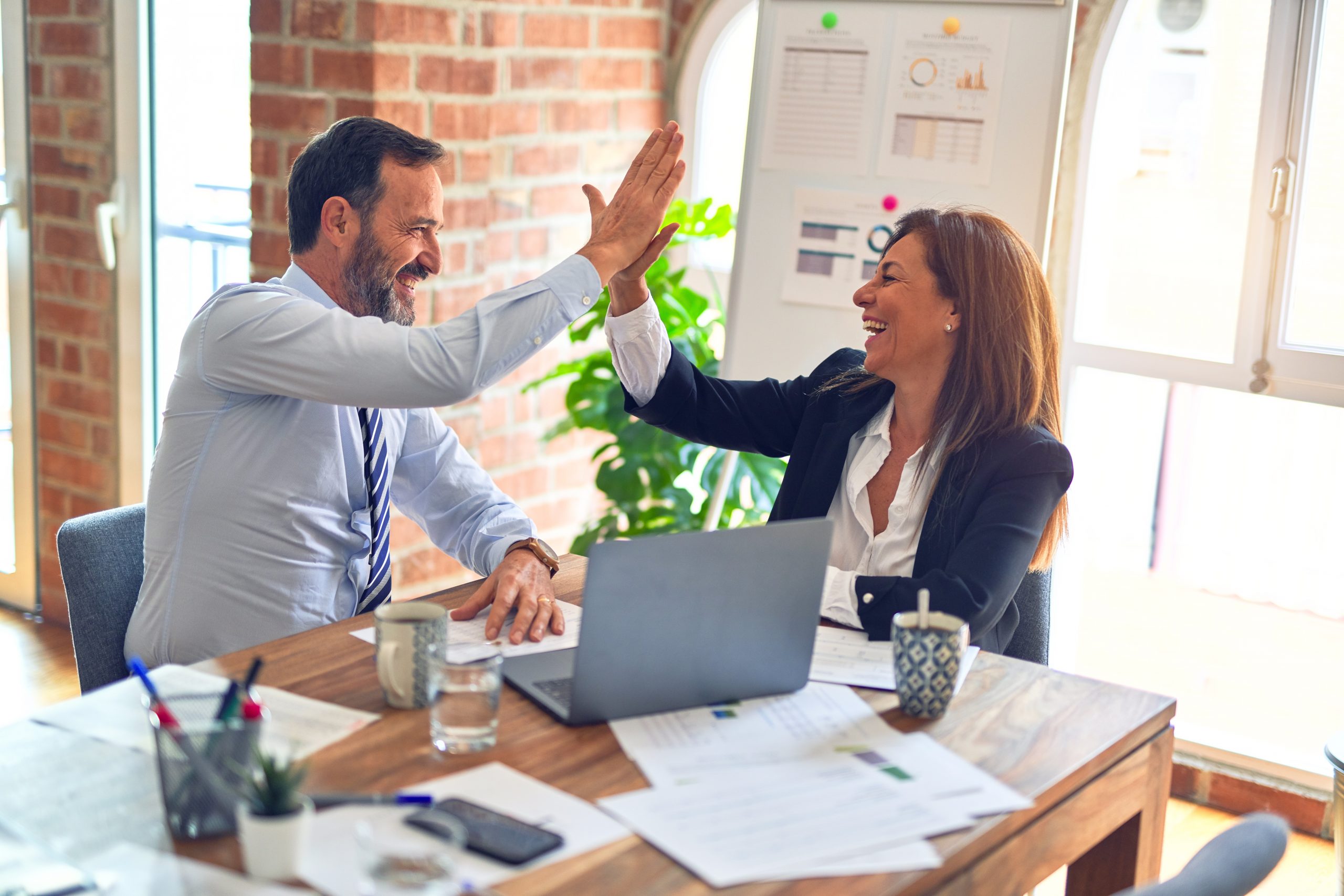
Practitioners should reach a strong understanding of the original Japanese 5S method so they will be able to educate others about it in a way that will garner employee buy-in and achieve the best results in helping their firm become more organized.
5S is a popular Lean Six Sigma tool that is designed to instill a sense of responsibility in employees and promote a disciplined approach. 5S was originally used by Toyota in Japanese factories, primarily at the shop-floor level, but now it is often used in the workplace to decrease cycle time and general flow.
There are many different translations of 5S. Because of this, practitioners should reach a strong understanding of the original Japanese method before introducing it to their workplace. By gaining this knowledge, they will be able to educate others in a way that will garner employee buy-in and achieve the best results in helping their firm become more organized.
5S: Lost in Translation?
The attempt to translate the Japanese terms for 5S – seiri, seiton, seiso, seiketsu and shitsuke – has sometimes caused confusion for those trying to implement the model.
For example, almost all English translations of the 5S model use as the first S the word sort, which is often used to mean “to place in different piles.” But seri is translated literally as “the identification of the best physical organization of the workplace.” This first step is often accomplished by discarding all unnecessary items. According to the original method, the activity of placing items in different groups happens in the second S, known as seiton.
In this article, the terms “sort,” “set in order,” “shine,” “standardize” and “sustain” will be used to represent the 5S model. Keep in mind, however, that there are several word variations using S, all intended to represent the original Japanese terms. For instance, shine, the third S, is referred to as “spic and span” in some cases, which is a more accurate translation of the Japanese word, seiso.
Because of these potential translation issues, the first opportunity to maximize success when implementing a basic 5S program is for the facilitator to clearly explain the definitions and use words that resonate with the employees. Some companies have decided to use the 5C model (clear out, configure, clean and check, conformity, and custom and practice) which is similar to 5S, but has an easier vocabulary for English speakers to digest.
Spread the Word
The next step in maximizing a basic 5S program is to study the company’s infrastructure and decide how 5S can best fit in the existing improvement structure. This should be followed with constant, but brief, communications to the workforce explaining the 5S initiative. Several formats, such as email, electronic bulletin boards and articles in the company newsletter, should be considered for this process.
The leadership team should be trained in the overall concept, and employees directly involved should be trained on each area of 5S. For example, in the second phase, seiton, or “set in order,” the goal is to place things in the right places. Will a color-coding system be used? Or will the team use a system in which the items that are most frequently accessed are placed in the most convenient area? In the seiso, or shine stage, piles are revisited, re-examined, and often cleaned or refurbished. Once again, what are the requirements? For example, art items may have a certain way they should be handled, and chemicals may have certain safety criteria. A series of workshops is one way to educate employees about these specifics.
Another way to educate employees is to develop solid, easy-to-understand documentation. For example, in seiketsu, or standardize, employees could be introduced to a schematic drawing showing visual controls and be invited to discuss areas of risk. For shitsuke, or sustain, employee training may consist of frequent updates on the success of the system through the company newsletter or targeted emails.
Clearly, proper education is one way to maximize the success of a 5S program. This also should include those facilitating the project. Facilitators and leaders of the 5S effort should have a strong understanding of project management and deployment plans.
Plan for Optimal Buy-in
The best way to gain buy-in to a 5S program is to start with a pilot that actually shows results. Select a small area or a neglected area that can show benefits within one week of implementation. Most companies have a supply room or filing systems that could use a face-lift. It is important to show quick, visual benefits.
Before embarking on an enterprise-wide implementation, develop a full rollout plan and discuss with all parties involved. Once the rollout begins, be sure to collect best practices along the way for future projects.
About the Author: Terra Vanzant-Stern, Ph.D., project management professional, is a Master Black Belt and lead facilitator at SSD Global Inc. She is the chair-elect for the Denver section of the American Society for Quality and also teaches classes in statistical process control and design of experiments. She can be reached at [email protected].