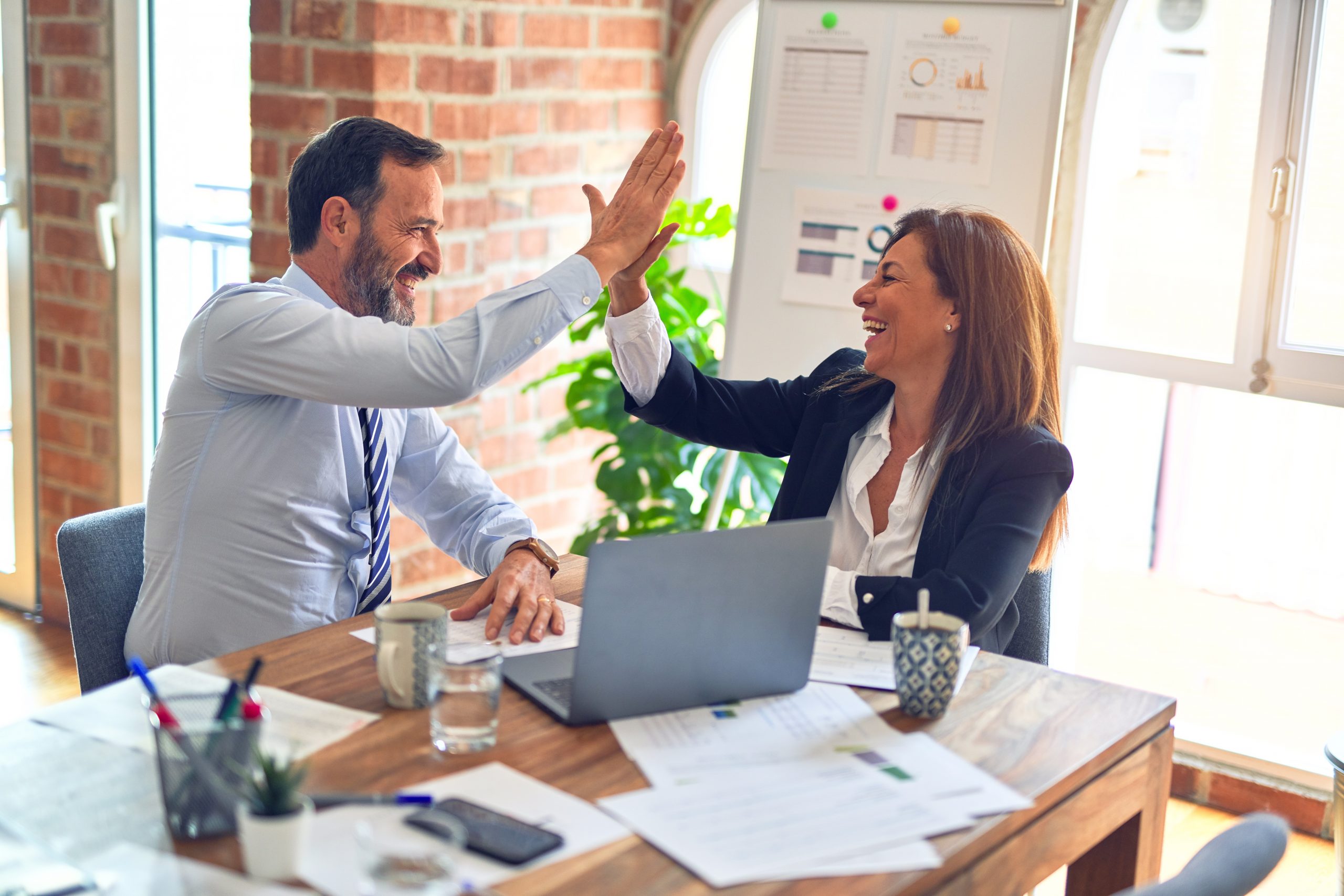
Next up is Stephen Turnipseed, Lean Six Sigma Advisor for Chevron Global Upstream. I’ve heard Stephen speak before. He is a great speaker.
Chevron does not have the luxury of a CEO driven deployment. They started Six Sigma as a grassroots deployment, and it has been expanding. Now it’s moving into supply chain.
Steve is going to contrast a grassroots deployment to a traditional top-down deployment. This will be interesting.
Assumption with a grassroots deployment:
- Employee driven initiatives will have more buy-in
- Early success will create pull
- Other parts of the company will try to emulate
- It will expand as champions move around. (this is the only true assumption)
The reality of a grassroots deployment: no career path, no recognition, no accountability, limited support, little buy-in, no time given to work projects, large degree of variability, slow maturation and financial benefit.
Critical success factors for grassroots deployments:
- A tolerant company culture
- Inspired individual –ability to influence, stake career on their belief, and able to carve out a position that allows her/him to continue the cause for the long term.
- Able to get funding for training and coaching
- Program achieves enough success to sustain itself
- Develop other inspired individuals and convert leaders
Stephen goes on to talk about how to roll out Continuous Improvement in the supply chain. And Chevron engaged their customers and suppliers to join them in Six Sigma training.