it ain’t broke, don’t fix it.” This comment comes from a lack of understanding of what is possible. It comes from an attitude of “We’ve always done it this way.” What they do not realize is that their system is broken.
It has been estimated that the service industry is operating with a level of waste at close to 80 percent. Many AEC firms do not even attempt to reduce that waste and have no problem passing the cost of that waste on to their clients.
Introducing LSS to an engineering office, architectural office, or a team of construction workers can be daunting. In general, members of the AEC industry perceive LSS as not applicable and not useful to their day-to-day operations. This comes from an attitude of resisting change and results from rejecting LSS before they understand how it works. They do not believe the LSS success stories and think they are overstated. This resistance, however, is certainly not insurmountable. It does, however, require a deliberate approach.
1. Make LSS Strategic
It is critical that LSS be presented to the organization as the new method of operation, not just an experiment. It needs to be clear that LSS is not a fad that will fade but a permanent approach to doing business. This means that LSS needs to be built into the company strategy. It needs to be apparent in the long-term vision, mission, objectives and metrics, and needs to be cascaded to every operational unit throughout the organization.
Every member of the organization should not only have a clear understanding of what LSS is but should also understand how it applies to his or her daily activities. Members of an organization should understand how to use the LSS tools that apply to their daily efforts and see a direct connection from their application of those tools to the organizational system as a whole. This requires an extensive training program to ultimately touch every person in the organization.
2. Make LSS Cultural
Far too often the application of LSS becomes a recurring cycle of selecting a specific tool to use, celebrating temporary improvements, and then getting frustrated when the same old issues come right back. LSS is far more than a collection of tools. It is a powerful management and cultural paradigm that should affect every decision, behavior and action throughout the organization. Ultimately, those short-term temporary improvements need to evolve into long-term continuous improvement; this requires that LSS be deliberately infused into the culture of the organization.
Making LLS a vital part of the culture requires that the purpose and importance of LSS be included in the principles, values and beliefs fostered by the organization. It needs to become foundational to the purpose of the organization and essential to the organization’s competitive advantage and long-term success. Instead of just applying LSS tools, develop a LSS culture of continuous improvement.
3. Make LSS Scientific
If the organization is going to effectively apply LSS, members of the organization will need to witness its results. They will need to have clear evidence that the effort will be worth it. This means that the metrics used by the organization need to track the improvements directly associated with a LSS approach; the metrics should be strategically focused and not just randomly applied. If LSS efforts are not being measured, members of the organization will not take it seriously. Team members will assume the improvement does not matter. When the positive impact of LSS is made clear using effective metrics, the organization’s commitment to LSS is magnified.
It should be made clear that metrics are not to be used to punish or assign blame. They are used to drive performance and influence behavior. This means that metrics should not only include key performance indicators but also key behavioral indicators. This combination measures results as well as the behaviors contributing to those results. It is difficult to achieve high performance without encouraging ideal behaviors that create and sustain that level of performance.
Example: Engineering Calculations
A staff engineer spends 20 hours over three days preparing the calculations on a project. After completing the calculations, the staff engineer sends them to a senior engineer for review. The senior engineer does not get around to reviewing the calculations for two days. He then spends two hours reviewing the calculations and provides feedback.
The staff engineer then spends three additional hours revising the calculations and returns them back to the senior engineer. After two more days, the senior engineer spends another hour reviewing and provides additional feedback. The staff engineer then spends two more hours making revisions and sends the calculations back to the senior engineer. The senior engineer then sends the calculations to the engineer responsible for stamping. After four days and three hours of review time, the engineer in charge provides feedback to the staff engineer including several changes to the design approach of the project. The staff engineer spends six hours revising the calculations and sends them back to the engineer in charge and cc’s the senior engineer. After four more days, the staff engineer follows up with the engineer in charge to determine if the calculations are approved and stamped. Two days later, the engineer in charge sends the stamped calculations to the staff engineer.
Does this process seem rational? Or is it overburdened with repetitiveness and redundancies? In this example, the inefficiencies of the firm’s operations resulted in nearly 45 percent wasted time. This wasted time resulted in an extra cost of more than $1,500. This cost is covered by the firm, the client or both. It took the firm 17 days to produce a final product that could have been produced in four days if the waste and delays were eliminated. Unfortunately, this type of scenario is not uncommon.
Applying a LSS perspective to this example, the total amount of time spent on the project was 17 days times 8 hours per day, which equals 136 hours. The amount of time spent working on the project was 37 hours. The total waste time was 99 hours (73 percent). The goal should be 37 hours. (In the Lean world even that would be too much since there are probably inefficiencies in the way the work itself was performed.)
Example: Purchase Orders
Overly excessive control can seriously damage performance as happened in the purchasing office of one of the world’s largest oil and gas conglomerates. In this case, because of a history of inaccurate purchase orders, a series of controls were put in place to make sure that all purchase orders were properly vetted. A purchase order now required 16 approval signatures before it could be released.
The process of routing this document often took six to eight months. The business needed to streamline the process. Each of the 16 signees were asked what they looked for on the document to determine whether or not to sign it. Every one of the 16 shared that all they looked for was that another specific individual had signed the document. If so, they were sure the purchase order had to be correct.
In the end, they had 16 control points for every purchase order, all of which created waste and time delay, and none of which added value, since none of the signees actually checked the document. The failed system drove this behavior because it caused a false sense of security for all the signees. It would have been better to have one control point where the document was looked at carefully. Then there would be more accuracy and significantly less waste.
This type of redundancy and waste is also seen in the engineering example. Using the same logic, there was 90+ percent waste in the way project submittals were created. And this waste equates directly to dollars.
Conclusion
Few organizations in the AEC industry use LSS. They continue to do things the way they have always been done. They operate with huge amounts of waste and are making little effort to reduce that waste. This information should be exciting to the leaders of organizations in the AEC industry. Because if LSS can be used to reduce the waste in an organization, huge competitive advantages can be gained. A business will be able to provide unmatched service, production speed and quality at unbeatable prices.
When working to apply LSS, make it strategic, cultural and scientific. That is the formula for producing sustainable results that will render the competition irrelevant.