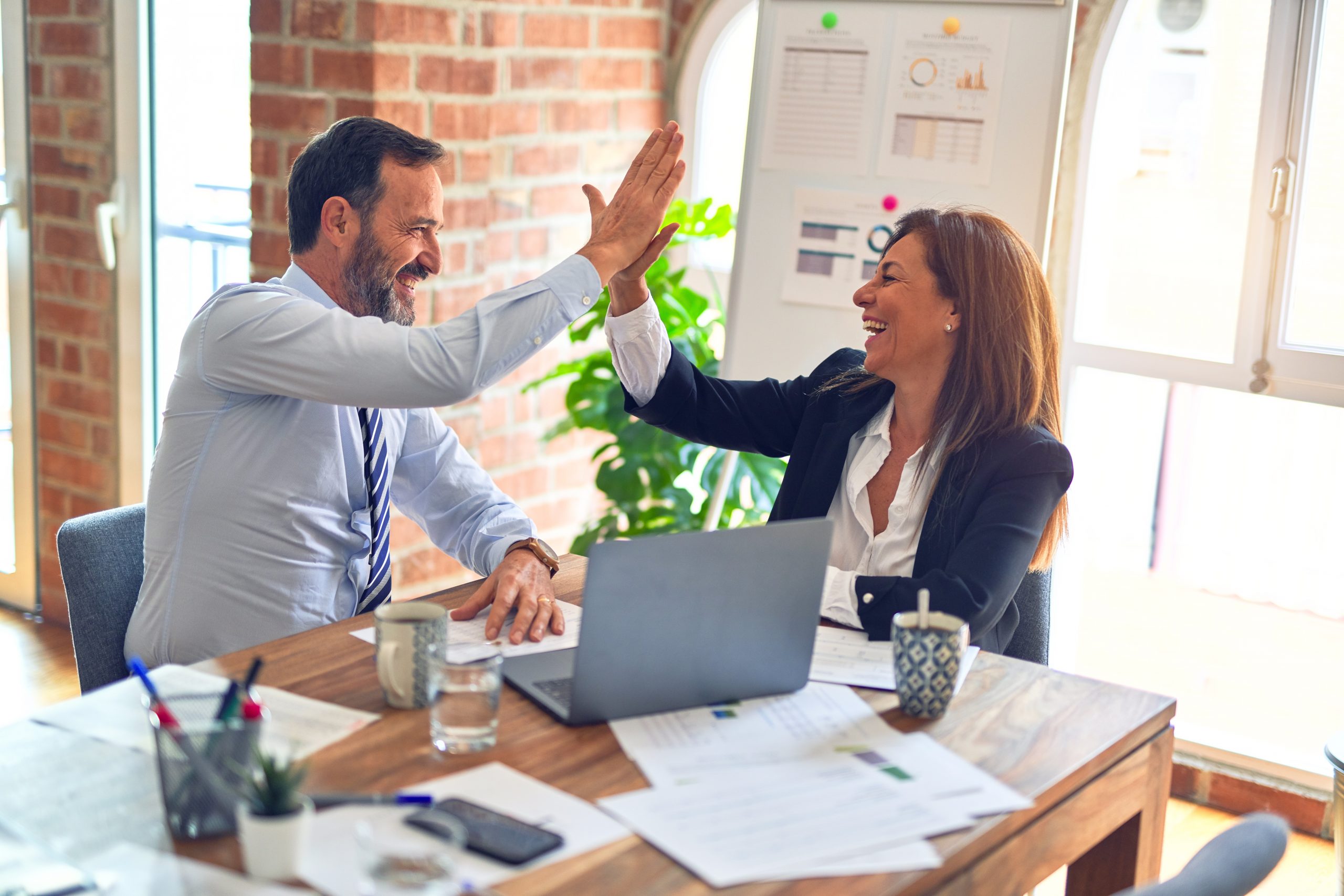
Perhaps you are both in error (as related to your Sigma calculations.) Do not be discouraged by such debate, as it is quite common among those new to Six Sigma. However, do be aware of a phenomenon I call “denominator management.”
This colorful term is used to describe the practice of inflating or otherwise distorting the denominator term of the classic quality metric called defects per opportunity. As should be apparent to the informed practitioner, such a practice is most often applied to effectively mask or confound the true quality of a product or service.
For example, consider a simple printed circuit board (PCB) that employs through-hole technology. In this case, we will exemplify the soldered connection between the two leads of a standard carbon resistor and the PCB. Given this, it is understood that each component lead must be adequately soldered to the PCB at two different but related points (i.e., on the top- and bottom-sides of the board).
For the sake of discussion, let us say that the performance category called “solder joint pull strength” is the CTQ of concern. Given the nature of this CTQ and application technology at hand, it should be quite evident that each PCB connection constitutes an independent opportunity to realize a pull-test failure. In other words, each lead of the resistor represents a defect opportunity.
If one lead of the resistor passes the pull test and the other lead fails the test, then the defects-per-opportunity metric would be properly presented as dpo = d / o = 1 / 2 = .50. A more liberal perspective would hold there are four defect opportunities since there would exist four separate solder joints (when considering the top and bottom side of the PCB). In this event, the defects per opportunity would be wrongfully reported as dpo = d / o = 1 / 4 = .25. Even more liberal would be the case that advocates six defect opportunities – four solder joints and two leads.
Taken to an extreme, some conniving managers might even try to say there exist eight defect opportunities – four solder joints, two leads, and two through-holes. In this case, the product quality would be given as dpo = d / o = 1 / 8 = .125. In this way, management could inappropriately create a 4X quality improvement by simply changing the rules of defect accounting. Thus, we have improvement by denominator management.
To avoid such an error of leadership, we must recognize that any given unit of product or service will inherently possess “Y” number of defect modes, where each mode has “X” number of active chances. Thus, the total number of defect opportunities can be described by the general relation O = S( Y * X ), where S is “the sum of.”