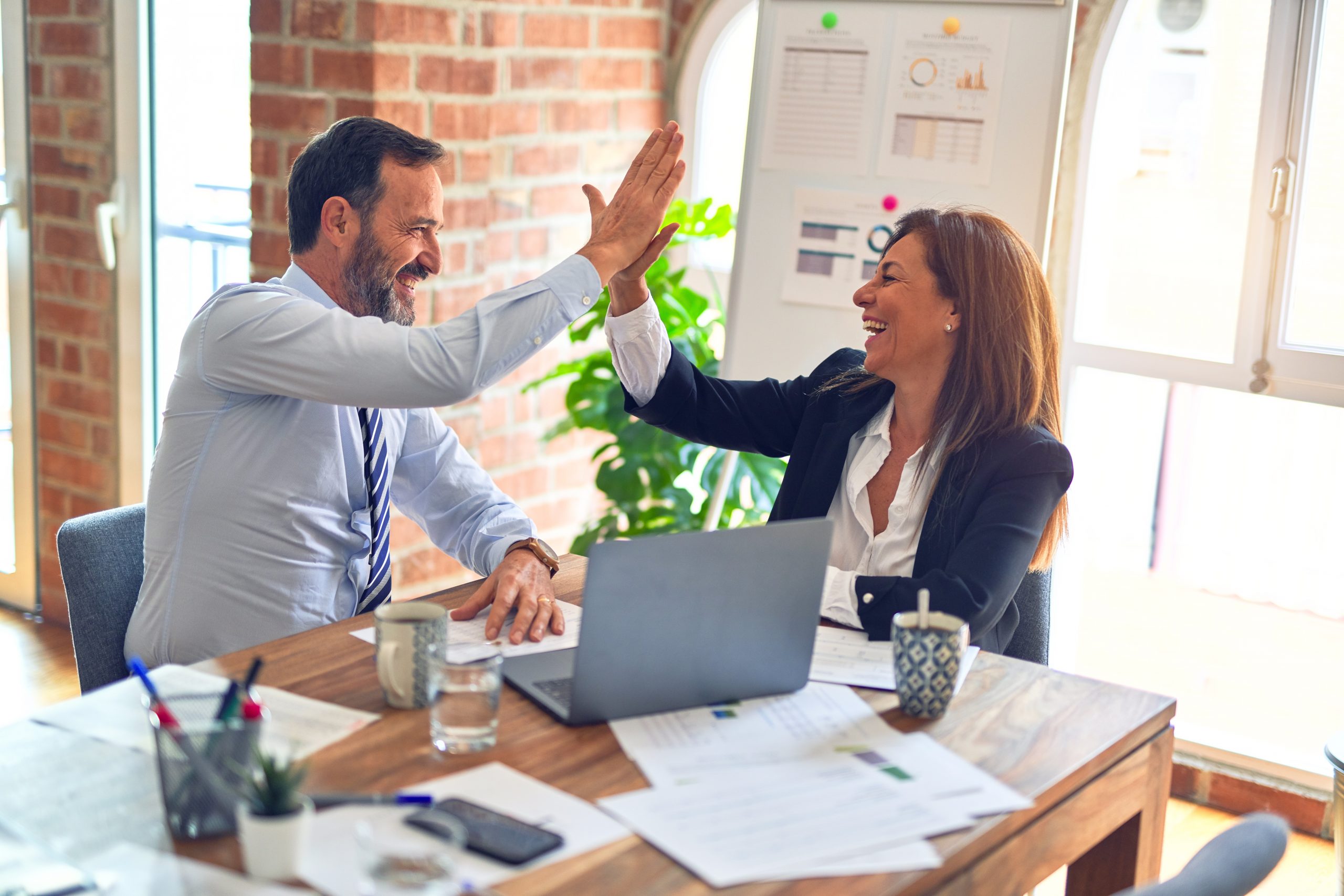
Wark will be presenting on the role of the CSB and the lessons learned from its investigations during a keynote address at iSixSigma’s Energy Forum for Process Excellence on May 17 in Houston. In an interview with iSixSigma Senior Editor Kirsten Terry, Wark offered a preview of some of the topics he will cover during his speech.
Can you share the U.S. Chemical Safety Board’s mission, and how it pertains to the Energy sector in particular?
I’d like to start by emphasizing that the CSB is a tiny little Federal agency with a huge mission that has not only national but international impact. Right now we have 18 open investigations – I’ll be covering those briefly as part of the presentation.
The CSB is an independent, US Federal agency charged with investigating chemical accidents and promoting prevention and public knowledge. We were authorized by Congress in 1990, which was a reauthorization of the Clean Air Act, but we actually weren’t funded until 1998. So we’ve only been around about 12 or 13 years. We’re modeled after the National Transportation Safety Board [NTSB]. A lot of our missions and functions are very similar to the NTSB, only they handle transportation accidents and we concentrate on accidents in the chemical and petro-chemical industry – which keeps us plenty busy.
On the board, we have five members, presidentially appointed and confirmed by the US Senate. I’m one of the five – I’m a Bush appointee and we have two other Bush appointees, and two members who were appointed by President Obama, one of whom also serves as the chairman and CEO. We have a professional investigation staff of roughly 42 to 43 people – not just the investigation staff, but the agency overall is only about 43 people. We’re located here in Washington, and also in a Western Regional Office, as we call it, in Denver, Colorado. We have about 12 people out there.
Our congressional authority specifically is to independently investigate accidents. I would like to emphasize that – we are an independent agency. We do our own investigations, and rely very little on any information we get from other agencies’ investigations, such as OSHA or Alcohol, Tobacco and Firearms, and so forth. In addition, we are not an enforcement agency, and we do not assess fines or penalties. That’s something we always like to emphasize because we’re actually all about prevention. We want to investigate an accident, determine the root causes, and make recommendations to any number of organizations or entities, such as OSHA, EPA, Congress, the State, standards-setting organizations, and industry and trade organizations, to name a few.
Since we are a tiny little agency, we’re very resource restrained. Our budget is only in the $10 to 12 million range. That’s miniscule compared to a lot of other government agencies. We do have investigation criteria that we use, with a weighted average process, to determine which investigations we go out on. Of the 10 weighted factors, of course death or injury and health effects is number one. If there’s an incident that requires an evacuation of a local community, then we weigh that very heavily too. Then it goes down the list: property losses, ecosystem damage, potential for actual consequences, lessons learned – that’s a biggie – and public stakeholder concerns and company history are the other factors in whether or not we deploy to an accident.
How can our attendees and their companies benefit from this analysis conducted by the CSB?
As I mentioned, we’re all about prevention. We like to promote awareness through any number of means. We do feel that information is essential for safety – the business we’re in. We make regular public statements. Also, the board members, as I’ll be doing on the 17th, present at conferences and other venues across the country. We also do press conferences and public meetings, often associated with wrapping up and releasing a report on our findings. That also gives the families who attend these meetings, if there’s been injury or death, some closure as to what we found and what would be of interest to them.
We also do reports, digests, safety bulletins, and – the thing I can’t emphasize enough – is our video program. The videos – we get requests for them from all over the world. They’re available on our website, which is www.csb.gov. They’re bestsellers, and one of the reasons they’re bestsellers is because they’re free. They constitute a significant part of our budget, but we feel it’s well worthwhile. You can either order them as hard copies – we have two DVDs that encompass most of our completed investigations – or they can also be downloaded directly from our website. We find these DVDs to be extremely important. We get a lot of very positive feedback [from people who use them in] safety training, which goes on throughout the industry – for instance, during brown-bag safety lunches. Safety professionals love them, immensely.
What lessons can process improvement professionals take away from large accidents like the BP Texas City Refinery explosion in 2005 or the Deepwater Horizon oil spill in the Gulf last year?
In my presentation, I’ll be covering the keys to what we feel is a successful chemical or other process safety program. Right at the top of the list, and something that we found out from several years of experience here investigating some very significant accidents, is the importance of senior management knowledge and commitment to a good safety program. We’ve found that senior management needs to commit to eliminating defects as best they can in their processes to have a safe operating environment.
Also, process safety knowledge and process hazard analysis [are key]. And something that sounds like a no brainer, but we’re finding that it’s important: to hire and train the right people. In a lot of cases that doesn’t happen, we’re finding, and it usually ends up in some type of untoward incident, sometimes tragic in nature. We also find that a pre-start-up safety review and mechanical integrity are big issues, and the proper maintenance of equipment. When we go to an accident scene, we sometimes find that maintenance requests have been unfulfilled. Or there’s poor or no maintenance of safety systems.
Another one is management of change – I’ll be talking about how important that is when you change either equipment systems or people, including going right up to the top of the facility, like a site director and not changing them out as often as we found is happening in some cases. [With this frequent turnover], sometimes there’s no continuity or institutional knowledge or real awareness or commitment to safety. Incident investigation by the facilities themselves and making sure they take proper corrective action is important as well.
I’ll also be covering something that I am particularly interested in. I think one of the reasons I was appointed to the board is because I came out of the emergency management community. Emergency planning and response is a big issue. This means making sure there’s good on-site/off-site planning between the utilities, the facilities, and the local community, especially if they’re handling dangerous materials that could cause fires or explosions with off-site consequences. An important part of that also is community outreach – making sure that if you’re operating in or near a community that you make sure you’re reaching out to them and that you’re doing everything to make sure that they are aware of any possible hazards and what to do in the event of an emergency.
I’m going to cover in some detail that we’re finding that CSB investigations reveal gaps in industry with respect to audits, where they look at accidents or near misses and a lot of times there’s little follow up. Or, if they do an audit, it’s just a lick and a promise, not much in depth as far as recognized hazards are concerned. Consequently, a lot of our investigations show that they don’t recognize a path to a pending disaster or change anything to prevent it. I’ll be giving some examples of that in my presentation.
Also, we find gaps in training, where there’s little formal structure or documented training. And when there is training, it’s not consistently reinforced like it should be. There’s little training in management of abnormal situations. In other words, if they have what we call an excursion, where the controls are showing that they’re having a huge increase in temperatures and pressures, what to do about that.
Another one I’ll be covering: We’re finding that in a lot of cases there aren’t any written procedures, or they’re ad hoc. In some cases they’re only anecdotal, with older workers passing them on to younger workers. They’re often irrelevant, outdated, unusual and unused written procedures. A lot of times the procedures are not enforced or they’re just not followed. There are shortcuts being taken.
We’re not really focused on ‘slips, trips and falls,’ as we call them. We’re interested in process safety and the high-consequence, low-occurrence type of accidents that gain national interest and certainly provide lessons learned for all of industry.