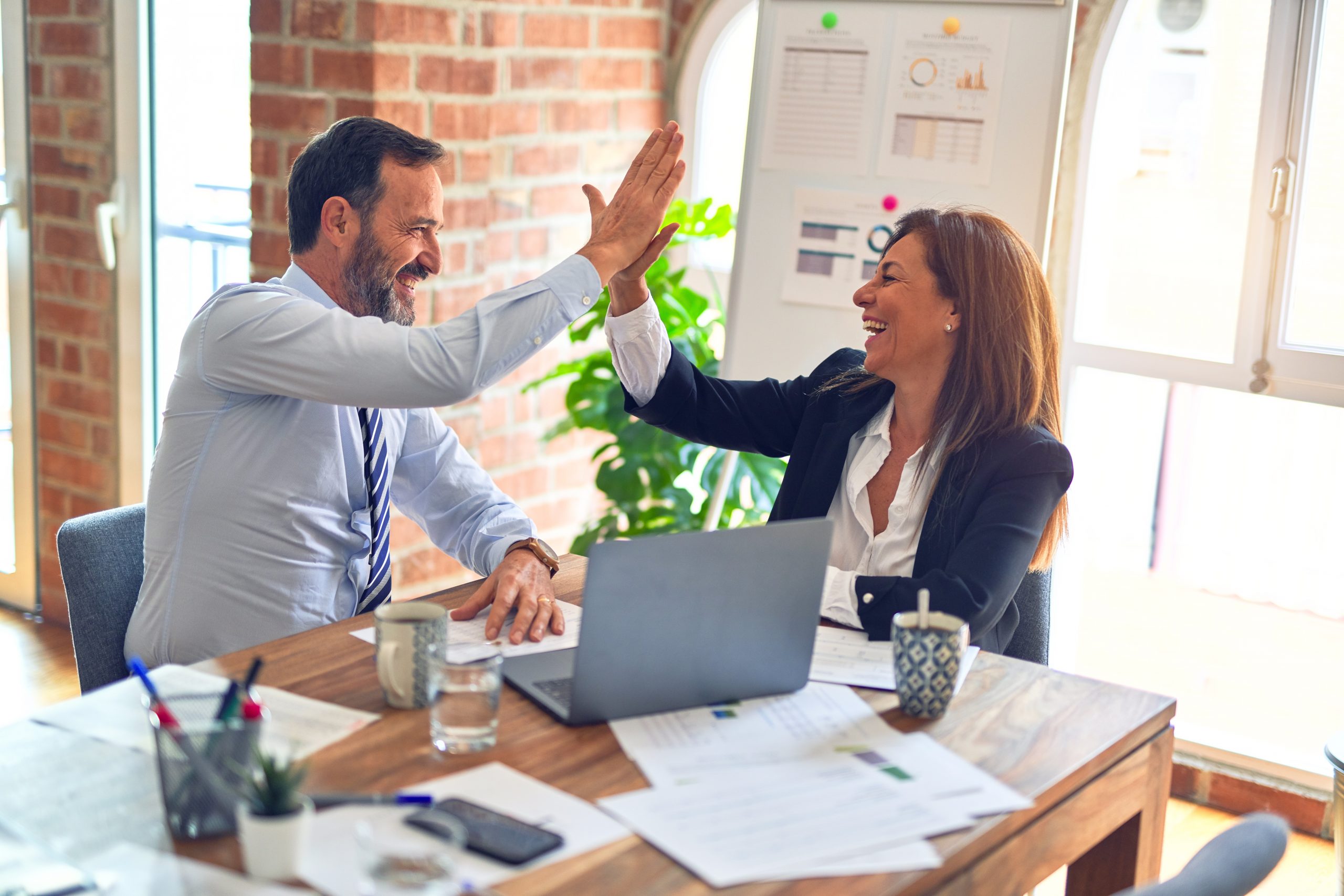
To better acquaint their employees with Six Sigma, the Y-12 National Security Complex published the following story in their January 2002 employee newsletter.
Bechtel Shares a Six Sigma Parable
You may have heard about the most recent process improvement initiative, Six Sigma, which is taking off like wild fire around America. Corporate giants like Motorola, General Electric, Allied Signal and Bechtel are embracing this new approach to work process improvements with enthusiasm and the results have been staggering.
Not to be outdone by the lower 48 states, Santa Claus has rolled out his own Six Sigma deployment to help satisfy the global demands of his customers. Kids throughout the world expect their gifts to arrive no later than 6 a.m. Christmas morning so that playtime can be maximized with the newly acquired toys. In recent years, Santa has been hard pressed to deliver the ‘goods’ by 6 a.m., December 25. But 2001 was different.
Early in June, Santa Claus assigned his Yellow Belt elves to map their own work processes and measure key cycle times, durations, and rejection rates. With his Champion, Mrs. Claus, Santa developed a high-level flow chart to illustrate all the key functions necessary to satisfy his young customers. With the data collected and summarized in a Pareto chart, Santa determined that the most critical and time consuming work activity is finding the correct gift stored in his sled for kids like Johnny in Portland and Jane in Seattle. The data indicated that 80 percent of Santa’s work time was spent rummaging around in his sled for the right gift during his delivery run on Christmas Eve.
Furthermore, incorrect gift delivery of more than 33 percent has led to many very unhappy customers in years past. Santa quickly assigned his resident Black Belt elf to work on the Process Improvement Project (PIP) that would improve the toy delivery system to ensure timely and accurate delivery.
By September, the Black Belt, working with the Yellow Belt process owner and other subject matter experts, had further reviewed the work process.
Additional data was then collected, and the Black Belt applied statistical hypothesis testing to confirm the suspicion that toy positioning in Santa’s sled did indeed affect Santa’s ability to efficiently deliver the right toy to the children of the world. The PIP team quickly developed an Improve Plan, requiring that a sequential delivery listing be developed prior to packing Santa’s sled. With this list in hand, the elves were then instructed to reverse-pack the sled in the order of delivery.
Furthermore, each gift was labeled with the name and location of the child. The Yellow Belt then implemented the approved Control Plan to periodically check the sled’s packing sequence and confirm that all packages were properly labeled.
Santa declared victory on Christmas Day, when all the children of the world had the correct gifts in time for their early wake-up schedules.