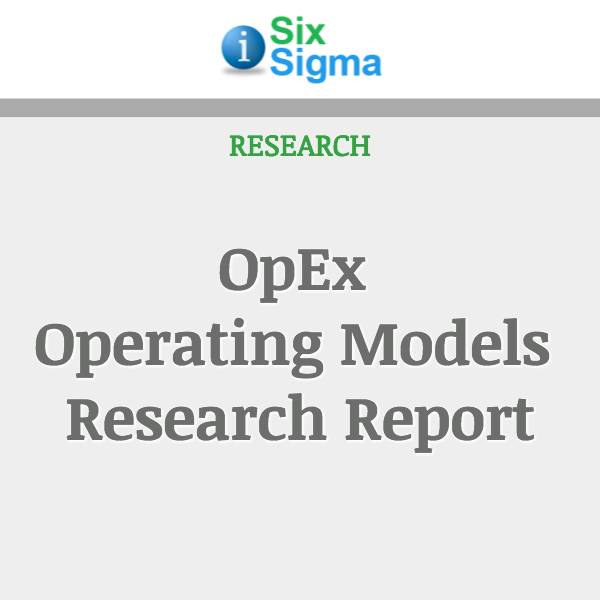
The Lean Six Sigma (LSS) Green Belt and Black Belt curriculum needs an overhaul. The original operational excellence (OpEx) Lean Six Sigma methodology developed by Motorola in the 1980s and made famous by Jack Welch at General Electric (GE) in the early 1990s is finding itself a bit long in the tooth in comparison to the digital transformation activity going on around it. Practitioners of Lean Six Sigma who learned their craft more than 10 years ago need on-the-job training or CE (continuing education) classes to remain valuable to their client companies. The digital transformation has overtaken this quaint methodology, and unless continuous improvement teams embrace the new paradigm, their ability to affect the world will get smaller and smaller.
To be fair, the Six Sigma methodology (DMAIC [Define, Measure, Analyze, Improve, Control] or DFSS [Design for Six Sigma]) was an amalgamation of the best statistical minds at that time. Designed to solve process problems that resulted in defects, or to stimulate product design aligned with customer desires, it offered a linear approach to fact-based decision-making with an eye to customer needs. It took the arrogance out of process improvement and drove intellectual curiosity, which eludes more managers today than you might think. In the 80s and 90s, technology was a distant star. However, while technology grew up around it, LSS engineers huddled in their corners, not realizing the importance of evolving to the new concept of predictive statistics, machine-based learning, neural networks, artificial intelligences and the management of the data as an asset in the sciences.
And this is where the change needs to happen. Even the classic Green Belt-certified practitioner should be able to parse out the difference between waterfall and Agile methodology for software build, and that should be taught in the “I – Implementation” chapter. Lean Software Development was written by Mary and Tom Poppendiecks in 2003, but few have embraced it as part of the OpEx body of knowledge.
In a digital world nothing, and I mean nothing, is ever built without a technology component. And yet, all the explorative knowledge uncovered in the D, M and A phases should be driving towards the completing of the standard technical documents (BRD, FRB and technical specs). A good Green Belt can be an excellent IT business analyst, with their ability to articulate design and root cause, and yet, very few trainers and students make this connection. It’s as if OpEx, IT and the digital world are separate planets around the same strategic sun. I proclaim they are linked, and here are my first 5 recommendation where OpEx, LSS and continuous improvement practitioners need to make the biggest changes in their body of knowledge.
1. Data as an Asset
Let’s recognize that anything digital means data as an asset. A “digital” company is data-driven and data-democratic. Therefore, we should teach the 5S’s (sort, simplify, shine, standardize, sustain) in terms of data governance or a data quality function. As if it was a factory floor, dirty data is a business showstopper, so let’s give a quick nod to the 5S’s for good data quality. These are the fundamental tenets of managing data in the digital age. True, you don’t take out a brush to shine the data, but if your OpEx practitioner is not providing solutions or disciplines for good data quality or good data governance, fire them.
2. Customer Behavior Analytics
Replace the analytical hierarchy protocol (AHP) chapter with a discussion on web clicks and neural networks. I am not saying this has to be in the Green Belt class, AHP was included in my Black Belt class, but please, there is so much more “behind the black mirror” analysis of what the customer wants, and coupled with predictive analytics (see #3 below), you don’t have to ask the customer anymore. An OpEx practitioner can add some neuroscience-based suggestions to new product/new service development.
3. Retire CTQ
Remove the voice of the customer (VOC) critical to quality (CTQ) tool completely. In fact, this part of the DMAIC/DFSS curriculum needs a complete re-write. With machine learning based on customer data, the traditional interview and focus group should be dying like the dinosaurs. We don’t have to ask the customer if our organizations are transforming to a digital world; we already know. If our company is not yet using customer predictive modeling, a good OpEx practitioner should be driving them there. A company that has embraced a digital transformation can predict customer behavior, even the irrational customers, and continue to track customer “voice” as it changes over time. These days, the CTQ tree is theoretical at most, obsolete at best.
4. Data Visualization as a Self-Service Tool
Data visualization is a key component of transformation to digital, but how many OpEx practitioners know how to navigate the big 4 offerings in data visualization technology – Tableau, Datameer, MicroStrategy and IBM Cognos Analytics? If an OpEx or a LSS practitioner is leaving the visualization to the data scientists/management information services team, the boat is sailing and we are not on it. Digitally transformed companies have ventured far away from control charts, pareto charts and box plots. The training emphasis is no longer the creation of the charts, but the insights that follow. The message is different, the solutions are different. OpEx practitioners need to gain exposure to the better tools and learn to self-serve.
5. Remote Communication, Collaboration and Project Management
Hard-goods manufacturing and pharmaceuticals may need shop floor or process improvement for efficiency, but the growth industries are financials services, tech and hospitality. A well-rounded OpEx practitioner should be able to apply the same tools in each. LSS barely addresses the underlying needs in those companies, although they are leaders in digital transformation. OpEx practitioners are also light on project management and project leadership. In the 1980s, there was no software for scheduling, coordination or collaboration. Newly minted Green Belts or Black Belts should be introduced to Jira, Slack, Noodle or at minimum, SharePoint or some other document repository/collaboration platform. In digitally transformed companies, data democratization and virtual teams form the new organizational and work effort design. It’s more hub and spoke than production line. OpEx practitioners may need to change their coaching and management style for this change.
Each of these recommendations must be considered if LSS is going to survive the transformation to digital. The Green Belt/Black Belt curriculum should not lean on obsolete spreadsheets, but offer the penology of software options that each practitioner could find in their organization. All OpEx practitioners can be brand agnostic, but digital companies will demand that we understand the new functionality now available to data engineers and data scientists. Without embracing our own digital transformation, OpEx practitioners will cease to be a strategic partner to leadership.