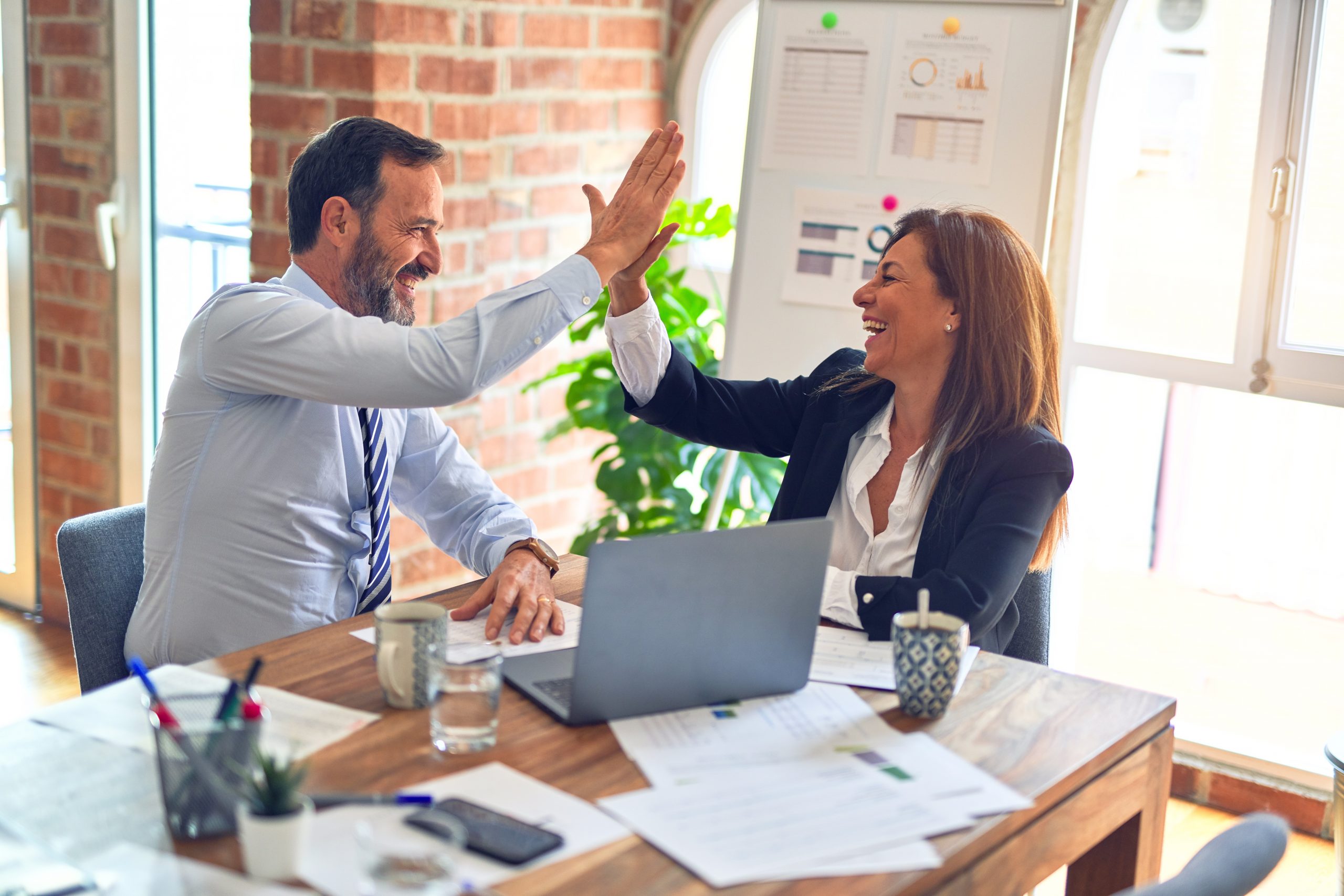
Over the years, I’ve come in contact with several different companies that say that they are “lean”. Yes, TPS (the Toyota Production System) is a great framework for production, with its teachings of one-piece flow, kanban, etc…but what about the actual implementation of the lean concepts at other companies besides Toyota?
I’ve seen desks with outlines of where the stapler and the computer monitor should go, yet with no sense of continuous improvement in the culture. I’ve also seen kanban implemented with min and max levels clearly marked, yet with no safety stock even left due to variation in production downtime. On the other hand, I have seen a really good “lean” production system operating every day as well, but that has been the exception.
What’s up here? It seems like that it is almost impossible to get to real ’lean’ operations unless you actually start up with a lean philosophy.
So here’s a burning question–
Overall, is “lean” a concept that is being actively implemented with success at “mass production”, or is it something that is being attempted by doing all of the easy things first while putting off the hard stuff?
As always, your input is always appreciated!