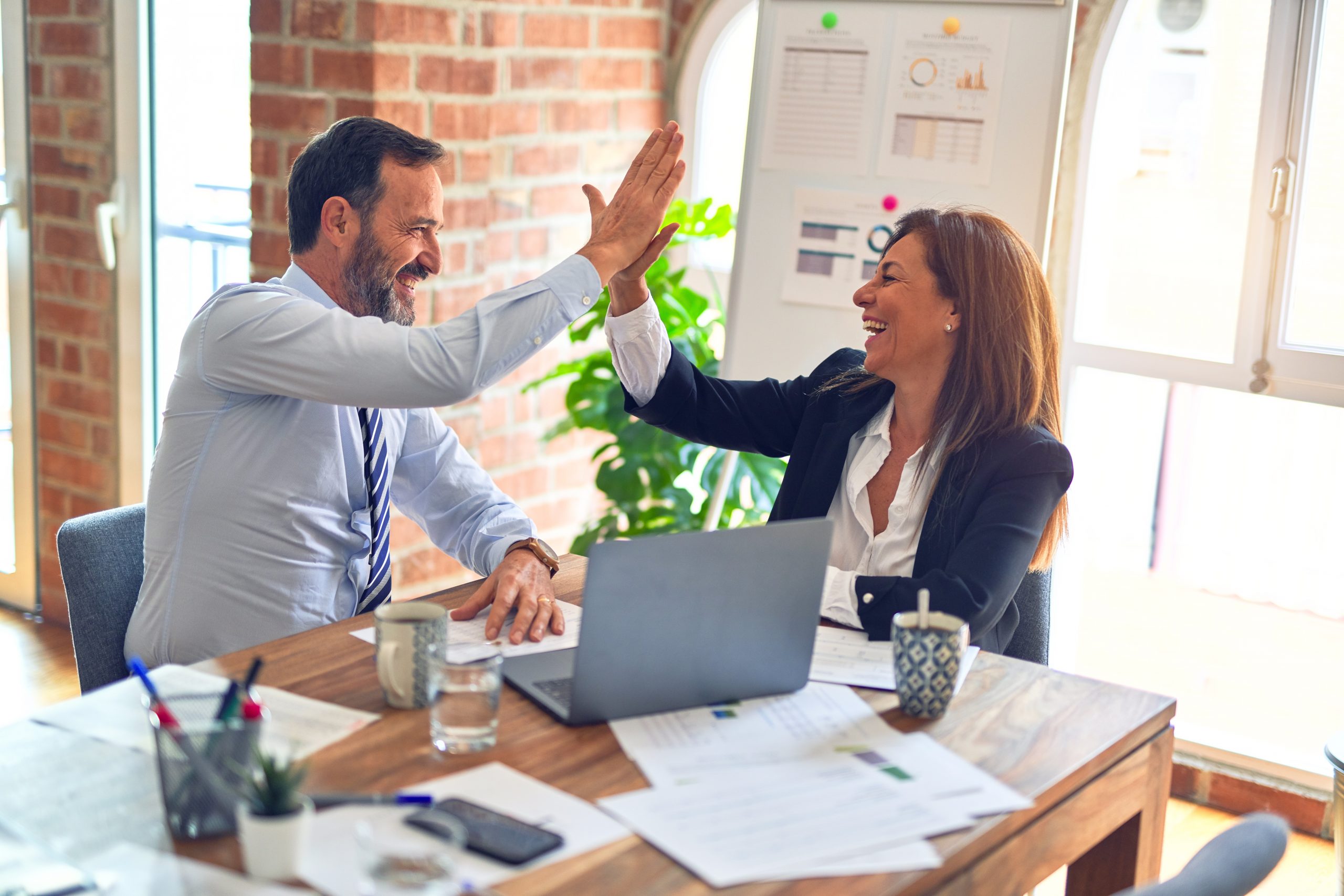
During the design or prototype stage of product development, there is a system of checks in place that can help make sure the product is successful in moving into the next stages.
The products that are released into the mass market have gone through many stages of development so that they can be trusted by the customer. One of the earliest stages of development happens during the design phase and is known as Design Verification, Production and Process Validation (DVP&PV).
Overview: What is Design Verification, Production and Process Validation (DVP&PV)?
DVP&PV can be defined as the process where planning, testing, and reporting occur in the design or prototype stage in the development of a product. The purpose is to make sure a part/component satisfies performance/reliability requirements.
5 benefits of Design Verification, Production and Process Validation (DVP&PV)
There are some major benefits to having DVP&PV for the design phase of your products that should definitely not be overlooked:
1. A well-established system
One benefit of utilizing DVP&PV is that it is already a proven system that has been in use for many years in automotives.
2. Failure mode elimination
By incorporating DVP&PV into your design stage, you are less likely to encounter failure mode.
3. Product reliability
DVP&PV helps ensure that your product is going to be reliable.
4. Cost-effectiveness
Investing in DVP&PV saves your organization money in the long run since kinks are sorted out early on in development, instead of having to be addressed once the process is further along and then have to be backtracked.
5. Saves time
Effective DVP&PV saves an abundance of time by helping to get your products into the marketplace efficiently and with less concern.
Why is Design Verification, Production and Process Validation (DVP&PV) important to understand?
DVP&PV is important to understand for the following reasons:
Process improvement
Well-executed DVP&PV is a key tool in process improvement for nearly any organization.
It gives you a leg up on the competition
If you have an understanding of DVP&PV and its worth, it gives you the advantage of getting quality goods out quicker and with more reliability than your competition.
Trust
Having an understanding of DVP&PV and making sure your products pass all the requirements, brings an added level of trust between your organization and the consumer.
An industry example of Design Verification, Production and Process Validation (DVP&PV)
In the automotive industry, each part goes through rigorous testing that begins during the design or prototype stage. This testing and verification process is known as DVP&PV. A part goes through a series of tests and sub-tests in order to make sure that it is absolutely safe for the consumer before it moves beyond the prototype stage.
3 best practices when thinking about Design Verification, Production and Process Validation (DVP&PV)
Here are some practices to keep in mind when developing DVP&PV for your organization:
1. Use dedicated software
Trying to conduct a DVP&PV report by hand would likely be a time-consuming and confusing prospect. Typically, you will use a spreadsheet with a template that has all of the necessary tests and their subsets listed out.
2. Collaborate
When putting together a DVP&PV report, run everything by developers or other relevant parties in order to catch any tests that should be included that you may have overlooked.
3. Be as thorough as possible
Test for any and all design issues that might come up. Do not ignore the ones that may seem minor. These can sometimes become bigger as a product moves on to the next stage and should be addressed before the product goes forward.
Frequently Asked Questions (FAQ) about Design Verification, Production and Process Validation (DVP&PV)
What is verification in the design stage?
It is where you verify that your design outputs are in sync with your design inputs.
What are examples of design verification processes?
A few examples would be fault tree analysis, package integrity tests, and failure mode effects analysis
What happens when a product does not pass the DVP&PV stage?
Design issues are checked and rechecked and adjusted until the product is fit to move onto the next stage or it is deemed necessary for the product to be redeveloped.
Design Verification, Production and Process Validation (DVP&PV) brings you better products
Having a system in place that checks for any issues in the design of a product so early in its development helps ensure that the consumer gets products that are safe and reliable. Without such thorough testing, who knows what quality level would be common in the marketplace?