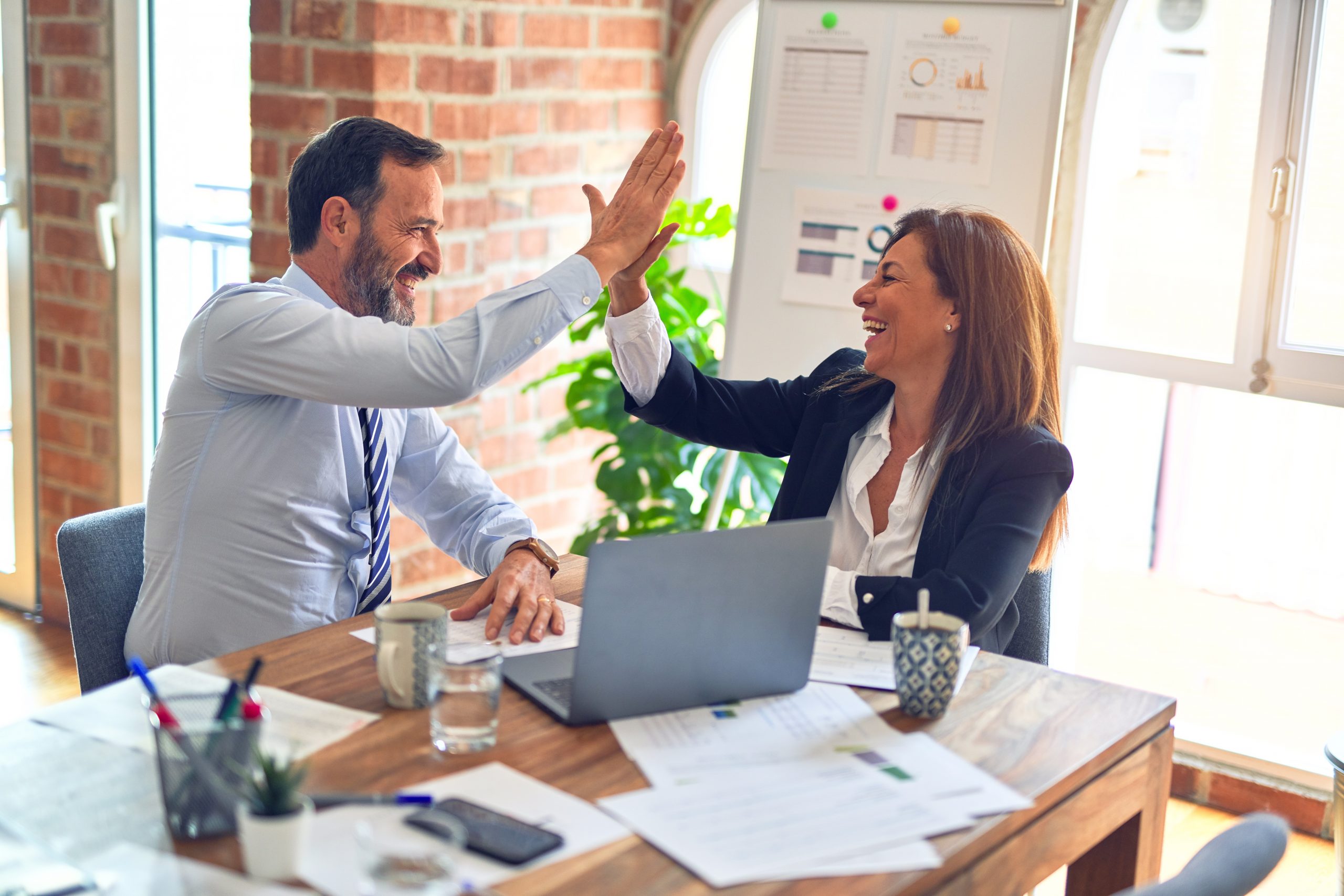
One of the things that I see as a challenge to companies that grapple with a Six Sigma implementation is effective use of tools in “live” situations. By “live”, I mean in a normal operations context, not in a project context. When looking at the use of Six Sigma tools, using them in a project mode in my opinion is an easier affair. A project leader can plan in a project context which tools to use, based on the DMAIC project model.
But what about “live” application of tools? For example, why can’t DOE used to diagnose problems on the factory floor outside of the DMAIC formal context?
Consider this:
A product is defective, and it is composed of 4 parts. Run a four-factor DOE with the factors being part presence (yes/no) and find the potential contributor(s) and contributing interactions. This will at least give you an idea if the component part inputs are influencing the defective condition, and will get you at least half way to problem resolution.
Most of the time in the case above I’ve seen engineers “measure their way” into a guess of a root cause to the problem, which can be inefficient to say the least.
My opinion is that the real power of Six Sigma comes once culture change sets in and real problem solving occurs as part of the business, and NOT in the form of Six Sigma projects only. It seems like common sense to me that advanced tools would be used anyway to solve problems, but in most of the different companies I’ve been involved with, I can honestly say that I have not seen much use of the statistical tools in “mainstream” use.
What restrains companies from using Six Sigma tools beyond the DMAIC project scope?