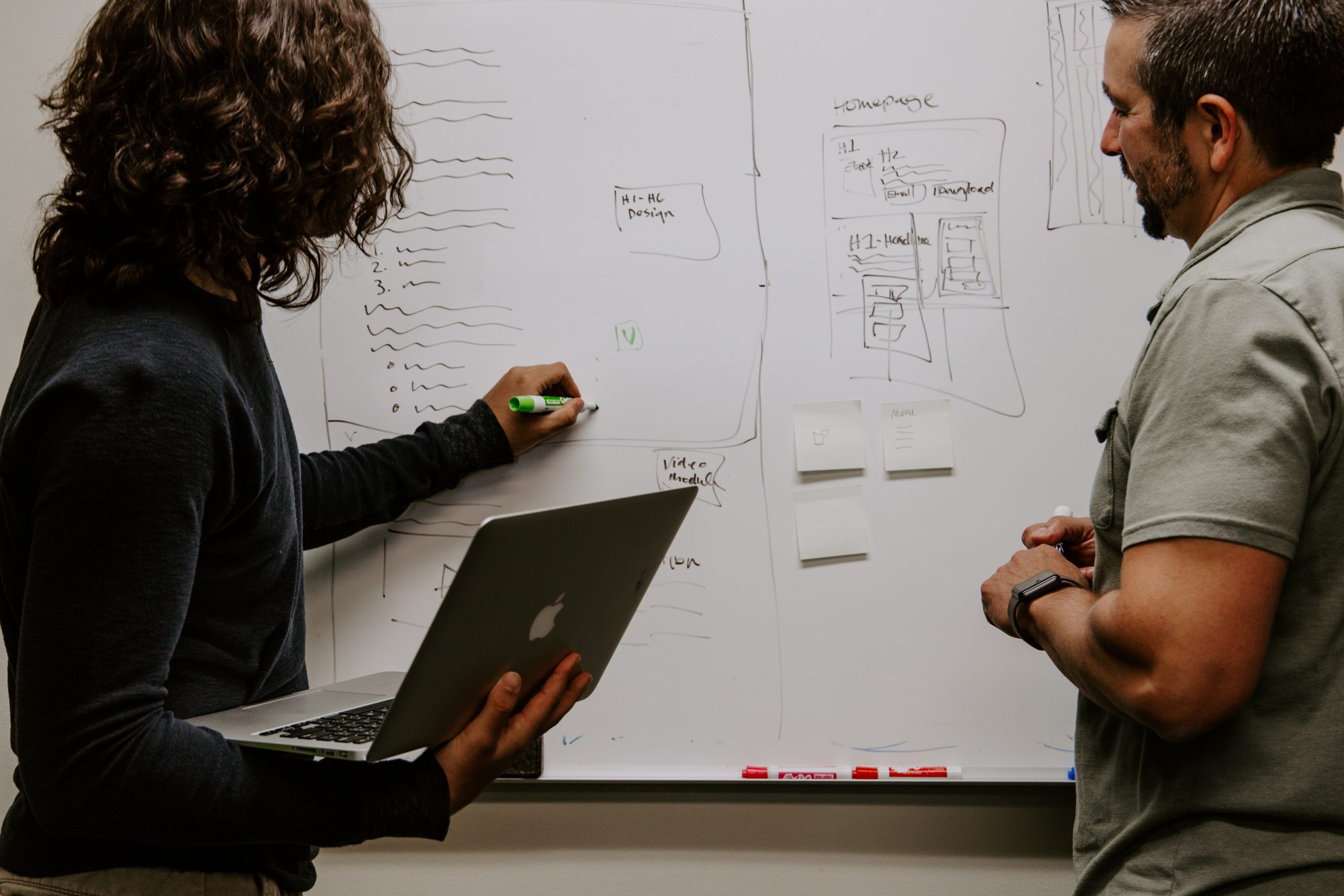
Key Points
- SOPs act as a blueprint for the tasks and activities performed by employees.
- Work instructions are manuals or how-tos for a given task.
- Both have their place within Six Sigma.
How do you choose between a standard operating procedure and work instructions? When you’re onboarding employees, it helps to have the right sort of documentation in place. Today, we’re looking at the differences between both of these concepts and where they apply within your organization.
What is Standard Operating Procedure?
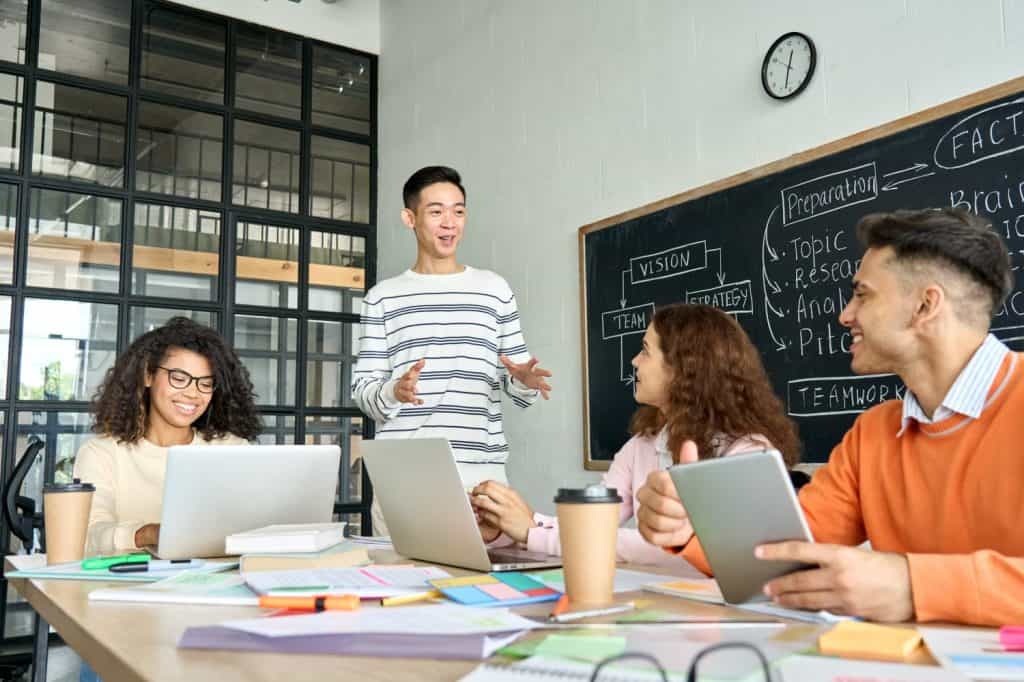
©Ground Picture/Shutterstock.com
Most established companies have some kind of standard operating procedure (SOP) in place, even if it’s a bit vague and outdated. Six Sigma practitioners have no excuse for vague or outdated procedures though because these things should be second nature when you are deep into process management.
A SOP is a type of informational aid that outlines and depicts the various activities and tasks needed to accomplish organizational goals. Typically, this document breaks down all core activities into tasks and assigns responsibility for different tasks to specific roles or people within the organization. Essentially it outlines all the things that need to be done and who needs to do them.
The Benefits of Standard Operating Procedure
Standard operating procedures are a great place to start strategic planning and process management because it’s a comprehensive approach from a high-level perspective. Before getting into gritty details, it’s important to structure all of the activities according to their position within the production or service process.
Perhaps the most immediate organizational benefit of a SOP is establishing accountability. Every task is linked to the person or people responsible, which eliminates confusion, excuses, and miscommunications on this front. It’s also a primary vehicle for company culture and values. These procedures demonstrate what things the company prioritizes and how they expect their employees to behave.
How to Create Standard Operating Procedure
Every business leader should get comfortable creating standard operating procedures, especially if they are embracing Six Sigma practices. Creating a SOP means starting at the highest level and working your way down through process mapping. Start with the end goal, which is usually a deliverable for customers, and work backward.
Standard tree diagrams are a good way to develop high-level process maps. The first level is key objectives, which are the final deliverable or outcome. The second level includes 4 to 10 general activities needed to accomplish the first level outcome. The third level is all the individual tasks needed to accomplish each activity. Once you’ve clearly defined all of the tasks for all of the activities, then you can create an SOP by organizing tasks and linking them to specific roles within the organization. Ultimately, it’s about personnel almost as much as the processes.
What Is Work Instruction?
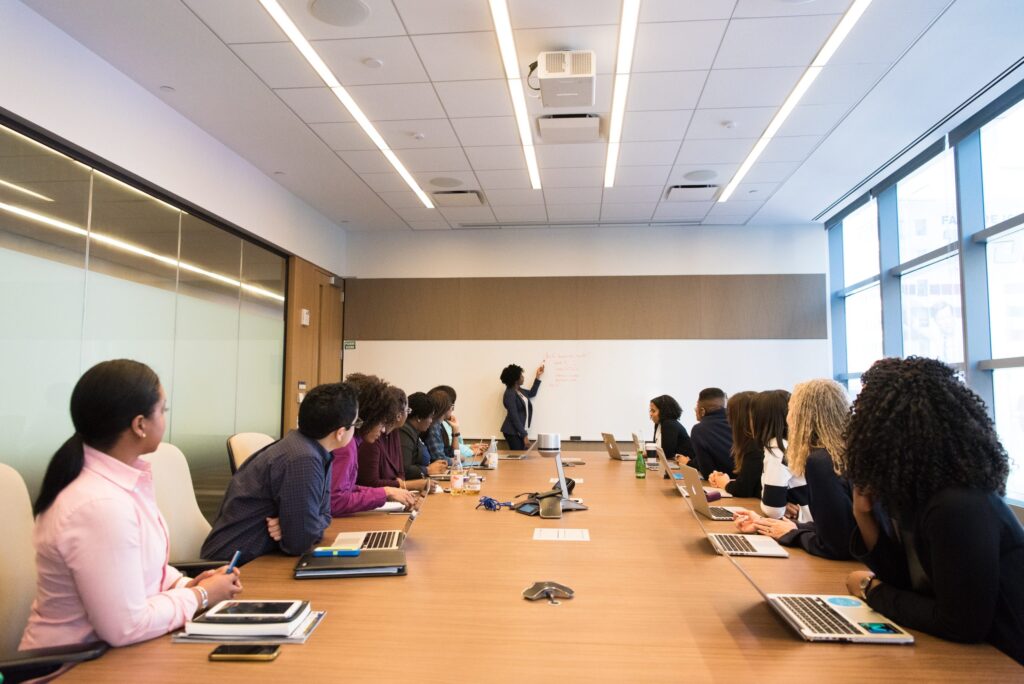
Work instruction is another type of informational aid that outlines how a company’s employees should act on the job. However, this type of instruction is much more like a manual or step-by-step guide for specific tasks. Work instructions are specific, technical, and detailed instructions on how to accomplish a particular task. They are a common sight at manufacturing facilities with diverse workstations that conduct different operations.
The Benefits of Work Instruction
The primary goal of work instruction is to create more consistent processes, which is also the primary goal of the entire Six Sigma program. Implementing work instructions can make it much easier to train new employees or move workers from one assignment to another. The ability to consult and follow a clear guide for the task means there is little room or excuse for error, which means less variability in the final output.
How to Create Work Instructions
Work instructions should only assume the most basic knowledge common in the workplace. When in doubt, spell it out. These instructions should include a chronological step-by-step list of instructions that covers every aspect of the task from beginning to end. The best way to create effective work instructions is to talk to people with lots of experience in the field and collect first-hand accounts.
Standard Operating Procedure vs. Work Instruction: What’s the Difference?
Work instructions and SOPs are both types of informational aids related to workplace operations, but they cover very different ground. Standard operating procedures are the skeleton of the organization. The idea is to maintain company values, priorities, and character through the way activities and tasks are carried out. It’s all about deploying responsibility and streamlining the organization as a whole.
Work instructions are much more specific and niche. They are only for the people carrying out a specific task or function, which could just be one or two employees in an organization of hundreds. Work instructions are just manuals or technical guides on how to do something the right way.
Standard Operating Procedure vs. Work Instruction: Who would use Standard Operating Procedure and Work Instruction?
Every company should develop both types of management aids as part of their strategic management efforts. It’s also one of the first things that Six Sigma practitioners do as they embark on the journey of continual improvement.
Standard operating procedures are about reinforcing a positive top-down structure that ensures consistency, quality, and control. Work instructions should be developed as needed alongside any new task or function added to the workplace.
Choosing Between Standard Operating Procedure and Work Instruction: Real-World Scenarios
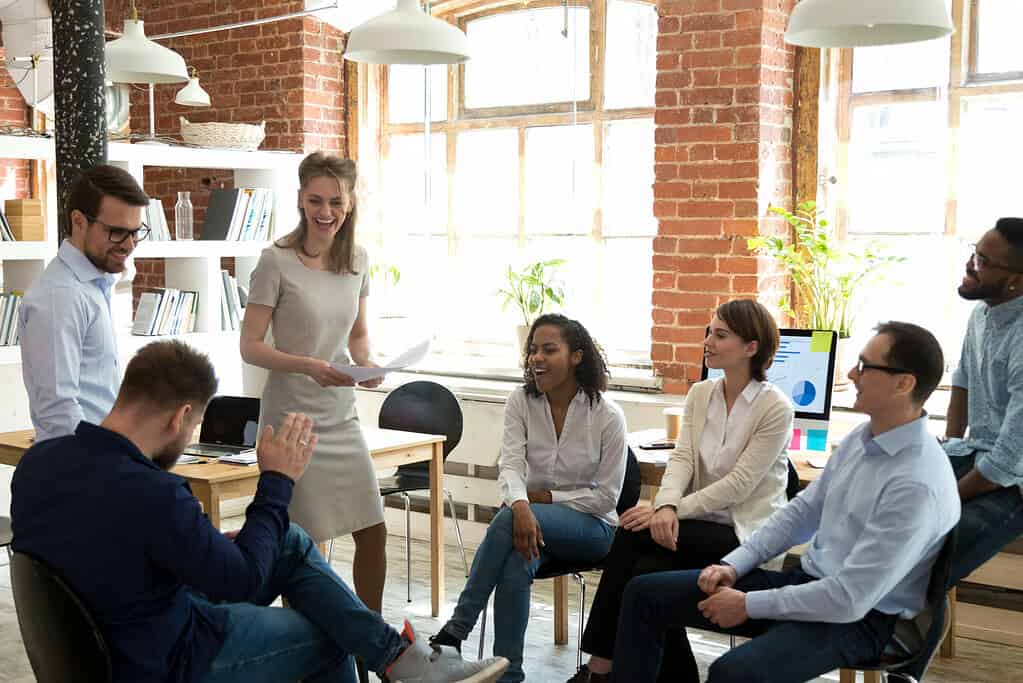
The owner of a struggling restaurant decides to embrace Lean management and strategic process management to save his business. One of the biggest problems the company faces is differences in quality of service between shifts partly due to lack of accountability or clear responsibility.
Developing a standard operating procedure would clearly outline the tasks and duties expected of each employee and each shift team as a whole.
Since the restaurant has a lot of turnover among employees, there is also a lot of inconsistency coming from individual work. For example, not all of the dishes come out of the wash cycle completely clean. To address this, they develop work instructions for washing dishes. The instructions describe how long to soak each item, what temperature water to use, and how much soap to put on each pan.
Other Useful Tools and Concepts
While we’ve explored these concepts at length, that isn’t the end of the road to learning. Learning how to account for the voice of the process and the voice of the customer is something every team leader needs to understand.
Additionally, accounting for the differences in lead time and cycle time can pay surprising dividends in the future. Production is already a complicated affair, but paying attention to the time measurements goes a long way to guaranteeing customer satisfaction.
Plan to Leave Nothing to Chance
Outlining, mapping, and delegating every single process can seem like a mundane and monotonous task for small businesses, but it becomes very important quickly as companies grow. That’s why it’s best to develop your operating procedures and work instructions right off the bat. These job aids are all about clearly communicating expectations to individual team members to ensure the success of the company as a whole.