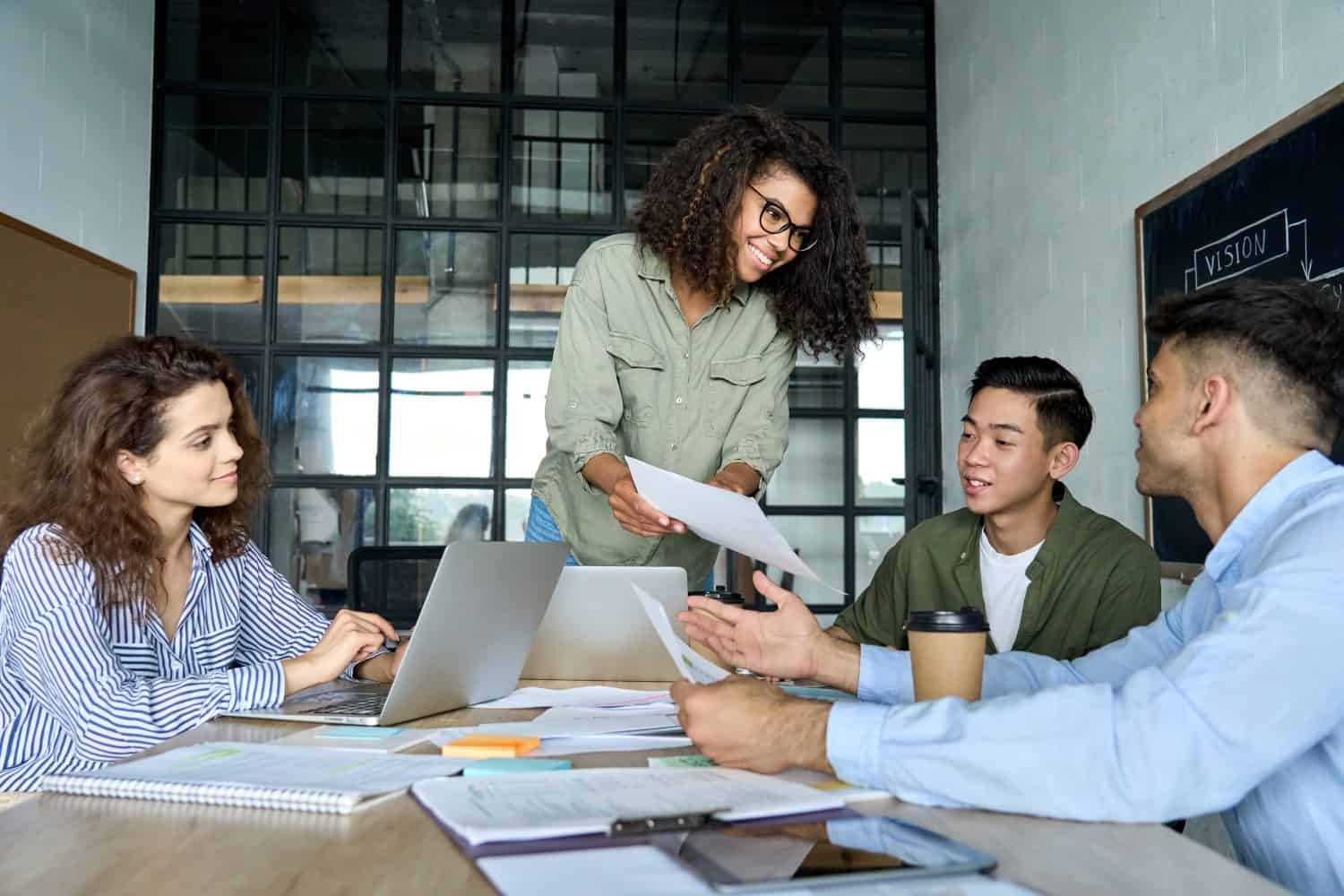
© Ground Picture/Shutterstock.com
Key Points
- The principles of TQM are vital to the success of the approach’s adoption by any organization.
- TQM places a heavy emphasis on a culture of quality rather than one-off projects.
- Successful deployment of these principles is a sure-fire way of improving morale across the entire organization.
What are the 8 principles of TQM? TQM or Total Quality Management is a great way of driving continuous quality within an organization. It isn’t intended solely for products but can transform a business when properly implemented. However, that is only part of the equation when considering the move to this approach.
Adhering closely to the 8 principles of TQM is where you’ll see the greatest successes for your efforts. If you’re new to the concept, that’s alright. That’s what we’re here for. As such, let’s take a closer look at the principles, define them, and explain how to make the most of your TQM efforts for your business.
What Is Total Quality Management?

©Ground Picture/Shutterstock.com
TQM is a systematic approach to quality that dates back to the 1980s. The core conceit behind the approach is standardization, something that those in the tech industry are likely familiar with. As you take on your improvement cycles, there’s room for standardization, which helps to make processes efficient and predictable.
Total Quality Management differs from approaches we’ve covered in the past, like Lean, Six Sigma, and Agile, due to its comprehensive take on an organization. One team isn’t performing TQM; rather, the entire company is doing so.
This does have net benefits, as you’ve got the means of focusing on long-term quality and success. However, there is room for stumbling across the finish line if you’re not adhering to the core tenets of TQM. The 8 principles of TQM aren’t so much suggestions but rather hard requirements when it comes to the successful implementation of the approach.
Why Organizations Are Using It
Standardizing your processes and focusing on quality seems like a no brainer for many businesses. However, that isn’t the whole picture when considering TQM. What has made TQM such an advantageous approach to deploy is that serves as a framework for the whole organization. Additionally, you’ve got other benefits to consider.
Depending on your market, you’ve got a far stronger competitive position compared to your contemporaries. Additionally, TQM serves a great means of keeping your organization nimble and quick to adapt to the changing needs of your customer base.
Employee morale and shareholder satisfaction increase with the successful deployment of TQM, thanks in part to its focus on people at all stages of production. Further, the most important thing is that your organization is fully in the loop when it comes to understanding the output of your organization. We can see the influence of TQM in other methodologies like Lean and Six Sigma, which are in no small part inspired by some of the principles of the approach.
The 8 Principles of TQM
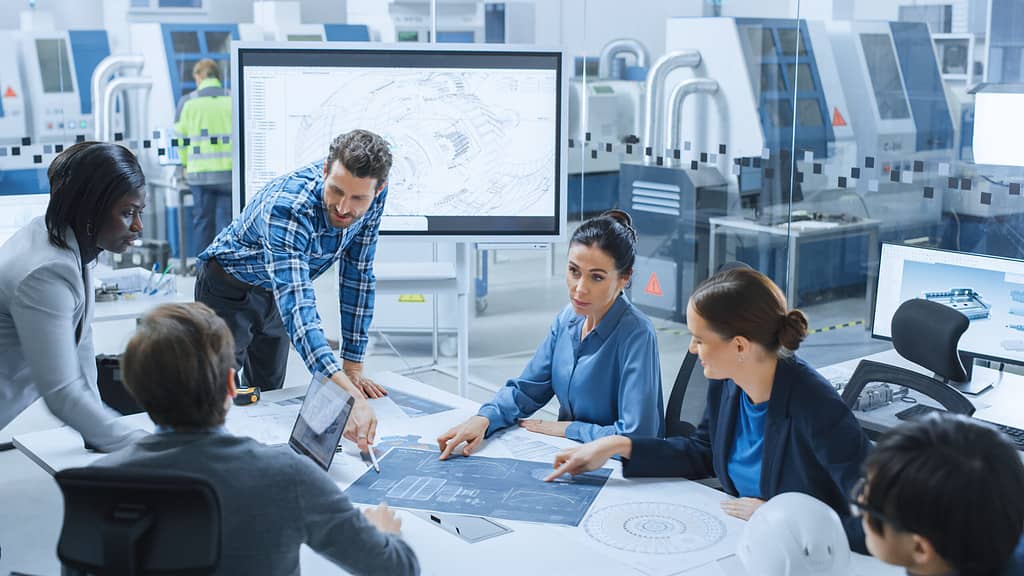
Now that we’ve taken a deeper look at the why behind TQM, I think it’s time to dive a little further into how the approach works. It is one thing to merely provide rote information. However, these principles are going to be core to the daily operations of any organization.
As I previously stated, TQM isn’t done by a single team in your business. Rather, it is the new guiding force behind your entire organization. While this can seem daunting at first glance, close adherence to the principles of TQM will help you achieve lasting success.
You’ll likely understand the why behind this as well. These principles aren’t nebulous concepts by any means. Instead, they are concrete and proven methods of improving your processes, the quality of your outputs, and the overall quality of your organization. Doesn’t get much better than that, does it?
Customer Focus
It isn’t enough to meet the requirements of your customers. Instead, what drives this principle of TQM is meeting and exceeding the parameters for success. This is done in a few different ways, depending on how your organization is structured. Market research and communication can aid in the development of satisfying customer needs.
However, you’ll find success conducting research into your competitors’ products as well. Nothing in a business exists in a vacuum, so looking at what works and where to improve your outputs is going to go a long way toward developing a lasting and successful relationship with your customers.
Consider the principles of TQM employed by an organization like Apple. Sure, they’ve had their ups and downs, but they’ve created an effective ecosystem that meets the vast majority of their customers’ needs. Painstaking hours of research and testing have created a user experience that is immediately grasped but deep enough for power users to leverage for their work.
Leadership
As we’ve discussed in other articles, most monumental changes in an organization take place from the top down. With this in mind, it only makes sense that the successful adoption of the principles of TQM are going to come about through the successful involvement of leadership and management. It is one thing to say that you’re committing to an approach.
However, when the rubber meets the road, leadership would do well to embody and champion the principles behind the approach. This keeps employees motivated, and it keeps everyone in the organization on the same page.
Other ways management can successfully embody the principles of TQM can come about through standard practices. Recognizing successes, giving frank feedback, and leaving the lanes of communication open for your employees is just how companies successfully implement TQM. Further, it helps to keep the focus on quality and improvement above all else.
Employee Engagement
Leadership isn’t what builds the products, although they are expected to have an active role in production. Your rank-and-file employees have to be fully on board with the principles of TQM to make the most of its deployment. This can come about through a few different methods, as you might expect.
I mentioned recognition in my point about leadership, but allowing the lanes of communication should point in both directions. Getting feedback from subordinates might seem unorthodox, but it has proven successful. Additionally, you’ll want to lay down clear goals. Projects can often bury the lede when it comes to pointing out the finish line.
Another solid way of embodying the TQM way of doing things is to place realistic expectations on your staff. You’ve got the hard data at the ready, you can easily see who performs best in what capacity. Additionally, take some time to celebrate your employees’ successes. Their victories are your victories, and that’s cause enough to roll out some incentives and rewards.
Process Approach

As you might guess, processes get some focus as well. When looking at the principles of TQM, people play a vital role. However, processes are how the work gets done. Approaching your processes isn’t done solely by improving them. You’ll be identifying them, documenting them, and taking a closer look at what those processes interact with.
TQM isn’t done with just the improvement of a process. Rather, you’re comprehensively and exhaustively analyzing your processes and taking action to make the most of them. Continuous monitoring and regular audits of your processes are a great way of making sure the improvements made are sticking.
Additionally, comprehensive documentation is an effective means of maintaining your processes. Your team might not always be in charge of the same processes, and whoever takes up the mantle needs some idea of what has been done to change these processes over time.
Comprehensive Improvement
Improvement is one of the core tenets behind TQM. As such, it only stands to reason that you’ll be doing more than just improving your processes. Improvement takes many forms, whether it’s through continued training, development of the systems behind the work itself, and so forth.
This is one of the principles of TQM that is heavily reliant on the people factor to make the most of it. After all, if your team and leadership aren’t on the same page, then how can you enact lasting improvements that will endure over the long term?
Improvement isn’t just one of the principles of TQM, but it is essentially the bedrock behind the entire methodology. It makes sense, quality is a driving force behind the modern business. Taking the time to analyze, document, and ultimately create solutions across the board is going to guarantee your business’s success for years to come.
Evidence-Backed Decision-Making
Evidence can be readily substituted with data. However, the concept behind this principle of TQM is making decisions not based upon instinct or feeling, but with hard numbers behind it. This is something we see time and time again in something like Six Sigma. Data plays an integral role in the success of any organization, and understanding and leveraging that information is the key to continual quality.
You can see where things aren’t working, employees ill-suited for roles, and customer feedback among other hard data points. Any business is going to generate a ton of data, especially as you conduct things like surveys. However, this is where you can put that quest for quality to the test and make good decisions with a solid backing.
Not every decision is going to be a winner; that’s just part of the game. That said, you’ll find that making decisions with evidence backing you up is going to do quite a bit for the overall quality of your organization and the overall satisfaction of your customers.
Management of Relationships
No man is an island, and the same applies to businesses. Unless you’re actively developing your raw materials, you’ve got suppliers, contractors, and so forth. This is one of the core principles of TQM, and it makes a massive difference when it comes to your quality outputs.
Long-term partnerships and open communication can be effective starting points for managing your relationship with your suppliers. Further, don’t be afraid to give honest feedback. A lasting relationship isn’t built upon negligence, but rather building trust through honesty.
Holistic System Approach
The final principle of TQM is key to the underpinnings of the entire approach. When I said the approach itself was systematic, this is exactly what I meant. Taking a holistic system approach means you’re taking a closer look at the key processes in your organization, defining good metrics, and far more.
This is where you start to develop standard operational procedures, provide the skills and training necessary to get processes running, and ultimately take the time to regularly assess the performance of your team.
Other Useful Tools and Concepts
Still raring for more? Well, we’ve got you covered, at any rate. You might want to take a closer look at the common pitfalls in adopting Scrum. Scrum remains a popular approach to the Agile project management methodology, but it isn’t always a painless thing to deploy.
Additionally, you might do well to take a closer look at Scrum vs. Kanban. These are two extremely popular approaches to Agile, and knowing which works best for your organization might determine the success of your next project.
Conclusion
The principles of TQM are vital to its overall success. This isn’t something like other project management frameworks where you can take pieces to create a working hybrid. Rather, it requires commitment, perseverance, and getting everyone on board.
The image featured at the top of this post is ©Ground Picture/Shutterstock.com.