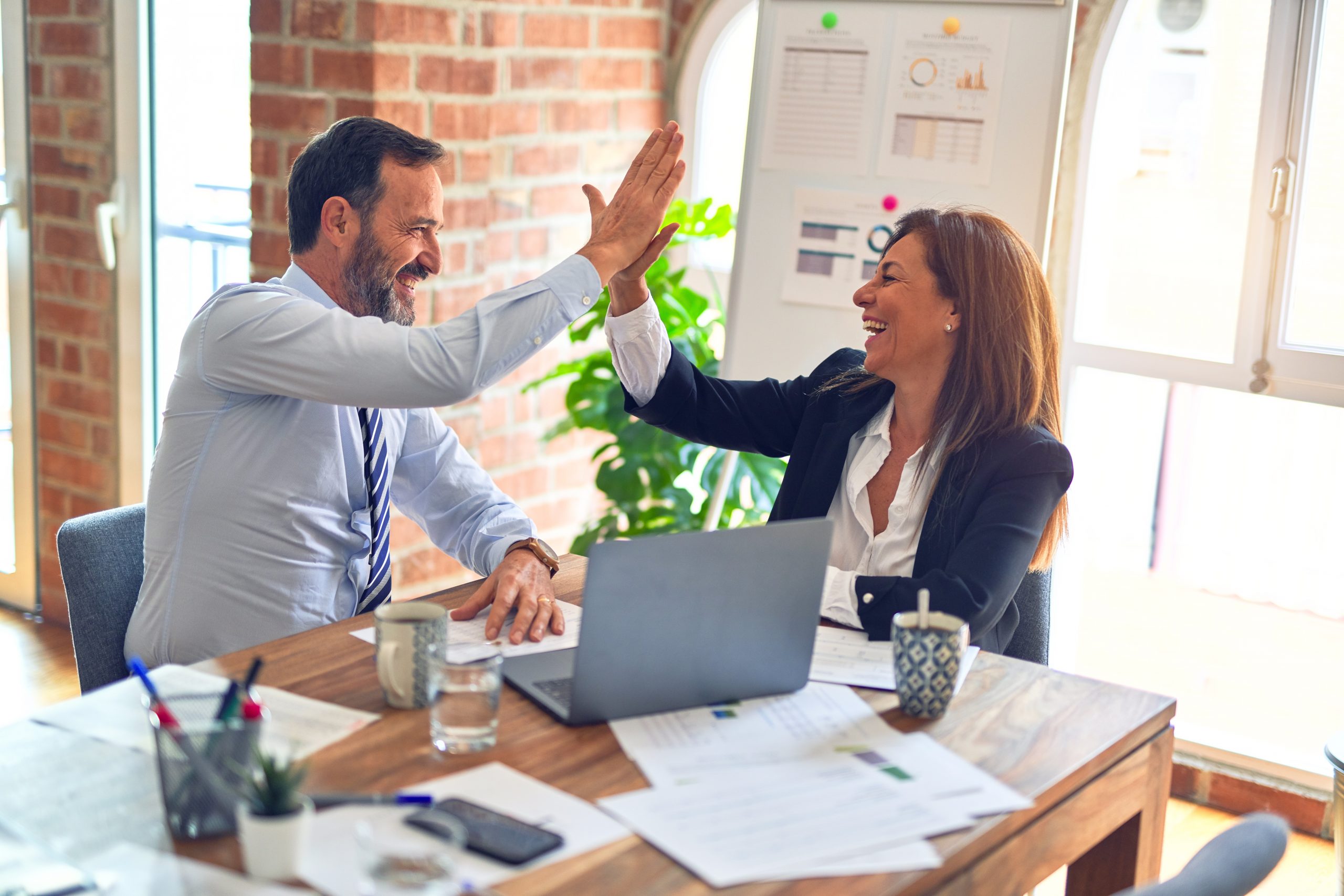
I have heard people say that once you have experienced the power of Lean Six Sigma that you will never be the same. I can vouch for that. Process thinking and waste elimination will begin to infiltrate every part of your life – including how you do laundry. I never thought of laundry as a ‘process’ but after watching my husband do laundry, I realized that batch processing was prevalent in our house. Some of it I can deal with – at least the part where you collect laundry, put it through a wash cycle and load it in the dryer. It’s the batch processing of laundry after it has dried that needed to be addressed.
Here’s how my husband does it. Once the laundry is dry, he first hangs up the shirts. Next he unloads the remaining clean laundry in a basket and takes it upstairs where he places the basket on the floor next to the bed. It can sit here for hours or sometimes days. Next he picks things out of the basket and sorts them into piles on the bed (kid’s clothes, towels, etc). Next he goes to each pile and folds the pile and stacks it on the bed. Finally he takes the stack to the final location and either puts it away or leaves it sitting on the kid’s bed for them to put away (right – like that ever happens). Taa-daa, the laundry is finally done. From dry to final location the laundry was batched up to four times and could take up to three days.
Being the process excellence zealot that I am, I advised him that changing his process to incorporate the concept of “one-piece-flow” would be much more efficient. For example, here’s my process. Get an item out of the dryer fold it and put it in the basket organized by where it needs to go. When complete, walk the basket up the back stairs making stops along the way – putting things in their place. I have cut the process down to one batch and have achieved a cycle time of 12 minutes.
After my husband told me what I could do with my one-piece-flow, he proceeded to batch the laundry. So what are the lessons learned?
1. One-piece-flow can drastically reduce cycle time
2. Cultural change is at the root of all efficiency gains
3. Batch processing is still better than having dirty socks!