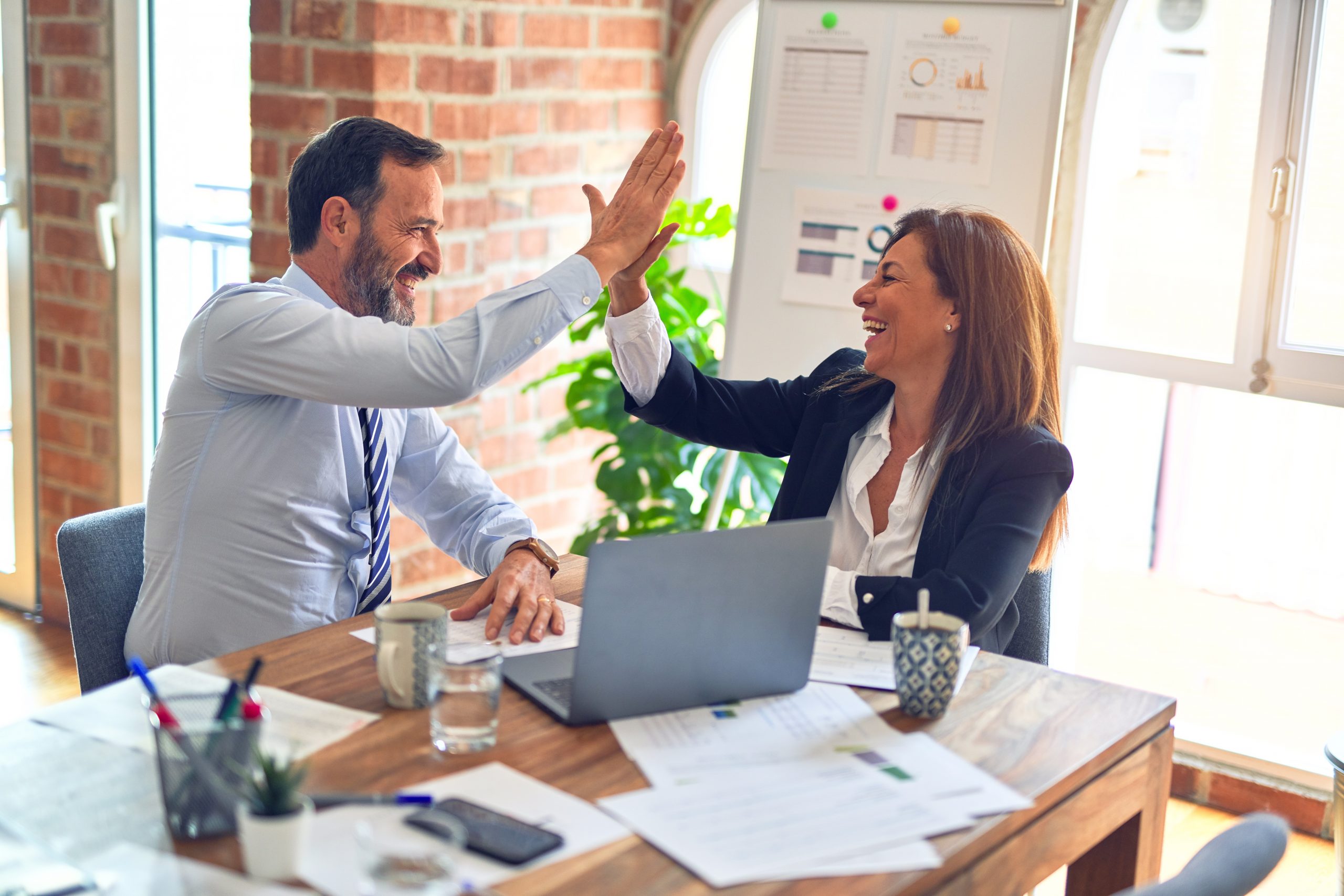
When we leave the shop floor and enter the back office, we might think that people’s desks are where they work.
We’d be wrong.
Their workbench, their tooling, their line … is in their heads.
This means that most knowledge work (information technology [IT], legal, management, product design, finance) is invisible.
My colleague Tonianne tells a story where she was working with a group of historians. One day the historians were sitting in a room reading. Their boss (yes, historians have bosses) came in and became angry. He yelled, “I don’t pay you guys to just sit around and read!”
He couldn’t see their work and, therefore, couldn’t see the value they were producing. But they were learning and thinking – which is what historians do.
Build a Workcell
When we build a workcell for a shop floor, we create a structure that is able to create the right product at the right time for the customer who wants it. This might involve customization. This might involve handoffs. But it mostly involves a small group, working on a focused workload, at a reasonable pace.
In the workcell we find the materials and tools with which to meet almost any combination of product and customization. The efficiency gains made by creating well structured workcells are well documented. The value the workcell is creating is usually apparent because the tooling – the means of creation – and the item created are all tangible.
The workcell is the gemba. We can go there, observe and learn.
Knowledge work needs a gemba.
After many years of working with knowledge work teams in nearly every vertical, I’ve found that most teams suffer from a combination of blindness and overload. They are blind to their actual work because it is invisible. Because it is invisible, they have no mechanism to know when they have too much work-in-process. This lack of understanding leads to workers taking on too much even when they are already overloaded.
Also, invisibility means no one has an idea what the knowledge worker’s capacity is. Which means the organization routinely over assigns work.
Make Work Explicit
To create a gemba, we must make the work explicit. Its duration, its associations, its impediments, its flow. We need something to observe.

A personal kanban board (such as the example shown right) provides a visual control for the team that makes it clear what their work-in-process (WIP) limits are, what work is being done and what is coming on the horizon.
This visual control is from a mid-sized financial services firm in the midwest. It is one of about 20 such boards currently in use in the IT department.
This visual control allows team members to know what other team members are doing, giving them the ability to collaborate and improve. The flow of tickets provides real cycle time metrics to the team and to management, allowing more precise estimation both before and during a project.
The image shows a value stream: Ready ? In-progress development ? In-progress testing ? Deploy ? Done.
Tickets representing actual work flow through that value stream. The tickets are all labelled with the item of value being created so that even non-team members quickly understand what is happening in the group. That understanding leads to less confusion, fewer political battles and fewer status meetings.
Flow is aided by limiting WIP. In this example, the in-progess columns are limited to 14 tickets at a time. Limiting WIP aids in flow, creating a pull system where developers pull items of customer value into the in-progress lane when they have capacity.
Before visualization, limiting WIP in the back office was nearly impossible. No one knew what was happening!
Visualization allows for the capture of cycle and lead-time data, leading to more predictable knowledge work and more stable knowledge workers. Management can get a better idea of what their overload looks like and react accordingly.
The fact that the board is a limited space means that descriptions of the project need to be both understandable and concise. The board’s space also means that the project’s status is no longer held captive in spreadsheets or large project planning documents. Everything is there for all to see, to act on and to improve upon.