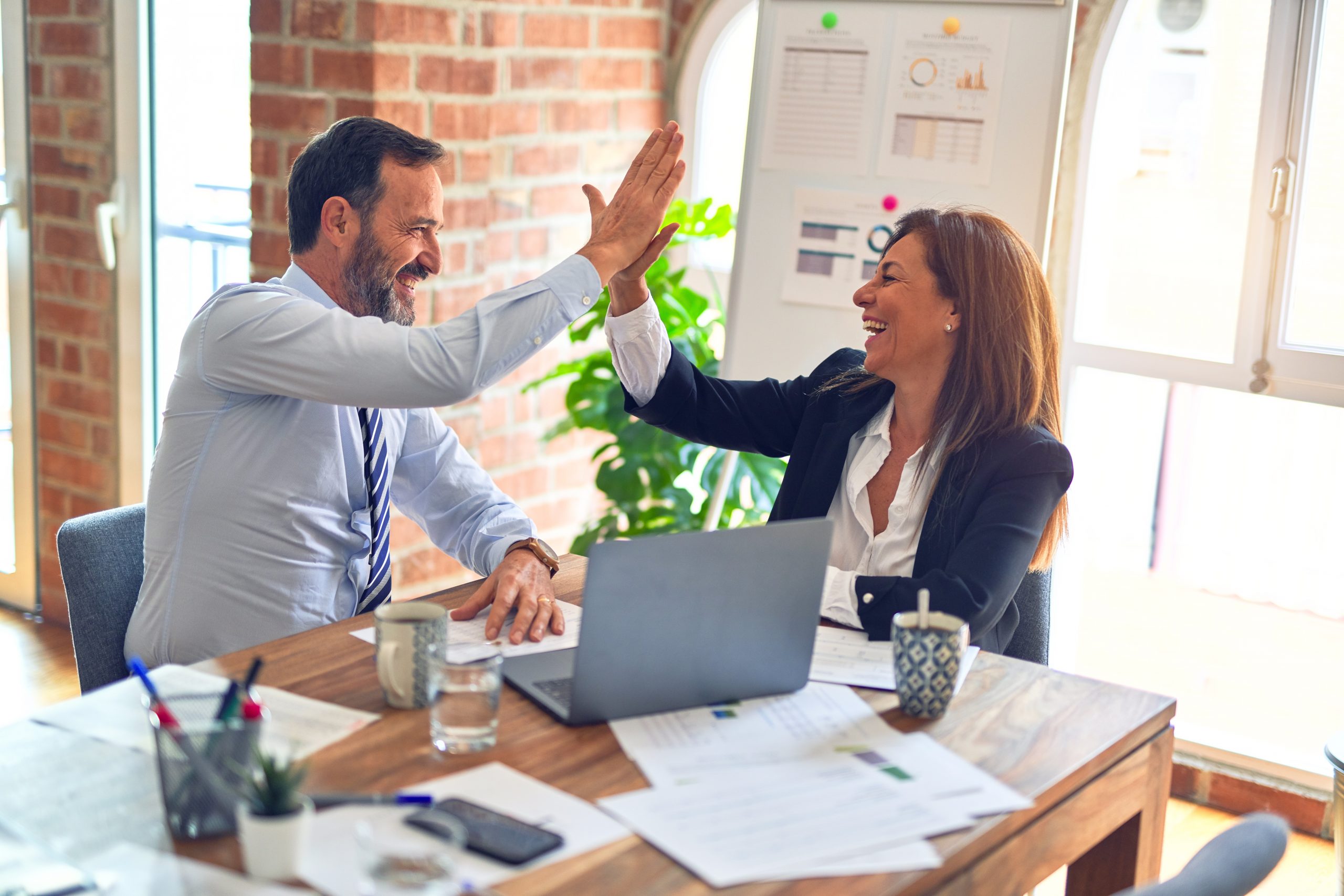
In my blog about a year ago, “How I became a Black Belt“, I wrote about Lean Six Sigma being “simply a scientific approach to problem solving and learning.” I am sure everyone understands LSS as a problem-solving methodology. But how does Lean Six Sigma help us learn?
First, let’s look at some common barriers to learning effectively. A good example is a recent Harvard Business Review article, “Why Leaders Don’t Learn from Success.” Starting with an interesting case study of the Ducati Corse motorcycle racing team, the authors argue that success can breed failure by hindering learning, and present steps to overcome three impediments to learning:
1. Fundamental attribution errors
“In business, likewise, any number of factors may lead to success, independent of the quality of a product or management’s decisions. Yet it is all too common for executives to attribute the success of their organizations to their own insights and managerial skills and ignore or downplay random events or external factors outside their control.”
2. Overconfidence bias
“Overconfidence inspired by past successes can infect whole organizations, causing them to dismiss new innovations, dips in customer satisfaction, and increases in quality problems, and to make overly risky moves.”
3. Failure-to-ask-why syndrome
“When you’re confronted with failure, it’s natural to ask why disaster struck. Unfortunately, success does not trigger such soul-searching. Success is commonly interpreted as evidence not only that your existing strategy and practices work but also that you have all the knowledge and information you need.”
The authors offer “a better model for learning, one in which failure and success are on equal footing and both trigger further investigation that helps us revise our assumptions, models, and theories.” Their model provides an excellent framework for improving organizational learning and is consistent with the Lean Six Sigma practice of PDCA. The authors even go as far as saying “Tools like Six Sigma and total quality management have taught us to dig into root causes of problems. Why not use the same approach to understand the root causes of success? ” I totally concur.
In addition, Lean Six Sigma gives us practical concepts and tools to address the impediments. For example,
• Cause-effect analysis helps identify all contributing factors before attributing the results to our favorite factors.
• Statistical Process Control helps separate special causes from common causes before reacting to an observed change in the outcome.
• Hypothesis testing and Design of Experiments demand explicit Y=f(x) relationships to test our knowledge and assumptions.
The value of the last example is often overlooked. Although we commonly use root cause analysis (such as Fishbone diagram and 5 Why’s) to explore what went wrong (or the failure), no test of Y=f(x), such as using correlation or regression, can be performed with data of only a single outcome (be it a success or failure). We have to have Y data for both success and failure to understand whether/how changes in x’s can lead to success or failure.
Therefore, anyone with a Lean Six Sigma mindset would never conclude a causal relationship using only experience in success or failure. Instead, they would always ask “Would the same underlying factors give the opposite result?”
We learn by asking the right questions, regardless of success or failure.