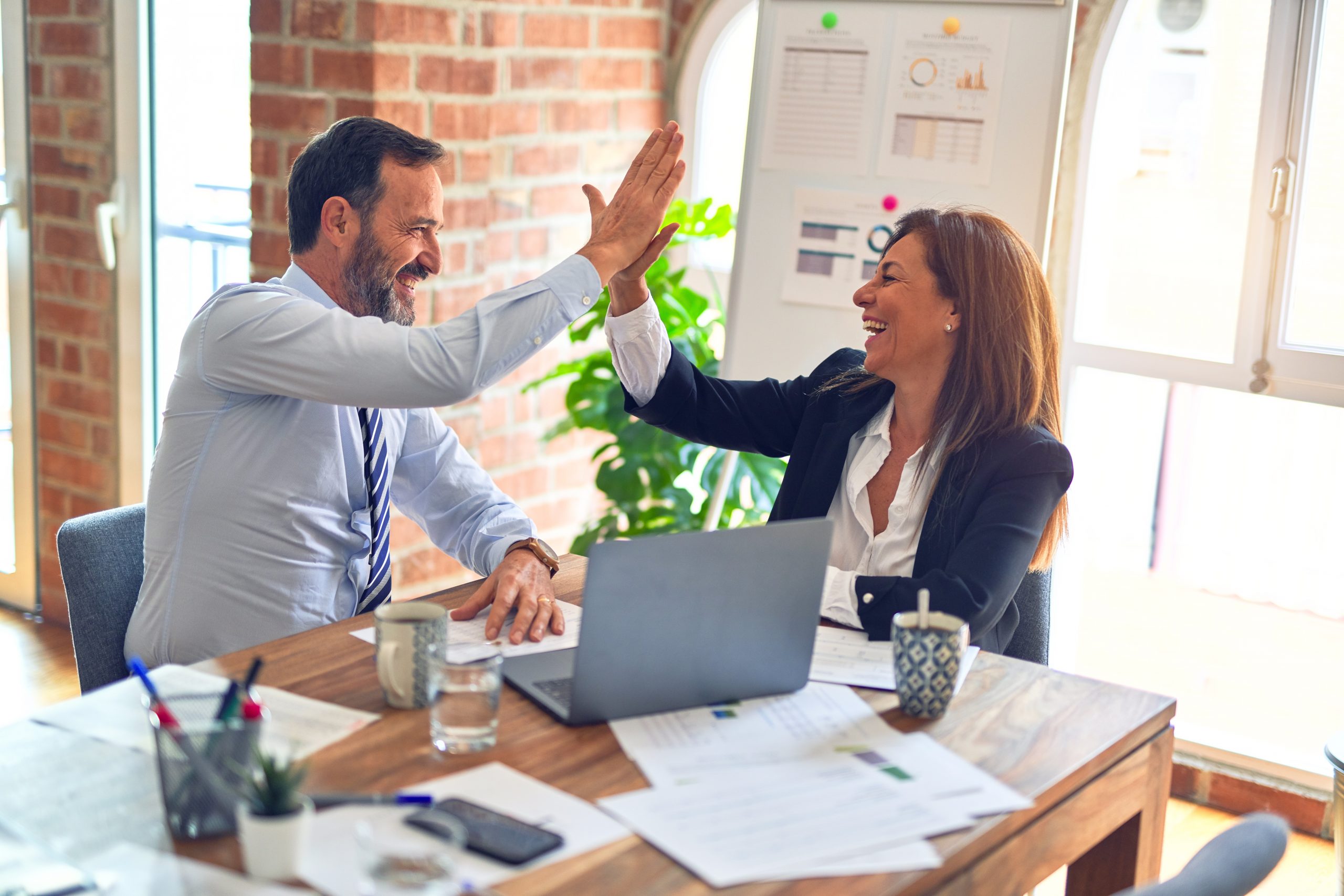
In 1979, Philip B. Crosby wrote what came to be seen as a landmark in quality management theory. The book, “Quality With” focuses on a managerial style that focuses on delivering quality in business, often in ways that are of little to no cost. One of the 14 steps listed on the way to quality improvement is error-cause removal.
Error Cause Removal
What if building up quality in our organizations need not be a costly undertaking? Philip B. Crosby proposed such an idea and listed 14 steps that would lead to quality improvement in any organization. Error cause removal is one of the steps and includes a nifty team-building exercise.
Overview: What is error cause removal?
This can be broadly defined as eliminating the cause of an error in order to keep the error from happening again.
In Philip Crosby’s book, he suggests this step be implemented by having employees list out on a one-page form, problems that keep them from being able to produce work that is free from error. These problems should then be addressed in 24 hours or less by the unit in which the issue pertains to. Showing that employee issues are being dealt with, serves to build more trust between the employee and the organization.
3 benefits of error cause removal
There are some definite benefits of implementing error cause removal in your organization. Here are a few of them:
1. Team-building
Embarking on error cause removal in the way that Crosby describes works well as a team-building exercise.
2. Trust
Error cause removal leads to more trust and belief from employees about the organization since they feel that their voices are being heard.
3. Quicker resolution
Error cause removal can allow employees to remedy many of the causes of error without having to wait for management approval.
Why is error cause removal important to understand?
Understanding error cause removal is important for the following reasons:
Prevention – By understanding error cause removal, you can prevent an error from occurring in the future
Quality control – With a comprehension of error cause removal, you have a tool that greatly enhances your ability to further quality control efforts.
Staff empowerment – Having a solid understanding of error cause removal gives you a way to eliminate errors while also empowering your staff.
An industry example of error cause removal
A team manager holds a meeting in which they plan to try a new exercise. The company is working its way through the 14 steps of building up quality in an organization, as laid out in Philip Crosby’s book “Quality is Free.” The last meeting was among the supervisors, where Step 10 was focused on and each supervisor relayed the goals of their people. Today, the employees will be putting their efforts toward Step 11. In this step, known as error cause removal, employees will list on a form the things that prevent them from having an error-free work existence. Within 24 hours, these forms will make their way to the appropriate party that can address the hurdle the employee faces and hopefully do something to rectify it.
3 best practices when thinking about error cause removal
If you plan on applying error cause removal in your organization as part of improving quality, here are some practices to keep in mind:
1. Hear every suggestion
The quality of your product/service is experienced by your staff through their daily work. Listening to every suggestion they put forth could lead to some major leaps in quality.
2. Work towards zero errors
Having zero errors is a lofty goal that will be difficult to meet, but should always be strived for.
3. Have employees state problems in a clear, correctible way
Make sure that your employees state their issues in a way that ensures that the problems can be corrected.
Frequently Asked Questions (FAQ) about error cause removal
Is error cause removal a suggestion program?
No. Error cause removal means that the problem is only identified by the employee. It is up to management to find a solution.
What company is credited with first implementing error cause removal?
General Electric is generally credited with first implementing error cause removal in the 1960s.
Is implementing error cause removal expensive?
It definitely does not need to be! All it requires is supervisor training, a simple form, and a method of keeping track of each ECR.
Seeing your quality improve with error cause removal
Working on this step of Philip Crosby’s quality improvement plan not only improves the quality of your products or services, but it also improves the quality of the work experience of your employees and their relationships to upper-management.