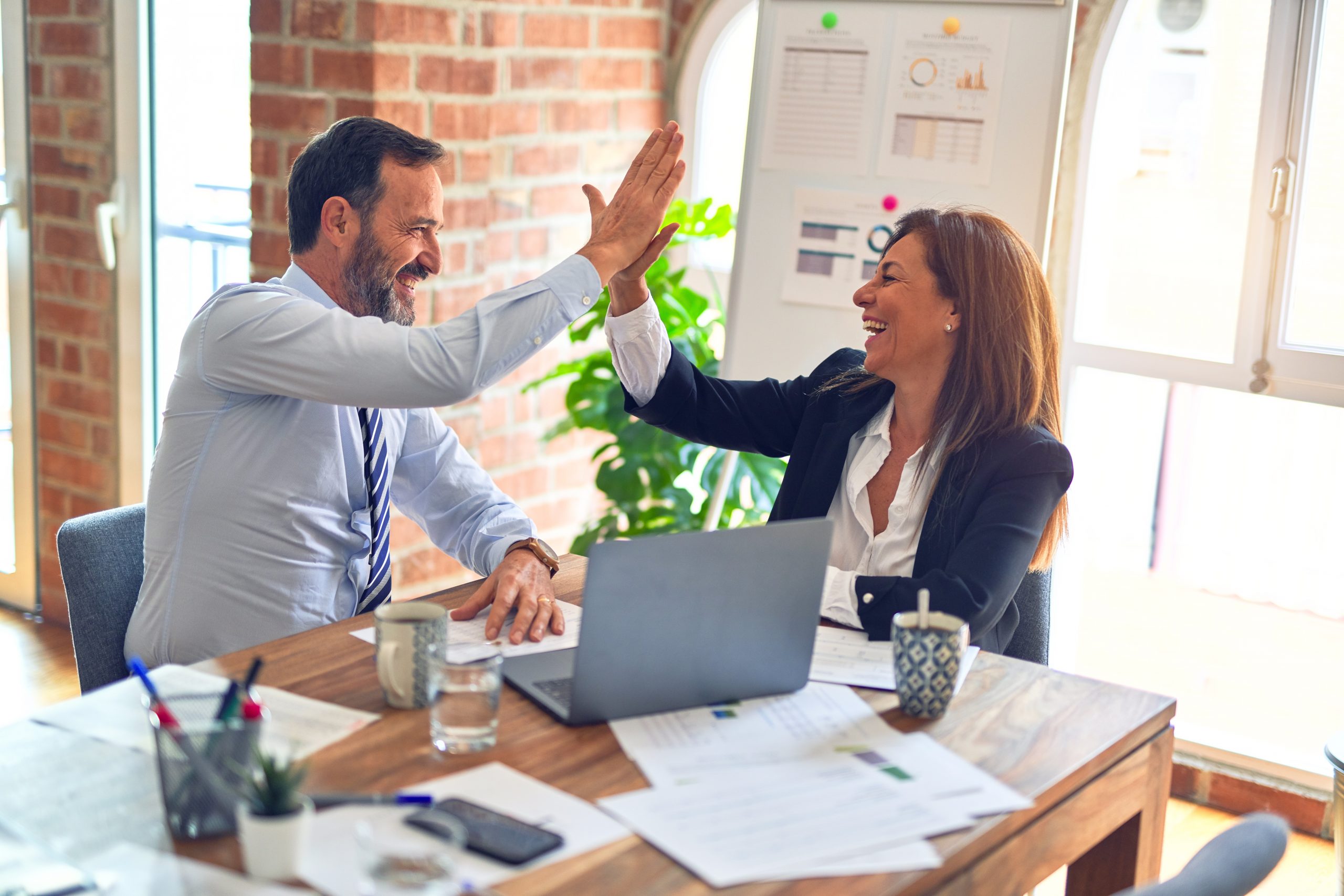
If you travel to multiple sites to support projects as I do, you know what it is like to drive on the highway during rush hour. Last week I was driving to another company site, which is normally about 1.5 hours away if there is no traffic. I was cruising at the speed limit until about 15 miles from the site, where traffic stopped on the highway. Then it moved, and then stopped, and moved again for the next 10 miles. As usual, most cars were moving along with the traffic. A few vehicles were zipping in and out of lanes, cutting in front of others, and trying to get ahead. Nothing uncommon.
As I was driving I thought this was the perfect example to show two critical Lean Six Sigma concepts.
1. Process constraints (or bottlenecks), and their relationship to variation and capacity.
What we often see is: bumper-to-bumper vehicles grinding to a halt in a stretch of the highway, and then for the next mile, the highway seems totally free and every car is accelerating to the top speed. Then they hit another pack of stopping vehicles before accelerating again. Why do we have stop-and-go traffic, instead of a steady flow of slow-moving vehicles?
One reason is the natural variation in how we drive as individuals. Various factors cause us to drive at different speeds, and we respond to each others’ varying speed as well. Both are natural. When the car in front of us slows down, we slow down. If there is no traffic and we keep a good following distance, we don’t necessarily have to respond when the car in front of us slows down. We can simply consume the available capacity (the distance between the cars) until the car in front picks up speed again or until reaching an unsafe following distance. Therefore, variation is not a problem when there is a large excess capacity.
However, during rush hour, the capacity is reaching the limit; the distance between vehicles is at or below a safe distance. Any speed change of a vehicle could trigger the reaction of the following vehicle and creating a cascade of reactions. Only slight overreaction (which is predictably normal) would accumulate the effect quickly. A few cars down the line, the cars would have to slow so much to the point of stopping. This is how the degree of variation and the amount of excess capacity interact to create constraints in a process. The larger the variation or the less the excess capacity, the more likely a process will see bottlenecks.
Surprisingly, many people managing business are unaware of this simple relationship. Having sufficient capacity to meet the average demand is not enough to eliminate bottlenecks as long as there is variation. The best way to reduce excess capacity and bottlenecks is to reduce variation.
2. Lead time, and its relationship to Work-in-Progress (WIP) and throughput.
We all know how to plan a trip and estimate the time of travel. If there is no traffic, we simply divide the total distance by our travel speed. However, when there are traffic jams, how do we estimate our own travel speed that is no longer predictable or controllable? Intuitively, we know that the actual lead time depends on how many cars are in front of us and how quickly those cars exit the highway or pass the bottleneck. If you have heard of Little’s Law, this is exactly the relationship.
Lead Time = Work-in-Progress / Exit Rate
Wait a second, you may say, I can be faster if I cut in front of other cars. Yes, you can. Little’s Law estimates the average lead time. The actual time for individual WIPs can certainly vary. But how do you know you will be faster than the others if they try to do the same thing?
The beauty of Little’s Law is that it tells us the overall outcome, regardless of individual performance. If one car has a shorter time, some others MUST have longer times. Think about it. Given the same number of vehicles on the road and the highway exits have a limited throughput, the average travel time is fixed. One can be faster only at the expense of others. In fact, if we consider the first relationship above, zigzagging in the traffic only creates more variation and therefore more bottlenecks, slowing down the entire flow. We could be faster if no one is trying to get ahead of the others.
Does this sound a bit similar in a work environment? An organization has only limited resources. The same resources are used at 100% capacity, working on multiple projects or tasks (WIPs). By definition, when we are at 100% capacity, the throughput or exit rate is fixed at its maximum. The overall lead time is therefore pre-determined. Yet, individually, a project or task can be completed ahead of schedule. But how? Only at the expense of others. Formally re-allocating resources to prioritized projects by management, or more often, dropping everything else by individual workers, may expedite some work. What about the impact on other work?
If we are managing a business or portfolio of projects sharing the same resources, the overall lead time can only be improved if 1) we reduce the WIPs (# of projects) or 2) we increase the flow rate in a process. The latter can be in the form of bottleneck removal. The next time you want to improve the business’s overall performance in terms of lead time, think about what happens in rush hour traffic. What have people done to reduce the travel time for everyone? Most likely, they have applied these two concepts.
Drawing an analogy from the traffic solutions, you may find a solution for your own process challenges.
[See my previous blogs: Lead Time vs. Cycle Time and Innovation in Pharma for more on Little’s Law, Lead Time, and Capacity.]