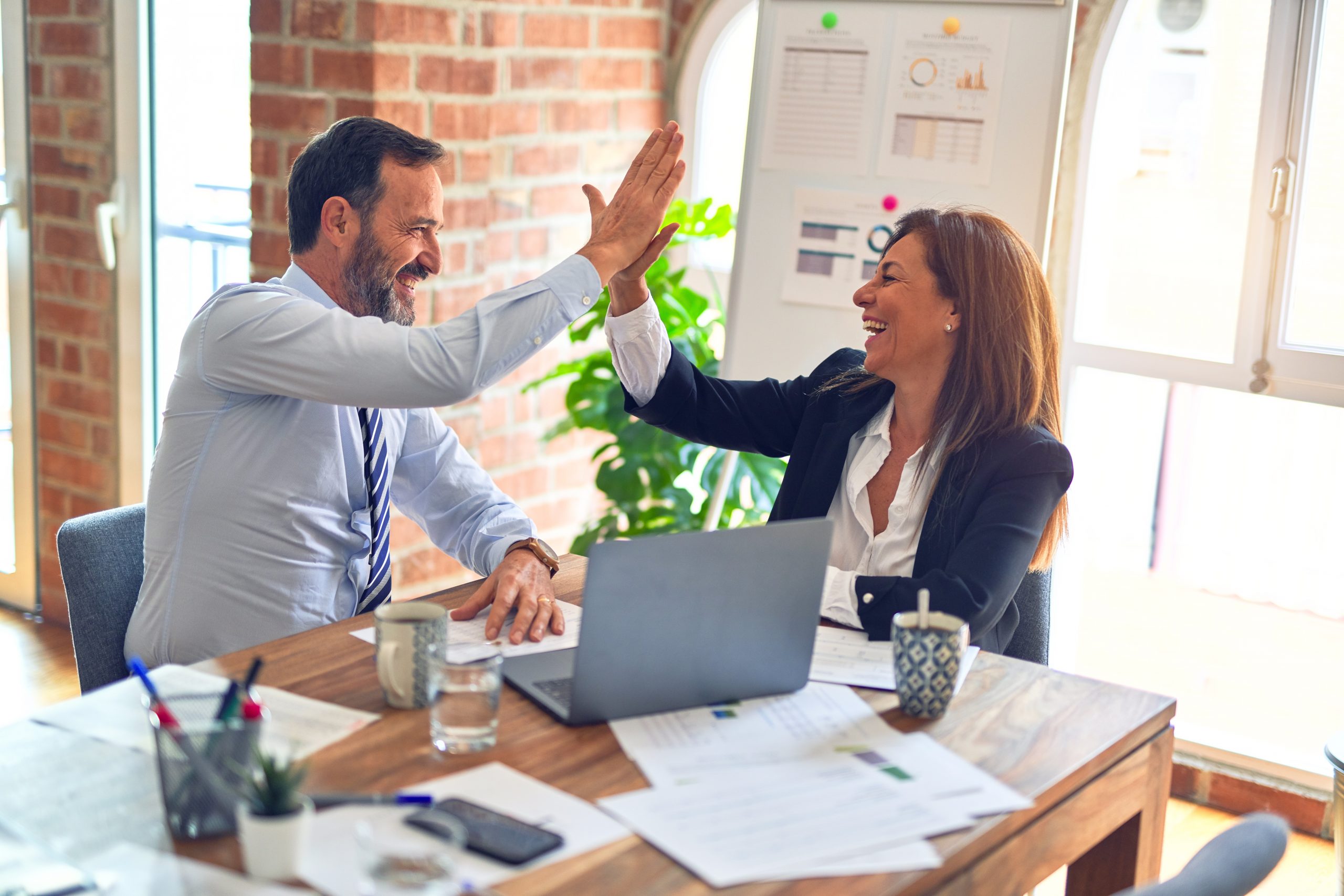
In a business process improvement project, a critical factor is documenting the standard work or the “least waste way.” One of the issues I have been dealing with recently is ensuring that documentation is in place and up to date. Unfortunately as the saying goes, “the only constant is change…” and as outside factors change (notably customer requirements), the “least waste way” changes as well.
A particular example I experienced recently was when one of our major customers changed to a new part revision number. This change caused one of our core manufacturing processes to change – slightly – but very critically to customer quality. The change was unplanned and pushed onto us very quickly. Our engineer and one of our manufacturing techs were more than able to quickly accommodate, but in the heat of the moment, documentation steps were skipped. One week later the engineer who received and translated the customer request to our manufacturing processes has left the company.
In the chance that our manufacturing tech originally tasked with the change calls out sick, goes on vacation, or just plain forgets, we will be forced into an expensive manufacturing line stop, and an embarrassing call to our customer for help on rehashing the revision change.
As the continuous improvement specialist in the department I am tasked with creating a way to ensure that the documentation steps are never skipped. We have a full centralized documentation system (WebDocz) in place, and virtually all employees are knowledgeable and empowered in the system. What methods are being used to ensure documentation without giving up or impeding customer needs/requests?