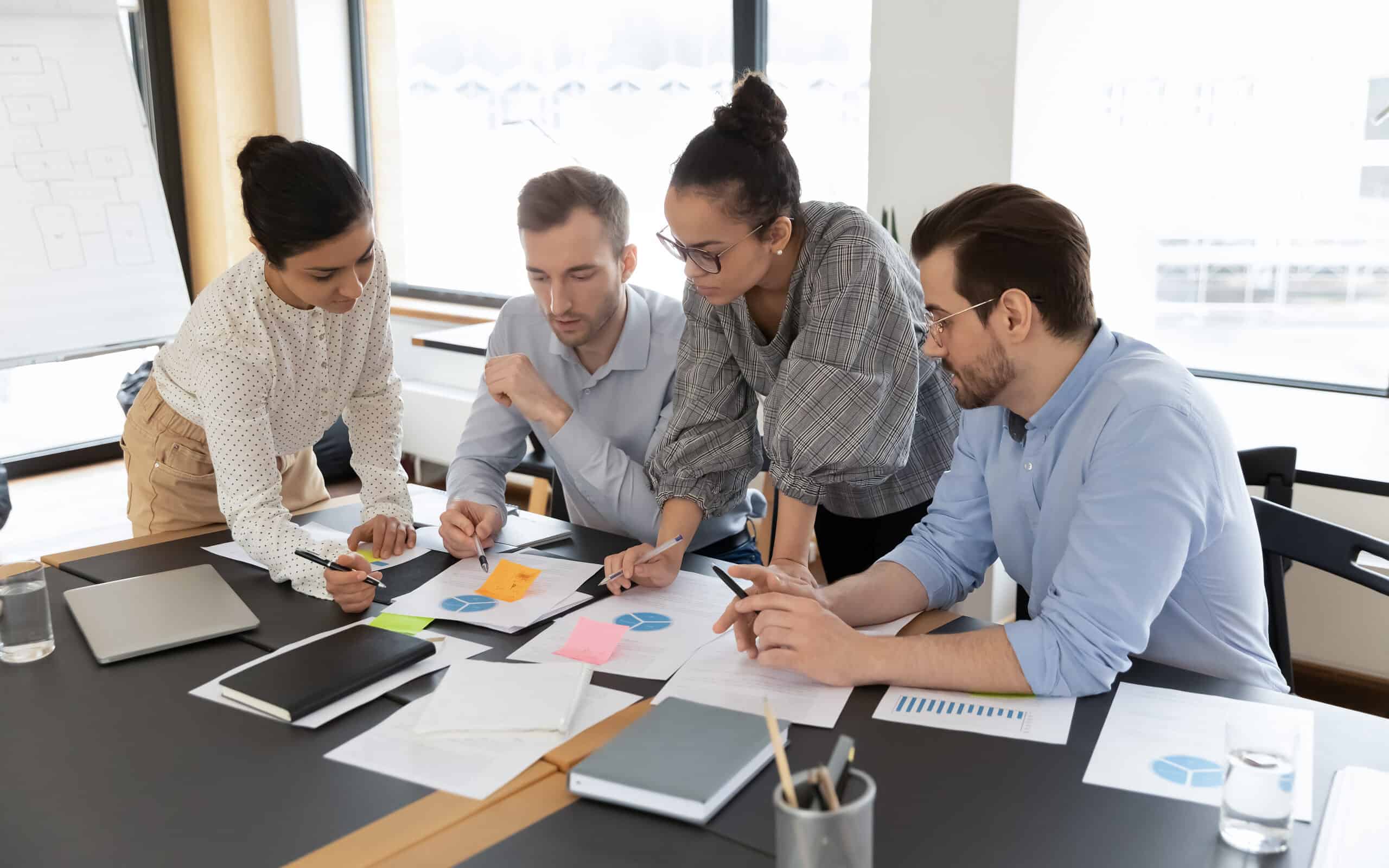
Background
A large national producer and distributor of canned instant ground coffee faced a significant challenge with product weight variation on their primary production line. The company’s specifications for fill weight included both an Upper Specification Limit (USL) and a Lower Specification Limit (LSL) to ensure compliance with regulatory standards and customer satisfaction. However, 13% of the product was either underweight or overweight:
- Underweight Cans: Violated requirements, leading to potential recalls or scrap, tarnishing the company’s reputation and incurring costs.
- Overweight Cans: Resulted in lost profit as excess coffee was given away for free.
The issue was costing the company millions annually, necessitating immediate action. Janet, the company’s Master Black Belt, conducted a process capability study to address the problem.
What They Did
Initial Analysis: Process Capability Study
Janet’s analysis revealed the following:
- The average net fill weight of the cans exceeded the specified mean (26 ounces), resulting in significant overfilling.
- The distribution of the fill weights was wide, with a large portion of cans falling outside the specification limits for both over and under fill. The specification limits were 26 oz. plus or minus 0.5 oz. for a range of 25.5 oz. to 26.5 oz.
- The Process Capability Index (Cpk) indicated poor process control, confirming excessive variability in the filling process.
This combination of high variability and an inflated average fill weight contributed to a high rate of non-conforming products. Janet recognized that to achieve cost savings and maintain compliance, the process required both reduced variation and a shift in the average fill weight.
Below is the resulting summary of Janet’s process capability study.
Janet first checked to see if the weight data was normally distributed. She gathered the data from 100 randomly produced cans over the course of 3 days. From the probability plot below, you can see that the data was not different from normal, so the assumption of normality is met.

Next, she did an Individuals/Moving Range control chart to test whether the process was in control and only showing common cause variation. From the control chart below, you can see that the process is stable and in control except for a single point on the MR chart.

Given that the underlying assumptions of normality and stability were met, Janet then did her capability analysis. From the graph below, notice that because the actual average weight is above the desired nominal, there are many points above the upper specification limit meaning that product is being overfilled but not being paid for by the customer.

Forming a Lean Six Sigma Project Team
To tackle the problem, Janet formed a cross-functional Lean Six Sigma team of production engineers, quality assurance specialists, and machine operators. The team employed the DMAIC framework to drive improvements:
- Define: The team defined the project’s goals:
- Reduce product weight variation.
- Ensure all cans meet specification limits.
- Minimize overfilling to save material costs.
- Measure: The team collected fill weight data over several production cycles. Key metrics included:
- Average fill weight.
- Standard deviation of the fill weight.
- Percentage of cans outside specification limits.
- Analyze: The team conducted a root cause analysis using tools like fishbone diagrams and Pareto charts. They identified key contributors to the variation:
- Outdated filling equipment.
- Inconsistent raw material flow rates.
- Insufficient calibration of sensors and machinery.
- Improve: The team implemented targeted solutions:
- Equipment Upgrades: Replaced outdated filling machines with advanced models featuring better precision.
- Sensor Calibration: Regularly calibrated sensors to ensure consistent weight measurements.
- Process Standardization: Established standard operating procedures (SOPs) for material flow rates and machine settings.
- Control: After implementing improvements, the team monitored the process to sustain gains. Control charts and automated alerts were used to detect and address deviations in real time.
Outcomes
The improvements led to significant changes in the production process:
- Reduced Variation: The standard deviation of the fill weight decreased, resulting in a tighter distribution of weights.
- Improved Cpk: The process capability index improved significantly, indicating a more consistent process well within specification limits.
- Eliminated Non-Conformance: No cans were underweight or overweight, eliminating recalls, scrap, and overfilling.
Shifting the Average Fill Weight
With the process stabilized, Janet recommended a reduction in the nominal (average) fill weight. This was possible because the reduced variation ensured that the product remained well within the specification limits even after lowering the average weight. This shift achieved:
- Material Savings: By lowering the average fill weight, the company saved over $2,500,000 annually in raw material costs.
- Elimination of Overfilling: No excess product was given away, preserving profit margins.
- Compliance Assurance: The reduced variation ensured every can met regulatory requirements, protecting the brand’s reputation.
See graph below for the process capability with reduced variation and shifted mean.

Summary of Outcomes
The Lean Six Sigma initiative led by Janet delivered remarkable results:
- Cost Savings: $2.5 million annual savings through material efficiency.
- Improved Process Capability: A higher Cpk indicated a robust process well within specification limits.
- Customer Satisfaction: Consistent product quality eliminated weight-related complaints and recalls.
- Operational Excellence: The production line became more efficient, reducing downtime and waste.
Wrap Up
This case study demonstrates the power of Lean Six Sigma in addressing critical production issues. By conducting a process capability study and reducing variation, Janet and her team optimized the filling process, leading to substantial cost savings and operational improvements. The integration of data-driven decision-making, cross-functional collaboration, and continuous monitoring ensured the company not only met but exceeded its quality and efficiency goals. This success highlights how Lean Six Sigma can drive profitability while maintaining compliance and customer satisfaction.